I don’t remember where I saw the article, but it was about measuring for cabinets using two overlapping sticks. It was either in fine homebuilding or fine woodworking. Can anyone here help?
Discussion Forum
Discussion Forum
Up Next
Video Shorts
Featured Story
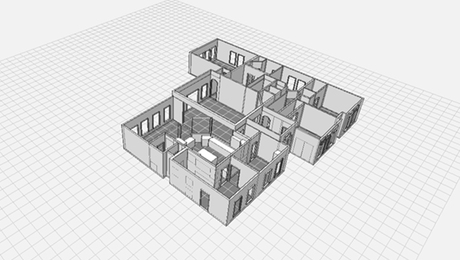
Hover's smartphone app offers an easier way to get precise 3D scans.
Featured Video
Builder’s Advocate: An Interview With ViewrailHighlights
"I have learned so much thanks to the searchable articles on the FHB website. I can confidently say that I expect to be a life-long subscriber." - M.K.
Fine Homebuilding Magazine
- Home Group
- Antique Trader
- Arts & Crafts Homes
- Bank Note Reporter
- Cabin Life
- Cuisine at Home
- Fine Gardening
- Fine Woodworking
- Green Building Advisor
- Garden Gate
- Horticulture
- Keep Craft Alive
- Log Home Living
- Military Trader/Vehicles
- Numismatic News
- Numismaster
- Old Cars Weekly
- Old House Journal
- Period Homes
- Popular Woodworking
- Script
- ShopNotes
- Sports Collectors Digest
- Threads
- Timber Home Living
- Traditional Building
- Woodsmith
- World Coin News
- Writer's Digest
Replies
Are you talking about story poles?
Shout out to Andy C. Namaste my friend.
http://www.hay98.com/
Don't remember seeing an article, but that's the method I use to get accurate measurements for replacement windows.
What was it you wanted to know?
I don't know where you saw this, possible both locations.
It is common old "trick" for getting exact inside mesurements.
Take two stick, each about 2/3 the lenght of the opening. Then the slide them that the end of one is against one wall the other against the other wall. Then clamp them together.
Lee Valley has some "guage heads" to make a set, but you can use any clamps.
There web site show them in use.
http://www.leevalley.com/wood/page.aspx?c=2&p=32585&cat=1,43513
Lee Valley/Veritas calls them bar gauge heads, from which I infer they call the tool a bar gauge or pair of bar gauges.
In furniture & cabinet making, we call them pinch rods (initially, they were just pinched together tightly), and we use them primarily to ascertain whether a carcase is square and, if out of square, by how much; they're ideal to taking inside measurements without measuring.
I start with quartersawn or riven stock (for stability) and rough them out out at the bandsaw, leaving the rough-sawn surfaces facing each other to minimize slipping. Next, cut the ends at an angle greater than 45-degrees (to prevent binding inside corners), and square the remaining faces and edges with a hand plane; making a pair 3-feet long probably takes 5 minutes or so.
I hope this is the kind of information your were looking for,-Jazzdogg-
Whether you think you can, or you think you can't, you're right.
chinese tic sticks my Dad used to call it ...
not sure why ...
and I'd bet he made that up the first time I asked what they were called ...
But that's the name I use!
Jeff
Buck Construction
Artistry In Carpentry
Pittsburgh Pa
What advantage would the sliding sticks have over my folding rule?
The awful thing is that beauty is mysterious as well as terrible. God and the devil are fighting there, and the battlefield is the heart of man.- Fyodor Dostoyevski
.......well, ya beat me to it.
A proper measuring device is all that is needed.
A Lufkin Red End extension rule comes to mind........wonder where I've seen one of those????
Oh yeah, I know. It's in my back pocket all day long!!
Might be a challenge though, some arithmetic skills are also required!
Eric
be an inside measurement.I Love A Hand That Meets My Own,
With A Hold That Causes Some Sensation.
