*
Should there be an air space between an exterior stone facade (4-5″ fieldstone granite) and a 2×6 stud wall? Additionally, any opinion on felt versus housewrap in this situation.
Discussion Forum
Discussion Forum
Up Next
Video Shorts
Featured Story
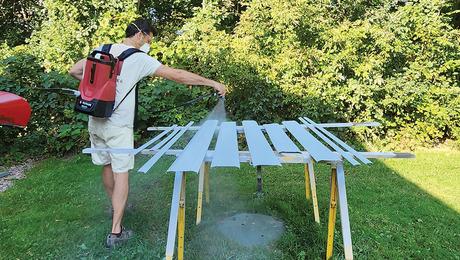
The Titan ControlMax 1650 cordless backpack paint sprayer is handy for medium-sized projects like a shed.
Featured Video
Video: Build a Fireplace, Brick by BrickRelated Stories
-
Podcast Episode 665: Rough Concrete, Good Workwear, and Framing a High-Performance House
-
Podcast Episode 664: The Best of the Fine Homebuilding Podcast, Volume 8
-
FHB Podcast Segment: The Best of the Fine Homebuilding Podcast, Volume 8
-
Podcast Episode 663: Green Stains, Larsen Trusses, and Insulating Behind Stucco
Highlights
"I have learned so much thanks to the searchable articles on the FHB website. I can confidently say that I expect to be a life-long subscriber." - M.K.
Replies
*
Once again, I find myself agreeing with Mongo.
Andy
*Andy,I was hoping that I might be able to find the reason why one says yes or no. Some have said that the air space is not necessary because the granite is not very porous, unlike brick. Any thoughts?
*The granite may not be very porous, but your mortar is. Unless you want water and damp problems, leave a cavity.
*What Mark said. And don't forget to flash the ledge on which the granite rests. Use a flashing material such as stainless steel or lead coated copper that will last as long as the granite.Andy
*Once again, I find myself agreeing with Andy.Mongo
*And don't forget the weep holes and careful flashing around all penetrations.
*My God, I'm agreeing with Bob, too! I'm thinking we've got one reasonable bunch here. Andy
*Just wait until he asks if the space between the stone and the framing needs to be vented...I think we're treading on dangerous ground. I fear that if we reach consensus on any subject, the server may implode.
*Actually, you don't need an air space at all.Due to the irregularity of the stone you will have always some gaps but there is no need for air on the outside of the envelope of a well sealed insulated wall system.Gabe
*Gabe, I think you're right in theory, but the reality is that most masons are sloppy and mortar in contact with the felt or housewrap is a great capillary path. An inch or two of air can avoid this problem.Andy
*Andy,Actually I would go so far as to say it's the opposite.All the loose or excess mortar ends up on the bottom of the cavity, thereby blocking all the weep holes, rendering them useless and should not be considered a viable line of defence.Forgetting all that for the sake of discussion, lets examine where water droplets could come from.Most of the condensation formed in cavities in colder climates would come from leakage of warm moist air from the interior and condensating on the cold bricks. Therefore, having the VB on the inside or warm side and sealing all the possible breaches would do a better job of stopping condensation inside the cavity than simply installing a gap and useless weep hole.Bricks get wet and bricks dry out. Moisture from the exterior masonry touching the wall would not get by the housewrap or felt into the house so where would moisture get into the house?Gabe
*Why felt not house wrap?
*Habit more than anything else. I prefer felt but tyvek is easier and faster for most people.Felt is installed shiplapped from the bottom up and makes a great rain screen when care is taken and still allows the house to breath.Gabe
*Gabe:"All the loose or excess mortar ends up on the bottom of the cavity"How about "Much of the loose or excess mortar ends up on the bottom of the cavity"In my admittedly limited experience in tear downs of brick, there is usually a lot of "oozed" mortar sticking out the back of the veneer. I suspect stone is the same.Also, for water sources, don't forget bad detailing and imperfect flashing.To the extent the EIFS experience can be applied by analogy, a perfect facade won't admit any moisture, but it ain't a perfect world and we need to use a drainage plane to deal with it when errors happen.
