*
I have a client who wants to have a couple of wood gates made for a 18’span. I’ve built several average size back yard entry gates, but I’m getting the feeling a 9’gate is a special animal. My thoughts are to construct the wood gates on edge with 2×8’s, either with pressure treated or clear cedar. I plan on using half lap joints at the corners secured with carriage bolts and either a 2×6 or 2×4 x-crossing in the middle. The two end post will be 6×6 pressured set approximately 3′[Oregon]in the ground. I plan an using a turnbuckle to help hold the gates in addition to some heavy duty hinges. The question is will this design concept work?? Am I missing something. Are there better ways of building the gates?? Will the gates twist or turn over time?? Any input or advice will be greatly appreciated.
Discussion Forum
Discussion Forum
Up Next
Video Shorts
Featured Story
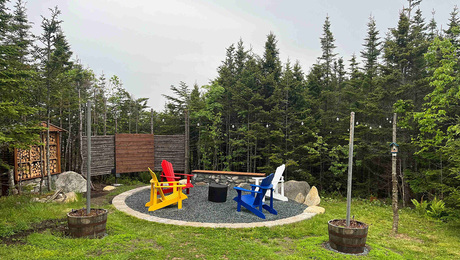
Listeners write in about fireplaces affecting family harmony and bionic suits, before asking questions about brick steps, ground-source heat pumps, and building a dome greenhouse in Maritime Canada.
Featured Video
Video: Build a Fireplace, Brick by BrickHighlights
"I have learned so much thanks to the searchable articles on the FHB website. I can confidently say that I expect to be a life-long subscriber." - M.K.
Fine Homebuilding Magazine
- Home Group
- Antique Trader
- Arts & Crafts Homes
- Bank Note Reporter
- Cabin Life
- Cuisine at Home
- Fine Gardening
- Fine Woodworking
- Green Building Advisor
- Garden Gate
- Horticulture
- Keep Craft Alive
- Log Home Living
- Military Trader/Vehicles
- Numismatic News
- Numismaster
- Old Cars Weekly
- Old House Journal
- Period Homes
- Popular Woodworking
- Script
- ShopNotes
- Sports Collectors Digest
- Threads
- Timber Home Living
- Traditional Building
- Woodsmith
- World Coin News
- Writer's Digest
Replies
*
A gate made with 2X material would be awfully danged heavy. I've never seen it used unless it was for large livestock, like a mean bull. We used 1X 6 material for most gates.
I don't know about half lap joints - never seen it done. Carriage bolts sound like a good idea. As for braces - I was taught to run them in compression. That way they wouldn't pull apart if there was a bad spot in the board.
A 6X6 sunk 3' in the ground doesn't sound like enough to hold the things up. I'd either go deeper, or use concrete around them.
*You'd get a lot of help from a wheel on the end of each gate.Maybe you could make a framework out of steel, like angle iron, and attach the wood to it.
*an old farm trick is to hang the gate from a beam that is balanced on the back side of the pivot with a rock that sets in a box on the top of the beam - I have a perfect picture of it my mind - sorry, it's hard to describe - but counterbalancing so the gate doesn't lever your posts is a good idea - don't think the setup you propose will be stable - tell me if you want me to try again - DOUD
*Ooops! Forgot to mention the concrete. Diffently set in concrete--thanks. The 1x6 sounds lighter, but a 1x6x9' sounds like it might not have enough strength. I guess one of my concerns is: will the gate twist out of shape in lets say a years time??
