I’m in the process of building insulated doors for a wine celler. The cellar is lined with cedar. I want to case the door with cedar in an arch…What is the best way to do this? I’ve thought of cutting 1×6 cedar into 3/16″ slices and then ‘laminating’ them, Any ideas on the best practices/techniques/process to do this would be greatly appreciated…
Discussion Forum
Discussion Forum
Up Next
Video Shorts
Featured Story
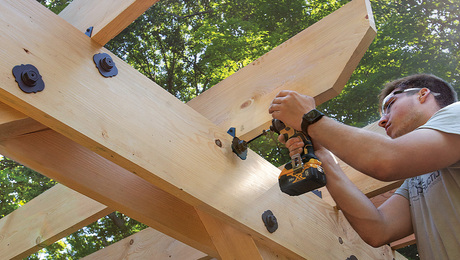
Built from locally sawn hemlock, this functional outdoor feature uses structural screws and metal connectors for fast, sturdy construction.
Featured Video
How to Install Exterior Window TrimHighlights
"I have learned so much thanks to the searchable articles on the FHB website. I can confidently say that I expect to be a life-long subscriber." - M.K.
Fine Homebuilding Magazine
- Home Group
- Antique Trader
- Arts & Crafts Homes
- Bank Note Reporter
- Cabin Life
- Cuisine at Home
- Fine Gardening
- Fine Woodworking
- Green Building Advisor
- Garden Gate
- Horticulture
- Keep Craft Alive
- Log Home Living
- Military Trader/Vehicles
- Numismatic News
- Numismaster
- Old Cars Weekly
- Old House Journal
- Period Homes
- Popular Woodworking
- Script
- ShopNotes
- Sports Collectors Digest
- Threads
- Timber Home Living
- Traditional Building
- Woodsmith
- World Coin News
- Writer's Digest
Replies
DB
If you are not going to have a profile on the caseing and all you are doing is a 1X whatever look than just segment the wood together( like a 1/2 of a stop sign) and whatever your radius is swing that on the segmented piece and you have a piece of caseing.
I'm not sure that is clear, if not let me know and I'll try to post some kind of drawing.
Doug
Doug,
How do you cut out your arch? Have done it a couple of different ways ( havent done it enough to have a 'preferred method' much less proficient). Have cut just shy of arc free hand with a jigsaw and then sanded smooth to the arc line. Have thought about setting up a jig and cutting the arch with a router ( may try that the next time need to).
M2akita
M2
If you have a router that you can put a guide bushing on then you can do it very easy, for instance if you have a guide bushing that is 1" then drill a 1" hole in a long board( length will depend on the radius) then mount a 1/2" straight bit in the router,
Now figure out the radius of your arch, for e.g. if your arch is say 35" radius to the inside edge of your frame than you will want a 1/4" reveal, so you will need to set your router to 35 1/4" for the inside radius on your casing, now if you want the casing to be 4" wide then your radius for the outside radius will be 39 1/4".
Now with a board about 45 to 50" long and about 4" wide you drill a pilot hole 35 1/4" from the far side of the router bit to the pilot hole, this will give you the arch on your casing at 35 1/4". Now screw the board down to a table top or a scrap of ply and mark the point of origin, that will be important. Line the wood for your casing up so that the arch will cut into the glued up wood, screw or fasten it down so it does not move. when you swing the arc and you cut the inside radius you will need to reset the swing point, now you will need to mark for your outside radius, make a mark 39 1/4" from the inside edge of the router bit and drill a pilot hole, now screw that down in the same hole that you swung your original arc from,(that is why its important that you make sure your in the same hole as the original or you will not get what you think you will) now swing the second arc and presto! you've got your piece.
The shop that I worked out of used this method all the time, took about 5 min to swing a arch.
I know that this is long winded but its really not very difficult, once you have done it you will think curves are very easy, I like the router method much better than the others such as band saw or free hand, there is very little to clean up with router bits, go slow and watch your direction so as to avoid tear out. If you would need multiple copies of the same arch don't swing each one, place one on top of the other and draw the arch out and rough cut close to the line, then place back on top of the master piece and use a flush cutting router bit and route out, presto, exact copy.
Hope this helps if not let me know, I don't explain as well as I can show so feel free to ask.
Doug
Doug,
Thanks for the very complete response. This clearly sounds like the way to go. Do you have any suggestions for building the arched jamb? The side jambs are cedar and the door I'm building is Pecky Cypress, so I'm trying to figure out how to create an arched jamb that would look right given these other materials...
DB
DB
Here are some pictures of some of the ways that we would make a jig to do a curved jamb.
