I am about to pour a slab on a small airplane hangar and have a question about the door details. The building is in NH, is 48’x48′, has a 4 foot frost wall on a 12″x24″ footing, will be wood frame above. Lot of steel in the foundation wall and footing. The concrete walls go about 12″ above grade, except where the doors are and then they drop to grade. The interior of the walls have R-10 EPS Performguard insulation from the footing to the sill, and the entire prepared slab gravel base has more R-10, 2 1/2″ foam (over 6 mil poly). The slab will go to the interior of the foam, not touching the walls, and will “float” on the foam underneath. Radiant heated floor, PEX 10″ OC, #4 rebar 20″ OC, 5″ 4,000 PSI mix. Residential garage-type floor loads. Site has water and poor drainage–Removed clay base, 3 feet of gravel inside the hangar walls, well compacted, footing drains to daylight.
I had planned to pour the slab over the foam and over the concrete wall door drops(in the foundation wall which has vertical rebar every 4 ft. to bend into the slab), but I have become concerned about cracking of the slab across the door openings due to load concentrations at the door openings (movement of the base, creep deflection of the foam, …). The entire 48×48 slab will be floating over the resiliant foam, except at the concrete door drops. Or should the foam insulation extend under the slab and over the foundation wall door drops to completely isolate the slab/wall intersection? Eliminate the rebar sticking up from the walls in the door openings? The doors are a 3′ man door, a 40′ airplane door, and a 9′ roll-up garage door.
Thanks for your advise.
Discussion Forum
Discussion Forum
Up Next
Video Shorts
Featured Story
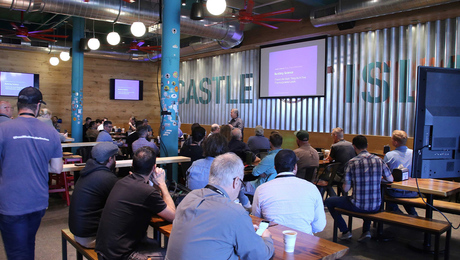
Listeners write in about shower panels and cordless tools and ask questions about old wiring, air leaks, and gutter covers.
Featured Video
How to Install Exterior Window TrimHighlights
"I have learned so much thanks to the searchable articles on the FHB website. I can confidently say that I expect to be a life-long subscriber." - M.K.
Fine Homebuilding Magazine
- Home Group
- Antique Trader
- Arts & Crafts Homes
- Bank Note Reporter
- Cabin Life
- Cuisine at Home
- Fine Gardening
- Fine Woodworking
- Green Building Advisor
- Garden Gate
- Horticulture
- Keep Craft Alive
- Log Home Living
- Military Trader/Vehicles
- Numismatic News
- Numismaster
- Old Cars Weekly
- Old House Journal
- Period Homes
- Popular Woodworking
- Script
- ShopNotes
- Sports Collectors Digest
- Threads
- Timber Home Living
- Traditional Building
- Woodsmith
- World Coin News
- Writer's Digest
Replies
I did the same sort of thing and the concrete guy put that 1" kind of soft material right at the outside edge of the apron that is the depth of the garage door jambs...and then poured the driveway right up to that joint in a separate pour the next day. That material is the only separation between the warm slab and the driveway, which I'm not worried about since a few stray btu's can serve to keep the ice melted a bit. That was in June, no movement yet , I'll know more next spring after a few freeze/thaw cycles.
I hope you get someone with more training or experience than me to give you a more solid answer, but I'll offer a suggestion.
If I understand your description, you'll have a 5" slab supported on 2½" foam, which you are considering bringing out to the edge of the slab where the doors will be. In that case, I think your concrete will crack. I would consider still using the foam, but thickening the slab at the doorways and installing additional rebar, making the edge, in effect, a grade beam.
You may want to have a local civil engineer whip you up a solution, calculating the concrete thickness and rebar placement.
I would definately lose the vert rebar 48"OC. 48"OC is not enough to do any good. #6 @ 12"OC would work.
Run the foam up to the door sill, the isolate the slab from the sill with 1/2" foam, scored 3/8" below finish concrete. After the pour, remove the top 3/8" of foam and seal the gap with a approved polymer.
Triple up the PEX for 2' in front of the 40' and 9' doors and double it up for another 2'.
Double up the PEX around the complete perimeter and in front of the man door for 4' inwards.
Other thoughts:
I would use foam only for 4' around the perimeter and add 2 1/2" gravel in the field.
