I want to build a home with decks on three sides cantilevered out more than eight feet, (on two of the sides anyway). I’d like to build the decks out of reinforced concrete for a number of reasons. Anyone here familiar with this sort of thing? Any ideas on where to find out how to go about it? Thanks.
Discussion Forum
Discussion Forum
Up Next
Video Shorts
Featured Story
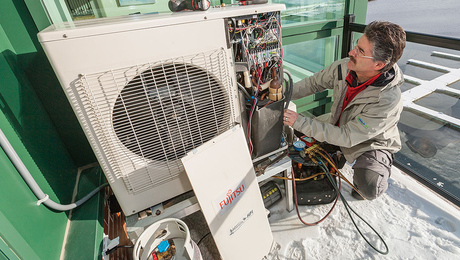
Self-installing an HVAC system requires a lot of thought and planning.
Featured Video
Builder’s Advocate: An Interview With ViewrailHighlights
"I have learned so much thanks to the searchable articles on the FHB website. I can confidently say that I expect to be a life-long subscriber." - M.K.
Fine Homebuilding Magazine
- Home Group
- Antique Trader
- Arts & Crafts Homes
- Bank Note Reporter
- Cabin Life
- Cuisine at Home
- Fine Gardening
- Fine Woodworking
- Green Building Advisor
- Garden Gate
- Horticulture
- Keep Craft Alive
- Log Home Living
- Military Trader/Vehicles
- Numismatic News
- Numismaster
- Old Cars Weekly
- Old House Journal
- Period Homes
- Popular Woodworking
- Script
- ShopNotes
- Sports Collectors Digest
- Threads
- Timber Home Living
- Traditional Building
- Woodsmith
- World Coin News
- Writer's Digest
Replies
Cantilevered from what?
I do commercial plumbing & have seen plenty of these decks on highrises.
6' is common, but have seen them up to 12'.
Post tension is the more common approach verses a thicker slab.
I fear no man & only one GOD. Me
It's done all the time in concrete construction. The downside is thermal bridging between the interior and deck slabs. The way to do it is to decide what size you want and consult a structural engineer who will spec. slab and steel for you.
Try doing an advanced search. I remember several threads on this topic with sound advice.
Ah, so the temperature of the slab is transfered to the interior part of the building? Never thought of that. I'll have a look around with the advanced search. Good suggestion.
"Ah, so the temperature of the slab is transferred to the interior part of the building? "
Yes, and there isn't any really good way to avoid it. Modern Swedish concrete construction often has the decks hung from the roof, attached only by steel ties to the wall, and some cities like Montreal have tradition of wrought iron balconies bolted to the exterior. Mostly it's just ignored. I have worked on hi rises in Ottawa where the only insulation at the deck junction was the carpet under your feet.
If you used a different structural system but wanted a concrete surface, you could use a metal pan with a concrete topping and isolate it from the interior. Depending on the length of the deck, the cantilever might be a little easier labor/budget-wise as well.
Hire a structural engineer. Make sure he inspects and signs off on the rebar placement prior to concrete placement etc. Load path would be simpler with concrete interior slab as well.
sunsen,
Probably not what you are looking for but ....
Last job I did used concrete "core-deck" ( prestressed concrete planks) cantilievered out over the foundation wall and then a cap slab poured over the top of those.
Just another way to skin the cat.
I'll have to look into this option. Sounds interesting though I can visualize some limitations as I think about it. Might be wrong there though. Thanks.
sunsen, Well if you are actually considering this solution then I will share more. It took more than just the prestressed core-deck to support the cant. There were a number of 5/8 rebar layed into the capping slab , as well as bar coming up out of the foundation walls that was then bent down into the slab. Also at the perimeter there were 4 ( IIRC ) 5/8" bar wrapping the core-dec and tied back into the buolding.
Now this was a commercial application and had more than a small chance of having some very heavy loads placed on it so I know from conversations with the engineer of record that he took pains to cover that possibility and still have the cant stay up.
