I am about to have a garage built, slab on grade, 24’x32′, 12″x16″ footing. Just wondering if it would be better to use wire mesh in the floor or to use the fiber that get mixed with the concrete at the batch plant? Is one better than the other? How good is the fiber? Thanks.
Discussion Forum
Discussion Forum
Up Next
Video Shorts
Featured Story
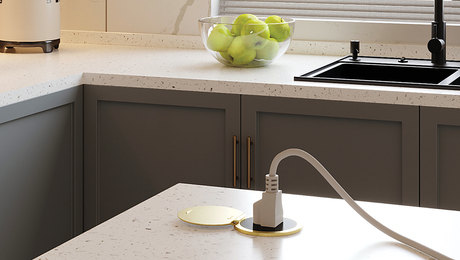
A new code-compliant, spill-safe outlet from Legrand offers a sleek solution for a kitchen island plug.
Highlights
"I have learned so much thanks to the searchable articles on the FHB website. I can confidently say that I expect to be a life-long subscriber." - M.K.
Fine Homebuilding Magazine
- Home Group
- Antique Trader
- Arts & Crafts Homes
- Bank Note Reporter
- Cabin Life
- Cuisine at Home
- Fine Gardening
- Fine Woodworking
- Green Building Advisor
- Garden Gate
- Horticulture
- Keep Craft Alive
- Log Home Living
- Military Trader/Vehicles
- Numismatic News
- Numismaster
- Old Cars Weekly
- Old House Journal
- Period Homes
- Popular Woodworking
- Script
- ShopNotes
- Sports Collectors Digest
- Threads
- Timber Home Living
- Traditional Building
- Woodsmith
- World Coin News
- Writer's Digest
Replies
Screws vs nails, Tyvek vs felt, wood vs synthetic.
A good fiber job is better than a lousy mesh job, certainly. Some mesh is so lightweight as to be useless, and often the stuff is improperly installed. And you need rebar in the footings, at least.
Any particular reason...
... you needed to ask the q 2x?
Maybe he couldn't find his way around?
http://forums.finehomebuilding.com/breaktime/construction-techniques/concrete-fiber-vs-mesh-0
Matbe it's like the guy who gets drunk on Ebay and ends up bidding against himself
I've done many slabs, much larger than yours, with fiber reinforced concrete, no wire mesh. Some building codes may have stipulations concerning rebar in the footings or using wire in the slab, check yours. This page says it all in my experience.
http://www.westrocinc.com/Concrete/Additives/Fibermesh/fibermesh.html
slab on grade, 24'x32', 12"x16" footing
huh, does this 'garage' have a 2 story apartment building built above it??
Somebody just trying to sell you a lot of concrete.
6" by 12" footing is fine for a garage unless you are bulding on soft clay or similar place like where the tower of Pisa was built. Low slump 3-1/2 non reinforced floor OK on most undisturbed soils.
Also, you don't even need rebar or mesh if you keep to 2-1/2 or 3" slump - most contractors around here throw in reinforcing 'cause they like to pour 10" slump soup vs. concrete !
Junk:
If it is a mono-slab, here anyway, 16" thick footings with a 4" slab on top are SOP. The idea is you have 12" below grade (min required on our state) and 8" of concrete exposed above grade for 20" of total thickness. Siding laps down side of concrete a bit, leaving a net of maybe 6.5" of foundation exposed, or in other words, the siding is 6.5" above grade. That would be for 1 or 2 stories. Haven't build 3 stories on top of a mono-slab. BTW – we don’t use rebar in these type of footings unless the soil is not 100% or unles it is specified on the plans by the engineer which is rare. Everything is inspected and if there is any fill BI requires letter from Soil Engineer.
Little story: One time had a soil engineer out to verify a substraight below a mono-slab house. It was engineered fill which had been placed a year or so earlier, (soil lifts inspected by the same engineering company as they were placed) so the idea was to have them back for one last check before placing the concrete to get a "transfer of responsibility:" piece of paper. Edges of concrete were the above standard 20" thick. So, the douche bag engineer tells me that the 20" thick concrete will be compromised by a 2" piece of PVC DWV pipe that is in the footing to drain a lavatory - perpendicular to the footing. OK - it was about 3" total as a 2" sched 40 pipe is about 2.25" plus it was wrapped in foam for isolation. Engineer says that the pipe has to be set below the footings. Admittedly the plumber should have set the whole drain system lower, but to fix the issue would have mean totally redoing all the slab prep (gravel, plastic, wire, etc) and the plumbing ground work, or maybe adding a few more inches of concrete for a cost of maybe $1 or $2 K. So much for engineers with common sense.
