Which ICF do people prefer the most considering cost, ease of install and strength. Have built with traditional forms but like the idea of insulated, water proof system after poor. I am building in Boulder, CO. Thank you
Discussion Forum
Discussion Forum
Up Next
Video Shorts
Featured Story
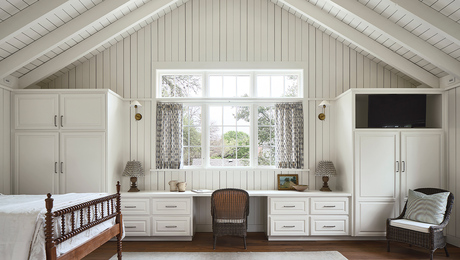
This 654-sq.-ft. ADU combines vaulted ceilings, reclaimed materials, and efficient design, offering a flexible guest suite and home office above a new garage.
Featured Video
Builder’s Advocate: An Interview With ViewrailHighlights
"I have learned so much thanks to the searchable articles on the FHB website. I can confidently say that I expect to be a life-long subscriber." - M.K.
Fine Homebuilding Magazine
- Home Group
- Antique Trader
- Arts & Crafts Homes
- Bank Note Reporter
- Cabin Life
- Cuisine at Home
- Fine Gardening
- Fine Woodworking
- Green Building Advisor
- Garden Gate
- Horticulture
- Keep Craft Alive
- Log Home Living
- Military Trader/Vehicles
- Numismatic News
- Numismaster
- Old Cars Weekly
- Old House Journal
- Period Homes
- Popular Woodworking
- Script
- ShopNotes
- Sports Collectors Digest
- Threads
- Timber Home Living
- Traditional Building
- Woodsmith
- World Coin News
- Writer's Digest
Replies
You'll probably get preferences from different people here, but here's my experience:
I've only used the ARXX forms because
1. The supplier offers one day seminars that were very well done and are part of a certification process for using the ARXX product. I assume that the other manufacturers also offer classes because it's to their benefit that the assembly is properly done to maximize success. On your first ARXX project, a factory rep or a supplier rep will be on site to assist with the assembly.
(There were some ugly stories about ICF failures a few years ago, but since they've proven to be a good building method when done right, the better manufacturers and suppliers have worked with building codes people to establish some standards which are now a part of IRC and CABO residential codebooks).
2. There is a factory within a couple hundred miles of me which keeps shipping costs tolerable. An ICF project for most residences will require at least one semi-truck load delivered and if the walls will be run to the roof, more truckloads (Low weight, but high volume).
So your decision might be determined by what's available locally....from what I read here, most posters have been happy with their brand of ICF system.
While the systems are similar, each has their own little quirks that you need to become familiar with....from setting layout, taping, bucks for openings and utility access, form bracing, attaching/setting reinforcing steel (very easy with ICF's), water proofing, attaching interior and exterior finishes, etc.
I really like them and I HATE building and tearing down traditional wood forms.
A lot of this comes down to what is available in your area.
One thing that matters to meis that some brands use a sort of T&G to snap together while otjhers have a Honeycomb pattern. I think AARX is one of the latter.
I dislike th honeycomb snap pattern because it can be damaged easier and because in winter weather, that can get filled with ice and is a real pain to pick it out of the crevices.
Welcome to the
Taunton University of Knowledge FHB Campus at Breaktime.
where ...
Excellence is its own reward!
I haven't used ICF's yet, but I'm led to believe the type used depends upon your design.
The ARXX mentioned, so I'm told, allows for more easily formed curves.
It is actually the Builderblock system linked above that has the easier corners to work with.I priced four different systems for the last job and found them all within a couple hundred of each other, making that issue nola contendre
Welcome to the Taunton University of Knowledge FHB Campus at Breaktime. where ... Excellence is its own reward!
boulderdog,
I go along with the other poster, your location determines which are good brands..
I attended the world of concrete a few years back where nearly every ICF mfg. had a booth. Some forms simply looked like they were designed to have a blow out while other brands really looked robust..
In the end I choose rewards forms. They appeared robust, the dealer was right there with advice, tech support, video's and even went so far as to send someone to check your site over before the pour to ensure you hadn't overlooked anything..
Unlike Piffin I like the honeycomb joint.. It's a much stronger connection and less likely to blow out.
My forms were all carefully wrapped to prevent damage to them and the company would take them back if they arrived damaged and replace them.
