I have access to free 3/4″ hardwood flooring but the problem is my house foundation is slab on grade. Is there any way to install this wood on concrete?
Discussion Forum
Discussion Forum
Up Next
Video Shorts
Featured Story
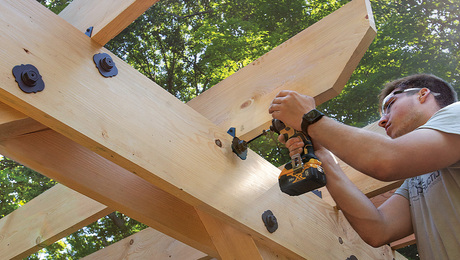
Built from locally sawn hemlock, this functional outdoor feature uses structural screws and metal connectors for fast, sturdy construction.
Highlights
"I have learned so much thanks to the searchable articles on the FHB website. I can confidently say that I expect to be a life-long subscriber." - M.K.
Fine Homebuilding Magazine
- Home Group
- Antique Trader
- Arts & Crafts Homes
- Bank Note Reporter
- Cabin Life
- Cuisine at Home
- Fine Gardening
- Fine Woodworking
- Green Building Advisor
- Garden Gate
- Horticulture
- Keep Craft Alive
- Log Home Living
- Military Trader/Vehicles
- Numismatic News
- Numismaster
- Old Cars Weekly
- Old House Journal
- Period Homes
- Popular Woodworking
- Script
- ShopNotes
- Sports Collectors Digest
- Threads
- Timber Home Living
- Traditional Building
- Woodsmith
- World Coin News
- Writer's Digest
Replies
The only way I've done it was to put down a barrier (two layers of 6-mil poly and troweled on asphaltum), then float two layers of half-inch CDX over that, seams offset, with the layers screwed to each other. Then nail the flooring to the CDX.
It's tough since you really can't validate or depend on a barrier under the slab as being effective.
Moisture/buckling would be a concern going right over the slab.
Much depends on if the slab is on-grade or below-grade. The one I did was below grade. Below-grade is more difficult, moisture-wise.
If it was on-grade you might be able to go right over the slab.
Sometimes in unconventional installations, engineered flooring is a better choice, as is can be more stable and less prone to movement.
How about using dricore under the wood. It will control the moisture and give you something to nail to. Just a thought. I have a stack in the basement waiting for a free weekend to install.
James,
We have installed many thousands of square feet of 3/4 hardwood floors on slabs without any problems. You need to test the moisture of the slab. If it is a fresh slab, you need to wait some time. If it is an old slab, the test we use is to tape a one foot square piece of clear plastic to the floor in a couple of spots. Come back in a couple of days. If there is moisture you probably should not glue directly to the slab but rather build a nailing surface with a vapor barrier between slab and the new decking. If there is no moisture, we glue directly to the slab using Bostick's Best urethane adhesive. Not a single call back yet. Do not use a water based adhesive.
Bruce
I didn't know you could glue down 3/4" wood flooring. Does it matter what species of wood it is? What do I do when I get to the threashholds of my exterior doors. Do I use a reducer?
James,
Back in NY, where I grew up and learned the trades, it was a sin to consider glueing 3/4 to concrete. When I moved to Texas, all they built was slab foundations and I saw many glued floors. I was very skeptical, but we tried it on one project, a 200 sf room. After one year it still looked great, no visible movement, cracks or cupping. So we did a bigger project. It worked just fine. If the floors pass the moisture test and the exterior of the house has good drainage, I do not hesitate to do a glue down. We have done nearly 20,000 sf this way with not a single call back. Please note that these are all above grade slabs and not basements. For threshold and transitions, we just rip down flooring to meet whatever the transition needs to be.
On exterior doors, sometimes the existing thresholds work just fine with sufficient clearance at the bottom of the door. Other times, we have needed to remove the door and raise it up so we have sufficient clearance. Just depends on the specific doors.
Bruce
Edited 10/11/2005 10:18 am ET by Hiker
Edited 10/11/2005 10:20 am ET by Hiker
Man, that is great. I live in Nashville and my slab is above grade and not a basement. I will do the moisture test that you recommended and go from there. Thanks for your help.
Jim
James,
Just a little more info before you jump in. We spend alot of time on the prep work. Usually we are removing carpet, linoleum or tile. The concrete surface must be spotless after removing these materials... even the mastic from the linoleum. Very often the perimeter of the rooms has a coat of latex paint and primer or texture. Again, must be removed to ensure good adhesion to the concrete.
