I am in the process of putting down a new floor in an 8.5 ft x 13.5 ft enclosed back porch. The existing floor is 3/4″ t&g porch decking with a 1/4″ layer of oak on top. Because the room was built as a porch the floor slopes away from the house. I have leveled the floor with angled 2″ wide sleepers anchored into the exiting floor. I left the old floor in because the sleepers run perpendicular to the flr joists so the floor makes a solid base for the sleepers. I plan on putting a 1/2″ subfloor on top of these, finished with 3/4″ t&g walnut. The floor joists are 2x8s that run the length of the porch – a 13.5 ft span. Each joist is notched in from the top by 1in. (x3in. wide) to allow for heating pipes. All are pretty close to 16in. OC. Do I need to worry about my joists holding the addtional flooring along with a couch, TV etc.? Thanks. Jim
Discussion Forum
Discussion Forum
Up Next
Video Shorts
Featured Story
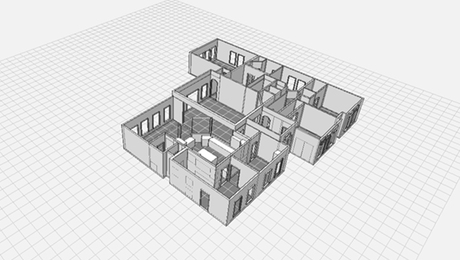
Hover's smartphone app offers an easier way to get precise 3D scans.
Highlights
"I have learned so much thanks to the searchable articles on the FHB website. I can confidently say that I expect to be a life-long subscriber." - M.K.
Fine Homebuilding Magazine
- Home Group
- Antique Trader
- Arts & Crafts Homes
- Bank Note Reporter
- Cabin Life
- Cuisine at Home
- Fine Gardening
- Fine Woodworking
- Green Building Advisor
- Garden Gate
- Horticulture
- Keep Craft Alive
- Log Home Living
- Military Trader/Vehicles
- Numismatic News
- Numismaster
- Old Cars Weekly
- Old House Journal
- Period Homes
- Popular Woodworking
- Script
- ShopNotes
- Sports Collectors Digest
- Threads
- Timber Home Living
- Traditional Building
- Woodsmith
- World Coin News
- Writer's Digest
Replies
A 2x8 @16-inches OC as a floor joist will span up to 12'-3" based on a 40 psf floor live load. You need the 2x8s at 12-inches to span 13'-6" you indicated.
Also, where is the notch located with respect to the joist span? If it is in the middle third, this worsens your situation.
Can you add a center beam, some posts and foundations underneath?
Notches are 7 inches outside the middle third of joists. This is a second floor porch with an identical room below so there's no way for posts or foundations. First floor porch is over a crawl space so there's a 6x6 lookout post running under the center span of those joists. If I tear out the old floor I stll won't be able to put additional joists in because there won't be enough room between existing joists to drop in a 14 footer wihout tearing up the walls. Not an option. The house is about 70 yrs old so the porch has been this way for awhile. I actually just removed a 6+ foot radiator that sat center span running between 2 joists. Probably about 300 lbs. Soooo, without any forseeable solution, how bad is it to go with what I've got??
You are overspanned, especially with the notches taken out.
but this floor will not suddenly fail and hurt you. What it will do is vibrate when you walk across it and gradually develope a sag to the middle.
If you can't reframe or add a bean midspan, just get used to the idea that not all houses are perfect. You can invite friends up to see your conversation piece..
Welcome to the
Taunton University of Knowledge
FHB Campus at Breaktime.
where
Excellence is its own reward!
Don't do it until you have given this more thought. You have an old joist system with some weak areas. You have T&G and oak and sleepers and you want to add some more 1/2 inch and a 3/4 layer on top of that. Go to the Home store and buy a sheet of each layer you want to add; get an estimate of the weight; and then calculate the total weight by converting the square footage. Then consider the dead and live loads that will be applied to the porch. It sounds like a recipe for a problem. If it is feasible to tear out what you have, it might be better to consider I-Joists. I-Joists with about a ten-inch thickness should not be much more expensive than your present solution. Also, they should easily carry the load. Use your present floor system for other purposes, even firewood, but not to carry the additional load.
