*
We are planning on building a new home here in Michigan. Most homes are built with 2×4 exterior walls, although some are built with 2×6’s. This increases the costs for door jams, window extension jams, as well and additional insulation, etc. One local lumberyard said it would take years to payback the added expenses (savings in heating costs). Does anyone have any opinions to any aspect of this? I would appreciate any response.
Discussion Forum
Discussion Forum
Up Next
Video Shorts
Featured Story
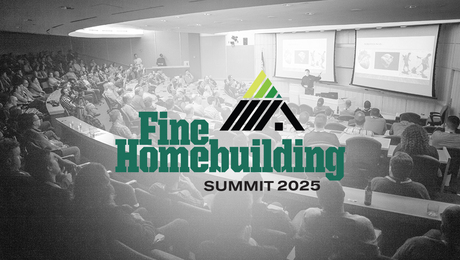
Join some of the most experienced and recognized building professionals for two days of presentations, panel discussions, networking, and more.
Featured Video
SawStop's Portable Tablesaw is Bigger and Better Than BeforeHighlights
"I have learned so much thanks to the searchable articles on the FHB website. I can confidently say that I expect to be a life-long subscriber." - M.K.
Fine Homebuilding Magazine
- Home Group
- Antique Trader
- Arts & Crafts Homes
- Bank Note Reporter
- Cabin Life
- Cuisine at Home
- Fine Gardening
- Fine Woodworking
- Green Building Advisor
- Garden Gate
- Horticulture
- Keep Craft Alive
- Log Home Living
- Military Trader/Vehicles
- Numismatic News
- Numismaster
- Old Cars Weekly
- Old House Journal
- Period Homes
- Popular Woodworking
- Script
- ShopNotes
- Sports Collectors Digest
- Threads
- Timber Home Living
- Traditional Building
- Woodsmith
- World Coin News
- Writer's Digest
Replies
*
There has been much debate on this question over the yrs. My advice is no matter what the thickness of the wall, be sure to use good air sealing techniques, a quality insulation material such as dp cellulose and have it installed by a real pro. I've seen dozens of homes with 2x6, insulation voids, plenty of drafts and air exchange.
*
Hi Jean,
As a Registered R-2000 Builder here in Ontario, I am fairly well versed in energy efficient housing.
Since Michigan, is somewhat similar to, Ontario in terms of climate, my advice to you would to definitely consider the use of 2 x 6 framing for added insulation in your walls. The code here is
R-18.5 which translates to 5 1/2" of batt type insulation. The additional cost in insulation and jamb extensions is negligible. I tell clients that mechanical (heating/cooling) systems and insulation is not a good place to skimp on money, afterall, whats the point of building your dream home and not being comfortable on a cold January evening or on a hot July afternoon.
Taking that one step further, I know of some clients who could not afford to heat their home and had to sell it on this point alone. How do you tell a prospective purchaser that!
Another consideration is using 2 x 4 framing with an insulating sheeting board. IE: Styrofoam Clad Mate, etc. Depending on the cost of lumber at the time, this detail can be even more cost effective and is even more effiective than 2 x 6 framing. This method is used by many tract type builders here when lumber prices are high.
Good luck with your project, but remember, it does not matter how nice your home is if you are not comfortable in it. Pay close attention to air barriers and vapour barriers to prevent drafts.
If I can be of any further help, just drop me a line.
Sincerely,
Leo Cianciolo
*
The lumberyard must be running short of 2x6's.
Seriously, don't forget to consider any framing savings gleaned by using 2x6's 24 inches OC vs 2x4's 16" OC. Not that the 2x6's will be less expensive, but at 24"OC the cost differential is reduced.
In addition, reduced heating and cooling costs will be improved dramatically by having a builder interested more in constructing a solid envelope than just a thicker one.
Myriad considerations. Don't just make a decision based on the yard salesman's input. Have an analysis run on your house plan that will show the proposed BTU's required to heat and cool the structure with both shells.
*
We have been using 2x6 wall framing here in the northwest in conjunction with the BPA Super Good Cents program for almost 20 years. And our electric rates are some of the lowest in the country and our climate is fairly mild, particularly compared to yours. You should ask your builder to get a copy of the Super Good Cents standards. They show how to save money in construction and increase insulation with smart framing techniques using 2x6 studs, box headers, open corners, etc.
*
Lat I knew Michigan got cold in winter, just like the rest of the Noerthern hemisphere.
Jean, look for previous posts by Gene Leger. He has a method using double 2x3's with 2 x 6 sills that ups the R-value substantially and eliminates the short-circuit of the 2x6. In terms of energy efficiency I think that using 2x6's is the low-end of the spectrum.
Ask your lumber supplier why he likes being addicted to utility providers. You see the two things EVERY HOUSE NEEDS are light and heat. These two connections to your house are like a drug delivered intraveinously. You need them and as a matter of law the price will only continue to go up FOREVER!! How long is forever? It means (no Clinton speak here) forever. Long after you are dead an inefficient building you build will be stealing money from the next owners. I am not saying you should lean over the plate and take one for the team but consider the future impact of your decision. I am not a tree-hugger, I just despise inefficiency. If it were up to me we would ration utility usage, and electric heat would be illegal unless the energy used to transport the fossil fuels exceeded the inefficiency of electricity generation. Now this sounds socialist, but every political system has it's good points.
The overriding problem with todays short sited financial views is that we are only hurting ourselves. Do any of us really need 15 minute stock market updates? So what if it took ten years to pay it back - when you are retired on fixed income the $100 a month you save may quite literally mean the difference between life and death.
-Rob
P.S. - did you guys here it was -70 dgerees F in Alaska last friday!! Assuming 70 degrees indoors that is a Delta-T of 140 degrees!! Yikes!!
*Jean,Rob may be correct that 2X6 construction is at the low end of the energy conservation spectrum, but that I don't know for sure. What I DO know is that I if I did decide to build w/ 2X6's my mindset would NOT be the extra COST OF insulation but rather, the extra OPPORTUNITY FOR insulation. It's really rather elementary.
*Hi Jean.My concern, first, is the strength of the structure.I believe that 2x6 is the smallest size that should be used.Also, use either southern pine or fir. Do not use "whitewood", pine-spruce-fir hybrids.If, in an emergency, or a well-thought-out risk, one has to use PSF, then first test it by throwing it into the air and letting it land on its side.If it breaks, dont use it. If it makes a thud, dont use it. If it bounces, maybe it will do the job for you. And always make sure the builder installs the blocking which belongs between all the studs at about 4' from the floor.Build first for safety, please.Hope this helps.