*various additional options:you can double the top and bottom rails. sandwich the sides and crosses in between. 2x8s for top and bottom, but maybe not for sides (picture doesn't develope correctly, in my mind anyway)use carriage bolts everywhere (you have this concept covered). lap the crossmembers with mortisses at overlap instead of cutting miters to join at center.i don't believe the turnbuckle may be necessary if done this way. not a bad idea, but probably something i would do down the road only when necessary. other option would be to reinforce corners with steel wrapped around the outside on your planned halflap joints.have a good one,brian
*Michael,For gates that big, I have always used steel for the frames. Use 1 1/2" square tube steel with a .083 wall and weld it together. Then weld a diagonal brace from the bottom of hinge side to top of latch side. Attach 2x4 with carriage bolts and pickets as usual. This keeps the gate frame from racking out of square after the gate is hung. If possible use steel posts also. Probably a 4" x 1/4" post set 3' deep and filled with concrete. It would carry the weight alot better. Just my ideas.Cole
*ColeSteel is an option I would rather use... however the owner is leaning more toward "all wood". I can purchase a prefab lite weight steel gate with 2x4 attachments to hang fence boards on. If it were my house, this would be the way to go.I guess I need to work on my "steel gate sales skills". Thanks for your input.
*I built a 20' (2-10') span gate for the entry of the driveway to our cabin. I used 2x6 green wood braced in a narrow triangle (like a shed roof truss, upside down) with 1/2" bolts, wood adhesive and three sets of heavy gate hinges - two near the top, one at the bottom. 4x4 post set in concrete, about 40" deep (MN). It's been there for five years without any apparent sagging or weakening. This is a rougher style than you're looking for, but it shows that the material works. It is heavy, but I would not substitute 1x material - guaranteed major warpage and cracking.-Randy
*Mike, my two cents worth, whatever the gate material, go 4' deep at the post supporting the gate,make the post atleast 6' tall, at the top install a gal. eye bolt, at the latch end of the gate,on top of the gate, install a gal. eye bolt,about 8'-10' parallel to the gate at ground level- install another eye bolt secured in the ground, run gal. cable with a turnbuckle at the appriate point from the ground eye up thru the top of the post eye and out to the eye bolt on top of the gate. Geoff
*Mike- I've done some post work here in Oregon and you're right to be questioning some of these finer points. One thing I've done is set double posts in concrete roughly 3' apart and tying them together with crossmember bracing. Another trick is to run your hinge post about 7' to 8' high and run a cable from a through eyebolt on the post to the same at the top of the gate where the two meet. Go as deep as you can when setting the posts. The deeper the better. Lap jointery and carriage bolts are a good idea. The rollers on the bottom of the gate might be good on concrete but on dirt they'll just trench themselves out of usefullness. I'd also use through bolts on the hinges with extra large washers to back the nuts. I always tend to overkill when doing beast work like yours so here's a few thoughts for food... Good luck
*Definitely go deep and strong with the postesI built some last year that were supposedly architect designed. They cost $7000 to make, paint and install like he wanted them. I asked if we could use steel for parts or all. Following my suggestions would have been much less but then I'm just the hired help ...We used red cedar for a lightweight gate that would resist rot. Easy for one man to lift a 107" x 5' gate.This had some curves so we reripped and laminated with West system epoxy. Used joints similar to half lap with epoxy and pegs. The epoxy at joints is good because anything else will loosen up with time.At the stressed hinge side, we laminated a steel bar into the stile.For yours, I would look at using 1x6 rails on either side of the ballusters with epoxy or other adhesive at all joints, plus screws. That way the water running down the balluster will shed right on through. I would not use PT. It is too heavy for gates and often twists and warps too much. I like the cedar for this. Doesn't necessarily need to be expensive clear red cedar.
*by the way. those wheels will set themselves into asphalt as well (won't even take that long during a good hot summer).brian
*Pictures.I was driving around to different meetings and estimates today so I openned up the shutter.This first is one of a pair that I built about twelve or thirteen years ago. It's built the cheaper way I mentioned above and hasn't warped too much though the posts are well leaned over. It's about 6'6" for each, 1x6s half lapped into doubles at bottom and top rail with bleeder space. curve capped with 3/8" twice. Screws still show. I used construction adhesive at the joints.
*I think that previous took about three days for me alone way back then.This one is the epoxy laminated set that spent a little more money. Had three men including self for about a week.