KAORISDAD is right on - 2X8s won't reliably span that far.
One must magnify and pay honor to the pure, and the innocent, and the righteous, and to the learned, to whatsoever people they may belong; and condemn the wicked and the men of iniquity [Genghis Khan]
Could you possibly cut the joists somewhere and add a beam and take it accross the 8.5' width to a couple of posts in the wall? I think you might need a 6x8. It might be worth your while to hire an engineer to provide a solution.
Otherwise, your floor, at least in my neck of the woods won't pass building code requirements.
What wood species are your joist ? By chance are they Net 2x8's?,, I suppose if you have some type of wall space, you would be able to kick up with some 2x4's at apprx. 45 degree, then wrap those 2x4's with something to match, that is if, you feel comfortable transferring the load to the side wall. Be Safe, Jim J
Don't know the species and they're cut to todays standards:13/4 x7. No room for 2x4's @ 45degree angle
MBEAR9,
After reading all of the threads, I have a couple of ideas for you. Only one would allow you to pass code, however, it might not be possible. If you have access to the joist system, you can double every other one even if you can't tuck in the joists on the ledge. This can pass code in most places. the other approaches are to plate the joists with 3/4" plywood glued and screwed to take the bounce out and strengthen the 2x8's especially were they have been notched. Since the porch has been around for 70 years, a strengthening approach would be a better solution.
Good Luck,
Benny
How old is this structure?
I usually see the type of porch you are describing on older, pre WWII houses when joists were bigger (much closer to actual 2x8 and made from stronger wood, and longer floor spans were the norm.
I think it unlikely it will give you any troubles, but cannot guarantee that, of course.
(If it _is_ an older house, I'll betcha that _everything_ is overspanned and by today's standards you are obviously living in a collapsed pile of pick-up sticks {G})
_______________________
Tool Donations Sought
I'm matching tool donors to a church mission to Haiti - we're shipping a bus converted to a medical facility in (now it looks like) April and can fill it with clothes, tools and all sorts of stuff needed in that poorest of all countries. A few hand tools or power tools can provide a livelihood for an otherwise destitute family. Please email me if you have tools to donate.
Thanks to Jeff and David and Jim and Rich and Steven and Mark and Jason and Shep and Jen and Mike and Joe and Bill and Ken for their offers!
Several donations have arrived! Thanks and God bless!
Right. I don't know why anybody is bringing up code issues. This floor is already there. grandfathered and time tested. The only thing compromising that is that it has since been notched and now a little extra weight being added. overspanning sligthtly doesn't cause catastrophic collapse. it just allows more deflection..
Welcome to the
Taunton University of Knowledge
FHB Campus at Breaktime.
where
Excellence is its own reward!
>>I don't know why anybody is bringing up code issues.
I think it is the nature of our biz to think in terms of current codes since they have such a direct impact on what we do today and how we do it.
I remember one of the first inspections I ever did was of an 1880s house in Sweickley (sp?) PA with a slate roof. When I stuck my head through the hatch into the attic I almost panicked - the roof rafters were 2x4's spanning probably 12 ft horizontal more or less and spaced may 2 - 3 foot OC.
"My gosh! This roof could collapse at any moment!" was my first reaction!
Fortunately, I realized that wasn't the case (and the house had survived pretty well for a century or so) before I came down and made a complete fool of myself!
_______________________
Tool Donations Sought
I'm matching tool donors to a church mission to Haiti - we're shipping a bus converted to a medical facility in (now it looks like) April and can fill it with clothes, tools and all sorts of stuff needed in that poorest of all countries. A few hand tools or power tools can provide a livelihood for an otherwise destitute family. Please email me if you have tools to donate.
Thanks to Jeff and David and Jim and Rich and Steven and Mark and Jason and Shep and Jen and Mike and Joe and Bill and Ken for their offers!
Several donations have arrived! Thanks and God bless!