*Hi alan,Blocking walls is pretty non-existent in my area.Do you really feel it's needed, and why?Steve
*Hi Steve.I think of building a home in the context of assembling a series of planes.For these planes to become a whole, they must be connected.Now, in the case of a wall plane. Nails are attached to the individual studs at the top plate, and again at the shoe plate. The movement of each individual members is then restricted, to some extent.When we add the 3/4" sheathing, the lateral movement for that whole plane is restricted.Without the center blocking, however, the movement at the center is free, over the 8' height. With the blocking, movement is restrained.Now, for practicle application...why is the restriction of movement necessary?At the finish end of any work, the restriction of movement in the framing will eliminate the opening of gaps in the finish. This finish could be just the miters of joinery, or it could be doors and windows, or it could be drywall joints.With the blocking, each stud is connected to each other, across the entire length of the wall. This tends to relieve some of the pressure placed on a drywall joint that might fall rest at the center of a stud within a wall.Think of building a structure like you would if you made a dog-house out of old hollow-core doors.Does this help?
*Hi Alan,Still seems like overkill to me. I run my sheathing (1/2" cdx) horizontally and nail it 4/6/8. This is going to pretty much solidify the wall--unless it could shear at the horizontal joint between plywood panels all the way across the wall (thought would be some trick!)I could see blocking to reduce twisting of studs, or to provide backer for the joint in the sheathing so you have better nail base for siding at that point or even to block the gaps for better wind sealing, or for firestops, but I don't think it would make the entire panel any more rigid.I've heard it is more common practice out west. Where do you work?Curiously,Steve
*Hi Steve.I lived in California for 15 years.Now, I am home , in Cleveland, Ohio.The biggest difference between the two areas, from what I have gathered so far, is that around here they presume that the ground will never move. At all. From anything, even an explosion.I am most afraid of the masonry. Chimneys that wiggle and twist almost in the wind. Nobody worries. And I dont understand.I know that the ground moves. I will always make my connections , rigid connections.I picture the house like dice on the craps table. You gotta be able to shake it. And twist it. And prepare for just one or two foundation walls evaporating. So that the house can just be jacked up and put back on the new foundations.A lot of peace comes in a home that is well-connected.
*AlanDon't put your boots to SPF. Spruce is all we frame with in Ontario, Canada, and I suspect the rest of the country and it does a HELL OF A JOB. It ain't second rate, not by a long shot, and we don't need to sheath with 3/4"ply to make up for any short comings. It might interest you to know that the Ontario Building Code abandonned the need for diagonal corner bracing, wall blocking, and 3 stud corners at least 10 years ago after doing studies into their structural usefulness. Admittedly we don't have to build to California seismic standards, or Gulf coast hurricane standards, but neither, I suspect, do you. Now I usually still incorporate all these elements, but I have a penchant for building in excess of the code when I feel its justified.
*Hi Patrick.Admittedly, I am not impressed with SPF. But, I test my lumber before using it.It is my guess that the lack of strengths, unique to this hybrid, will surface. It is my hope that at such time damages will not be deadly.I understand the need to sometimes put economics first.The species just needs more developement, thats all.
*Now, my understanding was that the blocking served as a firebreak. I believe it is code-required here for that reason, though of course our 60 y.o. house has none (a convenience when one decides to blow in insulation years later). I believe you that the blocking stiffens the wall, but doubt that a stud pinned between sheathing and drywall can move significantly. The greater danger appears to be not compression but racking forces... Is your desire for blocking and objection to SPF & 1/2" sheathing based on actual experience with house failures? Setting earthquakes to one side... Because 2x6's are set 24" OC there is no real strength advantage. Perhaps you are worried here mostly with the minor movements that mess up trim work, the stuff that drives carpenters crazy yet is all but invisible to the average homeowner. Or do you just like lifting heavy sheets (I could lift 3/4" ply, but not all day long -- it would be the greater hazard to my health).Willing to listen, AndrewP.S. Does anyone else have trouble with this software's Edit feature? Like, you keep going back to fix typos or slip in an extra sentence? It is aggravating my neuroses.
*Fred, intersting where you were headed there. Just last night I was commenting about my cousins remodelling job. I said to my wife that "Only in america will people complain about the cost of good windows, better insulation, and more efficient appliances; Then go out and buy a $3500 television set." Maybe it's just me, maybe I am backwards.-Rob
*Hi andrew d.Where are you at, that the fire-block is required?I dont mind 1/2" ply for sheathing, if glued and nailed properly. And, assuming it is void limited and does not come "pre-cupped" and stinky.But I have found that the 3/4", sanded-one-side, is $20 a sheet at the Home Depot. The 1/2" is somewhere around $18.50 a sheet. Handling the 1/2", for me, is harder than the 3/4" because of the greater tendency of the 1/2" to cup.Also, in a remodel, it is nice to have one size ply for all of what needs doing: the floors, the walls (if necessary), the sheathing, the roof, the outside soffits, the temporary cabinets, and so on.Probably you are right about the blocking and racking. I have been installing that fire-block for so long, I have not really stopped to consider all its advantages. But Bob Vila said...the fire-block is not for fire as much as it is for strength.
*B. One does not need 2x6s ín order to have " the extra OPPORTUNITY FOR insulation." One can , for excample, get an R-24.5 in a 2x4 stud wall. Adding external RFBI gives R-34.5....the framing has been ignored with these numbers.
*I'm in VA, though I may be mistaken about the requirement. BTW, 4-ply CDX 1/2" is about $12 here at HD. What gives? Or are you buying ACX? I can understand the efficiency advantage of buying just one stack of plywood.Quoting Bob Vila? What is the world coming to? I can't stand that varmit -- last I saw he was promoting some Robo-something one-size-for-all wrench tool that Sears came up with to mutilate every nut it finds.
*B. One does not need 2x6s in order to gain "the extra FOR INSULATION." One can achieve and R-24.5 with 2x4s and adding RFBI on the exterior gives an R-31.5. Sic transit gloria 2x6s. GeneL.
*Hi andrew d.Good price on your CDX. I have never used that product, so I dont know how it performs. Now, on Bob Vila...Surely, you jest. With that one wrench, a person can throw away all the others. Thats only one wrench to carry, instead of a whole tool box full of misc. That means a person only has to oil one wrench, instead of a whole box full, to keep the rust away.And, if a person carries that one wrench with them, at all times, they can tighten up any wiggling tables they might come into contact with. Whens the last time a tool was able to make friends for you?Bob has shown up on many jobs without fear of the cuts, scrapes and bruises most of us wear long pants to avoid. Have you seen his legs? Not a lick of injury!Whether he is a "varmit", I dont know. I have never heard him discuss his religion.And besides, how could one possibly learn this business without watching his shows? I mean, c'mon!Hope this helps.
