If I use 1 X 8 t&g vertical wood siding (or board & batten) nailed to 2 X 4 horizontal nailers, which are nailed directly to the studs, do I need any sheathing?
Discussion Forum
Discussion Forum
Up Next
Video Shorts
Featured Story
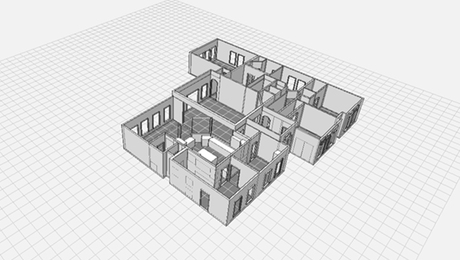
Hover's smartphone app offers an easier way to get precise 3D scans.
Featured Video
SawStop's Portable Tablesaw is Bigger and Better Than BeforeHighlights
"I have learned so much thanks to the searchable articles on the FHB website. I can confidently say that I expect to be a life-long subscriber." - M.K.
Fine Homebuilding Magazine
- Home Group
- Antique Trader
- Arts & Crafts Homes
- Bank Note Reporter
- Cabin Life
- Cuisine at Home
- Fine Gardening
- Fine Woodworking
- Green Building Advisor
- Garden Gate
- Horticulture
- Keep Craft Alive
- Log Home Living
- Military Trader/Vehicles
- Numismatic News
- Numismaster
- Old Cars Weekly
- Old House Journal
- Period Homes
- Popular Woodworking
- Script
- ShopNotes
- Sports Collectors Digest
- Threads
- Timber Home Living
- Traditional Building
- Woodsmith
- World Coin News
- Writer's Digest
Replies
kd
yes.
and no.
You'd need corner bracing-let in wood or metal should be approvable by your inspection dept if not in an area where shear panels are a big deal.
1. How do you plan to seal up this place?
I would seal it with air infiltration barrier. I am looking at this detail for a new design, and it is one area that I don't have resolved. I used 1 X 8 vertical wood siding for the house I am in now. It has the vertical siding on 2 X 4 nailers, but no sheathing. The inspector told me I did not need sheathing, and the nailers would be sufficient as bracing.
I could see how that might be debatalbe. The only thing that gives the triangulation of diagonal bracing with horizontal nailers is the spacing of the two nails where a nailer attaches to a stud. But there are a lot of those contact points over the whole wall.
If I were required to have diagonal bracing, I would use 2 X 4s on the outside of the studs, and interrupt the horizontal nailers for the diagonal braces.
KD
Back when I framed in another century and in another jurisdiction, we needed panels or more diag. bracing every ?-sheet , in the long walls. Man, wish I had half the memory ............. This was when using celotex (asphalt impregnated sheething) was the norm. And in Ohio where there is no wind or seismic regulations. At any rate-something to clear with the inspector.
If you install as I imagine-rainscreen, how do you plan on detailing anti rodent?
What you describe seems "odd" from what I'm used to. How and why did you come up with this idea?
Two questions ...
... just to satisfy my curiosity and help me visualise this wall.
1) Where in the wall will the air infiltration barrier go?
2) How do you plan to keep critters from coming in from the bottom behind the siding?
The infiltration barrier would be sandwiched between the outside of the studs and the 2 X 4 horizontal nailers. That would leave an air gap there of 1.5" between the studs and the back of the siding. Although, the insulation may balloon that air barrier outward somewhat into that 1.5" air gap.
The lowest nailer would be a treated 2 X 4 screwed to the outside of the concrete foundation with its top edge flush with the top of the foundation. So that would seal the wall cavity to animal penetration. Then the next nailer would be have its bottom edge flush with the bottom of the floor plate.
So these tech people can get this site better:
Who or what did you reply to?
This shows you replied to the original post you made up top. If you did, that's fine-if you didn't then these things have to get fixed.
However, replying to yourself doesn't do much good to keep a discussion going.
And of course, now that there's reply to this and reply to the original topic buttons, then there's the slip of the mouse to deal with.
Calvin,
I meant to reply to the post by WAwebfoot, but I am not sure which button I pushed. I am not used to a forum structure where you pick the post to reply to unless it is done for the purpose of quoting that post. What I have seen mostly is that you can pick any post and hit reply, and it will just add your reply to the end of the thread. And if you do that without quoting from the post you picked for reply, there will be no indication that you have replied to any particular post. So this gets a little confusing.