As Bob and Piffin said, If you are happy with the feel of the floor, I wouldn't worry too much about current code. And, as you add more layers of flooring, it's gonna make it stiffer. On the other hand, you said it was an open porch and was then converted to a closed in porch. As long as you are adding more dead load to the structure, and it was originally designed to support only the open porch load, I'd consider getting some framing anchors, joist hangers, etc and shoring up the framing connections a bit. Especially where the floor system is connected to the house and to the support posts. $10 worth of brackets and nails and 1 hr labor would be cheap insurance. Maybe even some reinforcment where the joists are notched to prevent sagging in the future. When problems happen, it's not usually that the lumber fails (breaks), more that critical load points come apart. And, if I read you correctly, and it is a 2 story porch arrangement, take a look at the understructure of the lower story floor system too.
Edited 1/30/2004 10:34:02 AM ET by DIRISHINME
I was wondering if glueing and screwing a 1/2" layer of plywood to the bottom of the joist would help the floor at as a box beam of sorts. Just a thought.
"Life is what happens when you are making other plans." - John Lennon
"And, as you add more layers of flooring, it's gonna make it stiffer."
This was my initial thinking for keeping the existing floor, in addition to having a solid base to secure my levelers since they run perpendicular to the the joists. The joists are not "joined" to the 6x6 beams but actually sit on top of them so I'm not worried about joint failure, just about the additional stress of adding 1 1/4 inches of new flooring to exiting joists with a 13.5 foot clear span.
Old lumber seems to be much stronger. I say that because looking in my attic which has managed to survive since 1916, hurricanes & all - are 2"x5" rafters ~28" o.c. Your testimonial about the 300# heater at mid span helps alot too.
Curious: If this was a porch, why did it have a heater?
If your floor framing is accessible from below, and you really want to get crazy, you could sister microlam joists to the existing joists. Obviously, this could be done from above too if you are tearing off the old porch floor. Otherwise, I agree with what others already said.
Old lumber is definitely stronger due to tighter growth rings that were common to the mature trees....that's not a mistake, it's rustic
""Old lumber is definitely stronger due to tighter growth rings that were common to the mature trees.
That's a pretty broad statement, but is mostly just a myth. While it may be true in some cases, it certainly isn't that simple.
The old lumber could be virtually anything - From poor quality ungraded white pine to clear solid oak. They may have been commercially bought lumber that was graded, or something someone cut out of their Uncle's pasture.
All old growth lumber doesn't necessarilly have tight growth rings. The tight grown rings indicate a slower growing tree. Any given tree may grow slowly or quickly depending on the fertility of the soil it grows in, how much sunlight and water it gets, competition from other tees, etc.
The typical lumber you buy now is graded and has set quality standards that weren't in place 40 or 50 years ago. It's strength is a lot more predictable.
So I just don't buy this "old lumber is always better" arguement.When cheese has its picture taken, what does it say?
I believe that you are wrong. Old lumber was stronger and wood does gets stronger over time. The code span tables keep getting changed (reduced spans) since new growth wood is less than older framing.
Boss ain't wrong. The GRADE is what matters, old growth, new growth..grade is grade. Fast grown Red Oak is much more resilient then slow growth with tighter grain patterns , and conversly old, SLOW grown heart pine is more resilient to piont loads then newer FASTER grown pine.
Just because wood is older does not affect the strength in ANY way...I have been at this a long enough time, to know.
Grade. thats a period.
Go Stab yourself Ya Putz! Ya think I Parked here?
Sphere is correct. Only concrete gets stronger over time (and not enough to matter). Wood only changes with moisture content, assuming no rot or excess moisture....that's not a mistake, it's rustic
>Only concrete gets stronger over time
Still looking for the growth rings in my concrete. Should I be pouring old concrete or new?
:)
You'd think he's talking about Limburger
Who ever invented work didn't know how to fish....
If you keep picking through your concrete looking for rings, your dome is going to roll over. You'll need a heck of a lot of drywall screws to put it back right....that's not a mistake, it's rustic
old wood looks like this...
Go Stab yourself Ya Putz! Ya think I Parked here?
Hah, I love it. Was that taken before or after you crossed?...that's not a mistake, it's rustic
Boss,
Older growth lumber is stronger, when comparing among the same grade and species. That is fact. What is sold today as Structural Select would probably have been graded No. 1, or even No. 2 50 years ago.