*Gabe, I'm not sure if the interior would be the chief source of moisture in this theoretical wall cavity. In your climate, maybe so. And you're right about bricks wetting and drying and about mortar blocking the weep holes. The latter is a reason to argue for a second set of weep holes a course or two up, but still below the top of the ledge flashing.However, I absolutely disagree with your contention that masonry touching the felt (Hey - we agree on felt - Does that mean one of us has to change our opinion? )or housewrap won't lead moisture into the structure. My assumption is that almost any masonry passes water. Perhaps with your commercial experience you've encountered effective waterproofing: I haven't in residential construction. Now, you're an outdoorsman. I'd bet that you've spent some rainy nights in a tent. What happens when you touch the inside of the fabric in that circumstance? You get wet, because you've established a capillary path for the water to follow. The same principle applies to masonry contacting housewrap or felt, without even factoring in the fact that the caustic nature of mortar will degrade the performance of housewrap or felt. So there's one way that moisture can bypass felt or housewrap.I would also argue that moisture in a masonry wall could easily bypass housewrap in the right conditions. I've made this argument before, but I won't let that fact stop me now. Imagine an air-conditioned house with a west-facing masonry veneer wall that's damp from a summer thunderstorm. Imagine the afternoon sun coming back out and heating the wall. Moisture drive is from wet to dry and from warm to cool, so at least some of that moisture will be driven into the cavity as vapor. Housewrap passes water vapor, and it doesn't care if the vapor comes from the inside or the outside, only the drive matters. So, the water gets into the framing in the form of vapor and condenses against the cool surface of the vapor barrier. Now it's liquid water, which can't pass through either the VDR or the housewrap. That's job security for remodeling contractors. Granted, this scene probably doesn't play out in your climate. I'm betting money that it does in mine.Andy
*Andy, I'll have to disect the post to answer."I'm not sure if the interior would be the chief source of moisture in this theoretical wall cavity. In your climate, maybe so. And you're right about bricks wetting and drying and about mortar blocking the weep holes. The latter is a reason to argue for a second set of weep holes a course or two up, but still below the top of the ledge flashing."You would have to have a water buildup of 2 to 4 inches in order for a second set of weepers to be effective, which would require a total failure of your masonry wall to do so. "However, I absolutely disagree with your contention that masonry touching the felt (Hey - we agree on felt - Does that mean one of us has to change our opinion? )or housewrap won't lead moisture into the structure. My assumption is that almost any masonry passes water. Perhaps with your commercial experience you've encountered effective waterproofing: I haven't in residential construction."I think that you would have to rephrase passes water, it absorbs moisture would be more accurate and moisture beads can form on the inside of the masonry wall as well as the outside.The only difference in commercial is the size of the walls we work with. A concrete shear wall 20 stories high covered with any masonry product will be tested to a level residential walls could not.Therefore, if the wall assembly holds up in a 20 storey building, it would be safe to assume that it would perform well in a 1 storey application.If the sides of the shear wall assembly are sealed and you only have the interior cavity to measure, there will be no water coming out of the drain holes in the bottom. Even during the heaviest of rains.Have a break in the seal on the sides and you will experience oozing of water every day between day and night temperature changes.The same cannot be said of a wall assembly on that same building that is made up of interior finishes, structural drywall studs, insulation, air gap and masonry. This would be because of air leakage from the inside. Anyone who has run a dehumidifyer in their house will attest to. You can empty gallons of water per day. Without that dehumidification going on, were does the water go?"Now, you're an outdoorsman. I'd bet that you've spent some rainy nights in a tent. What happens when you touch the inside of the fabric in that circumstance? You get wet, because you've established a capillary path for the water to follow." We've progressed past tents but I'm familiar with the dripping once you touch the ceiling of the tent."The same principle applies to masonry contacting housewrap or felt, without even factoring in the fact that the caustic nature of mortar will degrade the performance of housewrap or felt." Absolutely, mortar will damage any common wrapping. The question is will the damage be measurable enough to do noticeable damage to the interior? And the answer is not likely."So there's one way that moisture can bypass felt or housewrap." (Not to mention the 300 brick ties that make the bridging between the two)And this is also one way that