Finished this up a few weeks ago. Yellow birch stringer, risers & trim. Hard maple treads carpet center. Stained medium brown followed by 3 coats spray applied Sherwin Williams Kem-Var. Powder coated iron balusters, custom base shoes and our exclusive captured bark rustic maple railings and newel post caps.
Discussion Forum
Discussion Forum
Up Next
Video Shorts
Featured Story
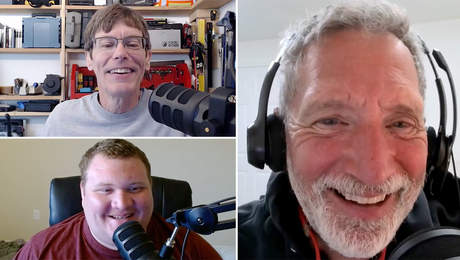
Learn more about the pros and cons of single-room ERVs.
Highlights
"I have learned so much thanks to the searchable articles on the FHB website. I can confidently say that I expect to be a life-long subscriber." - M.K.
Fine Homebuilding Magazine
- Home Group
- Antique Trader
- Arts & Crafts Homes
- Bank Note Reporter
- Cabin Life
- Cuisine at Home
- Fine Gardening
- Fine Woodworking
- Green Building Advisor
- Garden Gate
- Horticulture
- Keep Craft Alive
- Log Home Living
- Military Trader/Vehicles
- Numismatic News
- Numismaster
- Old Cars Weekly
- Old House Journal
- Period Homes
- Popular Woodworking
- Script
- ShopNotes
- Sports Collectors Digest
- Threads
- Timber Home Living
- Traditional Building
- Woodsmith
- World Coin News
- Writer's Digest
Replies
I like that a LOT. I might be pestering you about a quandry I have with my stairs ( yet to be built). I'll email ya. if thats OK?
Parolee # 40835
Cool send it off.
This staircase services a large walk out basement with 9-foot ceilings. Like most projects I end up with the designer did a totally screwed job of planning the stairwell opening. Somehow the design only allowed 5'-4" of headroom at the lower landing. I solved the problem by moving a closet on the main floor as well as extending the stairwell 18 inches into the foyer. Proof once again a sawzall and good crowbar can fix almost anything. I wasn't two thrilled about staining the staircase since birch has a tendency to become splotchy and is difficult to wipe out evenly.
Photo of boxed in support columns and capital
Since I always pre-fab my stairs I choose to build the understructure to my spec’s. Once the drywall is on I hate looking for backing that isn't there because somebody didn't second guess where I needed it. It saves me a bunch of time during the install since my templates are checked with the walls before I head back to the shop. Photo 06 shows the framing portion of the stair wall. The slab of masonite sitting on top of the stair wall is the stringer template complete with construction notes. I try to time this so the sheet rock guys are still on site. This way they can put the drywall where I need it and eliminates the chance of placing a joint where it might cause a problem later on.
Photo of main floor railing & newel. The wood is a little know fluke of the hard maple tree. Sometimes referred to as bark inclusions, ingrown bark along with a host of local slang. Basically its ingrown bark, captured or surrounded by new growth. The end result is pretty stunning, it's my number one seller when it comes to unique. A real bitch to work with since the bark contains impregnated sand that eats up cutters at an alarming rate.The lower left corner at the landing shows how I solved a problematic jog around a structural post.
Originally the stairs didn’t have the curved tread returns below the landing but rather made a conventional 90-degree turn complete with railing and lower newel. The client wanted a more open look so I opted to return the curved risers back into the main stair wall. This opened up another can of worms, as the code required a continuous railing on the open end of the stairs. At this point the landing was already built and the original railing died into the wood column and exited out the other side. I ended up moving the post 3 inches, the max I could get away with then jogging the rail around the column.
Armin, nice touch on the column capitol. Good job of playing with the cards you're dealt. Have you got any closer shots of the bark captured handrail?For curiosity's sake, why did you use the stop block at the skirt/base transition?As always, I enjoy seeing your stuff. Outside of the gates the trucks were unloadin',
The weather was hot, a-nearly 90 degrees.
The man standin' next to me, his head was exploding,
Well, I was prayin' the pieces wouldn't fall on me.