I do agree with you that since old lumber is not marked, you have to assume grandpa hacked the log from the yard. Unless a sampling of members are removed for testing, you have to use the weakest grade capacity for the material. Of course, that assumes an engineer analysing the old house can tell douglass fir from southern yellow pine. That's why I like steel. ...that's not a mistake, it's rustic
"Older growth lumber is stronger, when comparing among the same grade and species. That is fact. "
Not a fact - Just your opinion.
And my opinion is that you're wrong.If we are here to help others, what are the others here for?
I'm witcha Boss...
Go Stab yourself Ya Putz! Ya think I Parked here?
witcha
Is that like possesed???
Who ever invented work didn't know how to fish....
Is that like possesed???
You have to ask? Look at what he bought. <G>
PAHS Designer/Builder- Bury it!
Hey now..I re assemble that re mark..Ya know , old slow grown oak is almost impossible to bend with out fracture , where as faster grown STILL old is a bit more springy..IN OAK..I am not preachin to the choir I hope. In pine the exact oppisite is true...old, new, whatever it has a lot to do with growth rate..and can be verified by a book by Roy Underhill..The woodwright shop guy..I forget which book I have 3 of them in storage, may have been his first one.
Go Stab yourself Ya Putz! Ya think I Parked here?
Whaaat? I love your house. Last one I bought similar to it, I promptly pulled a demolition permit. County bureaucrats were apoplectic. 100 yr old house- very important, but not yet an "Historic Property" (now is). Everybody was happy when I sold it before razing. Looked like a money pit to me. My profit was on the land.
I understand about the growth rates. My only point is that I've seen no evidence that "old growth" was synonymous with slow growth. Clearly a lot of modern softwood structural lumber has been grown very rapidly, intentionally.
Looked up what Hoadley (Understanding Wood) had to say. I haven't read Roy, nor am I likely to. Caught Hoadley at a national woodworkers conference a hundred years ago. Every presenter there was hanging on his every word.
Conifers: "width of the denser, stronger latewood is least affected by changes in growth rate. As a tree grows faster, however, the wider rings have a greater proportion of earlywood; as the growth rate slows down, earlywood is narrower. The wider rings of fast-grown softwoods therefore will be weaker on the average. Growth rate, usually measured in rings per inch, is extremely valuable in visually stress-grading structural softwood lumber.
Hardwoods: "In ring-porous hardwoods like oak and ash, the width of the large-pored earlywood doesn't vary much, so the rate of growth is reflected in the amount of denser late-wood. Therefore, fast growth produces denser material. Among diffuse-porous hardwoods, growth rate has no predictable relationship to strength." "In ring-porous hardwoods, the faster the growth, the stronger the wood." The pictures show how this is.
Which I believe brings the crux. Hardwoods are what I've seen and understand. They're the historic structural wood around here, being all that was available. Anybody living in a softwood area may very well have had the other experience.
Hoadley doesn't mention, but I've seen the change in texture of newer and older hardwood, especially the difficulty in nailing. It can't be explained solely by moisture content. I've got a meter and used it. The USDA's "Wood handbook: Wood as an Engineering Material" goes into great depth about the effects of moisture cycles the wood endures and the effect on nailing. Also about strength properties. I'll spare you the details. PAHS Designer/Builder- Bury it!
Tom, In essence we are in total agreement..Hoadly's work has been very valuble to me as a way of furthering my understanding of what went awry, and why. Fast growth pine is WEAK...er. 'Brash ' oak is weak. By brash I mean the loss of early wood or more the absence. Weak and flexilbe are not interchangeable words.
About my house..I was just kiddin..now, hard f 'in wood? yup..and try to pulla 100 yr. old cut nail that was driven in green (wet) white oak..impossible. Unless, it got real wet and corroded out a hole.
I think that strength..in wood is a measure of elasticity vs. brashness..it all depends on how the load is applied and what we expect from it.
I would also have to write a book maybe to explain myself..an it's almost kick off!..basically, we are in agreement.
BTW..Mike Smith is gonna buy me and DW Dinner when Carolina wipes up the game..
Go Stab yourself Ya Putz! Ya think I Parked here?
Sphere,
Actually if you give a good whack inwards on on of those old nails they free up and are quite easy to pull out.On a hill by the harbour
I will try that today..thats what I am doing.