"Poor is not the person who has too little, but the person who craves more."...Seneca
I guess what I'm wondering is how you could do three sides surrounding a building with the core deck planks...? I keep thinking the three sided aspect doesn't allow for cantilevering all three sides with pre made planks, I'm guessing. Any thoughts on that?
Concrete:
Unless you have a rigid concrete beam element around the three sides, you will need a concrete floor. No idea of the design scheme, so to give sound advice is tough (I am a structural engineer). You may want to consider pre-stressed hollow core slab or another type of precast element available in your area. The advantage of hollow cores is they will keep the weight down and can easily accomplish such a span if you allow sufficient depth. A prestressed or post tensioned slab will also perform much better in the long term for a number of reasons. I doubt post tensioned will be cost effective because of the jacks, ducts, rebar and a structural design, but if cost is not an issue and you can find someone in your area to do the work, have at it.
Steel:
Easily accomplished if this is planned before proceeding and you allow some interior columns. Have done greater and stacked considerably more weight than any house atop the cant.
Wood:
Maybe possible if you have sufficient depth for a truss, but definetly tricker and deflection more of an issue.
Thats my two bits based upon the current info. Best of luck.
Thanks Brad. I appreciate the info. I saw a building down the street from me that accomplished what I would like to do in steel. I'm most interested in the concrete options you commented on though, for a number of reasons. I'll have a good look into it.
Do you have a small floor plan with basic dimensions of the overall building including the deck? This is a tricky design because if done incorrectly, it can lead to uplift problems. I assume the roof will cant over the deck, but will not bear on the deck? This does have similarities to Frank Llyod Wrights Falling waters. Are you aware of all the structural problems with his design?
Brad, I am aware of some issues with Falling Waters, and that it is, (or was), in a total rehab.
But from what little I have read, I didn't see anything that would be too difficult to overcome, with modern methods and materials. The biggest one I recall was the deterioration of the reinforcing, as water penetrated the cracks.
So, what else are you aware of?
I'm just a knock about engineer who designs stream restoration/rehab projects, and a few odds and ends related structures. I really would like to know, what else was wrong that couldn't be readily overcome with modern methods and materials.
I did not follow all the rehabilitation works at falling waters, but was aware of the sagging issues and the Wright arch's not agreeing with the structural engineers. All totally fixable using any number of current technologies. The spans were really not that extreme, but Wright wanted the thin look. The only point I was trying to make, was to be careful with his design. I find the trend with houses today is they are getting more and more difficult (large openings/tall walls/great rooms....) yet building codes do not always require the correct professionals to assist in designs. I read one article from an architects assocation where they wanted to eliminate structural engineers from multi residential projects that were less than 9stories, yikes.
Yes, that is scarey. Statics by grapical methods, doesn't really prepare them for real strutural analysis. But, they can just cook book their way through, and it will always work, won't it?
I was just up at the property this morning taking accurate measurements of the building site. I'll be drawing the design with a cad program and as soon as I have something I'll post it. The house sits on a ridgetop of sorts. I found this link to the Falling Water story the other day when I really started contemplating doing the design, although the real inspiration comes from a place known as the "Sturges house" Wright designed in Brentwood California. His design has a brace I'd like to eliminate as my cantilevers aren't going to be anywhere near as severe.
http://www.engr.psu.edu/ce/Divisions/structure/Research/FLW_research.htme
sounds like you have a nice site and are prepared to build yourself a nice home. You might want to find one of those fancy archs pretty early on to help get your vision down on a piece of paper. Sure everyone here will gladly give you some suggestions how to build the structure. I presume you are in the early planning stages and are trying to get a grasp on the ever present cost issues.