*Alan. Do you realise that if building inspectors, and most structural engineers had anything to say about the Voyager, it never would have been built let alone fly around the worls without refuelin?Several years ago, the building department in Andover, Massachusetts received a call from a homeowner concerning his difficulty in tyring to get windows to fit in the house. An inspector was sent to see what the problem was. To his utter surprise he foud the problem was due to the exterior studs. They were 2x3s. Well he decided to investigate further.He found the floor joists were 1x6s. He lifted up on his toes and quickly dropped down on his heels. The floor was solid.This house and thousands more like them were built in the early 1940s.Sixty years later many of them still stand.Are they unsafe?There are thousands of houses built with 2x3s. Are they unsafe?For 70 years the Norwegians have built two story houses with 2x4s. All framing is 24 inches on cneter. In a climate comparable to Canada's no problems have resulted from this type of framing. And what about Homer Hurst's houses built with full width rough sawn 1x lumber? One of his structures was a prize winner in a 1980 HUD competition. It was also selected fotr a construction award in 1981 and was built in 1982. an award ction award, and built in 1982. The house in question is a 36' by 46' 3 story fourplex, located at Houston and Harrell Streets in Blkacksburg,Virginia. Alan, the problem I have is why so many millions of houses are built and continue to be built with "whitewood." I take it that you believe the Arkansas House--except for the 2x6 studs--is a major mistake? As Joe Lstiburek says, "... wood is almost always moving. Wood has always moved and will always move. Nailing wood, screwing wood and gluing wood will not stop it from moving.It is not possible to build a wood walls, floor, roof or foundation and not have it move."Would you still require blocking if the walls were sprayed with spray-in PUR foam? GeneL.
*Hi Gene Leger.Thanks for writing. You touched upon some issues I have been giving consideration to, lately. Steve and andrew d. got me to thinking about why I seem to be taking a position of some kind, in subject areas which, really, may be foreign to me.My building skills were aquired, gained, formed, etc. in California, while I was experiencing my experiences as described in thread entitled "what do carpenters get paid in your area?". Therefore, it is entirely possible that I may have missed picking up something important.I have come to see many different styles, in my time with construction. I have seen that it is vital that the structure created blend with the environment, and surroundings. It might be that I was impressed, somehow, while being associated with building the strongest houses I have ever seen. Could be that I got it in my mind that the extra work involved to make a house stronger is worth it. More than that, should be done.These notions were likely reinforced when coming to Sally's 1920 Colonial Craftsman home and finding it wiggled and sagged and needed emergency help.I employed the methods which I learned in California to "stay" the movement in Sally's structure. That began, and will stay until this job is completed, on this job.Now, the question is, should these techniques which were learned in California be applicable to problems encountered in other regions? So, lets look at some questions and answers, in that regard: 1.Will there be an earthquake in any other region than California, so as to require same "rigid-connection" techniques in structures? If so, what about retrofitting? ANSWER: I dont know. But FEMA has done much research in this regard and has suggested techniques to "mitigate" potential damages from possible causes in an area. If it doesnt cost much more to do it, and its benefits are substantial, maybe its okay to follow the FEMA recommendations. The issues are so serious, I think it better to suffer a little now to make the structure stronger, than to suffer later because unprepared. 2. Is it reasonable to presume gravity as a constant? ANSWER: For those of us who have seen what can happen when that constant is removed, even for a moment, the answer is no. Gravity cannot reasonably be presumed to be completely constant. Gravity can be removed, and is removed, because of even the punk next door playing some wild music out some wild equipment. Any victim of this can attest to the feeling experienced each time one of those sound waves distorts things. And, likely, other things which will come to mind later.Accordingly, I will now state my position to be as follows: I learned how to build houses to be very strong against lateral forces. I believe that the techniques used to make such houses have applications which will improve the quality of building any house. And if someone were to incorporate some of these techniques, though feared to be overkill, they would discover benefits yet unperceived.In other words, if someone wants to know about a technique I may be familiar with, I will happily assist. But I will refrain from suggesting that these techniques are right for everyone.After all, Gene, I am the guy that is building this very strong house, and did not even know how to keep the heat inside before you guys helped me by answering questions on this board.Most humbly yours.
*Hi Alan I can't for the life of me figure out what you think SPF is. Where I live SPF is a grade stamp denoting that the material is either Spruce or Pine or Fir. . . real wood, formerly evergreen trees, not a man made product, not some sort of syvaculture "hybrid". I don't know what kind of superior framing lumber you guys get in Ohio (is it?) but to be superior to Fir, as in Douglas Fir, it must really be somethin'. . . framing with Oak are you? I noted that you also referred to it as "whitewood". Whitewood ,is also known, I think, as Basswood, or Lime; it's a soft hardwood now being used extensively for paint grade trim,as it's cheaper than Pine, and plentiful.I sure am envious of the price you pay for sanded (G1S) 3/4 ply. . .around here my price wholesale is about $40 per sheet, and it's made right here in the province!! No wonder you sling the stuff around like it was 1/4" chipboard!! If you bought your 1/2" ply at a real lumber yard instead of Home Despot they might store it properly and it would be flat like the stuff I usually get, which I pay about $25. for.Just the messenger.-Patrick
*Hi GeneMy high school latin's a little rusty. . . how does Gloria getting sick in transit relate to 2x6's.
*Patrick,Fir, as in SPF, I understand to be from the genus Abies, as in Abies concolor (White Fir), whereas, Douglas Fir is Psuedostuga menziesii...really not trying to sandbag you with the Latin. Douglas Fir lumber usually gets marked as D-Fir, has MUCH greater fiber strength AND is priced accordingly. But I do agree with regard to the plywood.....can't imagine 3/4-inch costing only 10% more than 1/2-inch.
*
Rob,
Couldn't help but agree with you. On your PS; You do realize of course that the Inuit and other artic tribes have been achieving delta T of 140 and more with: 1 afternoon of work, local free building materials, and complete recyclability, all for thousands of years. It is called an igloo and really is one of the most highly developed methods of adapting lethal environments to human use. These igloos can be quite complex with many chambers that are kept at specific and varied temps. The heating was traditionally always an oil burning brasier used for cooking and plain old body heat. Kind of puts us in our place, eh?
Enjoying La Nina at 60d in Kansas!
Lisa
*
Mondo. Let's stop perpetuating the myth that it's OK to space 2x6s 24"oc, but one mustn't do it with 2x4s.
David Edrington. It's too bad that all those who talk about Advanced Framing fail to acknowledge that these techniques came from the Arkansas House. The Arkansas two-stud corner came from, of coures the 1832 ablloon framed house. Savbe yourself some money and see if the library has a copy of my book, _Complete_Building_Construction_ 4th Edition. Read Chapter 11, Outer Wall Framing to learn about the Arkansas House so-called Advanced Framing techniques, and Value Engineering.
