I’m thinking of purchasing a tig welder to weld sheet copper and aluminum. I would like to find a 110V machine. I have 240V in the shop, but I envision using the rig on site where only 110V is available. Any tips, ideas?
Discussion Forum
Discussion Forum
Up Next
Video Shorts
Featured Story
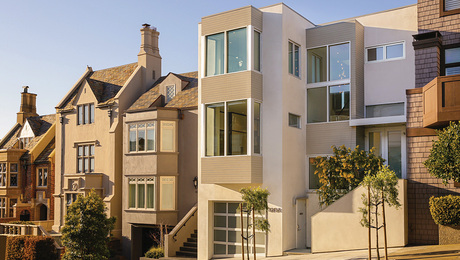
A sleek, modern redesign maximizes space and light while preserving the building's historical charm.
Featured Video
Builder’s Advocate: An Interview With ViewrailHighlights
"I have learned so much thanks to the searchable articles on the FHB website. I can confidently say that I expect to be a life-long subscriber." - M.K.
Fine Homebuilding Magazine
- Home Group
- Antique Trader
- Arts & Crafts Homes
- Bank Note Reporter
- Cabin Life
- Cuisine at Home
- Fine Gardening
- Fine Woodworking
- Green Building Advisor
- Garden Gate
- Horticulture
- Keep Craft Alive
- Log Home Living
- Military Trader/Vehicles
- Numismatic News
- Numismaster
- Old Cars Weekly
- Old House Journal
- Period Homes
- Popular Woodworking
- Script
- ShopNotes
- Sports Collectors Digest
- Threads
- Timber Home Living
- Traditional Building
- Woodsmith
- World Coin News
- Writer's Digest
Replies
http://www.chaski.org/homemachinist/viewforum.php?f=12&sid=df1ab677b3897350f2bfb60e236762f4
have fun just learned around a year ago i'm having a blast...........
" No matter how flat the pancake , there are always two sides"
Edited 9/12/2007 7:29 pm ET by alias
Nice forum. Thanks, Kent.http://grantlogan.net/
"he ot the placed closed down whyyy thhhattt nnooo gooodddd" - sancho
From what i gather 240 are better than 110 , because of versatility and recycling issue's . Again have fun and be safe ..." No matter how flat the pancake , there are always two sides"
The only problem with AL. is that you need AC to weld it . You can use DC but it is much more difficult and it needs to be spotless since you don't get the cleaning action with DC.
I have never seen a 110v AC machine for tig. That doesn't mean they don't make on. I like Miller machines personally but thats just my preference. Check Miller or Lincolns sites for info.
Headstrong, I'll take on anyone!
Since posting, I've been reading up and it appears a MIG might work for my application. Aluminum is not my main focus - copper is. My welding experience consists of arc welding steel. Any thoughts?http://grantlogan.net/
"he ot the placed closed down whyyy thhhattt nnooo gooodddd" - sancho
I've never heard of MIG welding copper? Do you have a reference? Actually now that I think of it I've never heard of TIG welding (actually probalby brazing) copper?
Thought the wife really want's a fancy-pants TIG welder (part of the reason why I married her) and if we could TIG copper that would be a bonus.
Daniel Neumansky
Restoring our second Victorian home this time in Alamdea CA. Check out the blog http://www.chezneumansky.blogspot.com/
Oakland CA
Crazy Homeowner-Victorian Restorer
If you just figured out by "reading up" that mig is for you instead of tig, then I'd suggest you need to read up some more. There's a vast difference in the methods and the reasons why one would choose one over the other. If you want real help you should tell a more complete story: what do you want to weld. That is.... thickness of material, alloy of material, is this structural or decorative, how "pretty" must the weld be, are you doing a lot of out of position welding..... and on and on. On the other hand if you just want to get going without a lot of fuss, then mig is the choice. One can be taught to weld steel with a mig machine in maybe ten minutes. You won't be good, but you'll be able to stick metal together. But with tig, be prepared to spend all day before you get any kind of bead.
If you just figured out by "reading up" that mig is for you instead of tig, then I'd suggest you need to read up some more.
I didn't figure anything out. I just got more info that suggested that TIG wasn't my only option. That's exactly what I said.
There's a vast difference in the methods and the reasons why one would choose one over the other.
That's why I'm asking. I know very little. I'm trying to learn enough to wander into the proper forum and ask intelligent questions. I've visited a number of welding forums and they don't appear to be very beginner friendly.
What I'm wanting to weld is sheet copper -no alloys. Mostly decorative. I solder this type of stuff now and am very good at soldering. But occasionally, I have a project where I don't want the solder to show. Out of position stuff is likely. Thankshttp://grantlogan.net/
"he ot the placed closed down whyyy thhhattt nnooo gooodddd" - sancho
try this :http://www.shopfloortalk.com/forums/showthread.php?t=12105.." No matter how flat the pancake , there are always two sides"
That's the ticket -Thanks.http://grantlogan.net/
"he ot the placed closed down whyyy thhhattt nnooo gooodddd" - sancho
Take a look at this site: http://www.millerwelds.com/resources/ Info for both MIG and TIG, weld calculators, and a whole bunch of other stuff.