Actually, I'm planning on doing the design myself, (that's more than half the fun!), then having a structural engineer fellow I know do the calculations and stamp the plans for me. He doesn't seem to have a lot of experience with the concrete/cantilever aspect of the job though so that's why I was wondering here. I've noticed that sometimes engineers farm out different parts of the job to various specialists. The last house I built had a different guy for the basement, (it was fairly involved, this being earthquake country and all). So maybe that's what will happen on this job. I'm just a builder so what do I know...?!
The site really is nice. It's about a half hour from Calistoga, in wine country, and I sure love how it feels to have so much nature around and about. I'm pretty excited about the whole deal.
I understand. When you post your plan can you attach a site pic, so we have a better idea of any constraints. Precast is great, but if you have any overhead restrictions or other site constraints you could very quickly end up needing a 100t crane or greater, and I am sure you know what those cost. Any geotech issues, slope problems...? Any flexibility where your stair core is located? If this can be located centrally in the building, it could be used as your primary support element for the cantilever concept. If there is a predominant view side, you might want to consider a larger cant on this side as a gathering location, seating area...
I know you had mentioned you were going to do some research into the precast idea. The PCI (Precast Concrete Institute) website is a great resource if you didnt find already. http://www.pci.org. You can find suppliers and many other resources.
Glad to help, gives me something different to think about other than boring buildings.
This is what I'm attempting to build. It's easy enough to draw on the computer but building it is another story. Isn't that always the case...?
Are you planning on having all that sand trucked in?
Always the case. Could you put a couple of dimensions on this or will the main floor plan print out to some scale? Any problems with a concrete sub floor in your master? Any living space below the master/living room? Seems pretty easy given the foundation requirements to suite the site. Cost concerns? You could drop some fairly serious coin to achieve this. The precast components i design cost anywhere between $20 - $30 per sq ft (can$) and you will need a topping for drainage. I will sketch up some ideas for you to take a look at.
Hi Brad. So do you think there's no way to pour this in place? My thinking was that with enough steel, appropriately placed, and using xypex, an additive designed to seal concrete by chemically altering it's porous composition, I'd have sturdy, weatherproof decks after the pour. My understanding of precast would mean that the panels are built elsewhere, which wouldn't be a problem, but I don't get how you can canitilever three sides of a building on account of the panels would have to extend into an area that is already occupied by a panel oriented perpindicular to itself, (if you get what I mean). Or else maybe you'd need some really huge panels, which might be a problem, given that the house is way out in the country.
I had hoped to do concrete floors throughout the area of the house featuring the decks then add a surface layer that would accomodate radiant heat so extending concrete into the interior is not an issue. I'll post a pic of the first floor plan with dimensions as soon as I have a chance. The biggest unsupported overhang is ten feet as drawn. Thanks for the input. Tom
If the cant is still 10', I do not need any other dimensions as I can figure out the dwg scale. Cast in place will work, but the main advantage of a pre-stressed panel will be its long term performance, crack control, ease of construction, speed and thickness. Post tensioning on site does not seem feasible, but without knowing the norm in your area I may be off base. The first thought I had was 4' wide hollow core panels 8" to 12" thick from one side to the other with a topping. Their length would not be a problem unless there are access constraints. The topping could be sloped to drains. The topping is structural because with proper cleaning, a bond will between will develop. Clearly some thermal issues to address, but worth considering. XPEX is great (used in mine), other than retarding the set time.
I was mistaken, the largest overhang is eight feet. The red lines in this plan view indicate the foundation below. Hopefully everything else is self explanatory.
I wasnt sure but I suspected the foundation line stepped out below. All fairly easy now. Can sketch some ideas.
Very cool thread
On a hill by the harbour
I still like pouring the basement, bringing in sand, compact, form slab add post- tensioning tendons and inserts and required knockouts and pour.
Gives you a nice grade to work off, and around. Then dig out sand and sell it to someone .
