Here’s my story
Ok, the wife wants a family room in the basement. All moisture issues have been corrected, cracks fixed and inside perimeter drainage installed. Humidity runs around 50% and the walls are below grade. The house is in Delaware. Pored foundation walls are solid, well sealed and painted but not very straight. I taped sections of 2 mil plastic to the walls in two different areas to check for condensation. Nice and dry so far, (about 3 weeks now.
Option 1,
Vapor barrier against the inside of the foundation wall, (6 mill poly or visqueen) then use 3 ½” steel studs floor to ceiling, (to avoid the rough finish of the concrete) then un-faced fiberglass bats and finish with drywall.
Option 2,
¾ eps foam glued to foundation wall,(remember it’s very rough and the foam won’t lay flat) followed by the steel studs, un-faced bats and drywall.
Option 1 is defiantly less expensive, and it’s what I want to use but I have read some bad press on this type of installation. The whole vapor barrier/black mold/cheese factory argument is really hurting my brain.
Any ideas??
Thanks Bill
Discussion Forum
Discussion Forum
Up Next
Video Shorts
Featured Story
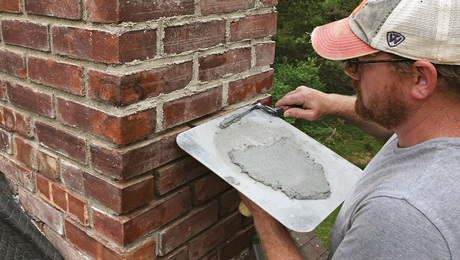
Old masonry may look tough, but the wrong mortar can destroy it—here's how to choose the right mix for lasting repairs.
Featured Video
Video: Build a Fireplace, Brick by BrickHighlights
"I have learned so much thanks to the searchable articles on the FHB website. I can confidently say that I expect to be a life-long subscriber." - M.K.
Fine Homebuilding Magazine
- Home Group
- Antique Trader
- Arts & Crafts Homes
- Bank Note Reporter
- Cabin Life
- Cuisine at Home
- Fine Gardening
- Fine Woodworking
- Green Building Advisor
- Garden Gate
- Horticulture
- Keep Craft Alive
- Log Home Living
- Military Trader/Vehicles
- Numismatic News
- Numismaster
- Old Cars Weekly
- Old House Journal
- Period Homes
- Popular Woodworking
- Script
- ShopNotes
- Sports Collectors Digest
- Threads
- Timber Home Living
- Traditional Building
- Woodsmith
- World Coin News
- Writer's Digest
Replies
I would insulate totally with Styrofoam without a vapor barrier just to avoid the "mold thing", but your challenge here is the non square walls. One author, Bruce Harley (Insulate & Weatherize), suggests that you first put 1/2" Styrofoam against the wall and then frame out using fiberglass batts without a vapor barrier. Even with this technique, he suggests that towards the floor (xx" -you make the call) use Styrofoam (vs. fiberglass) in the event of basement flooding. Another tip is to use cement tile backer board (no mold friendly paper facing) on lower half and leave 1/2" - 1" gap between the floor and the bottom of the dry wall to avoid moisture wicking up into the wall structure; use non wood composites (e.g. vinyl) for your baseboards.
Another consideration is the existing paint on the walls? - Is is a theroseal type product? If so, with a leaky vapor barrier, moisture could penetrate & condensate between it and the cold wall.
There seems to be no right answer to this. The opinions are across the board.
I've been struggling with the same thing for some time. The arguments that make sense to me seem to come down to:
VB against wall:
- keeps any wetness to the outside. Excess water will gradually seep back out through the concrete.
No VB against wall:
- water will continue migrating to the inside (if you use a dehumidifier)
Local code calls for the VB, but I don't like it for the same reasons you do. I've decided that all basements are/will be wet at somepoint, so don't trap it.
I've decided to go with glued pink EPS up against the upper 4-6' of the wall (leaving lower 2 ft clear...because a) the least amount of heat escapes there and b) nothing to get we down there if water comes in over the footing).
Then, metal studs, sheetrock on the upper 1/2 and some sort of vented wainscotting on the lower half. (to make it easy to get into the wall for mechanical updats (heat/wiring) and/or if anything ever got seriously wet)
As for the uneven wall (we have the same problem), I find that a benefit, as any water behind the foam can slowly get out.
That, of course, is just my opinion. There are others. ;o)
Rookie...when you say styrofoam...are you referring to the expanded white stuff or the extruded pink stuff. Would you recommend one over the other?
Hi Rookie,
My walls had been sealed at one time, long ago by the looks of it. The MAB guy told me to just use good paint cause once it's "sealed" more sealer won't help.
Darrel510,
I did something like that in my dad's house. He's got block walls with furring strips 16" o/c. I put 3/4 foam between the strips and made some simple baseboard by ripping some 3/4 BC ply into 5 1/2" strips with a small round over on top, primed and painted on all edges. I attached the base right to the furring strips and set 3/8" drywall on top. My thinking and limited budget was I could remove the base if he had any seepage at the floor joint. No problems so far.
I'm still not convinced the poly and un-faced batts are bad in MY situation. But a lot of expereinced guy's don't like it?????
Bill
40Billh: The Insulate & Weatherize book that I referred to earlier suggests using extruded polystyrene (XPS). In crossing checking with the guru of energy efficient building (Joe Lstiburek ) however, his illustration says to use either rigid unfaced XSP, or unfaced expanded polystyrene (ESP - the white beaded board material) against the concrete wall. However, this doesn't seems to make sense (to me) since their water permeabilities are so different; i.e. the loose celled EPS would allow moisture to move through it more freely than the dense celled XPS. In MY MIND then, it seems that we want our basement walls to "breathe", hence I'd choose the loose celled EPS material. - Rookie
Oh...one other thing I've seen and want to look into a bit more is insulating paint. Apparently, it helps in a masonry wall. I need more info on it, but might be worth googling...
I have installed 6 mil poly on exterior face (to seal exterior moisture from stud & insulation) of 2x4 studs, then 3.5" fiberglass insulation, with 6 mil poly on interior face ( interior moisture vapour barrier) , then drywall all about 10 -15 years ago with no problems.