bathtub tile surround wall preparation
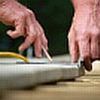
New construction (DIY HO GC type) at pre-drywall stage. Ceiling is already drywalled with 5/8″ sheetrock. 6’X9′ bathroom with tub not chosen or installed yet, but probably will go with 36″ “soaking” tub installed across 6′ dimension at one end of the bathroom (exterior wall) that will also have a shower head and shower curtain.
I’ll be DIYing tile surround around tub. Remainder of bath walls will be painted drywall. Question is: should I go ahead and drywall this entire end wall and portions of side walls that will be behind the cement backerboard, then install tub and screw the backerboard over the sheetrock, or is the backerboard better screwed directly to the studs? If over drywall, should I hang 15# felt between drywall and backerboard? Should I plan to tile all the way up to the ceiling?
I should add that there is 1/2″ THERMAX foilfaced urethane already up on the studs on the end wall with FG batts in the stud space.
Replies
No dyrwall under backerboard, when DW gets wet it crumbles. just tarpaer is OK.
Make sure you attach a 2 X 4 ledger to hold the lip of the tub so the tub wont pull away from the wall tile.
So I should go into this assuming that water will penetrate, getting through eventual cracks, seams etc, and failed grout/thinset that's holding the tiles to the cement board, through, I suppose, the screws that hold the cement board to the studs?
So I should hang felt right on the THERMAX, screw the cement board through that and into the studs, then tile over that?
Sounds pretty elementary, I suppose, but I've never done this before, and all I seem to get on internet searchs are companies that sell one-piece PVC surrounds.
By 2X4 ledger, do you mean to strap it right on to the studs, leaving the tub lip out 1 1/2" from the studs/THERMAX....or a series of 2X4 blocks in between the studs?
Edited 2/2/2004 3:27:43 PM ET by johnnyd
I subscribe to the felt paper behind the cement board practice although there has been some discussion about the need.
Your tub should normally fit snugly to the studs and have a support ledger under the lip of the long (back) side. With fiberglass or acrylic tubs you can also capture the top of the vertical lip with a few roofing nails or screws. Some people put the fasteners right through the lip, some don't.
This arangement now leaves a tub lip that is between 1/8" and 1/4" thick against the studs. Before you fasten the cement board to the studs you should take the extra time to fur out that distance so the board comes down over the tub lip without binding and bending. The Thermax board should be furred, too. This furring is your last chance to assure that the walls to be tiled are as plumb and smooth as possible. Some peoples framing leaves a lot to be desired. When applying the cement board, leave about 1/4" gap at the tub and run a bead of good caulk there before tiling.
Hi Ralph- I have never posted here before-in fact I only read FH occasionally but your reply did catch my eye.
What do you think of this?
If you felt the studs, fishscaling over the supported tub lip, you have a moisture barrier; add quarter inch furring strips on all studs and you have compensated for the protusion of the tub-lip(we use strips of scrap hardiboard)plus created a quarter inch drainage plane. Put quarter to half inch of any concrete panel product over (we use whatever the studspacing dictates for panel strength) and we now have a interior version of a 'rainscreen'. If you leave the board and tile uncaulked at the bottom the drainage cavity has a proper drain (we do not find lacvk of caulk at the bottom of the tile a problem if the tub has been supported properly). Deluxe versions involve peelandstick membrane fishscaled into the system at the bottom and further elaborations but if the above is done carefully it should be longlasting. This is Canada-obviously outside walls call for further elements.
The Thermax board makes your situation a little different than many. Typically, the tub and backer board go tight against the studs. There is a difference of opinion about the felt between the backerboard and studs. Some swear it's absolutley necessary, some think it traps moisture and causes problems. I'll take a middle road (after reading many thoughts here and in FHB) and suggest felt in the corners.
I've never installed a bathroom with foam board on the interior. Perhaps someone else can help you there. I'd consider a strip of plywood the same thickness as the foam where the tub hits the wall to provide a firm backing for that joint.
Al Mollitor, Sharon MA
I'm not familiar with Thermax, but it sounds like it's going to be between the backer board and the studs. How rigid is it? Will it compress in the places where the backer board screws go? If so that's not a good thing.
Thermax is not as rigid as extruded foam (dow blue or pink) but more rigid than styrofoam bead board. I've used it before, and when mounting relatively heavy items to the studs, screwing through the sheetrock and THERMAX, like a plant hanger or wall light fixture, you do have to watch out when you torque the fasteners down, but with normal drywall hanging, you don't know the difference, (except for seeing the studs :>()
If it's a big deal I can go with normal FG batts with 6mil VB.
However, I like the idea of a strip of 1/2" plywood between tub and studs.
Edited 2/2/2004 4:51:28 PM ET by johnnyd
If the CBU is going to distort when you screw it over the thermax, I'd be cautious. I've never used rigid insulation panels, but can you get more R's from some of that cut into the stud bays than from FG? Seems safest to screw the CBU directly to the studs, or to plywood over the studs.
One reason I'm using the THERMAX, which is foil faced poly-isyonaonate (SP), is that I ended up with a huge thermal bridge along the top plate, which for various reasons ended up composed of FIVE stacked 2X8s. That and the fact we changed window sides in two of the rooms after the the original openings had been framed in...which ended up with more redundant framing that will tramsmit cold straight through.
Anyway, yes, I like the idea of fastened the Durok directly to the studs. But I think I'll get a sheet and experiment to see how much deflection I actuially get over the Thermax.