the drying process can bypass the felt or housewrap."I would also argue that moisture in a masonry wall could easily bypass housewrap in the right conditions. I've made this argument before, but I won't let that fact stop me now. Imagine an air-conditioned house with a west-facing masonry veneer wall that's damp from a summer thunderstorm. Imagine the afternoon sun coming back out and heating the wall. Moisture drive is from wet to dry and from warm to cool, so at least some of that moisture will be driven into the cavity as vapor. Housewrap passes water vapor, and it doesn't care if the vapor comes from the inside or the outside, only the drive matters. So, the water gets into the framing in the form of vapor and condenses against the cool surface of the vapor barrier. Now it's liquid water, which can't pass through either the VDR or the housewrap. That's job security for remodeling contractors. Granted, this scene probably doesn't play out in your climate. I'm betting money that it does in mine."My first question to you would be, and so what. What is the volume of water that could be transmitted from the outside to the inside of the cavity on a wall 100 feet long, 10 feet high, 4 inches thick, during a 2" rainfall over 1 hour? I'm starting to enjoy this devil's advocate role all the more.The main consideration in residential construction is that nothing is perfect. You can't build a 2 layered wall without gaps, so what we're discussing is the amount of gap. 1/16th vs 1 inch.The amount of water one could reasonably expect to be produced behind a typical masonry wall would be about a cup per hundred square ft. Not enough to make it's way to a weep hole. A house will cycle as much as 10 gallons per day without anyone noticing.All discussions on building practices boil down to why do we do it, what benefits are there to doing it and what damages can we expect if we don't do it.I like a reasonable gap so that the masons are not impeded by the flaws in the wall to create a plumb and level plane of masonry.Gabe:)
*I actually don't think we're too far apart, Gabe. Building comes down to economic decisions in many cases. Building in redundant systems as safeguards costs money. But in the case of some, flashing, felt and so on, it's not much and the potential cost savings make doing so worthwhile. You wrote, "The amount of water one could reasonably expect to be produced behind a typical masonry wall would be about a cup per hundred square ft. Not enough to make it's way to a weep hole. A house will cycle as much as 10 gallons per day without anyone noticing. " I have no argument with your numbers, as long as the house has the potential to dry out. Some houses could probably handle ten times that, others might begin to rot at one tenth. We build lots of houses without much drying potential. You're dead right when you say that residential construction is imperfect. That's why I argue for redundant systems such as air gaps and felt. And hey, where do you find masons whose work is straighter than that of the carpenters they're following?Andy
*Of course we're not far apart. In reality, I wouldn't consider building without an air gap between the masonry and the wall system.Not because it makes the mason's work any easier but because of the extra measure of comfort it adds. You may not be able to measure the amount but no one will deny that there is some. Any separation between the interior living space and the exterior elements is to be considered a plus. The gap probably does more for energy conservation than it does for preventing moisture damage. Most houses leak enough to allow a substantial exchange of air.The technical requirement for an air gap can be eliminated by placing a foam insulation on the backside of the masonry. This would eliminate the condensation from bleeding through by making the masonry part of the VB system. This is not practical in residential.Wasn't too bad Andy, maybe some day we'll let you onto a commercial site, as a visitor of course.Gabe
*Gabe, there're days when I'd be happy to be there as a laborer.Like the foam idea.Andy
*My 2 cents worth ( and don't forget..with the currency difference it's actually worth about 1 of your cents )Masonry veneer is very common here in residential. ( on a percentage basis, my guess is 90% of residential would be veneer. )One of the things to take into consideration for water/ moisture wicking through to the felt/ pater etc are the ties. Our code requires 3 ties/sqmtr. As the wall builds up, if the mason doesn't wash his wall out at the end of the day ( a common enough experience ) mortar droppings accumulate on the ties and act as a bridge to the barrier. This encourages any moisture/ water entering the back of the wall to wick across to the frame.I've been inside very cheap cookie cutters where the bricks are already up before any board is placed inside and the builder hasn't put paper up ( i.e. you can see the back of the bricks ) on a wet day, and believe me, the back of the brick walls literally run with water. The couple of cups theory is is just that. A theory.The cavity has nothing to do with isulation. it's all about moisture control. Anything bridging that barrier ( including foam ) is only going to encourage moisture problems.