First you have to determine what the radius of the jamb that you need is. If your door is built with a radius of say 30" than allowing for a reveal then you may want the jamb to have a radius of 30 1/8" for example. Depending on the radius, the tighter the radius the harder to bend, subsequently the larger the radius the easier to bend. Then the width if your jamb, say 6" for the sake of this, I would resaw some 6 1/2" cedar at a thickness of about 1/4' and sand to finish or plane if you have a planer that can do this thin of wood, to 3/16th or 1/8", that's not as important as getting it to bend to what you need the radius to be. If your jamb is 3/4" then if 1/8" you will need 6 of these, that part is obvious. The reason that I would make the jamb 6 1/2 wide is to resize after the glue up, you wont be able to get the pieces lined up exactly in the jig. This way you can run across a jointer to clean up one edge and then rip on the table saw.
If I was using this as an exterior jamb then I would glue up with West System but you can use exterior glue, or some sort of resin glue.
Build your jig, see pictures, you can do one of two ways(probably more ways, but this is how I would do it) If you want to save some time you can use the one piece jig and still get good results, that would be the pic of the jig with all the red clamps.
You need to swing an arc of the radius desired to build the jig, do the same as the casing. To make the jig wide enough to accommodate a 6 1/2" wide piece you will have to build it wider, see pic.of the larger two piece jig.
I don't want to write a book on this so as not to bore you, I think the pictures will tell a lot about how to do it.
Some people will tell you to overcompensate when building the jig for spring back, don't worry about the spring back, this is woodworking not rocket science, You will have spring back but when you set the jamb in place you shim to the desired radius. There is a picture of a jamb that we did for a house and the door works perfect in it.
Let me know if I need to clarify any of this for you, I've said before that I show better than I explain, right side- left side brain thing I guess.
This is very easy to do, don't worry its just wood, if you screw up you just do it again right, you will learn better that way, just factor everything into it, such as the radius's and all the reveal's
Good luck, again let me know if there is any other way I can help
Doug
Edited 4/2/2003 10:27:14 AM ET by Doug@es
Doug,
Looks like I've got my work cut out for me! I can see where starting with the 1/4" cedar and planing down to 3/16" is the right way to go. Thanks for the advice. I've got a pretty tight radius, but I think I can make it work...I'll send pictures of the completed work.
Best Regards.
Dave
Dave
After I sent the message I thought of about 10 other things that I should have mentioned,
When you glue up make sure you glue 100% of the surface, and if exterior yellow glue remember it will not act as a filler, West system will however fill voids. We would often get our laminants down to 1/8th" so dont worry if you have to take it down to that, not that much more work.
Its kind of a pain cause if you only need the one radius bend then the jig isnt worth much for anything else, we used to through them away at the tune of about 3 to 4 a week.
If you have any questions just ask there are several people here who can help.
Good luck and post pic when you get it.
Doug
Go over to the Knots forum and ask those boys and girls how to do it. They'll show you how to steam bend it, cold form it, laminate with a bag and a vacuum press, carve it, piece it together using funky joints, and probably other methods.
But you will probably end up like me when I did this for a window and some base moldings, and cold-form it using laminations, glue, and a mold. I think you might want strips as thin as 1/8".
I use an adhesive that is just for this purpose, and it has a nice long open time. Highland Hardware sells it, and it is a syrupy liquid with a powder catalyst. Let's you paint it or roller it on both surfaces, lam after lam, and then fool around to get it all clamped up just right, without getting funky on you too early like yellow glue will. An epoxy can be had too, with a long open time, but the epoxies are messy, I think, and a little too slippery, causing your glueup to slide in places you don't want it to.
Go to Highland's website, and look for it. My can on the shelf has the brand name "Urac."
Here ya go.
View Image
Edited 3/28/2004 8:52 pm ET by Bob Dylan
i did an arched window a couple of years ago and had to make pine returns and a flat casing to suit, the returns were about 4 inches deep.
basically what i did was laminate the returns from 3/16 planed pine on a strongback (actually a mold fastened to the floor) to match the curve of the window, then used that as a guide to trim segented pieces of 1x6 pine to make the casing. believe me it was tricky but the final result was what the customer wanted so all were happy!!
some manufacturers offer a molded flexible(with some heat) casing trim that matches commom profiles, but i dont know the source
A router and a tramel is the way to go. After getting it setup it is quick and easy.
This is an active project for me right now and I would like to attach some pics but I am having trouble. I click attach file button and nothing happens. Any help out there?
Usually order the doors with the casing.
Custom built too be sure so time and price a factor.