[email protected]
One advantage is you can write all the pertinant info right on the sticks. They tell the whole story..widths, heigths, ect.
For some it is easier to use on side of a pair ( keep em matched up right) for each orientation. For just a quick inside measure, a folding rule with the extension is just fine. But for say a complete custom built in wall unit, sticks are indispensable. Spheramid Enterprises Architectural Woodworks
The Morphine s eems to do no good at all..I'd run all the way if I would not fall...
> What advantage would the sliding sticks have over my folding rule?Would be the same, if you have a folding rule with a sliding extension on one end. But a regular tape or folding rule can't take exact measurements between two facing surfaces.
accuracy?
Jeff Buck Construction
Artistry In Carpentry
Pittsburgh Pa
I use sticks a lot because they are not only accurate, but because I have a serious problem transposing numbers.
It's an ancient method and there's not much to it. It's just overlapping sticks with a marked scale on the one and an indicater line mark on the other. They just slide against one another from point to point. In cabinetry and framing they are used a lot to check diagnally for square, and they work well for I.D. measuring. I've made and used several of them. A story board is another thing.
No need for a marked scale. Measure the final length of the sticks with a tape, or transfer the measurement directly from the sticks to the workpiece.
JWool, I often use the 2 stick method while framing. It's a very simple, yet effective way to get quick and accurate measurements between two fixed points.
For instance, I needed to set a post under a porch yesterday. The post was a very heavy waterlogged 6 x 6 x 20'. I used two pieces of 1x2x 14' and determined that I needed about 18' of it. It took me about tens seconds without a ladder.
I often use variations of this technique to get other measurments.
Ironically, I've never noticed anyone else using this method around me. They are all so fixated on using tape to measure everything that they miss this very obvious easy measurement transference technique.
blue
I do this all the time. But when I'm near a surface (say, on a ladder measuring for the next piece of bevel siding in a gable), I just use my tape to measure from the left to a mark I scratch right in front of my face, then from the right to the same mark. Add the measurements.I do this also to measure inside dimensions (of a cabinet for example), because I don't have one of those fancy Lufkin red-end thingys.
of course yo know that when dealing with a gable end, a good cut man can calculate the difference in course lengths and once one pc is up, ought not need any more measurements. Unless a window or other jog occurs.
If the first pc is 12' long and you have the rake angle and the exposure of the face..it is simple to just deduct the shortage needed for the next courses. Saves the hanger a lot of measuring.
But you knew that. Spheramid Enterprises Architectural Woodworks
The Morphine s eems to do no good at all..I'd run all the way if I would not fall...
Yeah, but knowing that and actually making it work is many times a losing battle! While ship lap or gauged bevel (or log) siding keeps precise reveals and therefore consistent measurements (where calcualations are pretty effective), I've had much expereince applying 1/2 x 6" bevel cedar, ungauged, w/ theroretical 4 1/2" reveal. Problem is in theory vs. practice in this case...Due to slight differences in widths of the boards, the math starts to break down over a few courses and constant re-adjustments are necessary to keep the reveals from getting out of hand. Every so often, even us good cut men have to break out the tape!BTW, I always cut in gables tight against the (pre-applied) rake trim, unlike many who nail on the rake boards OVER their poorly fit gable siding. SHeesh, I've even seen "Fine homebuilders" do this.
I know what you mean about being fixated on using a rule or tape. I tried to show the guy I work with how you can place a tile exactly on the last full tile near a wall and then place another whole tile butted against the wall and mark across the first tile to get the cut for the partial. He refused to do it, measuring each gap with the tape and taking each tile one by one to the saw to cut. Very time consuming and not as accurate. But he knows it all and won't listen to me--I'm just a newbie.
Danno, you've described an overlap technique that I've been using on sheetstock for 25 years! I've often said I could lay an entire deck and roof without a tape or chalkline. Come to think about it...that's how I always do it!
blue
Danno.
The Ez way is to use the tape measure. No thinking required there.