(For curiosity's sake, why did you use the stop block at the skirt/base transition?)The base is 3/4 thick and the skirt ended up being 5/8 thick. Even if they had been the same thickness I still would have used the transition block for effect.
Makes sense, usually our skirts are thicker than the base, so we make a little roll at the transition.Hey, you been out on the water lately? Outside of the gates the trucks were unloadin',
The weather was hot, a-nearly 90 degrees.
The man standin' next to me, his head was exploding,
Well, I was prayin' the pieces wouldn't fall on me.
Edited 3/31/2007 3:36 pm ET by Snort
Usually our stringer skirts are thicker than the base however this time it didn't work out that way. I started using the transition blocks as a way to merge my stringer molding into the more conventional base molding profile. Yes I have been out on the lake. It's been a mild winter so I got in a few ice burg runs as well as the spring breakup last weekend. First whitewater run tomorrow, might be the only run I get in this season since the water is at an all time low. Sea pic's.
A few working photos of the curved risers under construction.I begin by drawing a full scale layout on birch plywood. The red bending brackets are screwed to the plywood in the appropriate places. The riser material consists of a face layer of 1/16 thick birch, a core of two layers of 3/8 bending luan backed up with final layer of 1/16 birch.After the glue is applied the whole stack is stretch wrapped and slipped into a long narrow vacuum bag. Initially I extract just enough air to snug up the bag to the laminates and still be loose enough to allow the stack of laminates to bend unrestricted around the bending brackets. Once everything is in place full vacuum is applied and maintained until the glue has reached final set. Note in photo 43 the end brackets are offset to lock the stack of laminates in place.
Armin, your bracket set is the ticket. What is the metallic looking surface on the riser face? Reflection? And, how do you keep the brackets from rubbing holes in the bag when it's vacuumed? You are the king of jigs and fixtures, I am impressed at how few and light the clamping is with those brackets. You made 'em too, didn't ya?<G> Outside of the gates the trucks were unloadin',
The weather was hot, a-nearly 90 degrees.
The man standin' next to me, his head was exploding,
Well, I was prayin' the pieces wouldn't fall on me.
*What is the metallic looking surface on the riser face?*Must be the flash reflecting off the clear poly bag. The bag doesn't drift enough to cause any wear spots. Besides the poly bag is pretty tough. I have one main bag that has seen almost daily use for the better part of 12 years and still doesn't have a hole in it. The old bag is big, can handle a 4 x 10 wood counter top with ease. In the case of laminating big stuff sometimes you have to rearrange the work piece in the bag, the wife refers to this as me being half in the bag. see photo.Yes I made the red brackets, a rather recent addition to my collection of fixtures. They were simple, cheap and easy to make, one of rare brainstorms that actually has a life beyond the one project I originally built them for.
Puts a whole new spin on bagging the big one<G> Outside of the gates the trucks were unloadin',
The weather was hot, a-nearly 90 degrees.
The man standin' next to me, his head was exploding,
Well, I was prayin' the pieces wouldn't fall on me.
Armin,Great work as usual. The jog around the post is excellent. is it from solid stock or a lamination?Chuck Slive, work, build, ...better with wood
It's laminated as 2 layers, the bottom is 1-7/8 thick with a 3/8 cap. Joints are concealed in the profile. to get a decent color and grain match all sections are sequence cut from the same plank.
tip 'o the hat -
thanks for sharing -
D
"there's enough for everyone"
Armin: As usual.. very nice elequent work. You are simply the best.
Stan
Edited 3/31/2007 8:45 pm ET by StanFoster
Thanks Stan, I don't consider myself the best, just always try to do the best work I can.
Nice pics. No way I'd take my camera out there. Went sailing, Mrs 'Snort didn't think the dry bag needed to be completely closed...she does now<G> How do you keep your powder dry? Outside of the gates the trucks were unloadin',
The weather was hot, a-nearly 90 degrees.
The man standin' next to me, his head was exploding,
Well, I was prayin' the pieces wouldn't fall on me.
I have one of those plastic, gasket sealed containers mounted to the deck of the boat. The biggest hazard I have is fiddling around to long gazing through the camera view sights, misjudging the distance and running the nose of the boat up on an ice burg. One near miss convinced me you pick your shot, aim, shoot and put the camera way. At a water temp of 34 degrees your wet suit is nothing more than a form fitting body bag.