I drew a sketch of what my thinking is on this deck thing. Does this seem reasonable? Doing the whole deck this way would save enormous amounts of time and energy, (not to mention $'s). I'm wondering if anyone has seen this sort of construction. Also, is post tensioning really that much of a hassle? And for sure I'll be hiring an engineer to do this but I'd like to draw what I want for him first, if it's reasonable.
I've been following this thread with great interest. Little to offer.
Regarding post tensioning, it's something I looked into as a roof alternative for my large span 300 psf roof. So I used steel. PT's a simple concept, but it requires specialized machinery/expertise. Closest crew was 3 states away at that time. Decidedly not commonplace, if extremely effective. Did get a guy to design T beams for me, incredibly expensive.
Looks like you're onto a solution. With the correct shape, you could certainly get adequate strength with thin shell concrete also. But I don't have the details.
PAHS Designer/Builder- Bury it!
Edited 5/19/2007 9:19 am ET by VaTom
Wow, three states away. You'd think they'd be doing it around D.C. all the time. I think I'll find out who does post tensioning in norcal. It is an intrigueing option. Thanks for the encouragement.
That was all I could find at the time, pre-internet. As with anything, you're dependent on who you can find to actually do the work. Gets expensive, sometimes very expensive, to bring in a crew. Unlimited pocket depth, no problem. Mine was the opposite.
Radiant heat with this? Major problem with a not-moderate climate. My experience is solely with inadequately insulated radiant slabs in Denver. Nightmare heating costs. Primarily from the edges.
Forgot to mention that I did find companies that declined residential work. Other than area, my project was more commercial than not.
PAHS Designer/Builder- Bury it!
Edited 5/19/2007 1:57 pm ET by VaTom
Well, I don't have an unlimited budget, that's for sure, heh, heh!
Radiant heat works beautifully around here, (here being northern California). The last couple of houses I've built utilized radiant heat. Personally, I think its the only way to go.
I'll be looking into the question of who does post tensioning around these parts come Monday. I'm thinking talking to concrete guys in the area is probably the most efficient way to go about that. I'll go with steel if necessary but on the face of it I can see many opportunities for cost saving with the poured in place version. It eliminates so many factors. Build forms, place steel, pour, strip forms and you're ready to build the railings and lay the surface material. If post tensioning is necessary that'll certainly affect the cost but building these decks out of steel has to be pretty expensive. There are so many more issues.
Radiant heat works beautifully around here, (here being northern California). The last couple of houses I've built utilized radiant heat. Personally, I think its the only way to go.
Heard that before. Personally, I have no idea why you'd design a house that needed an active heating system at all, but that's me. I don't.
My apparently missed point was that uninsulated edge, that you're proposing to greatly enlarge. Gonna be a major heat loss. Just like those Denver houses. Modern radiant design calls for insulated slabs, particularly from air. Works just fine.
PAHS Designer/Builder- Bury it!
Edited 5/19/2007 5:53 pm ET by VaTom
There's definitely a layer of insulation between the slab and your lightweight concrete, thermal mass layer bearing the tubing. That's how I plan to avoid the heat transfer thing. You pretty much have to do it that way around here. It works great.
I'm reading up on post tensioning and it seems remarkably straightforward. I can imagine you'd need a jack setup to do the tensioning but I can easily lay the tendons in the slab with my guys. I'm wondering why it would be cost prohibitive? Apparently there's a company out of Sant Rosa that does this in the area I'll be building so when they open Monday I'll be on 'em, lol!
Looks about right. Rebar continuous on top to resist sagging, bent down into the supports at the bottom to resist uplift.
One question though--you said this floor would be continuous into the house? I'd be really concerned about water getting in under doorways. I'd plan on at least a 1" lip where you go into the house.
An engineer will be able to plan for inevitable deflection. You'll want some drainage to the outside edge, so a bit of slope is a good idea.
No question I'd be bumping up the thickness at the exterior walls of the house and also sloping everything away from the interior, (although I didn't bother to show that on the cross section). I also plan on doing radiant heat in the house which would mean another layer of lightweight concrete on top of insulating foam bringing up the interior elevation even more. I think that ought to take care of the heat transfer problem someone on here mentioned. Have you ever seen decks done in this manner? It'd be great to know how they held up.
