*
I would like to put a full cellar under a garage I’m building. Any idea’s.
Discussion Forum
Discussion Forum
Up Next
Video Shorts
Featured Story
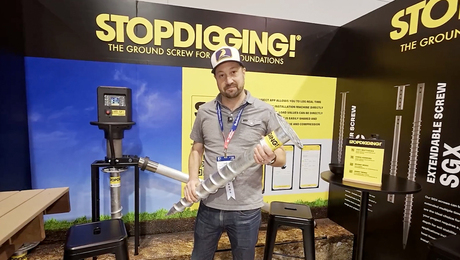
Discover a concrete-free foundation option that doesn't require any digging.
Featured Video
How to Install Cable Rail Around Wood-Post CornersHighlights
"I have learned so much thanks to the searchable articles on the FHB website. I can confidently say that I expect to be a life-long subscriber." - M.K.
Fine Homebuilding Magazine
- Home Group
- Antique Trader
- Arts & Crafts Homes
- Bank Note Reporter
- Cabin Life
- Cuisine at Home
- Fine Gardening
- Fine Woodworking
- Green Building Advisor
- Garden Gate
- Horticulture
- Keep Craft Alive
- Log Home Living
- Military Trader/Vehicles
- Numismatic News
- Numismaster
- Old Cars Weekly
- Old House Journal
- Period Homes
- Popular Woodworking
- Script
- ShopNotes
- Sports Collectors Digest
- Threads
- Timber Home Living
- Traditional Building
- Woodsmith
- World Coin News
- Writer's Digest
Replies
*
Troy;
You'll have to check your local building code to find out what is allowable. Is this garage attached to a house, or freestanding? if it's freestanding I'd guess you'd have more latitude. I once build what one might call a two story garage, the house was on a sloping lot and both the upper and lower level had grade access, I used reinforced concrete construction, it was a single car (per level) garage so the 11' span was no big deal, I think we used a 7" slab with #5 bar 6" o.c, but of course you need to have reinforced concrete designs checked by a qualified engineer. I think that the UBC does (or did, my copy is a bit old) allow wood floors in residential garages if they are covered with 2" of asphalt, but I might not be remembering corectly, I like concrete myself.
Jay
*Check with your local concrete product suppliers until you find one that sells prestressed concrete hollow core slabs. They should be able to tell you everything you need to know.
*I have seen a 3 car attached garage with the basement under the garage and house. Used the prestressed concrete. Obviously it was a very nice house. Can't say what the cost of this was but it is doable. Don't know if it would be cheaper to build the same space above ground, provided you have the room above ground.
*
Live load requirements for a residential garage are not excessive. I believe a uniform live load of 50psf or a concentrated wheel load of 2000 # is required. The load producing the greater stress will govern. Floor design must accomodate the governing load, not both. Ordinary wood frame construction can easly support these loads, if properly designed.
*
I helped a fella with this recently. In NY the minimum live loads is 100 psf or a 2000 pound concentrated load. The span was something like 26 feet. Hollow core prestressed planks are the way to go. Contact a concrete precaster in your area. We used NorthCastle(?) For our application, the manufacturer recommended an 8 inch thickness with a 2" concrete top course. They handled all the details.
Don't fool around with anything cast-in-place. There isn't ample quality control on a residential construction site.
*
Troy:
I have inspected three concrete garage slabs recently that were near failure. Two had storage underneath, the third had an indoor swimming pool. All the slabs were failing from water and salt infiltration from above that was penetrating the slabs through fine shrinkage cracks in the concrete. The water and salt corroded the re-bar over time and it eventually could no longer support the slab on the tension side. Would not want to be in that pool!! Im all for living/storage space under the garage. Make sure your slab is properly designed, use a concrete mix that will help reduce the chance of shrinkage cracks developing, insure the slab is properly placed and properly finished. A slow or "wet" cure and help to avoid shrinkage cracks. Once cured, seal the slab. Any shrinkage cracks that may develop need to be sealed with an elastic joint sealant and regularly maintained.
*
You can use cast-in-place, but you have to be willing to pay for good COT (construction observation and testing). I have seen many good elevated cast-in-place garage slabs that have lasted 30 and more years with no visible distress. This assumes that the slab covered (in a garage). If it is open, then you will need very good water proofing details below the slab (ie: one or two layers of bithutane or equiv, and NO NAILS)
The main problem (with either pre-cast or CIP) is the water proofing details at the uphill end of the garage floor. Make sure that you have concrete on concrete (slab on foundation). Assume that water will pentrate the concrete and design the adjacent wooden members (rim joist, floor joists, posts, etc) with that in mind. Otherwise, you will rebuild the uphill end of the garage within 5 years (or sooner).
*
I would like to put a full cellar under a garage I'm building. Any idea's.
*
A lot of interesting comments so I thought I'd throw in a different angle.
Did a project about 15 years ago where the owner was an engineer and had designed the garage himself. It was a stand alone and was also on a sloped lot. The front entry was to be used for his garage and the back, lower entry was to be for his shop.
The floor was constructed of 2x6s, glued and nailed on the edge, making a solid wood floor slab, 5 1/2" thick.
Steel beams were installed under the wood slab with a 6' spacing. The beams were supported at both ends of a 24' garage by the concrete walls and supported in the middle by a steel post made of 6x6 steel tubing.
The top level houses two collector cars and the floor was sanded and finished with a regular polyurethane.
Anything is possible is either you give it enough thought or money..