*
I’ve heard this a thousand times, but I can look at a commercial slab (like in a Home Depot) and not see any. What is done differently and why can’t it be applied to residentual work?
Discussion Forum
Discussion Forum
Up Next
Video Shorts
Featured Story
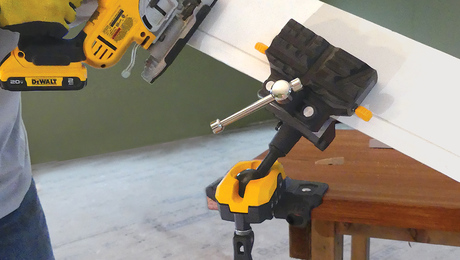
The IQ Vise has angled jaws, a simple locking mechanism, and solid holding power.
Featured Video
Video: Build a Fireplace, Brick by BrickHighlights
"I have learned so much thanks to the searchable articles on the FHB website. I can confidently say that I expect to be a life-long subscriber." - M.K.
Fine Homebuilding Magazine
- Home Group
- Antique Trader
- Arts & Crafts Homes
- Bank Note Reporter
- Cabin Life
- Cuisine at Home
- Fine Gardening
- Fine Woodworking
- Green Building Advisor
- Garden Gate
- Horticulture
- Keep Craft Alive
- Log Home Living
- Military Trader/Vehicles
- Numismatic News
- Numismaster
- Old Cars Weekly
- Old House Journal
- Period Homes
- Popular Woodworking
- Script
- ShopNotes
- Sports Collectors Digest
- Threads
- Timber Home Living
- Traditional Building
- Woodsmith
- World Coin News
- Writer's Digest
Replies
*
Great Question! I would like to know too.
Top ten guesses are;
10. Home Depots are new. Give it time.
9. The floors are poured thicker, expansion joints properly employed.
8. They use professionals not carpenters.
7. The subs have done a few right before.
6. Home Depot checks references before hiring.
5. The sub doesn't add so much water that it looks like soup.
4. They really do slump tests.
3. They use better than 2000 psi concrete.
2. They never pour on uncompacted fill.
1. They have the luck of the Irish.
Really going for a walk in the "Park" now, after I check my pretend stock game site!...
Jack : )
*Dave,I believe that all concrete cracks. I agree with ADK Jack's in that the slabs at HD are new, and have properly placed control joints. A control joint allows the concrete to crack in controlled locations. I worked for 5 years for a design build firm that promised crack free concrete floors. To do this we used post-tensioning, with well engineered slumps, mix, etc.. The crews were all highly trained. Still by the time I left 2 years ago, we were starting to get call backs to fix cracks, not an easy thing to do with heavily tensioned cables running through the slab. There are too many factors and variables to keep a slab from cracking, the best we can to is to control the cracks. Fortunately the old marketing VP whose idea it was for the crack free floors left before I did, and who knows how all the floors are doing today.
*
Here in central Florida residential slabs are often (usually?) poured at at least a 8" slump over plastic, left without any curing membrane, plastic or watering in the hot sun. Sometimes they crack and sometimes they don't.
I've also seen professionally cast slabs on span deck where they followed all the rules and they cracked 1" off of and parallel to the control joints. My experience with concrete cracking can be summarized 'sometimes it does, and sometimes it don't'
greg
*Dave, All concrete doesn't crack but rather all concrete can crack. When it does crack most times there's a reason. I like Jack's point of view, theres a lot truth in it. I think a point there is that residential practices mimic rather than replicate those of commercial although there should be no difference. As far as concrete in residential construction it's least understood and greatly misused and that's testamony to what an enduring product it is. If you keep in mind that you only have one chance to take all the measures that you can for good concrete, you will find yourself exploring the simplest failure to see if there is solution. I gave up on the "all concrete cracks" theory in 1984 and have successfully poured about 90% of my concrete crack free. Heres few basic things that make a big difference. 1) Proper compaction of base materials and this can't be accomplished with a track machine or backhoe bucket. 2) Non-structural slabs should float and not adhere to walls and avoid tieing into walls and foundations. 3) Learn about the three joints of concrete construction and use them wisely. 4) Apply a co-polymer sealer ASAP to all slabs particularly when a vapor retarder is used. The directions should state that application can be made as soon as the surface water has evaporated. At 15-20 dollars a gallon it's costs can't be considered against it's benefits. Also I never use less than 3500psi concrete. There's alot to learn about concrete, it's a remarkable product. Good luck, Keith
*Keith and ADK have good advice. Iwould add my 2 cents: Crack free concrete is not a crap shoot. First , know and trust your supplier. Learn how to read a concrete batch ticket and specify a water/cement ratio. Aside from concrete strength, the water cement ratio is one of the most important parameters (along with proper joint design) to assure your concrete reaches its design strength and remains crack free. I'm mostly experienced in commercial construction where a independent test lab is on site to take cylinders, check air content, w/c ratio, etc, beyond the budgets of residential construction. But there is info. available (check your local tech book store) or contact ACI (Am Concrete Institute) for pubs which will serve as good primers for assuring quality control and quality assurance. And if your supplier can't maintain QC, reject the load-it gets their attention fast. A good supplier is used to maintaining QC, but often knows he can get away with lax standards in residential-don't let them.