Is more work,more time and more mistakes. But no thinking required there.
Variables of the two stick method can be the answer to a good and Ez job.
Ceramic tiles,ceiling tiles,moldings etc etc.
Is funny to see guys using the tape measure for everything.
They even try to do multiple measurements on the same length of stock 1000 times and spend the whole day making mistakes,instead making up a marking stick and transfer the exact measurement 1000 times,.. perfect.
To me and my guys was ...anything but the tape measure.
YCF Dino
I agree with everything you said. It is frustrating because this guy will measure something and transpose numbers and so forth--the other day he took a panel home because we didn't have a table saw on site and cut it an inch short. Then he had to add a trim piece to cover the mistake. He often measures every repetitive cut instead of using stop blocks. It's like framers who measure (or worse, take measurements from drawings) to cut top and bottom wall plates.
My boss when I was framing once told me he would be late the next day and I should start by cutting all the window and door headers. So I cut them and marked them because when he cut them first he'd stack them and we'd spend a lot of time sorting through to find the right one. I wrote right on them what they were and he still put the wrong ones in because he didn't stop to look at what I'd written!
Once he told me to make saw horses and I made them with the legs angled forward and back about 10 degrees. He criticized my work, saying they were supposed to be at 90 degrees. I told him with my way the horse wouldn't rack under a heavy load like when we stood plywood on edge on them before lifting it to the roof--I was tired of his horses racking and dumping the plywood. He said he guessed they'd be okay this time.
It used to be the case that the Japanese master carpenter
would have all the basic height measurements for the house written in ink on a single tall stick, things like doors and
windows, etc. Then he'd go around and mark everything in
one pass.
There is also a technique using multiple sticks that allows
you to represent a two dimensional space, such as a countertop, quickly and accurately
without making a precisely fitting template. This is called "tick sticking." Check out this
illustration,
View Image
which I got from this thread at Woodweb
When the first poster talked about sticks I thought of the tic sticks; there was an article on how to use them in FineHomebuilding a couple years ago if I remember right.
Here are links to some related articles, available in the Fine Homebuilding Archive.
May 1984 Ticksticking Sam ClarkThis little gem describes a technique for fitting a flat panel into an irregularly shaped recess without any trial-and-error fitting or a bevel or a ruler or any math. Simple and effective.
November 2001Using a Story Pole to Lay Out Stairsby Lon SchleiningA simple full-scale pattern takes the confusion out of figuring consistent and safe stair-tread heights
This short article describes how to use a story pole instead of a framing square to lay out stairs and eliminate accumulated layout errors that can result in uneven tread heights.
May 1994Framing Gable Endsby Jim ThompsonYou can use a story pole and a level to lay out accurate cuts without a tape measure
A framing carpenter turned structural engineer describes his method for framing gable-end walls. He uses a level and a story pole instead of a measuring tape and explains how to use the "common difference" associated with the roof pitch to speed layout.
November 1997Installing Wood Clapboardsby Rick Arnold, Mike GuertinHow a seasoned crew uses a story pole and an efficient work sequence to install this traditional siding
This article covers the installation of wood clapboards, a traditional and regionally popular exterior wall finish. The authors cover all the basics, and also offer advice on what wood species is best. Ruth DobsevageTaunton New Media
When I need to lay out stairs I just whip out a quick computer program. Far simpler than any other approach.The tick stick approach would be good for cutting siding for a gable end. When I've needed to do it the roofline wasn't straight enough to just use repeat measurements.
Stairs are only 2 measurements, rise and run. What advantage does a computer add to calculating simple arithmetic?J.P.http://www.jpkfinefurniture.com
I've never seen a set of stairs without at least four critical numbers -- rise, run, tread thickness, and nosing depth. And there can be one or two more in even moderately complex cases. Plus, you don't know what the rise is until you work through the numbers.Plus, a stringer is at an angle, meaning the real critical measurement is the angled length of one step. It's that measurement that you need to first get to come out even (sort of) top to bottom, and then figure everything else off of that.
