Fininishing out an existing garage. Need to bring garage floor up to house slab level. (3″to5″) Question. Pour directly on existing floor, use bonding agent, apply/install something to seperate the two, reinforcing of some type, etc.,etc.. All of these and more have been suggested by people I’ve talked too. There has to be and expert out there. Thanks.
Discussion Forum
Discussion Forum
Up Next
Video Shorts
Featured Story
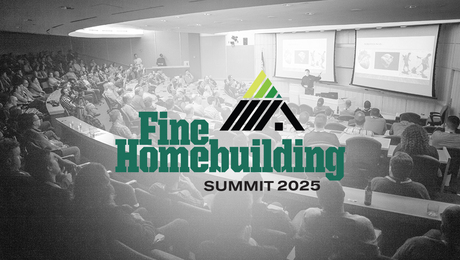
Join some of the most experienced and recognized building professionals for two days of presentations, panel discussions, networking, and more.
Featured Video
How to Install Cable Rail Around Wood-Post CornersHighlights
"I have learned so much thanks to the searchable articles on the FHB website. I can confidently say that I expect to be a life-long subscriber." - M.K.
Fine Homebuilding Magazine
- Home Group
- Antique Trader
- Arts & Crafts Homes
- Bank Note Reporter
- Cabin Life
- Cuisine at Home
- Fine Gardening
- Fine Woodworking
- Green Building Advisor
- Garden Gate
- Horticulture
- Keep Craft Alive
- Log Home Living
- Military Trader/Vehicles
- Numismatic News
- Numismaster
- Old Cars Weekly
- Old House Journal
- Period Homes
- Popular Woodworking
- Script
- ShopNotes
- Sports Collectors Digest
- Threads
- Timber Home Living
- Traditional Building
- Woodsmith
- World Coin News
- Writer's Digest
Replies
it will work but it will crack. why use bonding agent if you going to seperate.
Edited 4/6/2004 8:45 pm ET by BROWNBAGG
Brownbag. I was not saying that I was going to do all of thoes things. I was listing the various things that was suggested to me. Thanks. None
The only reason to bond one layer of concrete to the bottom layer is to give strength to the thinner top layer. In your case the top layer might be the thicker and stronger one. Get 4000 lb test mix and a roll of reinforcing wire and think of the job as a new pour.
Woodman, I'm not concerned about the structural elements. I was thinking that some light reinforcing might minimumize minor cracking. Maybe a lightweight reinforcing like the chicken lath that is sometime used on stucco. None
If all you are doing is raising the level of the floor with no other considerations, to get the best finished product with the fewest uncontrolled cracks, you want the slabs to be physically seperate.
Anything that functions as a bond break will work, I'd probably use a couple layers of Grade D paper (like what you put behing stucco). It comes already doubled up on the roll, so it's easy and cheap. High quality, easy and cheap . . . hmm, I don't hear that very often, do I? <G> Well, maybe back in the old days . . . <VBG>
I'd also run some E-joint (that asphalt saturated strip) around the perimeter.
The idea here is for the new slab to cure as evenly as possible under the least restraint possible. That way as it cures it can shrink the way it needs to with no curling and no uncontrolled cracking.
DRC
Thanks Dave. That sounds good. Makes sense to me. I appreciate the help. None.
Glad to be of help, but actually the thanks are due to Mr. Gabe Martel. I thought I knew something about concrete, but he really brought me up a few notches to say the least.
The amazing part is we've never met in person. Now that's a good teacher.
Thanks, Gabe.
DRC
I was also going to finish out my garage. The thickness of the new slab will only be 1 1/2"-3" from one side to the other. Should this slab thickness be treated the same as you discussed above or is a different technique required to prevent cracking.
It's gonna crack, no matter what you do.
Ray, I think the difference in thickness requires a little mor planning, but no reason why you can't get good results.
Where does the thickness change?
How much of the slab is 3" or thicker, how much is 2" or thinner?
Is it an even or sudden change in thickness?
Will you be driving a car over this slab?
What is the width and length?
Any re-entrant corners, or is it symmetrical?
What is the intended use of the floor?
What will be the finish?
DRC
A much different technique to help prevent cracks, 30% chance (SWAG) of it cracking anyway, but any cracks will be minimized.
You need to respond to Dave Crosby's post first.
SamT
Agree with Dave.