*Andy, some days I'd rather be a labourer myself.Gabe
*Mark,Can't comment on Aussie construction or products. Don't know what kind of bricks you refer to, clay or concrete and I don't know the density.On a good masonry wall, in our climate and location, a cup of water per 100 sq. ft. would be a lot. And that wouldn't be theory it would be fact. The whole picture is required to comment on but if your builders don't install vb or paper at all, don't insulate to our standards or simply don't give a damn, then moisture is only one of your problems.Of course any cavity has to do with insulation, the same would be said about installing storms. Keep the wind and elements off the interior wall system and it's easier to maintain a comfort zone.We have been using foam on buildings for more than 30 years and it's ability as a VB is well proven. To state that foam would encourage moisture problems is ridiculous.Gabe
*hmmmm...perhaps I should qualify that remark. I'm talking about foam without a cavity. That is brick in direct contact with foam. Foams do hold moisture do they not? Brick or block densitys have a bearing on moisture penetration, but once again, the mortar and or the brick/ mortar line is the weak point.
*Mark,No, commercial foams do not hold moisture unless totally submerged for a long period of time. Foams are sprayed directly onto the back of masonry walls and with 2 1/2" application is a type 2 vapour barrier.When sprayed directly onto the surface the bonding of the foam to the masonry make the two components as one and is one of the best walls systems.Gabe
*There is one important issue that hasn't been mentioned here. It is almost impossible to create an air space behind rubble stone veneer. Andy, Bob Simchock will verify this contention. If you want the wall to drain, therefore, you have to install a drainage mat. There are many varieties of these advertised in Masonry Construction magazine.A second issue that has been discussed has been based largely on conjecture. That issue is the amount of water that penetrates a layer of masonry veneer. There is no single answer to this question. It depends on at least three things: the location of the wall, the materials being used and, most importantly, the workmanship of the masons. Some brick walls leak like sieves but some test panels that have been subjected to 100 hours of water driven by hurricane-force winds have shown no sign of leakage.In her excellent study, "Masonry Design & Detailing," Christine Beall states that "Permeation may easily occur in units exposed in parapet walls, retaining walls, and horizontal surfaces, but it is unlikely for ordinary exterior wall exposures if the brick is suitably protected at the top by copings, metal flashing, or overhanging eaves." In my experience, a generous overhang is a good idea when building a brick veneered house.In North Carolina, a state that leads the country in brick production, brick veneer is very common. In the past, almost no one flashed the walls or provided weep holes. The tiny amount of water that made it all the way through the veneer trickled down the inside of the bricks and ended up in the crawlspace or exited via a drain system. (Many houses that I've veneered were built on masonry piers.) Now that builders around here are building full basements and using concrete for the walls, there would appear to be a danger of water collecting at the top of the foundation. In these cases, a drain system with weep holes would seem to be essential; it is, in any event, required by the code here.The frames behind brick veneer walls that I've pulled down (to build additions) have been dry. The only problems I've encountered were caused by negative grade and foundations built too low. All of these were built on crawlspace foundations.
*All those words and studies by others and the bottom line is that in experience, you have found them to be dry. So what was the point that wasn't discussed before?Gabe
*GabeI'm not sure what the method is that you are referring to though it is obviously Commercial ( is it used at all in Residential? )...are we talking a veneer application?..How is the "foam sprayed directly onto the back of the masonary walls"?i "Moisture between the brick veneer and the block wall, caused the brick to deteriorate. In turn, the moisture corroded the ties securing the brick veneer to the block wall and the shelf plates and angles supporting the brick. The mortar joints in the brick veneer showed major cracks.Water entered the wall through the cracks.The air-vapour barrier did not perform well and after water entered the wall, the UFFI (Urea Formaldehyde Foam Insulation) absorbed and held the water inside the wall. Residents complained of cold, drafty apartments.The excessive moisture in the wall decayed window frames and caused leaks."From this report of building problems in Canada, it would seem that foam does hold water. Note the subsequent problems associated with moisture penetration. Definately more than a cup per 100 sq/ft, wouldn't you say?regardsmark
*Mark,Know the building well and all the players involved.The foam we use is from BASF and is Polyurethane. It has a water absorption of less than 1 percent .62% to be exact.The building in question failed because of the poor design and execution of the Hasbro system. The Architects and Engineers in question were invited to a little courtroom dance and settled their dance cards before the actual dance nite.This example is not typical of buildings in Canada or anywhere else for that matter. It's an example of what happens when the bottom of the class gets the same title and ring as the top half.Gabe
*Andy,One last example to throw a little monkey wrench into everyone's theory.Examine an old stucco wall and explain how the lack of an air space plays out here.Gabe