Dan,I re-read my previous post and apologize if I came across as a little arrogant(azzhole).When I was building stairs the floor thickness was always the critical issue and what eventually determined the overall rise.Tread thickness was always consistent, and therefore was not a component in the overall rise, but rather a variable that was subtracted from the rough string in order to drop it to the proper height to allow for the addition of the tread so that the first step had the same rise as all the others.The nosing, or projection( not the same as run) was always additional as well. The overall run was calculated by what was required by code at the time and multiplied by the number of risers to come up with the length of the stair. At the time the nosing requirements were from 3/4" - 1 1/4", and were consistent throughout the going of the stair. The only difference in run of the stair would be at the top or bottom if one had decided to change the nosing projection.I understand that there are a lot of things that can go wrong with a stair. However the basics still remain. If you understand rise and run, then you can build a set of stairs. Didn't mean to hijack the thread.J.P.http://www.jpkfinefurniture.com
No problem. My point is that there are a dozen (at least) different ways to do it wrong, plus you have all sorts of trouble with cumulative error if you try something akin to the framing square technique. With the computer you can print out a precise list of measurements for each step (most importantly, the distance down the length of the stringer for each step), and, if you don't like the way it works out, just plug in different numbers.I'm tempted to make up a general-purpose stair program, but there are so many variables (trying to make nosings line up with trim, etc) that it would take some work and quite a bit of study to make a good general-purpose tool.
Dan,I agree that there are at least a dozen different ways plus one to screw up a stair. But the cumulative error thing was solved by Pythagoras.There have been many times when I have used a large pair of dividers to make sure that the string was not too long or long enough by measuring the hypotenuse of the rise and run.I would constantly check my math as I added treads to make sure that the last tread would end up where it was supposed to.This always came down to the understanding of rise and run. Or more simply, how much room is left and is it gonna work.J.P.http://www.jpkfinefurniture.com
Still sounds like you're describing a trial-and-error method, with plenty of room for accumulated error. And you still have to drag out a calculator to compute the ol' hippopotimus, unless you're one of the three people who remember the square root algorithm from high school (and know how to do it in inches and fractions).
Dan,
It's not trial and error. It is simple math. If I have a stair that goes to a second floor with an overall height of 108" from finished floor to finished floor and you have 14 treads (15 risers) your riser height is 7.2" or 7 3/16".You can then use the riser height to check your progression as you move up the stair to see if you are adding any error. I would do this mainly with closed stairs. Open stairs have the outside skirt which keeps things where they should be.If your tread thickness is 1" then drop the string 1" (cut 1" off the bottom) to keep the top and bottom rise the same. Tan = opposite/adjacent, So the angle of the stair is Tan-1 (7.2/10) = 35.75 deg. I used 10" as the run for the tread.Length of hypotenuse is the sq root of 7.2 X 7.2 + 10 X 10 = 12.32 . If you set a pair of dividers to this dimension you can step off the layout for the strings and skirt and use in addition to stair gauges with a square.The numbers are what they are. I don't see how to get cumulative error from this or how this is trial and error.J.P.http://www.jpkfinefurniture.com
If you step off the layout with dividers, by definition you're getting cumulative error."Cumulative error" is error that increases with each step in an operation. If you're off by 1/32" on the dividers, after ten steps you're off by about a third of an inch.If, on the other hand, you compute the positions for the steps, using essentially "infinite precision" (which computer arithmetic can easily approximate for simple cases like this), all measurements can be from a fixed reference point, and the maximum error is basically equal to your accuracy for any single measurement.You can do this by hand, but with English measurements it's a PITA unless you do the computation in decimal fractions and then convert back to the usual inch fractions (an operation which is itself quite error-prone). Much simpler if you use Metric, or if you have a rule graduated in inches and tenths.