Patrick. The original Latin is sic transit gloria mundi: thus passes away the glory of this world.I was attempting to say that when one sees what can be done with 2x4s a compared to 2x6s, sic transit gloria 2x6s--I do not know how to say 2x6s in Latin II by VIs?
Leo Cianciolo. A paster recently contacted me from Michigan. He said that on a spec built house of 2000 sq. ft. he saved 1200 dollars by switching from 2x6s to 2x4s with RFBI on the exterior.He mentioned nothing about the aviings in extended jambs and so on. Now $1200.00 is not a lot of money but it is a good savings nonetheless.If he switches to Arkkansas Houze technique he can run up these savings to as high as 2 to 3 thousand dollars.
Alan. I have no quarrel with your position. What is strong in New England--and we may be too smug here about the strength of our houses-may not be strong enough in seismic 3 and 4 zones in California.
Reading of the story of the origin of Value Analysis, now called Value Engineering (VE) should be required of all residential (the big commercial companies are well aware of VE)builders. You'll find a summarized version of it on page 262 in my book _Complete_Building_Construction_ 4th Edition.
There is really nothing I can add to what the book covers. I ask only that we design and build intelligently rather than build according to the 11th commandment. VE does not question the recent rush to rigidily connect structures. what it does ask is are the dozens and dozens of metal connectors necessary: is this redundancy necessary or is there a leas labor and material method of accomplishing the same result? Recent research by the NAHB Research Foundation shows that much of the metal connectors for shear walls are unnecessary.
We are as concerned as you thjat a structure be strong enough to withstand the imposed loads, but WITHOUT :-] suffering to msake it so. this is the difference between 11th commandment framing and VE building. Much in 11th commandment framing is OVERKILL that contributes nothing to the quality, comfort, energy efficiency, lowered cost of a structure. Jim Locke author of
_The_ Well_-Built_ House_ aregue against sheet rock clips in corners. He want 3-4 stud, solid corners so he can nail the bejesus out of the gypsuim board. When one looks at the load in these corners one realizes that the solid corners bit is so much nonsense. The very rigid UBC California code allow the use of the Prest-ON clip in corners as a replacement for the third stud.Has California taken leave of it senses, or does it realise that received wisdom framing is often nonsensical? . There is a housein Deerfield, Massachusetts built in 1975 that has SIPs and no corner studs. Oh yes, it still stands. Intelligently strongly yours,Gene L. .
*Jean,Forget everything you read here.Hire the best contractor you can find (get two other competing bids.) Check his work, call on his references, let him build his way, if you don't like what's built hold onto your money.Jack : )
*Alan,Top Ten Reasons Why I think you are a Master ____________;10. Less than a 2x6 is a deathtrap? Safety first?9. "They would discover benefits yet unperceived?"8. Blocking in all walls?????7. 3/4" plywood and glue??? Is the whole world in an seismic zone?? 6. 2x6 or die club??5.Emergency wood use procedures???4. SPF (not PSF)... a hybrid??3.How many wood tossers should a contractor keep on the payroll? Is it a fulltime job?2.Whitewood?1. Bob Vila.Have a nice day,Jack :)
*Sorry. I disagree.I believe it is most important to create understanding. For an advisor, or even a discussionist, to advise or discuss, on this most respectable board, the notion of disregarding this board and pursue a course into the unknown world of trying to get someone to do good work within their financial constraints, is unwise, I think.I have been called upon, many times, to clean up after bad contractors. I am part of a balance in such efforts. Everytime someone contracts for the picture they have in their mind, with someone who cannot know what might be in that someone's mind, problems develope. In your suggested scenario, the owner gives up learning through this discussion, and maybe others, and without further developement of understanding, rolls the dice with a builder. No architect, no understanding, just a matter of money.I have read your postings here, AdirondackJack, so I know you can do better. Maybe I just misinterpret your words, I dont know.But in my mind I picture that robot on Lost in Space throwing around his arms and yelling ...WARNING, Warning!Can you see him too?
*Thanks, Gene. I understand.I agree with you that cost is vital. But, for me, it seems, any mention about strength in a building causes an immediate presumption that costs are increased.I have seen people hammering cut nails in a plate, rather than use proper anchors. Where is the savings? And for whom? Someone either has to deal with that as a problem, or something else to ignore.I would think that anyone who had the chance to learn of other methods, other techniques, would jump at the chance so as to improve skills.Isnt that the first reason why we all come here?
*alan,Sorry to be getting under your skirt so I'll explain.You seem to think all walls and "planes" should be built as shear walls are built in your old state California. I never saw such confusing postings in my internet life. We all like strong structures but we all know that shear wall details are way overkill for standard wall construction. And where I live all the extras are a "plane" waste. By the way, 2x4s even on 24" centers or more, work for walls. What's right for hurricane areas is another story and I personally feel reinforced concrete to be best for high wind zones as do a few others.If you want, start a shear wall topic separately so as to minimize the confusion.Jean, Correction to earlier post; Forgetb halfof what you read on b your topic.Have a nice day,Jack : )
*
2x4 or 2x6? Using fiberglass insulation you'll get a higher R value with the 6". You need to calculate the extra costs involved with the 6" and compare that with your energy savings to determine if it is the better value over the long run. Up to two storys I don't think structurally it makes much differnce.
*
B
Useful sandbags are always accepted. . . as soon as I started to read your post the light went on.
*Alan. there is an error in my post on the house in andover, Massachusetts. I said the inspector foubd the exterior wall studs were 2x3s. change that to 2x2s! Gene L.
*Sam Goldwyn? H.L. Mencken? I think it's "underestimating the intelligence" -- "taste of the American public" is an oxymoron. (Oh! The snobbery!) But on the intelligence question, I think "average Americans" do pretty well.Everyone knows someone who buys a new car or remodels every few years whether they can afford it or not. Empty materialism, but it does keep a lot of other people in business.
*Alan. I concur about with you on achieving an understanding. In order to get what I want from framers, I take them to lunch, where we can discuss the project free of phone calls and other problems. As Code Enforcement Officer I always held pre-framing conferences, not common in residential construction. This provided the builder and myself an opportunity to get to know each other. The builder was given a 10 page booklet--prior to the pre-framing conference that explained much of what he would and would not be allowed to do.I provided and encouraged builders to challenge me.Cost is vital, but VE treats it as an element in a system of elements. Too many builders are obsessed with first cost so much so that it overides all other considerations.If you looked only at the initial cost of sprayed-in PUR foam you would throw the saleman out of you construction trailer. However, by looking at all the things it lets you do and eliminate you begin to see that it cost little more or less than FG or cellulose. Whether you opt for this different method of insulating, depends on your willingness to challenge 11th commandment. framing.GeneL.There is another error in my long post to you. I mentioned the house in Deerfield, Massachusetts. Change 1975 to 1725.