*I think you have it wrong! OOOPS, dare I say that? I think originally the expression was "All concrete SHRINKS". As it cures and dries (remember that "high early strength" concrete only attains 75% of its designed strength after 28 days - - - are slabs refered to in the feminine gender? - - - ) concrete shrinks. The two key words to remember are separate and control. If not properly separated (from adjoining walls, structures, slabs etc,) and controlled (with the proper placement of control joints and expansion joints), you will get those cracks which we all hate to see. You will probably get cracking in a slab with good control joints, but you just won't see them.The other important factor, as pointed out earlier is the proper compaction of a UNIFORM granular base.But hey, I'm no concrete expert, I just picked those tidbits up from a concrete seminar.
*AJ's top ten are right on the money, especially #'s 8, 5 and 2. I cringe at the thought of residential concrete work. Foundations are poured on uncompacted soil and 24 hrs later the forms are stripped to have the semi-cured concrete "bake" in the sun, severely reducing it's strength and weathering ability. Then our local "fine home builders" do their thing. The foundation is then backfilled in one great lift to then consolidate over the course of several years with surface water draining towards the structure as an end result. And to think they actually accept money for this "quality" construction. The building is only as good as it's foundation!!!
*
What do you concrete gurus think of adding fiberglass strands to the mix? In addition to, not instead of, the usual steel. I know a builder who swears by it but I've never tried it.
*
Dave, Although fiber is said to increase compressive strength,I think it's only short term and I don't see any need to use it together with wire. In fact haven't seen anything that's impressed me enough to use it at all. Nothing replaces proper means and methods for a particular application. I read fiber was first used in the 60's by the Army Corp of Engineers (that also doesn't impress me)and don't know that they still use it. My concrete's stuck on steel. Keith
*All this talk about concrete but no-ones mentioned steel!Having constructed several slabs, some 60ft by 30ft, with monolithic pours, our steel work was extensive to say the least.We also made the concrete suppliers responsible for the mix and strength at 28 days and 128 days by demanding 'contracts to supply' to a required standard! As Fred so rightly says "learn to read a batch ticket". Anyone want to scan a batch ticket onto this page and we'll all get the info correct? Or perhaps FHB would like to run an article in the next month or two!!!!!!Happy Valentines,
*Adding fiber to concrete DOES increase it's compressive strength, it also decreases "microcracking" due to shrinking during the curing process. Whatever you do, make sure the concrete is covered for at least a week while it cures. Most contractors won't want to hear that. The idea is to keep the surface damp for as long as practical. Concrete shouldn't dry like pottery, but gets it's strength from a chemical reaction called hydration. This requires water. Believe it or not, in the right environment, the concrete will continue to cure for years!!! Cool stuff!!!
*
I've heard this a thousand times, but I can look at a commercial slab (like in a Home Depot) and not see any. What is done differently and why can't it be applied to residentual work?
*
MDuval: The toughest concrete I've ever seen was in a cave in Sequoia National Park. A WPA project in the 1930's installed a trail and in that wet, 100% RH cave, the concrete has been curing and getting stronger for 60 years. -David