But, in any case, I was addressing the post by WAwebfoot where he asked where the air barrier would be placed and how I would keep the critters out.
by KDESIGN in reply to calvin [original] on Mon, 02/13/2012 - 18:06
you hover your mouse over the [original] and it'll show a number in along the bottom bar (on my computer)-that number corresponds to the post it was replied to : Which means pretty much zilch till you hover the mouse over the PERMALINK button of the post it was replied to.
However, if you click on [original] in that info line, it'll take you up to it.
It's like the 1880's as far as I'm concerned, but it's what we got and evidently won't get better.
This issue is further confused to the reply-ee when you have a choice of REPLY TO THIS (post) and REPLY TO ORIGINAL (or whatever the one next to it is)
Keep in mind that there's inevitably a gap between two adjacent boards (if not when nailed up, after they've dried a couple of years) and this gap at top and bottom is an entrance for large insects and possibly small critters.
Air barrier
Your air barrier layer needs to be rigid material, like plywood. Housewrap makes a lousy air barrier. If these walls are insulated with fiberglass batts, they will perform very poorly. What climate zone are you in?
Reply to Dan:
Dan,
That is a good point that I had not thought of. I have 1 X 8 T&G vertical siding on the house I built, but am thinking about board and batten for a new house design that I might build. With T&G, those bottom end openings where the tongue and groove engage are pretty small, so I don't think anything gets in there. But with board and batten, I could see that the large openings would be a problem. Some people talk about leaving a 1/2" gap between the boards. It could be caulked close, but then any water that gets in will run down there and get trapped. And the seam is where water will get in if it gets in.
Also, the horizontal nailers pose an issue for moisture drainage if one anticipates that there will be any. I don’t anticipate it, but it seems to be a forgone conclusion in the building industry that such moisture will occur behind the siding because rain will penetrate from the outside. I don’t expect that to happen with vertical t&g siding or board and batten, or at least not happen often enough to make any difference. What is really needed is some kind of woodpecker infiltration barrier.
DETAILS
WAwebfoot,
My experience with this is on one house I built, and another one that I am designing for the future. The treated nailer on the foundation is part of the future design, so I have not finalized the attachment method. I want a poured foundation, and the nailer would be a 2 X 4 on the outside of the concrete with its top edge flush with the top of the concrete. The siding would hang down a couple inches below the nailer. So the 2 X 4 nailer would cantilever the siding out overhanging the foundation by the 1.5” thickness of the nailer plus the thickness of the siding. On the present house and on the future one, the 2 X 4 nailers are not let into the studs. They are nailed onto the outer faces of the studs.
The house I built has 1 X 8 T&G redwood siding that has never been stained or painted. I flooded on a coat of linseed oil / mineral spirits about every 6 years or so. For the new house, I would stain right from the start, but the exact type and brand of finish is not resolved yet. If it were not for the sun and woodpeckers, the redwood siding would out last the pyramids.
For the new house, I am considering board and batten, but there seem to be a variety of different approaches to the detail of it. What type of wood did you use for your boards and battens? Why did you space your boards with the spacers? I see some reference to doing that, but I am not sure if it is universal practice. Are you saying that you only nailed each batten at the top and bottom, and there are no nails though the actual boards? I think I have seen references to an approach where the battens are nailed to the nailers, but the boards are not. So the battens hold the boards on and the boards can float for expansion and contraction. However, the boards might possibly drop if the battens are only holding them up by a friction grip.
I used Maze Stormguard nails. These were hardened ring shank, hot dipped galvanized, and painted. They have a small, flat head like a box nail. The paint can chip off when you drive them, so they offer plastic caps to put over the hammer head. I did not use the plastic caps, and just accepted any occasional loss of the paint from the nail head.
I drove the nails with the heads in flush with the outside of the boards. I have since read that nails should be driven so the underside of their heads just sit on top of the board face, rather than having the head thickness crush into the board face.
I put two nails in each 1 X 8 over each nailer, with the nails in about 1.5” from each edge of the board. If I were to do this again, I would used stainless steel nails, and locate them with a chalk line. And I would drive them with the bottoms of their heads sitting on top of the board, as mentioned above.
kd
You DO NOT want the batten nails to go into the vertical siding and it should be gapped for expansion/contraction.
And of course, you need more than a nail at the top and bottom of the battens.
That joint of the batten covering your gapped siding will be your weak link. Any water entry through there or knots/splits will be trapped at the cross blocking unless you use some form of rain screen.
