Looking for a suggestion for the favored roofing material for low slope roofs. I have a 3 in 12 roof currently with three tab shingles and I think when it is replaced next year, I would like to consider other options. Any help would be welcomed. Thanks.
Discussion Forum
Discussion Forum
Up Next
Video Shorts
Featured Story
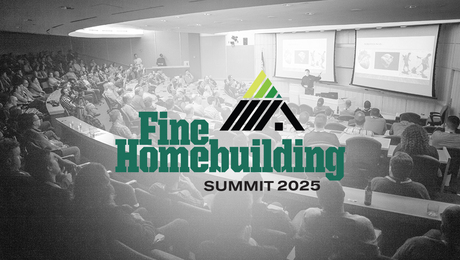
Join some of the most experienced and recognized building professionals for two days of presentations, panel discussions, networking, and more.
Featured Video
Builder’s Advocate: An Interview With ViewrailHighlights
"I have learned so much thanks to the searchable articles on the FHB website. I can confidently say that I expect to be a life-long subscriber." - M.K.
Fine Homebuilding Magazine
- Home Group
- Antique Trader
- Arts & Crafts Homes
- Bank Note Reporter
- Cabin Life
- Cuisine at Home
- Fine Gardening
- Fine Woodworking
- Green Building Advisor
- Garden Gate
- Horticulture
- Keep Craft Alive
- Log Home Living
- Military Trader/Vehicles
- Numismatic News
- Numismaster
- Old Cars Weekly
- Old House Journal
- Period Homes
- Popular Woodworking
- Script
- ShopNotes
- Sports Collectors Digest
- Threads
- Timber Home Living
- Traditional Building
- Woodsmith
- World Coin News
- Writer's Digest
Replies
metal..it's forever (almost)
Spheramid Enterprises Architectural Woodworks
Repairs, Remodeling, Restorations.
Hi..I agree w/ SPERE...metal is a great product...can handle slopes "down" to 1/4":12".
Since you have abit of time...I suggest you surf abit and see what roofing is out there...good luck.
Tony
IF there are no hips, valleys, ridges, or roof penetrations (i.e.: a simple shed roof), pre-fab metal roofing can be a good alternative. If you have any complications of any sort, you will likely find out the shortcomings of this product fairly quickly.
If you want to do a quality metal roof, you need to talk to Greencu; he can give you the skinny on the real McCoy, as opposed to what substitutes for it nowadays....
Other than metal, 3-in-12 with icegard membrane laid under asphalt shingles should work well. If you don't like the look of 3-tabs, there are alternatives. I would not recommend cedar, slate, or terracotta on that slope.
Maybe sod laid in a built-up roof pan...? You got mower access up there? <G>
Dinosaur
'Y-a-tu de la justice dans ce maudit monde?
Should one use Ice & Water shield under the newer type of metal roofs at a 3-12 pitch or is tar paper acceptable? Is there a large cost difference?
SS
The majority of the work I do is reroofs, so I religiously use ice & water shield under low pitch roofs mainly to protect during the reroof process. It's an added bonus after the roof is finished, although if my guys have done their job correctly, it should never come into play. On anything less than a 3/12, I usually go to flat (soldered) seam copper. Open, unheated, or less than 10' runs can be done with standing seam at a little less than 3/12. I personally don't perceive much value in prefinished steel roofing. It's going to have to be maintained (repainted, recaulked, gaskets replaced, screws tightened, etc.) and the manufacturers seem to disappear as soon as the warrenty problems come (same with synthetic slate). Slightly more upfront cost gives you greater value using copper. Some locales ( sea coast areas ) might dictate otherwise, but where I live it seems to be the smart choice.
If you want to use the modern stuff, yes, put Ice-Guard under it, and also caulk EVERY seam between sheets with BUTYL RUBBER caulking. Having a pneumatic caulking gun helps if the job is large.
But like I said originally, this stuff is overrated and if you've got to cut it at all, you'll find out why I hate it so much. Short of having the factory jigs to match the rib pattern and a hydraulic slicer in your front yard, there is no satisfactory way to do this. I use a pneumatic nibbler and/or a special blade for metal roofing in my circular saw to cut when I have to, but the results are far below what I consider acceptable.
You really oughta listen to Greencu and do soldered seam copper. It'll be ever so much better....
Dinosaur
'Y-a-tu de la justice dans ce maudit monde?
Dinosaur,
Glad somebody's finally backing me up on that pre-finished steel stuff. Most of the stuff I do has lots of valleys, hips, dormers, chimneys, etc. With all the cutting, fitting and forcing, it's much easier just to fabricate a piece to fit from scratch than trying to modify a factory piece that wasn't really the right thing for the job. If it's a fairly steep gabled ( or shed) roof with no valleys and minimal penetrations, it's fairly good stuff. Otherwise, your interior is dependant on how good a caulker (and how good the caulk is) you are. I've torn off three of these type roofs that were less than four years old. They leaked. Admittedly, all three were victims of the dreaded "installer error", but most of this stuff has disclaimers on every page of the installation manuals (if a manual is available). OK, I'm thru ranting. Hope you're doing well.