I can easily envision a web of enough heavy rebar to support people standing out at the edge of such a thing. I mean, you'd have a tough time bending the stuff even without the compression strength of the concrete. I just don't know about the sum total of all the weight and cracking and so forth. If the lower course of rebar were angled upward that would even supply some knee brace type action. I just wonder if this has been done successfully and what particulars were.
While the rebar has some compressive strength, the concrete has MUCH more so the knee-brace effect would be insignificant. The structural engineer will be able to tell you exactly how much rebar to lay and what size, where to lay it, where to make your splices, and what type and mix of concrete you need. MOST of the rebar will be in the top, to resist the deck's urge to sag.
Doing gypcrete on top of foam sounds like a good idea for thermal isolation, but you need to cover the 'crete with something. If you want to leave it exposed you'll have to go with portland cement concrete.
This type of deck is unusual for residential work, but it's nothing for a structural engineer who works on high-rises and the like. I could almost do the calculations for you but my structures classes were too long ago, and I don't have the expertise a practicing engineer would anyway.
What you are proposing to do is very similar to how thousands of high rise balconies are built. It is a very common detail which really doesn't require that much steel. As I remember, the last one I had engineered was 8" at the building and 6" at the rail. There is not much point worrying about the rebar size or placement - any Structural Engineer will have standard details for this, as they specify similar designs all the time.
Don't those high rises generally have quite a bit of material on the interior side of the balcony and aren't they prestressed panels? The thing I have a question about is how can you do three sides or even two that are perpindicular to one another? Wouldn't the inbound portion of the panels conflict with one another and if so, how is that dealt with, creating a corner out in space, so to speak? This situation seems different to me in that regard but I could be missing something here.
"Don't those high rises generally have quite a bit of material on the interior side of the balcony and aren't they prestressed panels?"
They have a floor slab inside as you do on the section you posted, but no, they are usually poured in place slabs supported on concrete columns with steel studs or curtain wall systems, so the exterior walls are not even loadbearing.
The whole thing structurally is much like kitchen table supported on legs. The concrete slab doesn't care whether it's inside or outside, or what shape it is. The reinforcing handles all this. In your case the exterior walls will replace the concrete columns, but the interior floor slab can easily cantilever out as your plan indicates.
I don't see the need for complicated pre-stressing or panels. What you are doing is very routine.
Excellent! That's exactly the information I was looking for when I posted here. Just out of curiousity, can I incorporate the railing into one monolithic pour which would include the deck? I can see that saving even more time and money, not to mention I'd get the look I want. I'm thinking a lite dash finish on the whole thing when I'm done.
It would be quite difficult to pour the railing at the same time as the slab. Your concrete finisher is going to want to power trowel the slab and I don't see how he could do a good job if the forms for the rail are there.
We used to pour 30" curbs around the roofs on high rises to hold the snow and provide anchoring for the window washers. They were always poured after the slab and were tied in by reinforcing. Railings in wood and metal are always a maintenance problem. Pouring them might be a bit complicated, but once they are in you sure wouldn't have to worry about them again.
I can visualize a way to form it up using temporary braces and snap ties. I think the braces could be removed after the horizontal portion is poured and then the railings could be topped off. I probably wouldn't need to finish the slab either on account of the stone surface I'll be doing after, maybe just bull float it is all. It's good to know that's essentially what folks do, in two parts anyway, with solid concrete railings. That answers my question. Thanks for the input, it's been helpful!
Good luck and if you get the time when it's finished post pics.