Yes, I am a little concerned about water on the inside flowing down and being caught and trapped against the back of the siding by the horizontal nailers. But I am a fan of extreme roof overhangs, so between that and getting the joints nearly waterproof, I think I can keep water from reaching the back side of the siding. But I am thinking about some type of rain screen along with an air space, and maybe even circulating ventilation like with the roof.
Are you saying that it is typical to nail board and batten only through the center of the battens and not through the boards? Why would a gap between the boards be needed? The 1 X 8 T&G is put together tight. I had the impression that a large gap was maybe intended to get a little coverage out of the battens in addition to the coverage of the boards.
Here, from WRCLA
http://www.wrcla.org/installation_and_finishing/installing_siding/board_batten.htm
In the drawing, they call the member the boards are nailed to a "stud". I'm not sure why-but in this case, as the type states-it would be your horizontal furring.
I agree about the flimsy housewrap and a see a need for a rainscreen-either one you buy for that purpose or one engineer of wood strips and air space with a water resistive barrier.
Never was a fan of vertical T&G siding and most especially when they wanted you to get artisitc and run some on the angle. Seams in wood is an invitation for allowing water in and oftentimes trapping it within the t's and g's. Lap siding, wood shingles and vertical B&B all play on overlapping to repel water.
Large overhangs assume no wind and a short house, with no splash back.
I would nail it just like it shows in the drawing. If the boards are wide enough for two nails, keep them relatively close together, so they cannot grab too much of the board as they fight the expansion and contraction. I nailed my T&G with that kind of nail spacing.
I agree about the diagonal siding. I hate that idea. It is just flies in the face of siding theory. There are some pros and cons to vertical siding compared to lap siding. But diagonal T&G is the worst of all worlds. And it seems to actually look bad for that basic reason. Basically, I do not like the look of big fields of diagonal anything in architecture. But I think herringbone patterns can look really nice. The alternating patches of diagonals work against each other to keep the field in balance.
The big overhang on the roof won't prevent rain from hitting the siding in some storms, but it can greatly reduce the frequency of that over time. My ideas for a house look kind of like a small size railroad station circa 1900. I use eave brackets to help hold up the overhang.
Looks like the drawing is wrong
Either the drawing is wrong for vertical b&b, or more likely, they're showing a side-view of horizontal b&b installation. Another possibility is that what they call a "stud" in the illustration is actually blocking installed between studs, but I don't understand how they put blocking between studs once the sheathing is already there, and they don't show the studs at any rate. A fourth possibility is that I don't know what I'm talking about.
I agree
Upon reading once, the looking at the pic and then reading again-I came to same conclusion-the script sees to tell the story, the drawing's word "stud" seems to confuse.
So no, I think you came to the same conclusion, in which case-we both know diddley.
The purpose of board-and-batten is to allow the wood to expand/contract without requiring a machined joint like a T&G or a Dutch lap. If you nail the battens to both boards you prevent the expansion/contraction (until one of the boards splits, that is). And an initial gap between the boards prevents buckling in the event that the wood is drier than the environment.
Details
KD,
Boards and battens are western red cedar. I slab sawed the boards to get the widest boards I could. Of course, this also means my boards are variable width, some up to 14 inches and a few wider. If the wide ones look like they might split, they become two seven inch boards. <g> I think 3/4 inch battens look somewhat puny in large areas, so I cut the battens at the full inch in thickness. On the batten width, my thinking went as follows: Most references I've seen say for six inch wide boards use a minimum half inch space plus minimum half inch overlap on each board. That gives a minimum width of an inch and a half for the battens. Increase both space and overlap proportionally for wider boards. I didn't feel comfortable aiming at a half inch space behind a batten, so I used an inch space and a full inch overlap, giving me three inch wide battens. That's what I did; use dimensions that you think will look good to you.
The spacers were my home-grown solution to two issues. The first was consistent spacing between boards. The second was to keep critters out of the space between boards & behind the battens. I don't recall seeing spacers mentioned in any of my references. In fact, most of them mention vertical siding in a brief section with board and batten getting an illustration with possibly a brief paragraph. Brief being the operative word here. The web page cited here has the most extensive discussion of board and batten I can recall seeing. I've picked up the rest from talking with other guys who've done similar siding. Seems no two guys do it exactly the same. The overall approach is fairly standard; the differences are in the details.
