I’m looking at insulating my Attic. It previously had holes drilled in the attic floor and 7″ off insulation between the attic floor and the room ceiling. I’m probably going to go with blow in on the attic floor. My question is more about the soffit venting and the situation that I have. The baffles that come pre made are 23″. My roof rafters are all different sizes 19-25″. I was thinking about just nailing a 2’x8′ 1/2″ thick either polyiso or polystyrene foam board to the rafters spanning a couple (instead of between each rafter) . Any thoughts or reasons this wouldn’t work? I have about a 1″ gap between my soffit area and the deck of the attic. Would moist air rushing past this from the soffit up to the attic be an issue? Any advice or previous experience would be much appreciated. Thanks
Discussion Forum
Discussion Forum
Up Next
Video Shorts
Featured Story
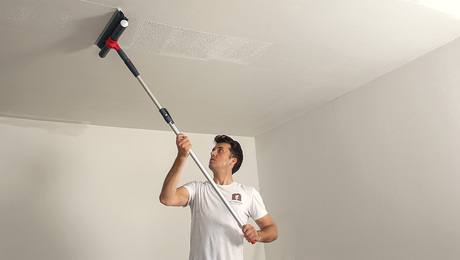
Skim-coating with joint compound covers texture, renews old drywall and plaster, and leaves smooth surfaces ready to paint.
Featured Video
How to Install Cable Rail Around Wood-Post CornersHighlights
"I have learned so much thanks to the searchable articles on the FHB website. I can confidently say that I expect to be a life-long subscriber." - M.K.
Replies
What would fastening 1/2" polyiso boards to the underside of your rafters (particularly after insulating your attic floor) do for you?--besides waste your money and further tax the environment for no reason.
Second, you may want to do yourself a favor and review the principles of a developing a proper thermal envelope appropriate for your climate zone (which you completely ignore in your request for advice here) on a building science website...or pay for a professional energy consultant that can help you look at your complete building envelope as a thermal barrier that achieves (at least) code minimum comfort while avoiding risky condensation issues. My guess is you will have to pay for specific advice catered to your existing conditions rather than try to get proper advice here for free. You may not realize it, but there is a vast number of people that perform that service professionally. Which means they make a living doing so. If it were found otherwise for free on building forums like Finehomebuilding, then that wouldn't make for a very wise career choice--wouldn't you think?
Additionally the two photos you supplied don't tell a complete story that could even render good advice. And the third one was just a waste of upload time and server space. No personal offense; just being honest.
The polyiso would keep the insulation from filling between the rafters. This would allow air flow to travel up the soffit along the roof deck and out the ridge vent. I thought it was pretty clear what I was trying to accomplish when I mentioned the baffles. I don't really want to use gable end vents to vent the attic unless that's the consensus. I've talked to a couple local insulation contractors and unfortunately they mostly just want to spray foam the roof deck and have a sealed house (This is very costly at the moment). I don't like the thought of having an unvented roof deck with black shingles. I didn't mention my location that was my bad... I'm in NW Ohio so climate zone 5. The last picture is showing the 1" gap at the attic floor out to the soffit. Just to give everyone a visual pictures speak a 1000 words. I was just looking for a little guidance to steer me in the right direction. If a majority of the people on here would say no that won't work you need to vent through the Gable ends then I would have a baseline on what I need to read more about. I believe in having some basic understanding of things before just telling a contractor yep do what you think is best. We don't have a code inspection on air sealing or insulation in my county. I'm not asking for a 3-D drawing and an estimate just trying to learn.
I think I understand what you want to do, and it seems like a fine idea.
more insulation on top of the attic floor is a good idea. You could lay unfaced batt insulation if you like, or go for the blown-in.
You also have a good idea to maintain the attic venting for the good of the roof deck.
For most of the year water vapor from the soffit vents will be much less than the vapor that comes from the heated air inside the house that makes its way into the attic, cools and when the attic temperature is below the dew point, condenses inside the attic, where you do not want it. Remember warmer air has a much higher capacity to carry water vapor.