I fervently hate that stuff. I only work with it for two reasons: 1) it's very popular up here (just like 'Floating Flooring'! LOL), so I get a lot of calls from HO's already convinced that's what they want, and nothing I say is gonna change their mind; and 2) I haven't learned how to do traditional metal roofing.
In fact, I'm not sure there's anybody up here who does it anymore. That's a shame, because there are a lot of older buildings with standing seam, flat soldered seam, and a third style I don't know the name of--the roofing is made up of large diamond-shaped metal shingles, about 2' on a side. I think they're interlocked but I'm not even sure. You know about that style?
Anyway--when these older places finally need new roofing, usually about 50-60 years on, there's nobody to replace the original material with the same stuff, so they slap on the pre-fab sh!t and screw it down. Nice and colourful--but not a clean job and anybody who knows what they're looking at can see it from 100 feet away....
Dinosaur
'Y-a-tu de la justice dans ce maudit monde?
The nicest thing would be to fabricate a copper roof with a copper gutter.
Its really not all that difficult if you have a brake to bend the copper on and looks great when youre looking down from an upstairs window.
If you have no upstairs windows and can't see it from the ground copper may not be worth it.
My neighbor in an historic house used roll roofing on two front porchs.
Looks disgusting but I figure they figured originally that they couldnt see it from the street or yard yet when they look out a window.yukkk.
I did a cedar roof on a low pitch (4:12) with the entire deck of water/ice shield and Cedarbreather.
If I get ten years out of it I'll be happy.
Its not all that big an area to rip and do over.(15x6 ish)
If you can't see it than go with a less expensive roof than copper like rubber or a less expensive metal.
Be covered
andy
Just a front porch roof that looks awesome from my upstairs window along with the rest (60 sq) of the adjacents roofs that are on about an 8:12 pitch.
The secret of Zen in two words is, "Not always so"!
http://CLIFFORDRENOVATIONS.COM
Edited 7/8/2004 3:21 pm ET by Andy Clifford(Andybuildz)
> Its really not all that difficult if you have a brake to bend the copper ....
I'm doing exactly that right now. There's a real learning curve to copper work. I spent a lot of time on what I thought would be an excellent gutter design, then spent more time bending up test strips until I proved that my wonderful design was physically impossible to make on a Tapco brake. (I ended up redesigning it as two pieces.) The order in which you do the bends to make a complex shape is a very interesting puzzle. You have do do it in such a way that the metal never has to be where any part of the machine already is. I've found that it can be easier to figure out working backwards, start by deciding which will be the last bend to make.
I got the Tapco Max brake, which is theoretically rated for 32 oz. copper. It works quite well on 16 oz. But try doing a 1/2" hem on 8 ft. of 32 oz. No matter how tight you make it clamp, no matter which way around you put it in the brake, it'll just pop out and do some edge damage rather than bending. The solution I've found is to put the big part in the brake, and start it by progressively bending the hem for the first 60 degrees or so using a 5 in 1 painter's tool. From there out, the brake can take it around to about 150 degrees. For small 90 degree bends, the problem is that the progressive start stretches the metal, and induces a curve in the main piece, arching it up maybe 1/2" in the middle. So I have to follow up with body shop techniques, hammer and dolly to expand and straighten things.
On larger bends, it tends to overbend at the ends producing a sharp crease, and underbend with a larger radius in the middle. I've handled that by bending the middle to the final angle, then hand tweaking the ends back into place.
-- J.S.
Re: Metal roof on 3-12 Pitch
I have installed a metal roof on a 3-12 pitch and have had a problem with snow. The good news is the snow will not build up on a metal roof great for cottages etc. However snow sliding off a roof of 800 Sq.ft.
can cause a lot of damage and injury if you find yourself passing under the roof after you have given the front door a good slam.
Metal roofs on the plus side
- Easy to install
- Easy to to install solid insulation
- Easy to allow for air space
- Long lasting
- Snow will not build up
- May not require the ermoval of existing roof surface
Metal roofs on the down side
-Sliding snow over walk ways
-sliding snow removes new porch railing
-Noise in any rain
-Noise as sun heats up metal and metal expands
George
> snow sliding off a roof ...
I got to visit Norway and Sweden a couple years ago. No hip roofs, and doors are always on the gable ends of houses. Those folks know about snow. ;-)
-- J.S.
John,
If you ever get your hands on a well tuned shop brake you'll never want to use a portable brake again. I've got a Tapco Max that hasn't been used in almost 2 years. I ought to sell it, but if I do I'll need it. The last time it went out was to do a courthouse dome and we took it up on the scaffolding for touch-up and adjustments. We also took a 4' shop brake up there and the Max hardly got used. I still did 99% of the bending in the shop. How's your project coming and when are you gonna post some pics?
Alas, there's no way I could afford a real shop brake. Progress is real slow, I've had to do other things with my nights and weekends for quite a while. We sold the little house we had in the valley, and bought a much better one for the kids. Both of them took some work. So, all I've got done is making up some parts for the gutters and fascia.