*
Alan, I gotta go along with Steve's assertion that the horizontal blocking is just owl killing!
The need for that type of lateral bracing is just not needed. The stresses that you are worried about are rectified with diagonal wind bracing.
If the loads were so great, horizonal blocking would still not be the answer. More, or larger, vertical members would be better.
Additionally, the blocking provides additional conduits for heat/cold transfer. This reduces the energy efficiency and drives up energy costs.
Care must be taken to provide a reasonably, structurally sound strucure, but not at the expense of all other factors! Balance is essential to optimize each structure.
saving the owls,
blue_eyed_devil
"Save a tree: Eat a beaver."
*
Hi Gene.
On Bob Vila's show, I have seen that 2x2 framing. If memory serves me, it was in New England and Hawaii where he was remodeling such.
In those cases, the frame was rotten at the sills. Notably, even though rotten, still standing level, at those points.
From my book, WHY BUILDINGS FALL DOWN by Matthys Levy and Mario Salvadori, on page 289, as follows:
..."...Today buckling is considered a very dangerous structural phenomenon because our strong materials allow us to design thin elements in compression (columns, struts, arches, and domes) that buckle without giving notice"...
I think we have to keep in mind that a building of this sort may be the exception, in most cases. Unfortunately, we do not document why a house failed, so this exception can only be considered an exception because we know there were more people who needed houses at the time those houses were built, than houses of that time which remain today.
And, this too, reminds me of a story...
Back in 1982, when I had my woodshop in San Francisco, I had someone working with me in the shop. He was from Morroco. Every time I asked him how long the job I would assign him was going to take...he answered "one hour".
And he came to work everyday, and I liked him. After work, he would take home the "rippings" from the material used that day. I thought nothing of it for a long while. Then I was wondering what could he possible be using those rippings for. And when I would ask him, he would respond, "making things".
One day, I was invited over his house for dinner. He was the cook of what he said was genuine Morrocan food. Stuff the Morrocans eat with their fingers. But he gave me, the only American, a knife and fork, and everyone laughed.
As he was cooking, I noticed that he had made shelving out of all those rippings, which he laced together with twine, and attached by twine to the wall with a single nail on each side. And he had loaded that shelving with more dishes and kitchen things than I had seen at any of the restaurants I washed dishes at, in my youth.
I was in a state of shock. I told him that I viewed his apparatus to be an emergency. That I would not have given him the material if I knew he would create an unsafe condition with it.
And he kept telling me, "but alan, its doing the job!"
Point being, people have a tendency to used what is available at the time.
Nowdays, I think, we want our structures able to withstand time, the forces that come with time, and any remodels over time.
Having said that, I wonder if, in the creation of that house in Andover, the makers unwittingly developed what we would call a torsion box, after that 2x2 frame. Can you tell me where I might get more information about that design?
*Gene,Can you tell me what is this 11th Commandment framing you speak of?Thanks.
*Hi AdirondackJack.Very good comments. Number three is my favorite!
*
From the look of it, you have plenty of opinions, all of which are worth exactly what you paid for them. As a builder in the harshest climate in the U.S. may I suggest you contact Alaska Craftman Homes Program ([email protected]) and get a copy of their book Northern Comfort, Advanced Cold Climate Building Techniques.
Insulation is the least expensive material you re going to put in the house, yet the most valuable in terms of comfort. If you are an owner builder, I hope you enjoy your project. I liked it so much it became a business.
Another source of information would be the Cooperative Extension service.
Good luck. Alan
*Hi Jean,I've been reading the replies to your question.Itlooks like you are pretty well confused by now. As you can see there is no simple answer. What I would suggest is talking to at least three builders in your area.This will give you an idea of the way they think.I have been in this busines for 15 years and have gone to many seminars on this and others aspects of building.What I believe is the most critical thing to concern yourself with is air movement. Air transfer is the biggest heat loss wether 2x4 or 2x6 construction. There are many places to loose heat that would not occur to even people that have been building for years. A good place to ask is your county extension office or your local electric utility. Electric utilities were required years ago to assist in decreasing heat loss in homes and have come up with many suggestions. Personally I didn't even realize houses were still built with 2x4 any more unless an exterior insulation board is used. I feel 2x6 is stronger and better than 2x4 for many and varied reasons.I don't know what your budget is, but there are many options to explore. good luck.
*
Gregmark,
Please join "payback" topic thread.
Had a nice day,
Jack : )
*Alan,I know you're an FHBer, so what's with all the "Bob Vila in your posts?"Bob Vila and Norm and my early days... Let me tell you what they did on the first show of theirs I watched in reference to a siding job I was about to start in a day. Free help from "TV experts" what great timing! Anyway. So Norm, his carpenter at the time, starts packing machine cut cedar shakes(shingles) as tight as he can to each other. Then he even shows how to trim the odd irregular edge so as to make it fit perfectly tight to its neighbor. Big dilemma for me as the addition I was about to side had to match into existing siding (it all had the proper gaps but they showed gapless as b the way it's done.) Well thank God I didn't install it Norm's way as the job right next door was done his way and boy did those shingles flip out over the next few months. Moral; I like the shows but think this site is above referencing them directly. And it is FHB's Breaktime not the Bob Vila site. I'm not the judge and jury here but think personal experience to be the posts of more interest to all. There must be a Bob Vila site specifically for discussing his shows. Fellow FHBer and really trying not to get up your skirt...Had a nice day,Jack : )
*Jean and Ryan,Ryan...Your post illustrates beautifully what I think is going on in the building industries "change over years" (shall we say the "poly years.") I think we all have 100% good intentions to build homes using the latest methods but don't realize that combining "this good idea" with "that good idea" works about as good as picking out all your favorite things to eat, mixing them up in bowl and diving in. I like pizza or ice cream but not together.As to your post; 100% agree- I've been reading the replies to your question. looks like you are pretty well confused by now. As you can see there is no simple answer. What I would suggest is talking to at least three builders in your area. will give you an idea of the way they think. have been in this business for 15 years and have gone to many seminars on this and others aspects of building. I believe is the most critical thing to concern yourself with is air movement. Air transfer is the biggest heat loss whether 2x4 or 2x6 construction. There are many places to lose heat that would not occur to even people that have been building for years.....don't know what your budget is, but there are many options to explore. good luck. 100% disagree- A good place to ask is your county extension office or your local electric utility. Electric utilities were required years ago to assist in decreasing heat loss in homes and have come up with many suggestions. Personally I didn't even realize houses were still built with 2x4 any more unless an exterior insulation board is used. I feel 2x6 is stronger and better than 2x4 for many and varied reasonsSincerely, enveloped as all...but starting to see the "b Fred L(ight) at the end of the tunnel....Sweet dreams all,Jack : )
*Hey, I saw that exact show by chance a few weeks ago! I was wondering about nailing those shingles so tight on a nice, dry day. What bugs me about the TOH enterprise is the arrogance of the principals -- the "THIS is how you do it, aren't we special" attitude, and the reverence in which they tell viewers to hold the priesthood of "master" carpenters, pros, etc.An exception is Tom Silva: he seems entirely practical, no-nonsense, get it done right, get it done fast -- like I'd like my hypothetical contractor to be.I'll be quiet now.
