*
Today I had to install the largest stairway I have ever moved out of my shop. It consisted of 17 treads each turning 10 degrees for a total curvature of 170 degrees. The floor to floor height is 132 inches. It took 10 guys to carefully screw it through the 36 inch front door, and set it into place. I was a little tense on this until I saw it fit the existing curved wall very nice. It took about 2 hours to get it all lagged in and secure.
Discussion Forum
Discussion Forum
Up Next
Video Shorts
Featured Story
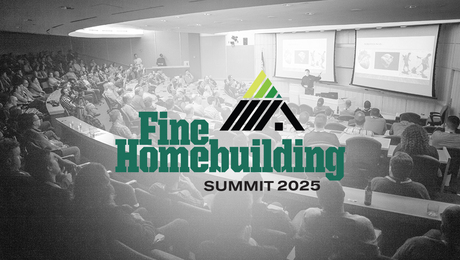
Join some of the most experienced and recognized building professionals for two days of presentations, panel discussions, networking, and more.
Highlights
"I have learned so much thanks to the searchable articles on the FHB website. I can confidently say that I expect to be a life-long subscriber." - M.K.
Fine Homebuilding Magazine
- Home Group
- Antique Trader
- Arts & Crafts Homes
- Bank Note Reporter
- Cabin Life
- Cuisine at Home
- Fine Gardening
- Fine Woodworking
- Green Building Advisor
- Garden Gate
- Horticulture
- Keep Craft Alive
- Log Home Living
- Military Trader/Vehicles
- Numismatic News
- Numismaster
- Old Cars Weekly
- Old House Journal
- Period Homes
- Popular Woodworking
- Script
- ShopNotes
- Sports Collectors Digest
- Threads
- Timber Home Living
- Traditional Building
- Woodsmith
- World Coin News
- Writer's Digest
Replies
*
truck and stairs ready to go
*stairway in front of its new home
*ten man install crew starting their task
*starting the screw operation
*more twisting
*twist/grunt
*grunt/twist
*careful
*almost in
*now just manuever it through the great room and then attach the newel posts
*getting closer
*grunt again
*in place
*side view
*top view
*another top view
*top view
*underside view
*I think my stomach would be in knots, like a father waiting for the birth of a child. Any repairs you had to do from the move. Scratches dings scrapes.Are these designs yours or were they drawn up by the architect.
*Dale: There was no damage to the stairs, just a little drywall scrapes as can be seen in some of the pictures. I had to design this stairway to fit the opening. It has an 11 inch walking line run. The outside stringer radius is 96 inches, the inside radius is 46.5 inches. I was a little tense until I saw it drop into place, and that there were no gaps at the outside stringer.
*Now my wife has more proof that stairbuilders must be mentally handicapped. The ten man team of volunteers is the reason why I disassemble the entire staircase before it leaves my shop. My wife and I are able to reasemble everything ourselves, very little chance of damage plus it allows me to prefinish everything eliminating the hassel of finding a good finisher. In a way I envy you for having a squadron of help available, I could never find 10 carefull bodies in this neck of the woods to save my life. Oh, buy the way, as always Nice Job!
*Sorry for the lack of understanding. Whats a walking line run? Is that the tread width at the center of the tread?
*Armin: Thanks again for the compliment. Coming from you, it means a lot. Everyone has his pet peeves. I love to stay in the sanctity of my shop and do 95% of the stairwork. I do not like onsite work very much. I just have to measure carefully and allow for any variance in the floors, walls, etc. I have only built one curved one on site and that was the freestanding one that was way to large to even consider moving in one piece. Otherwise, I have had very little trouble moving and installing my curved stairs. When I load my stairs, I do not get volunteers, I pay my loading help well, and I just have it in the bid as part of the expense of the stair. Everyone is happy. On the delivery end, I arrange with the owner upfront during the price setting of the stairs, to supply a bunch of guys on delivery day. I figure it costs me 200 dollars to get the stairs loaded and installed. That is "change" considering the price of the whole stairway. Also, I know I can build it in far less time in my shop, than if I build it, disassemble it, and then reassemble it. Obviously there are stairs that have to be built on site, and I would build it that way, but it would be a much higher bid. Dale: The walking line is the line that I set at 15 inches from the handrail. That is where the average body is while traveling up and down a staircase. This is where you should figure your run. If you were to measure in 15 inches on this posted stairway, you end up with over 11 inches for the run. This is not including the 1.25 inch nosing. I like to shoot for at the very least, a 10 inch run, which is minimum for code where I am at.
*Boy, You know you ship!! Do you know of many people in your area that build stairs like you do, or are you pretty much the man people go to.
*Dale: There used to be another guy near me, but he has moved. Otherwise, most people just go to the big stair hatcheries in Chicago, which is 100 miles north of me. I am just a small mom and pop type company. I do not want to get big. I love my work and there isnt much stress to it except on the day I set these behemuths. Once I see the stairs slip into place, it is very satisfying.
*I can only imagine how satisfying it must be after spending the time you do and see it come to life in front of your eyes. Where did you learn your trade?
*Dale: I picked up an issue of Fine Homebuilding, December 1989 issue, there was an article about custom stairbuilders that I have never forgotten. I have been obsessed with stairways ever since. I was working as a trim carpenter and basically taught myself. Then I really got hooked when I started building curved stairways. Most people do not want to take the time to figure straight stairs, let alone curved ones. This leaves the curved stairbuilders with an advantage. If one does something that most dont want to do, then supply and demand enters the equation. Anyway, it is very challenging, very rewarding, and I do not have to go at it like I am killing snakes. It is a very layed back occupation, and I lock my shop no later than 4 p.m.