So, I tell the guy that the 2” pipe is NOT going to compromise 20” of concrete and explain to him that the only reason it is 20” thick is to get the foundation up above grade enough. He tells me “Look – I’m NOT some rookie soil tester, I’m a real PE, who normally works in the office but just had to come out here because we were short today of field testers”, and “This has to be fixed”.
Then I pull out the big guns: :-) I tell him: Look: first of all you are here to inspect the soil, NOT verify the footings and slab. Next, if you write that down on that test report when you hand me that piece of paper I’m gonna crumble it up and throw it on the ground and be on the phone to another soil engineering test company before you can get in your truck”. :-) "OH - and I'll make sure my company never uses your company again". I think we were both taken aback…. :-)
So he says “wait a minute” and gets on the phone. When he gets off he says “OK – put 2 pieces of #4 rebar above the pipe and all will be good.” :-) We shook hands as he left. Maybe with his tail between his legs. :-)
I was just looking at a house yesterday (my son't interested in buying) that was built about 1950. The house was in good condition, and the garage looked good on the outside, but the slab was badly cracked. Even though the garage was sound -- no rot or leakage anywhere, it's predictable that it will have to be torn down or extensively rehabbed in the next 10 years or so because the slab is moving apart in three directions and taking the garage walls with it. One crack was through the side door opening and had just about spread the door frame as far apart as it could be and still latch.
So by my estimation something like rebar in the footing is worthwhile, to simply keep the whole slab more or less together.
Actually rebar is to add tensile strength.
Wire is installed to hold the slab together. In the example I have above, the point was that a 20" thick piece of concrete is pretty stout even without rebar - although we actualld do use wire... Also consider theat the here ground does not freexe to a depth of more than about 1 inch.
In your garage example, the cracking was probably due to freeze/thaw of the substraight or am unstable substraight. Further, if you are saying it is a mono-slab - and I'm guessing it is in MN where you are, what do you think the chances that the footers don't even extend below the fost line.
Certainly in the case I was quoting (and I've seen other similar cases from the same era), there's a good chance that ground prep was poor and there is a minimal footing. But the point remains that you need something to hold the slab together. Even with a good footing, if the slab itself freezes there's going to be frost heaving outward that will want to tear the slab apart. Cracks in a garage slab are ugly but generally harmless, but when pieces begin to move different directions structural integrity is threatened.
I hate wire mesh.
The trouble with 6" x 6" mesh is that you can't walk anywhere as you're placing the mud, or the damn stuff gets trampled down to the bottom of the slab where it's worthless.
The slabs I'm doing right now, I'm going to put in #3 rebar on 12" centers on 2" dobies. That lets you step in between the bars, no problem.
I'm also putting 8" of #3 gravel under the slabs, and running a plate compactor over it. (Waiting on the next load of gravel at the moment....)
-- J.S.
#3 gravel?
How do you all size your rock?
Around here #3 is 1 1/2" to 3", and that stuff won't compact with a plate compactor. It take a good size vibrator/roller to get 6" of it down for a common asphalt driveway.
I have started using washed #8 or 9's lately. It pretty much self compacts when it is shot in. I single 6" lift and a follow on with a plate compacter will ussually yield about a 5 to 5 1/2" base. it is also a heck of a lot easier to grade than #57's (3/4").
#3 Gravel ....
At Balboa Brick & Supply, #3 means 3/4" & smaller, with a fair amount of crusher dust. I'll be hitting it with the plate compactor tomorrow. I'm doing the excavation, base, forms, and rebar myself, and hiring out the place and finish work.
-- J.S.
Here in central Va stone is sized like Dave's. # 3 can be 4" depending on which supplie delivers. 57's are the washed about 3/4". 21A is the 3/4 and smaller with crusher run fines in it. A good driveway topping.
Frank DuVal