These are an improvement on the AARX, last time I bought them, they were cheaper, too.
There is a plant in Colorado Springs.
http://www.buildblock.com/
I used to use the AARX, but on the last one we used ( I did a thread here called something like, "Jack that house, John Henry") The builderblocks. I liked them much more. The dentil style locck mating was as strong as the honeycomb but it didn't lock water in to freeze, there was less shipping damage to the edges, and the bigest plus was the reversable orners so it was easier to calculate and build without having to track left and rightcorners in the layout.I have also seen the Polysteel demnonstrated but not distributor here for them that I know of.
Welcome to the Taunton University of Knowledge FHB Campus at Breaktime. where ... Excellence is its own reward!
The Buildblocks are the best I have used, and I am AARX certified. I also think the corners are better designed, as well as being reversible. I like the measurement grid on the blocks.
Very similar to the AARX, but with well thought out improvements.
Polysteel has undergone design changes and improvements since I last worked with them, so I can't comment on their current offering.
Ever tried Rastra?
Nope, but if they are whay I think I have heard and read of here,, they are harder to work with but a better system overall - nice and solid.
Welcome to the Taunton University of Knowledge FHB Campus at Breaktime. where ... Excellence is its own reward!
They are the ultimate, but - heavy and pricey, harder to work with.
Heck,I have only used the Rastra-type block, and only on one building. You say "they are the ultimate." Why do you feel this to be so? I'd like to hear from someone with wider experience than my own.I chose them because they were the only product to address all my needs. And they ARE heavy!The only aspect of the other systems that tempted me was the ability to fasten stuff to them with screws into plastic or steel inserts, and the ease of hoisting/assembly.Thanks,
Bill
Bill, the Rastra ICF is simply a much more substantial form than any other that is made out of polystyrene.
It is sturdier, fireproof, doesn't outgass, you can attach to it's surface, doesn't blow out during pouring, and is a 'greener' product than the others.
It is harder to work with, it is harder to cut and place, it is harder to run electrical.
I prefer to work with the BuildBlock, but I feel that Rastra is the superior product.
Thanks, Heck.What I liked about the Rastra was the absence of need to brace the forms for the pour, and being able to plaster directly onto the skin surfaces, in and out. It wouldn't be my choice for a wood sided house, but I am partial to lower maintenance anyhow. The other compelling factor was the termite resistance of the Rastra.My back did NOT appreciate the mass of the blocks, however.Bill
On a slightly similar topic, how difficult is it to run plumbing and electrical through the ICF's? I've heard it's easy, I'm just not sure what tool would work best for it. I'm thinking of using the Arxx system also b/c that's the only one available in our area.
Also - I can only really afford to do the ICF in the basement when I build - are the future cost savings enough to justify about a 15% premium in cost fo the ICF?
Thanks again for all your help.
They make hot knives just for slotting ICFs.
Easy as pie.
Forrest - done it in class
What Forrest said about the tools that are available for working foam: There are hot knives that make short work of it.
I still use my 12" electric chain saw for slotting romex runs in the foam. I drilled a hole in the bar 2" from the tip and fastened a bolt there. The bolt is my depth gage, and I can slot almost as fast as I can walk along. Then, after the wire is in, a little spray foam secures it.
Plumbing takes more planning to keep the larger drains and vents out of the way, usually it's the fittings that want to protrude from the wall. Bring the plumbing waste and supply through the floor if you can.
As to the cost - is there really a 15% difference when you get around to insulating your basement, and then having to furr out to attach drywall? With ICFs, it's already there. I am supposing you mean the basement walls would be 15% higher cost, not that the entire budget would be raised by 15%, right?
Grandchat 27
I've run electrical before the pour and it's as easy as cake.. if I think I might some point in the future run extra wires I put it in the pipe they have available for it and actaully put the boxes etc. in place. foam covers a lot of sins..<G> never had an issue of a blow out as long as I don't pump like a mainiac.
I've never run pipe into the outside wall. Pipe comes up thru the floor. It's too cold here in Minnesota for that to be a good practice.
You could of course run it in the wall if you were absolutely sure that you'd never need to move it or have it plug up on you.. , Just make sure you don't use copper as cement will attack copper pipe.