Go Stab yourself Ya Putz! Ya think I Parked here?
What is sold today as Structural Select would probably have been graded No. 1, or even No. 2 50 years ago.
You can change the grading any time you like (a grader once worked for me). That doesn't change the way trees grow. There is nothing valid in the "old growth = tight rings" mantra. On our property I can see the difference between trees in different growing areas. Some are close-ringed, some wide. Has nothing to do with age. Further, having dealt with a number of 100-200 yr old structures, out of curiosity I measured the rings. No difference from today. Fast growth areas yield fewer rings/inch. Slow growth areas yield more. Pretty simple.
Boss and Sphere are correct.
As are you, about the steel, if there's much load to carry.PAHS Designer/Builder- Bury it!
Boss
You can have all the opinions you want, however, the National Timber grading for wood species has repeatedly lowered the allowable bending stresses on typical framing lumber over the years for the same grade.
...that's not a mistake, it's rustic
Edited 2/1/2004 1:23:27 PM ET by Bungalow Jeff
I'm, not necessarily gonna get into that of old groth lumber is better discussion, but will say that "whens ya drive some spikes in thems 100 yr old 2x4s they be as hard as a honeymoon d*!!!
Edited 2/1/2004 11:51:19 AM ET by DIRISHINME
"Curious: If this was a porch, why did it have a heater?"
Maybe I should be a little more specific. Porch is attached to the back end of a brick two flat, a common element to small, multi-family buildings here in Chicago. The structural framing consists of 6x6 vertical timbers for the outside corners of the porch connected to 6x6's horizontals at each floor and roof, that run back and are built into the wall of the building. Joists for floors and roof sit on top of these 6x's. Finished framing was then sheathed in 1x6 and finished on the outside with a charming asphat shingle/siding. Inside walls were generally left uninsulated and unfinished. Each porch has a few windows and an oversized radiator for those owners wanting to utilize the room in winter. Fifteen yrs after buying the place I've finally gotten to that part of the honeydew list that leads me to my question and a great reason to spend some quality time at Breaktime.
Aren't ya glad ya asked! ;)
Jim
certainly
Aren't ya glad ya asked! ;)
Don't mean to dwell on the structural integrity issue too much, especially since you said:
"The structural framing consists of 6x6 vertical timbers for the outside corners of the porch connected to 6x6's horizontals at each floor and roof, that run back and are built into the wall of the building. Joists for floors and roof sit on top of these 6x's."
Sounds very strong, although it's a little hard to visualize, since it's not what I would consider standard construction (by todays standards). One very basic building concept that I think escapes many novices is that a major part of what gives a wooden framed building structural integrity is when materials are stacked on top of each other - that way the nails just kind of hold things together, but are not actually load bearing. In other words, anytime you have a load bearing framing member attached to the side of another member, nails are not enough - bolts (preferably thru-bolts) or framing anchors (joist hangers, brackets, etc) are required. A perfect example of this is attaching a deck or porch to the side of a house; you can't just nail it up there, It's gotta be bolted, or otherwise tied back into the structure (which is the best way). This sounds like it is well addressed in your structure.
That said, I have one question: Again, you said "6x6 vertical timbers for the outside corners of the porch connected to 6x6's horizontals at each floor and roof" What is the connection between the vertical and horizontal 6x6s? Are the horizontals sitting on top of the verticals, or are they connected to the side of the verticals? Matt
Matt: The horizontals are notched into the veritcals at a 45 degree angle.
Jim
Edited 2/3/2004 10:41:57 PM ET by MBEAR9
Hey- Span is too great to be rock solid...just like everyone is saying. But if you are close to your dirt on the bottom side of the 2x8's you can post each of them at center to a pier pad or paver. You only need to post & beam it if the porch is like 3+ feet up, and then it isn't too difficult. If you have any sag existing, use the beam and a hydro. jack to take out some. Engeneering is probably a little overkill- unless your TV is from the 50's and the couch made out of steel & stone.
Eric
in the Evergreen State
I've read all the mesages, and here is my take on it. I agree with Piffin about the bounce/failure issue.
What the extra layers do is help to distribute the loads over more joists which should also help mitigate the bounce problem. Bridging, if it is there, helps to distribute loads as well.