*Andrew,It's been well over ten years since I viewed that "Shaky Advise Shingle Siding Blooper Show!" This helps prove how misinformation supported and spread by "armchair," "never done it" now "internet enabled expert" information-rebroadcaster types gets around and eventually becomes "gospel."Maybe someone can find their fame and fortune cutting out and reshowing all this errant info and name the show "Worlds Greatest Building Show Bloopers." In fact I better copyright this quick! Any investors out their, send email or cash! Remember to wrap a few sheets of plane paper around it and enclose your email address so that I may thank you and of course I will move your name up on the list....By the way I also love the speed demon no-nonsense man and woman duo though since I'm terrible at remembering names I won't be able to break my own rule by quoting them in "FHB land."Have a good day,Jack : )
*Jean:Just wondering, after all the self important and digressing discussion are you still with this thread? Or, do you even care any more? Guess the Bill & Monica thing isn't the only one that can be yawned to death even though starting with a valid issue.
*Jack,SPF refers to spruce, pine and FIR. I'm here in central Connecticut (one might say, 'near' NYC)and we use it here. The next material that you refer to, ie, 'fir', I assume to be Douglas Fir, marked D.Fir, DFir, or D-Fir, a material with about a 20% greater fiber strength than SPF. It DOESN'T hurt to be very specific when referring to these thangs. It avoids a lot of confusion....but then again, I've known those that thrive on confusion.Brian
*
Actually it was P.T. Barnum, who also said "There's a sucker born every minute." Used to charge people a quarter to leave the circus. How? He put up a sign that said, "To the Egress, 25 cents." They lined up and paid.
*
I think this thread is chasing Pressure Plans for the record. Of course once it breaks 100 posts the board will crash and we'll loose a mess of them.
*Alan. 11th commadment framing is thou shalt not frame anyway but 16-inches oc; thou shalt have solid corners; thou shalt have solid headers even in non-load bearing walls; and the list goes on.Notice, Alam, in all the discussion of 2x4s vs. 2x6s no one offers any structural calculations to show that because 2x6s are "stronger" than 2x4s they are ergo "necessary. Value engineering would akks, OK, a 2x6 stud is stronger, but is it necessary? Gene L
*I read at the Drudge report that Jean wasn't even reading this anymore. And that at least two people on this board have actually spoken to each other. Where is the video??-Rob
*Bman,I used the names commonly used by carpenters that I have talked to but agree with your correctness.With your corrections I may be able to delete and repost...I think we should also point out that the F in SPF stands for a lesser grade of Fir than the commonly used D-Fir grade, right?Out on a limb,Jack : )
*Patrick, I think there are (jump in and help anyone) three main 2x wood framing materials in North America. b Grade (sort of the species).........b Region SPF..........................................Eastern Canada (also used in Upstate New York, but not near NYC,) D-Fir.........................................Western US, Midwest, NYC, NJ, where unions thrive, etc S. yellow pine.............................Southern US, etc Their use however is usually very regional. Much of this has to do with what grows where, makes sense... And lastly on this planet we will (till the internet finishes shrinking the globe) see regionally based individuals proclaim one grade(species) the "best" and forget the rest. By the way, I have picked up the odd lot of crap shipped to me (SPF) and secretly employed the patented Alan "toss it up and see what it does upon arrival back to Earth" method. Don't tell Alan but it works pretty well. Have a good day' Jack : ) PS- This post has been b (B) refined on 2/8/99. Thanks B.
*Gene,Right......The reason grocery bags aren't made of 1/4" steal....but nuclear power plant containment walls are just a tad thicker than 1/4".....My whole building career I have prided myself on overbuilding to the strong side but in the last few years have tried to not "over do it" just for the value engineering reason you mention. The "Seismic it" strength everything idea just threw me off my chair.Going for the record Bill,Jack : )
*Hi JackSo what is Alan using in Ohio( do I really want to ask this question. . . is he still out there?)Which worked well, the test or the lumber?We too get crappy wood, but not weak, or breakable by the Alantest , just propeller grade, and the like.
*Hi Patrick,Alan can tell you but his posts point to...b "Seismic Grade"Fellow "propellor grade" abuser,Jack : )
*You know Fred, that cable thing has always irked me too. The only reason we don't have it is because we chose not to - there are better things to do with our time. I watched a special on PBS about the first round of single mothers getting kicked off of welfare. They were all having trouble of various sorts, the show was actually quite objective (if you ask me the immediate results of welfare reform are of little concern, it's ten or fifteen years from now that's important). When it came time to discussing bills and financial hardship they ALL mentioned cable. It was as if there was no other way to receive electromagnetic waves!!-Rob
*Alan. who knows--the Shadow knows but nobody bothers to ask him--perhaps your Moroccan friend was on to something. I, of course don't advocate using something merely because it works. That it works is only one of a number of criteria it must meet.I have no idea how many 2x2 houses were built. I first learned of them in 1982. And the insulation contractor I used for 20 years had the opportunity to Spray PUR int0 some large buildings construcxted with 2x2.As to why they used 2x2s--why not 2x3s? it was war time and materials were in short supply.Remember that VE originated at General Electric as a result of material shortages.I just called the Andover, Massachusetts building to see if I can get more information. Unfortunately Leo Daley is no longer there nor is his boss, who retired. I'll keep you posted.Finally, we all need to recognize the difference between something just thrown together and a engineered structure. The Arkansas house was engineered. It provided a safety factor in excess of 2 to 1 for load and racking in spite of the fact that it had 41 percent less framing than the FHA MPS 11th commandmment house.GeneL.