Many years ago I use a system called permaform I consisted of 1 1/2 " polystyrene sheet each side with 4" rewire mesh every 4" it was held together with a wire on the outside attached to the rewire inside . So every 4" there was a thermal bridge . then the rust problem that will in future years bust the concrete as the rust builds and expands. Too much obstruction inside to pour real concrete.
the next system I used was Rforms with plastic spaceRties every 16" oncenter . That made placing rebar easy on the outside of the foam was a 4" square plastic pad that allowed fastening sheet goods. The open inside allowed the use of real concrete . We used a convayer truck to place the concrete . Much less cost than a pump truck and we did not need the pump mix.
I think that I would use Reward or a simalar system as long as it was open inside had plastic tyes and a locking profile on the blocks.
I would not use polysteel forms because of the thearmal bridge and the mesh inside that holds things together ,restricts concrete flow..
I use PolySteel and got along great. I "think" it's the largest block at 2'X4', makes construction a tad quicker. My distributer lets us use his panel jacks <http://www.buildblock.com/products/bracing/reechcraft.asp> so that saves a bit on rent.
The one thing I didn't like about the block specifically was the corner. The material used for the internal fastener didn't hold very well...I understand that they were to re-design it...but it was a challenge. Everything else was fine...poured from the basement to trusses, nothing even close to a blow out.
I like polysteel also the steel is great to attach to and is strong and wont crack like plastic when you put fasteners in it .
Jim III
I believe this is a good survey topic and report for FHB.
What's the pro's and con's of each brand? Pricing, availablity, whether your SIL can set them up, the fastening systems,etc.
I used BuildBlock on my project, and I found them to be a very quality product. I stressed for a while about which brand to choose, and after doing a job myself (a DIY'er) I determined for the most part, blocks are the same. Yes, some blocks have nice features over others, but all will get the job done.
IMHO, I think the more important things to consider over block manufacturers are A. Level of support on whatever blocks you choose and B. A good alignment system. Most modern alignment systems are very good, but my rep tried to screw me over with absolute junk that would not keep the walls plumb.
Outta curiosity, do most vibrate their crete in an ICF?
We were told to just drop it in, pull it straight out - if the slump is 5-6, and with #7 stone, that's enough to speed the flow and consolidate, and doesn't stress the form.
Forrest
<edit> also, they said the goal was for a 45º "angle of repose" as you fill the forms. Any shallower, and it's too wet or too much vibration; any more and it's stacking up and will have trouble in rebar-choked areas and flowing under windows.
Edited 9/17/2007 8:12 am by McDesign
RippySkippy,
It really varies from the contracters I've watched.. some do, some don't and the technique is wildly differant.
I did and in only one spot did it pay off. The rest was fine just as it was.. the spot that it mattered was more than a blocks worth of air..
There is a document you can buy online called "Concrete Consolidation and the Potential for Voids in ICF Walls" that addresses consolidation. I didn't buy this before I poured my walls and I worried about it afterwards (even though there was nothing I could really do about it). This analysis of their findings was you MUST vibrate to eliminate the possibility of voids.Having said that, my pump operator claimed he does literally 100 pours per year and they never vibrate except around tight spots, like lintels above windows, etc. I did do this in my case and I am glad I did. Most people only use 2500 lb mix of #1 stone. In most cases, this is the minimum you can use. I used 4000 lb mix that was a little on the wet side. The mix didn't bother the BuildBlock at all, but the combination of that with less sand made the mix very flowable. If you do vibrate your walls, just keep in mind that you don't want to get crazy with it or you can cause a blowout!
My electrical contractor just starting setting in my electrical boxes and cutting away the foam. I am happy to say I don't see any voids, which isn't a very scientific test but gives me a little more piece of mind. If I had to do it again, I probably would vibrate the forms just in case. But at the same time, I think upgrading the mix to a 4000lb was worth the extra $10/yard.
Take what I say with a grain of salt, this is the first house I have ever built and also the first time I ever used ICF's. However, I did build a shed once :)
PolySteel recommends 30% fly ash to improve flowability, FWIW.
Forrest
The Colorado builder I design for swears by the Nudura system -- says it substantially reduces bracing required to achieve straight, accurate walls. By the way, I'm now a certified "installer" without ever having touched an ICF in the field. About the only way I can recommend Nudura over others is to state that I trust the judgement of this builder over my own on this particular subject. He's been doing this for some years now, and has displaced almost all other ICF builders in the region.
}}}}
Thanks a lot Ted