Say that you build a vaulted ceiling with 2 x 10 rafters, and install closed cell spray foam against the bottom of the roof deck, filling around the rafters. Now say that over the next few months, the rafters shrink 3/8” across their width. Will this cause the bond between the foam and the rafters to shear?
Discussion Forum
Discussion Forum
Up Next
Video Shorts
Featured Story
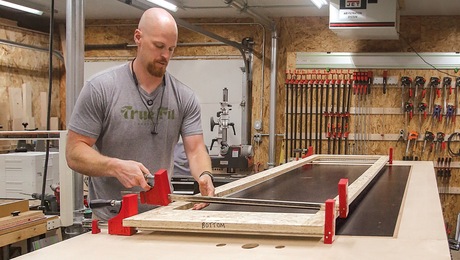
A custom finish carpenter shares how he designed and outfit his two-car garage shop with all the tools, jigs, and accessories he needs to comfortably do great work.
Featured Video
How to Install Exterior Window TrimHighlights
"I have learned so much thanks to the searchable articles on the FHB website. I can confidently say that I expect to be a life-long subscriber." - M.K.
Replies
width or depth?
A 2X10 is only 1-1/2-inch thick, if it shrinks 3/8-inch it has shrunk 3/12, or 25% which is way more than is possible with any structural grade of lumber. Even if you started with it green, the most I think you will see is about 10%, from saturated to oven dry in Western Larch. .
I am referring to shrinkage across the width. I have seen 2 x 10s shrink 3/8" or more across the nominal 10" width dimension. I assume that any significant shrinkage of the lumber would cause it to shear the bond that the foam has produced.
Here is what I am getting at. Closed cell foam is claimed to be able to act as its own vapor barrier, and therefore, not need an independent polyethylene film vapor barrier on the warm side of the wall or roof with vaulted ceiling. However, for the foam to serve as a vapor barrier, it must be form a continuous surface that does not leak vapor. This raises two concerns:
The lesser of the two concerns is that vapor will be stopped by the foam, but will be able to penetrate the studs or rafters. As it does so, it may condense as it moves through the wood. This internal wetting of the wood may not cause rotting, but it will raise the moisture content of the wood during the coldest weather. Then the wood will lose moisture as the temperature cycles back to warmer periods. So the cycling gain and loss of moisture will cause the framing to swell and shrink in a fairy frequent cycle.
The greater of the two concerns is the intial net shrinkage that often occus as kiln dried lumber loses more moisture after installation. This may shear the bond between the studs / rafters and the foam. This shearing will begin at the interior side of the foam because both the foam and the rafter will be locked to the common base of the roof deck. So the greatest difference of movement will be toward the interior of the room. This shearing will create a gap that vapor can penetrate and move toward the outer, colder regions. As it does so, it will condense and wet the outside of the lumber. Again, this will cause a swelling of the lumber, which might encourage further shearing of the wood-to-foam bond, thus deepening the gap.
So, altogether, this breakdown of the foam vapor barrier at the studs or rafters seems likely to lead to rotting of the wood members and the growth of mold, particularly because the moisture produced by condensing vapor will be trapped around the wood by the moisture-proof foam.
I don't think you would have a problem
The foam is somewhat elastic.
The wood doesn't change moisture content quickly, as in a daily swing, it takes a week or two so nothing is going to happen quickly. But, the foam will probably loose elasticity as it ages.
So, I think you could be on to something, and in fifty years we may actually know. That is part of the problem, with the rapid changes in emphasis, and the new materials we are seeing now. Very little of it has actually stood the test of time.
The fact that you are seeing considerable shrinkage of kiln dried lumber limplies that you ae somewhere with a very low realitve humdity. So, there may never be an issue where you are.
I know that where I am, the probability of moisture damage is pretty low. Snow sublimates here in the winter, so things are really dry. We have 70-year old timbers in direct ground conatact on some of the older buildings, that are not showing any signs of rot.
Those 2x10s will shrink 3/8"
Those 2x10s will shrink 3/8" as they dry... but how will they dry when they are surrounded by vapor retarders? When sealed on their 9.5" faces, they will only be able to release moisture through the edges and ends. Depending on the construction details, the path to dry may only be on the interior drywall side or only on the exterior side. But even these pathways are pretty slow pathways, and that slow movement out might reverse during the seasons change, so they may be taking a small amount of moisture in every year as well, further slowing the total dry time.
Rafter Shrinkage
Yes I see your point about the foam slowing the moisture release and absorption. When I mention the 3/8" shrinkage, I am referring to the loss of moisture that occurs when the new lumber loses its excess moisture initially upon installation. That change is often many times greater than the seasonal loss and gain of moisture after that first intial loss upon installation. In the normal seasonal fluctuation, I would not expect a 2 X 10 width to change more than say 1/16 inch.
The reason I am asking about this is that I am researching the pros and cons of foam versus fiberglass for superinsulated house design. I see several claims being made in favor of foam. Its ability to eliminate the need for a separate film vapor barrier is one of those claims. Yet I have talked to people who have opened up hot roof systems in remodeling projects. They report evidence of moisture and mold as well as foam separating its bond to the rafters.
The proponents of foam boast a claim that foam is very stable and does not shrink or move at all. They also say it is strong. Yet we all know that lumber moves, both in the initial dry-down and in the seasonal changes. The vapor barrier effect of foam can do no good if it is not perfectly sealed to the framing members. So I question the claim that foam can serve as its own vapor barrier.
How can this strong and stable foam remain bonded to lumber that moves?
I suppose the answer is to eliminate conventional framing lumber. But I'm not so sure that KD lumber will shrink all that much from purchased dimensions. An interior vapor retarder could also be used to further reduce air infiltration.