As for the nailing, no. Each board in nailed at each nailer, at the mud sill and at the top plate. One nail per "bearing" location. Only one edge is nailed so the board has freedom to expand or shrink as the seasons and humidity dictate. (Alternatively, nail in the center of the board, but always keep the nails in a single vertical line) The battens are also nailed at each "bearing" location, through the center of the batten, so they are not fixed to either board, allowing the boards to move underneath the batts. The top of the spacer at the top plate is even with the top of the board so the batten nail will go through it. At the mud sill, the boards and battens hang down a bit, so the bottom of the spacer isn't even with the bottom of the board, leaving a small, open-at-the-bottom space for spiders and their kin to hide in. This seems like a good place to mention that the tops of boards and battens are cut square. I run the boards up so the soffit boards can butt up against them, but hold the battens down so the soffit boards will slide in above. I clamp a 3/4 inch board to the truss tails and jam the batten up against that before I nail it. At the bottoms, both are undercut with a slight bevel to give a drip edge.
I've driven the top of the board nails flush with the board so the nail heads won't hold the battens off the boards. I also drive the tops of the casing nails even with the surface of the battens. Perhaps someone can tell us which is preferred, and why?
Stainless is nice, but spendy. Hence the galvanized, which seems to work fine, here.
Be careful about the color chalk you use if you aren't covering the line. Some of that stuff doesn't want to come off!
WA,
Thanks for that information. So as I understand, you put one nail through the center of the batten and one nail at one edge of each board. And that nail at the edge of the board falls under the batten. When I nailed my 1 X 8 T&G, I drove the nails with the heads sunk into the board, so the nail head suface was flush with the board surface. It seems like the natural thing to do because it feels like assurance that the board is sucked tight against the nailers. But apparently, the advice to keep the head thickness above the face of the board is to avoid crushing open that little pocket for the head and exposing the tiny sides of that pocket to water intrusion into the end grain around the pocket sides. And any future expansion would also tend to sink the head in deeper. I would do it that way the next time, but I doubt that it is critical.
I would also try to use boards and battens long enough to avoid end joints. For my siding, I did have end joints. I lapped them at a 45 degree bevel, and coated the ends with silicone sealer before pushing them together. The thing about those joints is that they must fall on the nailers, which are 2 ft. O.C., so the joints easily form visual lines when you look down the wall from an angle.
Generally board and batten is associated with a rustic look because it was used as a quick siding solution to relatively primitive buildings. I would do everything possible to build in a high quality appearance. Your use of thicker battens seems like it would help with that objective. Battens can easily look flimsy because they have a natural tendency to twist and shift around due to the inability to really nail them securely. And even if they are secure and straight, they can look sort of losely tacked on. The thicker they are relative to their width, the better they look. I could see them being square if they are not too wide. I put a herringbone 1 X 6 T&G pine ceiling in as a vaulted ceiling with the joints on every other truss. So the pattern changes direction every 4 ft. It was not possible to perfectly end fit the boards at those joints, so the idea was to cover the joints with battens. The 1 X 6s were V-joint T&G, so those chamfers ran under the battens. And generally, it was not possible to make the battens lay down absolutely tight on the boards.
I could not make something like a 1 X 2 batten look good in that application. So I ended up with clear pine 5/4" X 1 1/2" with the 5/4 surface against the boards and 1 1/2" standing. So they look more like mini-beams as opposed to flat strips of covering.
history
The board and batten was developed to utilize the most of a plane sawn log possible. It was orginally used in the rough cut form for barns and other utilitarian structures, where inexpensive unfinished wood was used. As opposed to houses, and finer structures intended to be occupied by humans, where dimensioned, planed, and painted wood was used.
The boards, or wider sections, come from the middle of the log. The boards have pretty much verticle grain and don't cup much, but do swell and shrink in width quite a bit, while staying more constant in thickness.
The battens were cut from the narrower pieces at the outside of the cut. They will have more rounded grain and are prone to: cupping with moisture change; shrink and swell less in width; while, shrinking and swelling more in thickness.
The boards are center nailed, with two nails about 4-inches apart, leaving a gap between the boards large enough to accomodate the swell cycles. The nails are close together so the shrink swell cycle does not split the boards. If you nail the edges of a wide board, it will split down the middle after a few years due to the strain of the seasonal moisture changes.
The batten is then nailed over the gap, with the grain orientated so the cupping will be towards the boards. The nails on the battens are close together in vertical line, and about two or three inches apart vertically to limit splitting, and are set so they do not touch the boards. Their purpose is to seal the gap between the boards, and keep most of the water and wind out.
At some point architects decided they like the look, and began trying to adapt it to houses. Personally I think it is a poor visual choice, unless you are doing an addition to a log cabin. Where you want a rustic look.
If I were doing it on a modern structure I would sheath with a full exposure rated plywood or other panel, and then apply cosmetic battens over that.