In the damp, hot summer, If you run air conditioning to reduce the temperature inside the house below the dew point, at some place you will have water vapor condense inside the insulation. But as long as this is short term, it will evaporate as the weather and seasons change.
For these reasons, air sealing wherever you can is a worthwhile effort to reduce this airflow from inside the house conditioned space. adequate volume of venting air
The only drawback to placing something under the rafters at the low end to keep insulation from blocking the venting path is that it will not allow additional insulation at above the wall, or at the end of the attic floor nearest the outside walls. Purchased or site-built baffles that allow an inch or so of space below the roof deck also allow the rest of the space in the bays between rafters to be filled with insulation where this helps insulate the attic floor at the edges.
There are rules of thumb for attic ventilation, (1:150 for vent area to attic floor area) and as long as you have enough net free space for venting at the soffit and at the peak, you do not need more at the gable ends.
https://www.finehomebuilding.com/?s=roof+venting+area
Lots of fine reading related to this subject.
UncleMike42:
"In the damp, hot summer, If you run air conditioning to reduce the temperature inside the house below the dew point, at some place you will have water vapor condense inside the insulation. But as long as this is short term, it will evaporate as the weather and seasons change."
I don't believe this is true. Water vapor will not condense within polyiso; particularly 1/2" polyiso in climate zone 5. In order to avoid condensation issues from leaking cool air meeting up with hot, moist summer air you probably need north of R-10 for any part of your building envelope structure that is susceptible to creating condensation issue. 1/2" polyiso is maybe an R-3 at best--and a perfect condensation surface for water vapor to become liquid and/or bulk water. Because polyiso is relatively vapor impermeable, chances are it will condense on the underside and drip down to wherever your iso board ends (because you probably wont be able to fit it all the way down to soffet in such a way as to have bulk water evacuate your structure) under certain dew point conditions. And chances are it will drip onto materials that, unlike polyiso, "care" about moisture. By that I mean they readily absorb moisture (like wood framing and trim; paper faced drywall, etc.) which can possibly lead to propagation of mold; particularly as you intend to fasten it at an angle that promotes run off from surface accumulation. Any potential run off into a cavity could prove very problematic because you only need an R.H. above 70% in a relatively trapped cavity to lead to increased wood and paper pulp moisture content through absorption. In turn, these food materials that, again, care about moisture take on a higher fiber moisture content (MC) level. Mold, like any living organism, merely needs a sustained moisture source to survive and propagate while feeding on the cellulose fibers. That can happen over the course of a few damp weeks.
This why I believe you should consult with an energy audit company along with contracting with an insulator. Most insulators are not aware of condensation and dew point dangers and it is difficult to hold them accountable for future damage which can develop and worsen over years. Most simply want to sell material and labor and they will point out that they performed exactly as you specified; your problem, not theirs (if they are even still in business). To be fair, some insulators are knowledgeable and point you in the right direction. However, since you are reaching out to this forum for free, it doesn't sound like that's the case. Its good that you are providing more information and I see that UncleMike is truly trying to be helpful. I'm sure he is knowledge on a number of building issues, but even he does not see the complete picture...and probably never will. The details of your roof lines and depths are all critical factors which have been totally ignored with his advice. The way you use your home is also critical and that has been ignored as well. A building science website will help you understand the basics (hopefully for free) but again, a professional energy auditor that can visit with you on site is your best course for due diligence protecting and improving the comfort of your home which is such a huge asset.
Even though you may think I am being negative with your approach, I am, indeed, trying to help you as well. As an Architect and 40 yr remodeler, I've seen all kinds of bad mistakes made with poor insulating jobs (particularly retro-fits) resulting from the lack of understanding of the basic physics (mainly that hot moves to cold, wet moves to dry, and high pressure moves to low pressure) involved with each uniquely built, and oriented, dwelling structure. Again, a professional home energy auditor will help guide you through making the best decisions for your particular home, IMO. Good luck!