Edited 6/7/2005 11:39 am ET by DanH
You do avoid the trial and error aspect by dragging out your calculator and figuring the hypotenuse and stringer angle. No way to avoid trial and error without the calculator (or being a real math whiz).
OK, just for grins, here's a crude Java program for doing stairs. (Actually quite a bit fancier than I'd do normally, since I would just plug the numbers right into the program, vs all the prompting and keyboard input.)[The program sort of assumes a simple deck stair, in order to have some basic set of assumptions.][Added the angle of the stair. See next message]Hopefully this attaches reasonably well:
Edited 6/7/2005 5:48 am ET by DanH
Here it is, with the stair angle added:
I've used that method lots of times for fitting bulkheads in boats. Another method thats good for scribing is run a washer along wall with pencil in hole and transfer right on to your sheet goods or board that needs scribe.
Very interesting Talking Dog!
I'll remember that picture and technique when I find myself in a corner some day.
Thanks.
blue
"Pinch rods" , or "Pinch sticks". Thats what I've heard them called. I've worked with old timers who used them for cabinets and such. I've made them myself and used them. Take two straight pieces and bind them together in two places with just enough friction to hold them tightly together when they slide against each other. The ends are beveld to fit into corners, to check for square etc. I've seen fittings to make them advertised in various woodworking catalogs but the ones I've seen on the job were homemade, bound together with wire or plumbing fittings or what have you.
I'll add that I love this kind of stuff. This old carpenter technology that is still applicable on todays jobsite. Like many here I've spent a lot of time training unskilled help to do basic carpentry. Some folks just cant do numbers very well, or follow complicated instructions. We used to call them Knuckleheads (I are one). I try to show my helpers the simplest way to do accurate work with the least calculations. Someone here has the tag line "Scribe once, Cut once", and Ive been saying that a lot lately. I'd like to see a thread talking about these kind of techniques, or maybe an FHB article?
Edited 6/4/2005 11:38 am ET by mcfish
Story sticks are extremely useful for any number of tasks.
For anything up to 8’, I like to use a single stick – 1/4” thick by 1 1/2” wide, which leaves plenty of room for written notes. But you could certainly make longer sticks by ripping them from longer pieces of stock.
For any kind of built in (including kitchen cabs), I use one stick for vertical and another for horizontal. On these you can keep track of outlets, casings, plumbing stuff, etc.
After the job is completed, I sand off the pencil lines, and they are good to go again.
For lengths longer than 8’, I will generally use two sticks (with register marks). They need to be clamped (or screwed together, but Lee Valley has solved that problem (see link in Post 4 in this thread). But their set-up must be used with stock that is only 3/4” wide.
Once you get accustomed to them, you’ll find story sticks are indispensable for a variety of measuring jobs.
********************************************************
"I tend to live in the past because most of my life is there."
-- Herb Caen (1916-1997)
Thanks all for the feedback. I guess no one has seen the article I seem to remember. Although I don't profess to be a master at anything (more like a jackass of all trades) I do appreciate simple methods that have stood the test of time. One thing that I like about stick measuring is that there is no conversion involved - just a direct measurement that is not subject to arithmetic errors or rounding up or down. I'm an engineer by training so I don't have a hangup about math, but I still occasionally make mistakes measuring things with tapes thanks to the steady demise of brain cells. I guess I need to dig out my cache of old issues and do some searching.
Sounds like the technique I used for measuring for my suspended kitchen ceiling (gotta post pictures of that sometime). I needed exact measurements for the distance between the two sides of the soffit, which was 6 feet +/-. I bought a 10' piece of 1x3, cut it in half at about a 45-degree angle, then jury-rigged a pair of sliding clamps so that the two pieces could slide relative to each other and be clamped when the end points were touching the sides. This gives you an very exact measure, without having to have someone hold the "dumb" end, and without having to fudge for the curl in the tape.
The measurement from this can be transferred directly, or you can measure the length of the clamped poles with a tape and transfer that way.