*b Topic- 2x6 walls and the extra cost needed just to contain 2 more inches of insulation.Lots of supposition and theoryizing, here goes;Typical spec/building system; 2x6 16" OC, standard friction fit fiberglass insulation, wood exterior sheathing, tyvek; inside poly, 1/2" drywall. No seals used, lots of electric boxes installed, recessed fans and lights, in wall ducting, drilled framing for wires and plumbing runs, inside breathing fuel fired heat...or many b minor variants of same.This "system" seems to be an outgrowth of years old post war "we gotta build zillions of houses, where are we gonna house all the GI'S?", 50's tract house, California boom times, building methods (which spread back across the country as the years rolled by.) The balloon to platform transition (for the sake of time and money) period. There weren't too many Building Science Corporation outfits led by PHDS rather all was done to fill the basic need at the time.Then comes the Arab Embargo days, gas lines, talk of oil supplies running out before you could flip a coin.Lots of experimentation followed but as things settled down its back to the business of selling homes at a price people would pay with systems and crews that were available to do the task.Tyvek took off due to good marketing to the press. 2x6 walls were easy to stomach for the average framer, and cost wise the GCs held the line on labor costs and only really had a small added cost for material.The only real changes made over the period were adding poly, tyvek, and switching to 2x6 walls verses 2x4. And outside air-source heating appliances...Note also that some of us think many of these minor changes (the use of poly, etc)and their misuse by themselves or in unknowing unworkable combinations are leading us into an age of all kinds of b "method induced building failures." Thats where we are today and as far as tomorrow...the business of homebuilding will rule....If the price is right.....then there's a market.b For me, I am not going to build with typical "2x6" construction methods.But I'm not the norm,Jack : )
*
Gene,
I stand corrected or at least expanded upon. It's been so long that I had forgotten about the Arkansas framing system. It is the basis for the Super Good Cents advanced framing details, though I think BPA has made a few improvements. I won't comment on the rest of the issues in your last missive.
David Edrington
*
!!2x4s COST TOO MUCH!!! A few years back my mother had a house built in a retirement community. The houses were 2x4 with r11 and 1/2" foam sheathing in the walls. The attics were r25 FG and the slab had 1" foam around it. I was able to talk the builder into a few upgrades. 2x6 24"o.c. with r22 batts and 1" foam sheathing, Raised heel trusses with 2 layers of r25 and 2" foam around the slab. The improvements added $8 per month to the mortgage each month and saved her on the average $40 a month on her utility bills. So my mother spent $32 LESS a month for a quieter and more comfortable house than her neighbor. My mother did less conserving also, she set the thermostat at 72 deg. and "glued down the knob" while her neighbor used a setback thermostat and wore sweaters all winter and used the a/c as little as possible in the summer.
Personally I find 2x6 as not enough, I now usually build with 9 1/2" or 11 7/8" TJIs as wall studs with blown in cels. I haven't built a wall less than r30 for 20 years.
*b Addendum to my post #25 above.I didn't clearly state what I will be building for the present;b I will build much higher quality walls than 2x4 or 2x6.Clearing the air,Jack : )
*Well it's time for me to interject. I am currently designing an overhaul of my house, one that will I retire in. I intend to use a double framed 2x4 system. Each wall will use studs 24" oc. The plates will be seperated and there will be no wood "conduit" to the exterior.I could downsize the studs to 2x3's (trussed style), but it is not worth the trouble to me.I believe that this system is far superior to 2x6's. The nails that hold the exterior foams, and the resulting convection, conduct a significant amount of heat transfer. I am not going to use any horizontal blocking. I don't mind worrying about an earthquake collasping my house. I have insurance for that. I also am not going to worry about asteroids hitting it because most of the asteroid launchers are pretty bad at aiming. Jean, you can build your walls any way that you want. It is really a matter that needs a bit of calculating to justify each decision. Then you have to justify it in terms of your own pocketbook. Each "improvement" costs, and has payback. Do your homework, then find a pro who will work with you.Do not neglect your comfort value in your decisions. Blue, designing to avoid freezing in MI"Forget the Joneses, I keep up with the Simpsons."
*DAVID EDRINGTON. Thank you for youir comments. I'm not certain that BPA made any improvements to the Arkansas House framing techniques.But I'd appreciate any information to the contrary you have. The problem I have with Super Good Cents (SGC) program and other similar programs, is that as long as the builder meets the performance standards program managers DO NOT CARE:-} how he frames.The result is unnecessary added costs. As the head of one state's SGC program wrote me "the builder can build SGC homes for about $1.00[psf] over conventional practice, and cash incentives usually cover that cost, SO THEIR INCENTIVE TO INNOVATE IS LESSENED."(my emphasis.) GeneL.
*Ron Schoeder. The developers of the Canadian Saskatchewan conservation House did not just out of the blue decidde to use a double 2x4 exterior wall. their choice was the result of analyzing 17 different wall combinations: single stud, double stud wall, most of the common insulations, sheathing or no sheathing and so on. They graphed the results of this study and found that at insulation levels of R-35 the double 2x4 wall, was the least expensive. They found the cost of increasing the depth of the wall was linear. But, the cost of increasing the depth of the single stud wall followed a 2.5 power law--in other words using 2x10 and 2x12s the cost shot off the chart.With the right insulations I can achieve an R-31.5 in a 2x4 wall. GeneL.
*Blue Eyed Devil. In the 1977 8-inch double 2x4 wall of the Leger House, I achieved an insulation R-value of between R-33 and R-35.As I read your post, I wondered if I had know then what I now know, would I have done a double wall? As you may or may not know in 1981 I abandoned the double wall as a brute force, unnecessary overkill method. We needed, I said, better walls not deeper walls. The issue is not performance.It is rather cost. And the unnecessary cost is something the super insulation community long refused to acknowledge.GeneL. An air-tight 2x4 wall with the through-stud convective path broken,and with an R-(insulation)of R-31.5 is mighty tempting. sorely tempted to do a 2x4 wall in which i could achive an insulation of R-31.5 iI Knowing what I have known for many yeras now, I wo know today
*Blue eyed devil. In your 2-13-99 post you say "The nails that hold the exterior foams, and the resulting convection,conduct a significant amount of heat transfer." Do you have any data to support your--or others -claim that the nails "conduct significantr amount of heat transfer."? Note. The issue I am addressing in not that nails don;t conduct heat. GeneL.
*Gene,I like the TJIs for wall studs because of the low environmental impact of them and the cels that I use for insulation. As far as labor, I can usually train a crew in under an hour on how to use the TJIs. Around here cels is A LOT cheaper than PUR per R. Full sheathing is the norm around here because cedar shingles are very common (I use 7/17 OSB even though most builders here use 1/2 or 5/8 CDX). A TJI wall is easy to lift for a small crew. I usually use 9 1/2" TJIs except when I got 800 ft. of 11 7/8" for under $.75 /Ft. from an overrun at an apartment job. The customers really like the wide window sills of the thick walls and sometimes put the curtains inside the window wells. How do you frame a R-31.5 wall with 2x4s?.....24" o.c. with PUR plus Rigid foam sheathing? That would be expensive around here.