Dinosaur
How now, Mighty Sauron, that thou art not broughtlow by this? For thine evil pales before that whichfoolish men call Justice....
Mig welders generally feed the welding wire through the cable to the "stinger" by having a drive mechanism at the welder which pushes the wire through the cable to the gun/torch. One of the problems with MIG welding with soft metals such as aluminum (and I would assume also the case with copper) is that the aluminum wire is often not stiff enough to get pushed through the cable to the gun. To avoid jambing, you may need a "push pull" system where there is a motor drive in the gun which pulls on the end of the wire at the gun while it is being pushed through the cable at the machine. Unfortunately, these push-pull guns are expensive. Another option is a "spool gun" in which the drive mechanism is a separate unit that is placed close to the item being welded and thus requires a much shorter cable than the standard push system. Also expensive. If you get lucky and get a good cable (preferably one with a sheath designed for aluminum welding) you might be able to get by with minimal problems.TIG welding generally gives a much more attractie welding bead and produces less distortion to the materials being welded (assuming it is done correctly). Since the welding wire (rod) is fed by hand into the weld puddle by hand, there is not the problem of the soft material getting hung up in the feed mechanism. There is the problem, however, of being coordinated enough to smoothly feed the rod with one hand while handling the torch with the other and adjusting the welding current with your foot - something I have not yet totally mastered (the coordination required is something like patting your head and rubbing your tummy...) Welding students often practice at length to be able to smoothly feed the rod along their gloved hand by manipulating their finger to slide it along. There are 110v TIG units available, but I assume that you would be limited to something like 1/8" thickness. You can do a web search on "110v tig welder" or similar and find some units. As with a previous poster, I am a fan of Miller welders, but I haven't checked to see if they make a 110v unit. One thing to watch for, particularly on a 110v unit, is the duty cycle, which is the amount of time in any ten minute period that you are supposed to be able to weld. The rest of the time is supposed to allow the unit to cool down. I have seen 110v MIG units with a duty cycle as low as 10% for the rated maximum power - which means that you are suppoed to be letting the unit cool for 9 minutes out of every ten - which means that you had better have a rich fantasy life to avoid geting bored out of your skull while attempting to weld...
You might want to check out this site: http://www.artmetal.com/They are lightly traveled at times but the members do mostly the kind of welding and fabrication that you seem to be interested in. I have welded bronze with both mig and tig but not copper by itself. My text book indicates that copper and it's alloys are mostly readily welded. Pure copper appears to be the easiest to weld with some alloys nearly impossible. You will want to do further research. To save yourself a lot of grief.... purchase the best machine you possibly can. Don't get an inexpensive rig from a chain store to just get by for while you're learning. Welding with poor equipment is a recipe for frustration. Included in my gotta have list are an auto-darkening shade, and good supple well fitting gloves.
I have mig, tig and arc experience but never heard on mig on copper. Mig is great for steel but is a colder weld than arc. Tig is a very precise welding. You can weld thin steel and aluminum. With multiple passes you can weld as thick as you can imagine. I've done up to 1" but it takes days. I'll look into tig for copper but I've never done it.
Headstrong, I'll take on anyone!
I found you can tig copper with DCSP (direct current straight polarity). You need Argon a your shielding gas.
Headstrong, I'll take on anyone!
Would this me fusion welding or using a rod? If so what type of filler rod would you use?
Hurray this could be justification for a nice tig rig...
Daniel Neumansky
Restoring our second Victorian home this time in Alamdea CA. Check out the blog http://www.chezneumansky.blogspot.com/
Oakland CA
Crazy Homeowner-Victorian Restorer
Either way. They make copper filler rod. I found the way to tell in tig if you need filler rod is if the weld will me undercut or shallow in the puddle then you need rod. Don't add to much rod or the puddle will be to thick.
Headstrong, I'll take on anyone!
I haven't done much TIG aluminum other than "messing around", and I have never done copper, but I would like to.
That said, I do know that welding either, especially copper, will take quite a bit of heat- current.
I also know that the quality of the welding machine is directly related to the amount of money spent.
Options for 220v site power include a cheater cord wired into the panel, an independent generator or an engine driven welder.
I believe the major manufacturers (Miller and Lincoln) both have entry level light duty machines that run on 110v.
I HAD the perfect welder your looking for. It was a needle arc plasma welder made by LINDE Corp. Great machine. I had it for several years, never had a need for fine welding, only 10 amp max, up to 1/32. I thought it would be great for metal art work. The machine I had was made in late 70's, Geezz It was heavy! 100 lbs? Water cooled and 110 volts.