*Allright!!! I love it. I am just getting started into this. I was also driven by FHB. My father is one of those jack of all trades and I payed close attention and asked alot of questions. I have my dads patience which allows me to do nice work although not alot of experience does make me slower than most. However most of the guys within a 10 mile radius bang them out and still manage to do crappy work. I just don't get it sometimes.
*Dale: Welcome aboard. All I can say is figure out ways to do a quality job, then should an idea come up that keeps the quality level up while also doing it more efficiently, then you are on your way. One thing nice about stairbuilding is that you do not have to have a huge outlay for tools. An average table saw, (mine is a $400 Grizzly), a jointer, I had been doing all mine with a 6 inch, but have now acquired a Grizzly 8 inch, a good three horse 1/2 inch router, thickness planer, hand tools, and you are ready to build stairways. Circular work just requires accumulated experience, and a little more math.
*Grizzly huh? I've seen them in mags and heard people say great things about them. I loved my wood shop in high school ("87"). We had some ungodly machines and hand tools. I loved the 12"jointer(WOW). We used all rough cut lumber and milled what we needed. Boy oh Boy if I ever assemble a shop like that..............but for the time being I have more than enough tools. for now at least.
*Stan-Did I hear you say "piece of cake?"Man, that is some staircase.Next time ask the builder to leave the front door off till you get the stairs in.I can't believe you got that set of stairs thru that door.Beatiful Job!Bob
*Bob: Thanks. The trick is just having lots of people for a short time. That stairs would go through a 24 inch wide opening. You just have to have 10 guys. On a normal 90 degree stairway, 8 guys is comfortable.
*Getting a good start on the curved landing tread and apron boards.
*Here are some pictures of the stairs finished. There still is finishing work being done.
*serpentine railing----214 balusters
*First of all, let me congratulate you... These pictures show an _impressive_ job. They also raise a bunch of questions for me...How many pieces of wood went in to the long curved hand railing on the floor?How did you join these (bolts inderneath, adhesive + finish on site, ...)?The inner stringer now has a wall under it. Was this really necessary (I think not...), or is it because of the clients desire?How long have you been working on this particular project (shop time, installation time)For this question, I'll understand if there's no answer (but I'm asking anyway...): How much do you charge for this kind of work? (I hope you make a good living...)I've been watching all your posts for quite a while now, and must really say you are a master!CL
*Stan-I think you might want to think about tuning up your tools. You did that whole project and could not get any of it straight! The stairs are all curvy, the railings are all bendy. I don't mean to criticize, but your jigs and fences must be way out of alignment.I hope your customer pays for the job. I have an idea though. You could tell them you meant to do it that way. Maybe they'll believe it. Customers are so gullible. It will just be our little secret ;-)Peace.-Rob
*Rob: I always tell everyone that I can't build anything straight, thats why I do curved stairways.
*Claude: Thanks for the compliments. The hickory railing consists of ten laminates. The serpentine section adjoining the top of the stairs was a 47 inch radius, serpentining the other way into a 66 inch radius. The other radii were roughly 100 inch radius. I used rail bolts to joint the fittings and the serpentine sections together. This particular stairways inside stringer was stout enough for supporting itself, but it was designed to have a wall under it. Had the owners requested it to be a "walk under", I would have made the inside stringer a little thicker.I honestly dont have an accurate log of my hours on this stairway as I had seven going at once. But I bid it as a 4 week job and I feel I was close.I make a comfortable living doing this, and I do not go at it like I am killing snakes. I try to be laid back most of the time. I stay busy and my wife helps me part time. I am reluctant to reveal any prices out of respect for my clients.
*Claude: I missed a question of yours. I have my stairs finished onsite after all the fittings have been sanded. The steps are all finish sanded and everyting is pristine after all the assembly is over. I have had to assemble stairs that were prefinished and it never works out as well for me. You have to be so careful, and many of my fittings have to be onsite fitted and sanded. This way there is no blending of finishes.
*Claude, Stan is right, it takes a lot of care to prefinish stairs in the shop and deliver them to the job site. I do it all the time and have developed some unorthodox methods to splice fittings on site. I choose to do it this way simply because it gives me an edge over the big stair companies, partially because the quality control produces a knock your socks off finish and also when I leave the customer knows it's finished, no need to worry about some painter messing it up.
*Stan,This is inspirational. Remember that laminated mahogany one from the Aug/Sep 83 FHB cover we discussed a while ago? I think about that one practically every day. After I finish installing my floors I wanna start one. Did some experiments with the bamboo flooring, ripping them down their thickness and planing to see how much they'll curve. Lined the inside of the circ stairwell with them where the stair goes through a floor. That's a start toward figuring out a curved, laminated, "walk under" bamboo stair. Gotta come up with a design though that doesn't plagerize that one on the cover. At least I'll get to build it in place, so won't need 10 helpers. Thanks for the continued inspiration. In 2002 I'll probably come back at you for continued advice! Jim
*Cloud: I cant wait to see your project as it unfolds. I am sure it will come out exceptional.
*I just took some finished photos of this 170 degree stairway today.
*StanElegant.You're a lucky man.Terry