I was looking over your plans on friday aft. Actually, with the reduced cant and the arrangement proposed it is really quite straight forward so long as you willing to cast the complete floor including the cant in concrete and you are not doing a cost comparision(s). An 8 to 10" thick slab will suffice. Only thing I would suggest is that you extend the cant to the main entrance (option #1) or stop the cant in line with foundation wall (option #2). It may be possible as drawn, but the exit stair may cause some difficulty. Only calculation will prove/disprove this.
The tapering as proposed will likely be more of a nuisance than its worth from a cost perspective because from your description of the site it sounds like the entire slab will be conventionally formed. The taper may likely slow the forming process and the added cost of the forming will balance the concrete cost savings. The taper would be beneficial from a design standpoint as it reduces the weight of the cant.
Post Tensioning is not really worth the headache in this case. I should also add that it is not something anyone without specific knowlege should attempt as it is far to dangerous. It would save you some concrete and improve some the long term slab performance, but an acceptable design that meets all ACI code requirements can be achieved with a conventionally reinforced slab. An 8' cant in a residential application does not require post tensioning.
Hi Brad,
Extending the cant to the entry would not be a problem at all. I did find a company in the neighborhood that does post tensioning on a regular basis and they seem willing to work with me on the pour. I'd do the form work and pour the concrete; they'd lay the tendons and do the tensioning.
However, due to a lot of input I've been getting on the one other site I visit and asked this question of, "Chieftalk" over at ChiefArchitect.com, I'm rethinking the use of concrete altogether. One of the most knowledgeable fellows on there advised strongly against it along with a few others, (the architect who advised against is someone I know personally from buiding here in the San Francisco bay area and I trust he knows his stuff), and those folks passed along some interesting information about various concrete issues. So anyway, I'm thinking steel at this time. I just have more confidence in the structural integrity of steel and ultimately, after pricing a few things, I don't think it's going to be that much more expensive. A couple of the guys that have worked with me over the years are about the best welders I have ever seen so I'm inclined to take advantage of that. Plus, since I can keep most of the structural steel work "in house", so to speak, I can control the process better. I do appreciate your input; this conversation has been a very interesting learning experience for me.
I wouldnt be concerned about concrete in the least unless strictly from thermal or cost perspectives. I would not be surprised in the least if it were the most expensive option.
Good luck with the project.
Thanks Brad. This will be interesting, that's for sure.
sounds like a frank lloyd wright style house.
How about some of those reasons?
What's going to be below?
8' is not far.
3 sides is easier than 2. 4 sides is even easier.
Concrete might not be the best material.
Hire an engineer.
My brother did it on his house. The foundation walls are block. The house is on the concrete deck which opened out onto a brick patio. Worked out great. It was a smallish lot and it gave him a nice open feel on the main floor.
Under the cantelevered deck he bolted false beams so they looked like they were holding up the deck.
How long ago did he pour the deck? Is it one slab that overhangs the exterior walls of the entire house? Any issues with deflection, creep, cracking, waterproofing? How about the thermal bridging problem and what was the maximum distance he cantilevered?
This article really made me think twice about using concrete:
http://hoffmannarchitects.com/public/journa/direct/pdfs/vol23n2.pdf
The house is in So Cal so thermal bridging really isn't a big concern. Being in So. Cal it was fully engineered because of the earthquakes. That's the way he builds anyway.
The slab covers/spans the whole foundation. The house sits on only 3/4 of the slab though. The rest of the slab is a patio that goes out over the cantilever. So the house feels like there is a yard on the slab. It's pretty nice on the patio. I don't have a pic of that. I took the pic of the stones above the doors and windows because i did those and I did the arched jams.
I don't know all the details. I just thought you would like a pic of how he did it. It took three years to build.
Personally, I would never do anything like that unless I had a lot of money. To rich for my blood.
I had the time and he wanted the rock work and the jams so I did it.
It does look like you had fun with the stone. I got a kick out of the way the beams are carved too.
Brad485 - I know this is an old thread, but I wondered if you still may be on the forum. You seem very experienced with hollowcore and wondered if I could ask you a question. By the way, where in Canada are you from?