Next, we inspect the floor for flatness. 1/8" over 6' is the maximum allowable, preferably less. If the slab is not flat, we use Custom Level Quik to flatten out the floor. This is the hardest part. If you cannot do it quickly, you end up with a bigger mess than you started with. I recall that level quik is a cement based leveler as opposed to gypsum based. When cured, it is much harder and seems stronger than the gypsum based floor levelers. We also use Level quik because it was approved by the cork flooring manufacturer for one project who specifically forbid the use of gypsum based leveling compounds.
For random high spots, we use a diamond faced floor grinder to bring it down. ( we try to minimize the use of the grinder-it gets to dusty for projects where the homeowner is living) and we avoid a wet grinder as it seems to send water/mud in every direction.
Let the floors cure for several days, a week if you can to help eliminate moisture. Test the floor prior to installation.
I am sure I missed something,
Good Luck
Bruce
When you apply the floor leveler do you use some sort of a screed to spread it in the low spots. Also, to find your high and low spots can I run a string line along the floor at a certain height and then measure the distance from the string to the floor or do you do it a different way?
>If there is no moisture, we glue directly to the slab using Bostick's Best urethane adhesive.Your success with it acknowledged, this is not recommended--recommended against, in fact--by most hardwood flooring providers. http://www.lumberliquidators.com/faq.asp is just one I found quickly, but also told that by the big suppliers I've dealt with locally. Bostik product sheets are a bit ambiguous and I didn't call their tech support, but it's a practice that lots of people recommend against, so caveat emptor to the user. I mention that as a big fan of Bostik's Best.
Cloud,
Before I did that first project with direct glue to slab, we either did the two layer plywood install over felt or walked away from the project. We walked away from quite a few because most houses we worked on could not deal with an 1 1/2 floor height difference. As I checked out numerous successful installations around town, I felt I missing out on a significant opportunity. Still not convinced that a solid 3/4 inch floor was doable, we would do engineered floor installs but I quickly grew discontent with the thin veneers and relatively high prices for the products.
After reviewing the various flooring trade association guidelines, the concern was the effect of moisture on the flooring product and therefore they recommend against it. If slabs were so detrimental, why were engineered flooring manufacturers comfortable with a direct to slab install? So I decided if the floor was dry, then we would give it a go. Many square feet later, I am glad we did.
I am aware of Lumber Liquidators position, and I also know that probably half the 3/4" solid flooring they sell in Austin gets glued to a slab.
This issue was one I worked on for several months and the logic to me was that if the slab was dry, the site was well drained, and the glue also acted as a barrier, why wouldn't it work. By no means am I disregarding the position of the trade associations or the manufacturers. If the slab is not dry we will not do the floor.
This is the first and only area in all the work we do that I have done things counter to trade association and manufacturers recommendations. I have no problems warranting the work we do in this regard and have not had a call back.
I hope this does not sound arrogant or flip. I really struggled with this issue. I learned flooring from an oldtimer in Westchester County NY and I know he would be rolling in his grave. I think much of the basis for recommending against glue on slab comes from parts of the country where the only slab is in a basement subject to highly variable moisture conditions as opposed slab on or above grade with limited variability depending on how they were built.
Anyone else with personal experience in this matter? I appreciate your thoughts on the matter Cloud, and I was hesitant to post my experience, particularly to DIY's that will go out, buy the hardwoods, buy some cheap glue and start slapping it in. I do believe that installed in appropriate conditions with appropriate materials and preparation, it can be successful.
In the midwest, we would never ever glue down hardwood.........mostly because of reasons that you said.
But down here, they put in ALL hardwood floors on slabs with a tar based glue---
Course they only get 2 inches of rain a year here, so moisture isn't much of a problem.
When in doubt, get a bigger hammer!
Edited 10/11/2005 8:04 pm ET by custombuilt
Why would I not be able to float the wood?
James,
Are you speaking of a floating floor on top of a pad-similar to Pergo type installations? I personally do not care for that type of floating floor, just does not feel right to me when walking on them.
Bruce
Yes, but I didn't know if you could float 3/4" floor. I dont know why one could not install 3/4" this way. What do you think? Personally I dont care what it is going to feel like when walking on it because the wood I am using is free. Now if I was buying it that would be another story. I just am trying to find out the best way to install this stuff. So far Ive got some good ideas but floating it would be the easiest method I would think.