I would use #4 rebar @ 12"OC and PEX @ 12" OC. Except in front of the doors and around the perimeter.
Limit the length of any given PEX line to 400' to 500' and try to achieve a cross flow effect where the fluid flow in adjacent lines is opposing.
See my exquisite drawing attachment
Can you garuntee that a loaded fuel truck will never drive inside?
SamT
Hard to give concrete advice :) without seeing the site and reviewing the soil reports and specifications.
I would forget about pouring the threshold monolethic with the main slab. Pour them separately and install an expansion board between them as well.
Your main slab will not have too great a live load by itself but you do have a large area to concern yourself with. The wheels of a small plane don't represent as much loading as a car wheel but if the substrate is not rock solid and consistently supporting the slab, it is enough to crack a typical slab.
At the very least, I would divide the slab into 4 separate zones and pour them separately.
Gabe
Many thanks for the replys. I normally do remodeling work and don't have much experience with large concrete jobs.
It really makes sense to me to isolate the floating slab from the stepped-down foundation walls at the doors. Couple of questions:
1. Gabe suggests a separately-poured door threshold area isolated from the slab. Sounds like a good idea. Would a monolithic slab pour to the outside of the wall with a deep saw cut couple of feet inside the building parellel to the door be equivalent? In either case, should the slab rebar extend through from the slab to the door threshold area?
2. What if we extended the under-slab foam insulation under the slab and over the stepped-down foundation in the door areas? Eliminate the vertical rebar too. Wouldn't that serve to isolate the slab and wall?
3. Gabe also suggests doing the slab in 4 pours. Given the radiant PEX, (tubing everywhere, one big zone) would be complicated. We had planned on 1"+ sawcuts every 8-10 feet. Would this be equivalent? We have done everything we can to compact the substrate-used good gravel, big Bomag vibratory roller, jumping jack along edges, sat open all summer in the rain-forest downpours we had, etc.
Thanks again!
One of the least considered aspect of slabs is shape. Yet shape has a lot to do with cracks and pressures.
If you draw your slab on paper you will see that by extending it over the threshold you are creating 2 inside corners. If you put pressure on an inside corner, you will create a condition for cracking.
If your slab is floating, then it must be independant of all structure.
The reason I was dividing your slab pour was more personal than absolute.
First, 48 by 48 is a large area to control and by dividing it into 4 areas of 24 by 24, you minimize the stress on the slab.
Secondly, by dividing into manageable pads for pouring the concrete and subsequent finishing is easier.
Third, by having your tubing in 4 areas, IF you did have a serious problem, the remedy would be 1/4 of the headache and cost of one big slab.
Taking the afternoon off for some early fishing.........be back later this weekend if you have other questions.
Gabe
2. What if we extended the under-slab foam insulation under the slab and over the stepped-down foundation in the door areas? Eliminate the vertical rebar too. Wouldn't that serve to isolate the slab and wall?
Yep, especially if you use a thermal break between the slab and sill.
Given the radiant PEX, (tubing everywhere, one big zone)
I do hope you mean several parallel zones and not ONE BIG ZONE! you're talking about around 2500' of tubing and no way is water gonna stay hot thru that length. Most of the literature I have studied limits any individual run to less than 600' and the prefered method seems to be 400'.
The one that did suggest 600' said it was because PEX comes in 600' rolls, so there would be less waste. And you don't want any joins that would be buried under concrete 'cuz of potential leaks. If you do use 600' runs it is more important to lay the PEX in a cross flow pattern to help prevent cold spots.
A cross flow will have one runs cold end next to another runs hot end. Another bene from it is that if one run does develop a leak and you have to shut it down there is still a good run in the spot since with a cross flow there must be 2 runs in each zone.
This does not add significantly to the cost as each zone is twice as large as a single tube zone.
When I reccommended that you only use slab insulation around the perimeter, I took into consideration that radient heat is too slow to use only part time, therefore the heatsinking of the bed gravel would not be a problem.
SamT
Sam T, Thanks, We ended up running the PEX over the weekend. We used up about 3,000 feet, broken into 10 nearly equal 300ft. runs. Manifolds for the 10 supply and return loops. The loops were run serpentine-style, so the cool return and the hot supplys were naturally next to each other. I had built a nice PEX un-spooler from scrap stuff which worked really well. Hard to imagine doing a job this size without it.