I think the key to this is to not use wet lumber!
I live in SoCal where the air is pretty dry. Our wood is all DF, probably from Canada. It's usually soaking wet. I stack my wood in my garage to let it slowly dry - If I don't seal the end grain they will dry too fast and check like crazy. I can take the time to do this because I'm a slow as molassis DIY who has more time than sense. I've got some 2x10's right now that measure a little under 9" across after drying out!
Production building is a whole different deal, where you get your materials just in time to put up. All the wood is green and dries in place. With time constraints in putting up a home, I would not be surprised if the rafters still had a bunch of moisture before they were sealed up. That is a fixable problem however! The problem isn't with the materials or the application - the problem is with the planning.
Avoiding the problem
Yes, I would try to avoid the shrinkage either by letting the lumber season for a while or by using something other than 2 X 10s. My experience with this degree of shrinkage has been with 2 X 10 D.FIR-L, S-DRY. So, it is classified as having been dried to 19%.
But even though I would anticipate the shrinkage problem and try to offset it, the industry does not mention this issue when they tell the customer that they don’t need a separate vapor barrier with close cell sprayed foam.
In the larger perspective, I would not install spray foam without a separate polyethylene film vapor barrier.
The only thing you loose by doing that is the added structural rigidity of having a continuos solid bond on the back of the drywall. Not what you are looking for, I know, but that is supposed to be a beni of using closed cell foam.
Question:
Isn't the drywall typically installed after the foam has cured and been trimmed back flush with the studs? How could there be any bond between the foam and drywall, whether using a film vapor barrier or not?
Well, it might really depend on the climate where you are building!
Up in the Arctic Circle that is climate zone 6 and 7, the vapor barrier goes on the inside, as all those walking meat bags give off water through breating and bathing while the outside stays crispy dry from the cold.
Everywhere else, the water vapor comes from the outside, so the vapor barrier goes up there.
In the heating climates, it would make sense to have that air and vapor seal be just behind the drywall. A layer of sealed rigid foam board might be placed before drywall, or you could hang the drywal up (finish it later) and seal it to the studs with foam, leaving the exterior sheathing for after the foam is placed. Probably not normally done like that, but no reason why it couldn't be.
I have read the thread thru and don't see that you differentiate betwen open celled and closed celled foams. The two are very different in the way they each effect and react to the theoretic forces you are cinsidering
As for the reported observances of molds and separation, it would be important to understand the other surronfding factors for that to have any meaning.
In my experience, there are a few things that can allow some minor separation, and thiose are controllable at time of application. A poor mix of the chemicals can leave you with a foam that is too stiff and brittle. A good applicator knows his stuff an will avoid that like the plaque, in part because it will cost him a LOT more per sq ft for the materials to install.
The other thing is if the surfaces are too cold when the spary hits it. The foam will shrink back from the sheathing and or the framing like your ding-a-ling shrinks if you jumnp in ice cold water.
The only complaints or incidents of molds and mildews are from allowing moistrue to migrat to the foam and to condense there. If the foam is thick enough, you have no dew points and no condensation.
Open celled foam tho, will absorb and will hold moisture. Lots of molds are reported with it.
There is no comparison between closed cell foam and a Fibreglas blanket. NONE. That is a race between a leaky canoe and a cigarette boat.
I stipulated closed cell foam in my first post. I agree that the observations of separation and mold growth in the same cavity does not necessarily mean that the separation cause the mold growth. However, it seems to me that separation would certainly lead toward the possibility of vapor condensing in the separation gap as it moves outward toward cooler regions of the cavity.
I am convinced that closed cell foam will be sufficiently impermeable to the passage of water vapor, but I am not convinced that water vapor will not somehow find a path to circumvent the foam. My mention of the bond breaking would be one way for vapor to get past the foam. Your example of the foam not bonding due to the surfaces being too cold is another way.
I agree that spray foam and fiberglass are very different, but I disagree with your assertion that foam is far superior to fiberglass. There are tradeoffs with both materials.
If I install fiberglass batts or rolls, I can do it perfectly. If I use foam, the option for me to install it does not exist. If I hire an installer, I might or might not get a good job, and there is no way for me to check it. It seems to me that there are way too many things that an installer can do wrong to feel assured that the job will be done right on blind faith alone.
I have heard the pitch for foam versus fiberglass, and I feel the claims of R-value are often exaggerated. The claim that it does not need a separate film vapor barrier is dubious for the reasons we have discussed. The claim that foam makes the building stronger seems like grasping for straws. What practical difference does it make if foam makes the building stronger?
Foam has the advantage of a higher R-value than fiberglass, but the disadvantage of a higher price per R-value than fiberglass. The cost of foam installation is highly variable. The higher R-value of foam is an advantage if you want to limit your walls and vaulted ceiling to single studs and rafters, and yet want the highest R-value possible.
I am sure that foam is a fine option for people if they are routinely building houses with limited wall and roof cavity thickness, and are able to use an installer they know does quality work at a reasonable price. But that would not be my circumstance, so I would rule out foam and use fiberglass. I have already done it once for a superinsulated house, and have had no performance problems.
I thoughtthat you were lookingfor information to make your dcision which to use, but I see you have already made up your mind based on cost and innaccurate assumptions so I won't bother taking the timeto dis-abuse ou of your errors
Well, my mind is chageable, so I would indeed like to hear your comments on my assumptions. I won't commit to a final decision until I build a house or write a book about it. I have never used spray foam, and had a neutral opinion of it until I read an article in Fine Homebuilding (July 2009) about it. After reading that article, I decided that I would not use foam.