*Ron.I have fond memories of the deep window well provided by a 12-inch deep double wall, in the last double wall house I ever built. I just called one of the local lumber yards for a price on 11-7/8 TJIs: $1.94 LF or $15.52 for an 8 footer. A sawn 2x12 8 footer is $10.40 or $1.30 LF. But a KD full widht rough sawn 1 x 12 is $6.00 or $0.75 LF. If you are able to get TJIs for $0.75 LF grab them. Yes the TJI is environmentally preferable.I am certain you have read my many posts on why I changed over to sprayed-in PUR. Agreed that there is a vast cost difference between cellulose and PUR.Of course I did not just say to hell with the price. We all have budget constraints. By rethinking framing and refusing to be bound by 11th commandment framing, I was able to justify the high costs. It allowd me to get rid of the double wall, the labor intensive VDR. Framing everything 24"oc in-line eliminated a lot of lumber. When finished I found that I either had a small increase vs cellulose, or I had no added cost because of the PUR.Finally, is there a better way than TJIs; a way that not only costs considerably less than 2x10s or 2x12s or TJIs? Is the better way also better thermally? I believe there is. so far the better way wall has been done only to a depth of 6-inches. Good for you on the training of people to get what you want. Yes the R-31.5 2x4 wall is 3-1/2 inches of PUR and 1-inch of foil faced RFBI on the exterior. GeneL.
*I'm a bit confused by the typos in your post. I think you are saying that the double wall is overkill. It probably is. I'd have to do quite a bit of research to find that out though, and to me, time is money!I'd easily recover the additional cost of the second wall by staying at work one extra saturday morning. Researching the perfect wall could take me 1000 hours easily!You also challenged my assertion, that the nails that penetrate the exterior insulating sheathings, reduce the energy efficiency.I have no data other than common sense to back me up.Do you have data that refutes that assertion?I'm just a simple carpenter, not a scientist!Blue"According to my calculations, the problem doesn't exist."
*blue eyed devil. The last sentence of my Number 30 post should have said, If I knew in 1977 what I now know, would I have done a double wall? Tree years later I abandonded the double wall as unnecessary.We needed better walls not deeper walls. If we want deeper walls only for insulation reasons then we are misleading ourselves into thinking they are necessary to get higher R-values.You write, " I'd easily recover the additional cost of the second wall by staying at work one extra saturday morning. No offense intended, but isn't this a bad business move? Who pays you time and one half? When Canadian Dave Eyre and his staff chose the double 2x4 wall, it was a result of an analysis of 17 differents wall configurations: single studs, double studs, many different insulations and so on. They founbd the the cost of the double wall increased linearly. It cost no more labor to make the double two feet deep than to make it one foot deep. They found that at insulations levels of R-35 the double wall was the least expensive, way to do it. But the cost of using deeper and deeper studs followed a 2.5 power law. In other words the cost of going from 2x6s to 2x12s went off the chart. After the first Leger House I decided that the double wall was unnecessary. Rethinking framing, and changing over to very expensive but higher R-valued insulation allowed me to eliminate the doublewall and wipe out the difference in cost between cellulose and sprayed-in PUR foam. As noted one can get an R-31.5 with 2x4s, I am not selling a 2x4 wall, but merely trying to show that high R walls are obtainable without 2x6s and the added cost of extended jambs. And even more energy efficiency is had by simply indenting the platform in 4-inches from the foundation edge and putting the 2x4 wall down on the sill plate. This breaks the conductive path between the outer wall and the platform. It further eliminates the need for cutting and fitting RFBI on either the interior of the joist headers or on the exterior. The headers are insulated at the same time as the extrior wall.All the caulking and sealing of these areas is eliminated because it is done at the time the wall is insulated.When I asked you " Do you have any data to support your--or others -claim that the nails "conduct significant amount of heat transfer."? I also put a qualifier after my question: "Note. The issue I am addressing in not that nails don't conduct heat." Nails conduct heat. The question then, is how significant is the amount of heat conducted? There is research on this but I at the moment do not have it handy. It shows, if memory serves, that the amount of heat lost is insignificant. As soon as I locate the research I'll cite it on this page. Tnx for your comments GeneL.
*Okay Gene, you may have a cheaper, warmer method.I'm still going to use the double system. I like the idea of building on a platform. I don't want to increase my foundation wall thickness (10" poured wall with a 4" brickledge). I am going to put in fiberglass batts.I don't like, or trust foams.I might be getting old and senile.I'm also going to put my rafters on 24" centers!How's that for a little living on the edge?Some of your ideas make sense, but I wouldn't frame for you if you were a builder. I like to stick with the oldfashioned Kiss types, even if its all wrong!blue
*well blue dude got to agreed with you. Since none of us are getting younger remember the fuss of double vapor layers of the 70's. Plastic inside and out,result rotted studs in a few years. Time will tell about the use of foam. No one here thinks that air is a good insulator? Did a 4500 sg.ft. with double walls two years ago that used batts for insulation. 2x4 walls top plate was build up plywood top plates. Let me know what you thinks about this
*blue eyed devil. The only insulation I don't trust is fiberglass... but for potential health reasons."Some of your ideas make sense, but I wouldn't frame for you if you were a builder. I like to stick with the oldfashioned Kiss types, even if its all wrong! " I am a builder and hire framers over a long dinner and lengthy question and answer session. They get a free meal and learn what they can expect fromme and whjat is in it for them.Assuming -dangerous-that we both understand the term KISS, there is nothing KISS about oldfashioned framing. It is not an issue of wrong but that it does not comply with KISS.Good luck. GeneL. If the double wall --and performance is not an issue--although a lot of double wall houses are poor performers-were the way to go I'd still be doing them.Good Luck. GeneL.
*Blue,I know this is an old thread but..........Set the floor in another 2" and put 2" RFB around the band. Hang the outer wall out 2" over the foam. The inner wall can be framed exactly like the outer one. If you line the rafters with the studs, you can use a single top plate if you want. Batts are a bi*@h in a double wall, hard to prevent voids. Go with blown in ANYTHING, preferably Cells.
*
We are planning on building a new home here in Michigan. Most homes are built with 2x4 exterior walls, although some are built with 2x6's. This increases the costs for door jams, window extension jams, as well and additional insulation, etc. One local lumberyard said it would take years to payback the added expenses (savings in heating costs). Does anyone have any opinions to any aspect of this? I would appreciate any response.