Thanks, Dick
1"+ sawcuts every 8-10 feet,,,,,,, Wow, a brave individual, thats according to my way of thinking. On this one,I wish you, the best of ,,, Luck?? Jim J ps I would sure keep a close eye on just what that tubing is doing at time time of pour.
44,
Yup, I sure would not want to nick the tubing! The floor is 48'x48', with 3,000 ft of pex tubing. Rebar is 20' OC each way. We laid the North-South bar. Then zig-zagged the tubing parallel to the NS bar, tying with ties. Then over that, we laid the E-W rebar, adjusting the ties so the tubing, which is 10" OC, is straight and parallel, and spaced off the rebar it is parallel to. It is easy to do it this way, and it ensures that the pex is held under the top layer of rebar. It took a couple of hours to arrange the tubing and to tie it neatly. I do not think it will float up during the pour such that it will get in the way of the saw cuts. Doesn't mean I won't worry though!
Tie the slab to the foundation wall at the door. The wall should be stepped down at the the door 8" - 10" below the top of the slab. The wall should have a key and #5 bars at 12" - 16" o.c. that can be bent into the slab. The slab should have a thickened edge at the wall with a couple of #5's running the lenght of the opening. You want the slab to move with the building not the driveway.
I disagree.
A floating slab should be independent of the building. The worst thing would be to tie it at any one end.
Gabe
I disagree. At doors you want the slab tied to prevent movement and creating a hump at the threshold. We sometimes tie the drive way into the garage slab with a thickened edge that has bars extended into the garage slab. The garage slab floats at all of the other edges. Never had any problems in Chicago with differential movement cracks.
Archy, any place you have a large point load moving from one slab to another, like a hiway or garage sill, there will be differential movement between them. In california, land of the earth moving, I worked on a 150', 4 lane concrete box beam bridge. The ends of the bridge sat on a 4" thich styro/poly foam pad.
The foam will absorb the movement and rebound. If the slab, with or without a 'grade beam', is resting directly on the concrete ledge at the sill, it will crack where the point load crosses from solid bearing to foam bearing.
The threshold spoken of above, if it has no foam insulation under it, (the gravel will also absorb force and rebound, though,) just moves the line of transition away from the sill.
Build in a "crack" by running the insulating under-slab foam up to the door sill, then isolate the slab from the sill with 1/2" foam, scored 3/8" below finish slab. After the pour, remove the top 3/8" of foam and pour a freeze proof, flexible, hi bond polymer into the gap created.
The foam will bridge the abrupt transition from rigid support (the foundation ledge) to flexible support (the gravel bed.)
SamT
I need to do this, as I have done what you described with a slab and apron joint...but what brands/source can you recommend for:
" a freeze proof, flexible, hi bond polymer into the gap created. "
Sonolastic SL1. self leveling, good stuff!
Go with Gabes advice on the seperating the interior floating slab from the apron. Your interior perimeter insulation provide a thermal break from the foundation stem wall. Why compromise it at any opening? To me there is no such thing as a minimal heat loss at those opening, if it can be avoided with a good thermal break.
I might leave the vertical steel in the dropped portion of the foundation wall, but turn it out into the approach aprons. A lot of that decision would be based on personal experience with local soil and climate conditions.
Dave
http://www.epoxysystems.com/proguide.htm#Expansion%20Joint%20Materials
I'm not familiar with this. I googled to find it. They specialize in runways.
Hope it helps,
SamT
What..........no crack in Chicago?
Never had any problems in Chicago with differential movement cracks.
That cost you a little credibility.
We sometimes tie the drive way into the garage slab with a thickened edge that has bars extended into the garage slab.
And this one cost you the rest.
This is why architects leave the building to professionals.
Gabe
I disagree with SamT about leaving out the insulation under most of the slab. With the heat source in the slab, you'll loose a lot of your heating dollars into the ground if you omit the insulation. If you look at the compressive strength rating of the foam board you'll find that you have quite a factor of safety and you won't crush the insulation.
Two ways on the foam, I've heard, depending on how the heated space will be used:
1...if you are only going to heat the space once and awhile, foam the whole thing so you get quicker response time from the slab.
2...if you are going to want a 24X7 70 degrees in there, leave some foam off the center portion so you can use some of that substrate as a heat sink.
I've also heard that this is BS....that the slab takes so long to heat up when it starts to get cold outside, and acts as such a good heat sink by itself, that the substrate heat sink thing becomes negligible.
I insulated under the whole thing...let you know how it turns out this winter.