Use a slipsheet of some sort, and treat it like a new slab.
have fiber (as in fiberglass) added to the mix; costs about 7 bucks per yard, and reduces cracks.
Some codes require a drop between living space and attached garage. I won't pretend to know the specifics.
drop usually reuired to keep gasoline/oil spills out of the house
I have been wondering about the elevation issue as it pertains to attached garages, and after much research with the '1997 Uniform Building Code' , I can find no requirement for an elevation change. I wonder why we have always done it? I can't recall one that didn't have some drop from the main house in 30 years of building, but I can find no regulation specifically requiring it.Anyone else?
Heckwhat the heck was I thinking?
when I started my house, I frame the front porch as the same elevation as the slab. County inspector wrote me up on it. I poured it anyway. That was the beginning of the conflict with the inspectors, I wanted it so a wheelchair could get in, with my bad knee I might need it ten years from now.
My post was just from experience/word of mouth mixed/best guess as to why, but I don't know of any code section. Just makes sense that you would want to contain a gasoline spill. Also, I don't think I have ever seen an attached garage w/out a drop down.
gas fumes from a leaking fuel tank in a car -- fumes are heavier than air and because of this the fumes stay close to the slab and tend not to creep into the house -- believe this is why there is a step up from the garage
Rick and Dudley-
I have never seen an attached garage without a step down either, and I agree it makes sense-But is it or was it ever a 'code' call? Mostly curious about something I had taken for granted for years, but recently the issue has a little more importance to me: I am starting a house with an attached garage that is drawn at the same level as the main floor, which is a radiant slab. I questioned the designer, who wasn't sure if this was a code violation. I have posed this question to my building inspector, and he and I went through the current code book, to find no reference to this detail. Later I spent a great deal of time with the code book looking for any reference to floor elevation requirements...to find no reference. I can find no requirement in the 1991 UBC book, either. Nor the dwelling construction guide.So.....what's the deal? Was it a code call at one time? Is it a current UBC requirement, and me and the inspector are blind? My inspector said he would ask some of his supervisors what they knew about it.It really doesn't matter to me what elevation the garage slab gets poured at, it will make no difference to the cost of the structure, but I do want to do it right and to code. If I find out the answer, I will post it here.
Thanks, Heckwhat the heck was I thinking?
since gasoline fumes are heavier than air the drop would help to keep them out of the house.
As I recall, the requirement for open flame (water heater flame if located in garage) is 18" above the floor.
the usual 8" drop (one step) or 16" (two steps) from the house to the garage would be a good kind of back-up protection against a failed door seal, etc.
This does sound like something that could be in a code somewhere. But even if not, the code is only the "bare minimum for safety" anyway.
Now, if you would like to eliminate the step for other reasons in your project, and find there is no code requiring it, you might want to consider some passive ventilation of your garage space or something.
Modern cars leak very LITTLE fuel vapor, but things do go wrong with all machinery, eventually, and lawn mower gas cans and so on could leak.
Hope this helps,
Norm
DONT FORGET TO PUT EXSPANSION JOINTS AROUND THE PERIMITER WET THE CONCRETE AND COVER IT WITH PLASTIC IT HELPS MAKE THE CONCRETE CURE BETTER
All concrete does not crack.We pour concrete a couple times a week and it rarely cracks.Most cracking is do to high water content.Most people try to make the job easy by adding water.Water wakens concrete.The other factor in cracking is not retarding the cure.The surface will try to cure faster then the core and since concrete shrinks when cured it cracks within itself.We always cover the slab for two days or use a curing agent on the slab.If we need more workability we will add a plastisiser to make the concrete perform as if it had more water but its just chemical.I was at a job today with a slab 28 X with 10 wire on six inch centers on two inches of insulation and radiant tube.After 6 months not a single crack and we didn't cut any week joints.I just want you guys to know with the proper care and planing your slabs will come out fine.Also don't get cheep and pour less than 6 sack mixes.
Rod
IASM, you're on the right track there, except for one minor detail. Concrete cracks when it drys before it cures.
As it drys, it shrinks like a sponge does when it drys. Too much water in the mix causes small voids that become cracks as the water evaporates.
SamT
Also if your floor is not all one pour, IE. there are planned cracks and you want to overlay it i'd consider lining up those cracks with planned cracks in the new surface. Chances are they will reflect up regardless.
It sounds like you're converting the garage into finished living space? If so, you could always put in sleepers and a conventional wood subfloor.