The gutters are roughly 12 ft long (one side is 1 5/8" longer than the other), so each consists of an 8 ft. section and a small piece, with a wrap-around splice. The pieces come up 3/4" short, and the splice hides the adjustment to the final length. Over the weekend I hope to get all that soldered together. My plan is to put everything from the inboard side of the fascia around to the apron on the roof together as a bench assembly, then lower it over the side using ropes and clamps, and pull it up into place.
I haven't taken any pictures of the copper work yet, it's too mangled and bashed to fit. I'm too far down the learning curve to have anything worth showing.
-- J.S.
OK, if this works, here are some pictures of the gutter forming in progress....
That seems to have worked, so here's what the pix are:
635: Downspout end of South gutter, showing the 1/2" type K pipe that will get crimped and soldered into the outboard lip to stiffen it, sorta like a wire hem on a grand scale.
638: Test strips of the high and low ends of the design that turned out not to be possible to make on the Tapco Max. I finished these by hand to show what I was going for. This design had the top of the gutter level and only the bottom sloping down 1/4" per foot. In the final design, the taper is in the back surface only , and the cross section of the front is the same all the way across, and slopes down. (Note also the 5 in 1 that made the Tapco usable.)
641: Wide shot, both gutters with the splices dry fitted. The clamp is on the North splice, which is the sloppier of the two. The 3" DWV pipes will become the first piece of each downspout.
644: Closeup of the South splice. Left of the pink dustpan is the adjusting key for the Tapco.
647: Closeup of the North splice, note the crappy adjustment to the piece on the left, it's the one that slipped the worst in the brake.
650: A mock-up of how things go together. This is the splice end of a gutter. The 16 oz. cutoff is where the outer fascia piece will go (I won't make it until I've tried the rest in place to get a good dimension). The 2x6 represents the cross section of the rough fascia. The little piece of 16 oz. under it gets cleated to the back of the wood fascia, and the copper fascia outer piece single locks under it and over the lip on the gutter. Then a 32 oz. apron piece single locks over that and gets cleated to the roof. Finally, the field pans will also lock around that making a drip edge into the gutter.
653: A splice taken apart.
-- J.S.
Edited 7/9/2004 8:11 pm ET by JOHN_SPRUNG
Edited 7/9/2004 8:12 pm ET by JOHN_SPRUNG
Edited 7/9/2004 8:14 pm ET by JOHN_SPRUNG
Edited 7/9/2004 8:22 pm ET by JOHN_SPRUNG
Edited 7/9/2004 8:22 pm ET by JOHN_SPRUNG
That is kool . does the copper tube run the full length or is it just at the splice?
The pipe runs the full length on the South side, and on the North it's 1 1/4" short with a small piece added on. Turns out I made a really dumb mistake, fortunately not too hard to fix. Originally the dormer had been built a little off center. When I re-framed last summer, I corrected that. But I forgot about the correction, and was making up the gutters to the old dimensions. Then I triple checked my numbers and had one of those "oh s--t" moments. Fortunately the splice pieces are 5" wide, so now they bridge gaps of 3/4" on the South side and 2" on the North.
I soldered up the North assembly over the weekend, and the added pipe really makes it nice and stiff. The idea is to have nothing in the way for future gutter cleaning.
Soldering with furnace heated coppers and "meter bar" solder is a whole different thing from the plumbing sweating I'm used to. It's possible to get the solder in a condition in between solid and liquid, and to push it around almost like an extremely hot caulk. But for doing the long pipe, a sort of continuous sweating worked best. I was surprised that distortion due to expansion wasn't a problem. Sweating with a propane torch also worked well for the splice pieces, the solder flowed all the way thru the joints. The coppers and meter bar were much better suited to attaching the 3" DWV pipe for the downspouts to the gutters. It filled in around all the little slits and bends.
-- J.S.
Jon , try putting a small strip of metal on the hinge over lapping the edge of the break apron . then put the metal in the break . It will /should slide making a better break.
I tried that, too. It doesn't solve the problem, because the real problem is that the Max isn't strong enough to stay clamped on 32 oz. copper. It opens up visibly even with the adjusting screws so tight I can barely close it. The slight progressive pre-bend gets me out of the range where the force of the bend is acting nearly straight up against the jaws of the brake, and into the range where I'm pushing more horizontally. I also tried cleaning the brake and copper with isopropyl alcohol, in case it was residual oil from the rolling process making it slip. That wasn't it, either.
-- J.S.
line the clamping surfaces with some self stick sand paper..my buddy had a problem trimming Ipe on his chopsaw ( interior trim and crown moulding) I told him that trick and it worked like a charm..
3M, or klingspor..forget the chinese paper
Spheramid Enterprises Architectural Woodworks
Repairs, Remodeling, Restorations.
Metal, especially copper is wonderful, as long as you're able to pay for it. Look into a membrane roof. They are relatively inexpensive and they aren't used almost exclusively on commercial roofs because they don't work.