"I see that UncleMike is truly trying to be helpful. I'm sure he is knowledge on a number of building issues, but even he does not see the complete picture...and probably never will. "
I am not sure at all where you formed you opinion of what I do or do not know, or how your crystal ball shows what I may or may not learn in the future.
How would it be if we try to focus on the subject at hand?
I think you did not read the original post.
he has an attic floor, which has holes drilled into it and blown-in insulation between the attic floor joists, below the attic floor and above the ceiling below. this insulation is 7 inches thick.
(7 inches could result in somewhere around R20) codes are more like R49.
He is contemplating additional insulation blown in on top of the attic floor boards, and is asking how to keep this additional insulation being installed from flowing against the roof deck, and blocking the flow of ventilation air from the soffits.
His proposed use of polyiso is to retain the additional blown in insulation by being installed on the lowest two feet of joist surface. It does not sound to me like he wants to cover the underside of the roof with foam board.
My comments relate to the net sandwich on the attic floor of blown in insulation, on top of a gap-filled wood deck, on top of blown-in insulation. At some point damp air will be inside this sandwich below the dew point. But with a proper ventilation ratio area, this should not be a huge issue for his climate zone.
I agree that consultation with local technical help is a good idea.
Oh, I read it. If he leaves the attic floor in place and blows insulation on top (not sure why you would do that vs. laying down batts-- but that is a moot point as I will explain) it will not be that effective. It would seem that the floor joists are 2x8's. Blown in insulation, even with the best of work, result in about 75% fill. After settlement, my money would be on a net fill of about 5" at best. That leaves a 2"+ air space between the existing insulation and the old. This air space (with no air seal anywhere) short circuits the effectiveness of the two layers of insulation. Its like wearing a sweater in a cold snap and suspending a thermal jacket above your head to keep warmer. It just doesn't work. Convection is working against you. Thus, I would argue, with the extremely air permeable fiberous insulation layers + soffet venting channel that won't be well sealed, you've cut the effectiveness of the new layer of insulation by half, at best. Any way you look at it, it is not very cost effective insulation strategy. The best thing to hope for with a cheap improvement is find some fiberglass batt insulation that someone is recycling and lay it up as tightly fit together as possible and cardboard baffles the positive venting path. Heck, put 30"+ of it up there if you can find it cheap. Keep criss-crossing batts if you can.This would be a fair improvement with no possible negative health effects to occupants ...or the environment. Bear in mind that by keeping the existing floor in place, that 2" air gap will always be working against you.
Besides all that, I understand that he wants to keep blown in or batt insulation away from roof deck for positive roof venting. My original point was (and remains) that Polyiso is just not the best product with which to do it. Scored cardboard in "V" shaped configuaration between rafters would work just fine to maintain positive venting and allow additional fiberous fill. Recklessly introducing a virtually impervious sheet membrane within the thermal envelope layer is costly and needless; we live with far too much needless plastic in the world. Polymers have a huge negative impact on the environment. That is NEVER factored into is manufactured costs. Nature always has paid the factored price. Most folks don't give this a second thought...and have been indoctrinated to believe it should be used as much as possible. It shouldn't. For that matter, I would argue that spray foam falls into the same category. It is way overused and oversold. Im glad this (wisely) was dismissed for this job. Besides all the continuous off-gasing health issues (closed cell), just wait till all these spray foam jobs need to be remodeled. What a nightmare. This thread brings up all those issues that folks should really do well by themselves (and future generations) to consider. I always welcome a difference of opinion around which we can learn. But I hope we are, at least, on the same page there.
Cheers!
Those attic insulation baffles also are pretty easy to cut. Would be a bit of fussy work to measure, cut and install, but another option.
The long-winded explanation of why cellulose would be bad, but fiberglass would be good wasted a lot of this thread (In my humble opinion). :-) All the reasons against adding cellulose because of convection and air gaps, blah, blah, and finding lots of recycled fiberglass batts, are removed by simply knocking the existing plugs out and topping up the existing cellulose to eliminate the air gap, then adding additional cellulose on top of the floor. And use cardboard for baffles, no need to use expensive polyiso.