James,
The floating floors I have seen have some method of connection between the adjacent flooring pieces, usually some kind of snap and lock or glue together joint. I am not sure that this would work with traditional 3/4 T&G flooring-I have never tried it-again mainly because I do not like the feeling of floating floors. Others may have done this , but I don't think the traditional T&G flooring joint would be verysuccessful because the joint is not a tight fit, there is space in the joint itself on the bottom and in the t&g part- so the only point of connection will be the upper part of the joint.
Bruce
I do appreciate the way you've worded that, and my concern is yours--that someone will make that decision without the experience you've had, without the precautions you take, and without understanding it to be a calculated risk. They'll hear that someone has done it successfully and think, "Oh, cool, I'll do it too!" without concern that circumstances might be completely different. I've done bamboo as gluedown over an elevated slab, but would still leave hardwood gluedown as the exception rather than the rule. That said, do you, as I do, have a love-hate relationship with Bostik's Best? Very effective, but what a nuisance to work with!
Cloud,
Love-Hate is great descriptor-the glue functions great, very tough to work. The other frustration is I do not get any where near the square footage of coverage they claim-I am lucky if I get half.
Just a question to throw out to the pack, aside from moisture issues is there any other valid reason not to glue down to a slab?
Bruce
Edited 10/12/2005 12:44 pm ET by Hiker
i've noticed some of these glued floors that get heavy use tend to pop loose in a couple areas....
When in doubt, get a bigger hammer!
Hiker,
You did great with the moisture test idea. That is exactly what some manufacturers recommend. As someone mentioned, the grade/drainage/gutter situation could possible change the moisture situation particularly with a new home, as could uninformed homeowners who leave the windows open during high humidity.
Back in the old days, it was suggested, in this trade, that one install a cheap sheet floor (I can't remember if it was a Urethane or Vinyl surface) as a moisture barrier for on grade.) Also important, as I think I saw mentioned, was if this was an older slab or possibly not yet fully cured. New homes seem to be plagued by that issue. I do question the plywood subfloor as it is also wood and subject to moisture issues as well, but have not experience to share on that topic. Moisture causes wood to expand and contract as you know.
If it were me, I'd check the manufacturer's website on their recommendations. If in doubt, call the distributor and ask for an "informed" person (usually the sales reps who looks at the problems) who can offer advice. Sometimes the manufacturer is very "safe" in what they will recommend and warranty, but other times, the pros who inspect problems on behalf of the manufacturer, or the seasoned installer, know what might work based on their experience. You don't want to assume liability for voiding a warranty and you want satisfied customers with a great installation.
I commend you for your question and interest in doing the best possible job. That is the sign of a good professional.
I have a parquet entry on grade, for years, and it has performed very well, with no problems, although the home is 70's, so the curing issue was moot, plus it went over old VAT tile which could act as a moisture barrier. We also have laminate flooring installed over both slab and vinyl sheet flooring (adjoing rooms, single looking installation, close to 500 sq. ft.) Both areas have performed perfectly. The dining room had existing parquet (from the 70's?) and it has not fared as well, however, but I don't know why for sure. Some tiles slip a bit depending on the season and humidity. Plus I suspect there was some leakage from the kitchen before we moved in about 23 years ago. This doesn't bother me enough to repair or replace an area we rarely use.
You have good instincts and experience in your locale. It sounds as though you are doing everything you can regarding the moisture issue. You are very wise to check things out prior to installation and should do well. Who needs headaches and liability unnecessarily? One last idea, which may not be the only one, is that Hartco has a 5-ply product that "was/is" warranted as one option for dimentional stability and may have been warranted for below grade, I just don't recall now, and things may have changed. I am not promoting one product over another as I am no longer in the field and there are always new improved offerings of which I am unaware. Again, I appreciate your concern about doing a good job and not accepting conditions for a potentially problem installation. Kudos on being "on it". It's nice to see someone who cares about a good installation. If you and Cloud have good results, you are both on track. Cloud and you seem to have a great work ethic. Great luck to you both. I wish you both many successful installations and no call-backs!
P.S. The D.I.Y.'s need to do their homework or hire a pro. Nobody wants to shell out the bucks for a problem.
Hiker/dtgardengirl,
I have sheet vinyl in my kitchen and about 9 SF of wood flooring at my front door. The house is about 3 years old. If I had moisture wouldn't these floors have problems? I moved in 2 years after the wood flooring was installed so I dont know exactly what kind it is (engineered, laminate, or other) but I know it is glued down.