I am thinking about doing some small time welding. Like purchasing a oxy/act welding rig as steel related is in big demand. Bars for basement windows, gates, etc. I am interested in opinions of fellow remodelers or builders on ease of use, cost, etc.
Discussion Forum
Discussion Forum
Up Next
Video Shorts
Featured Story
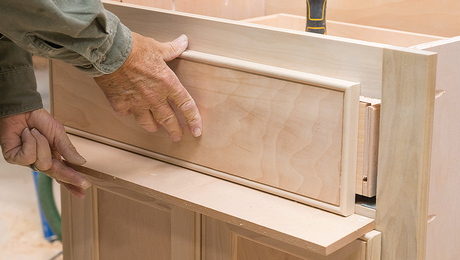
From building boxes and fitting face frames to installing doors and drawers, these techniques could be used for lots of cabinet projects.
Highlights
"I have learned so much thanks to the searchable articles on the FHB website. I can confidently say that I expect to be a life-long subscriber." - M.K.
Fine Homebuilding Magazine
- Home Group
- Antique Trader
- Arts & Crafts Homes
- Bank Note Reporter
- Cabin Life
- Cuisine at Home
- Fine Gardening
- Fine Woodworking
- Green Building Advisor
- Garden Gate
- Horticulture
- Keep Craft Alive
- Log Home Living
- Military Trader/Vehicles
- Numismatic News
- Numismaster
- Old Cars Weekly
- Old House Journal
- Period Homes
- Popular Woodworking
- Script
- ShopNotes
- Sports Collectors Digest
- Threads
- Timber Home Living
- Traditional Building
- Woodsmith
- World Coin News
- Writer's Digest
Replies
Sign up a class at your local junior class. It will be a bargain $200?, they'll have a range of equipment (oxy/acetylene, spot, stick, wire feed of various flavors) and instructors to show you the ropes. They'll also have ideas about how much of a rig you need for yourself.
Someone who is good with oxy/acetylene can weld or cut most anything. But it takes a lot of practice and a lot a gas, especially oxygen if you are cutting. Wire feed is a lot more user friendly for beginners.
You can run afoul of building codes putting bars on egress windows. And properly so. Losing your stereo to the local kids or coke-head is not nearly as bad as dying in fire, unable to escape, IMO.
Thank you very much for the information. I am in the Washington DC area. The chances of finding blue collar courses are not that good. We have a billion how to program in Java classes unfortunately.
David,
Don't know exactly where you are in DC area, but every community college, and most High School systems that I know of in the Washington area have Vo-Tech classes including welding. Most are offered in the evenings as "adult education classes" I am in Charles County and I know they have it, as do Fairfax and Montomery Counties. I know guys that do nothing but take these "classes" in order to do thier own welding projects ! Check Northern Va Community College ( NOVA ) for starters.
The other possibility is to find a fabrication shop and see if they need an apprentice. It takes a lot of practice to gas weld properly and efficiantly. Mig welding is pretty much the norm now days and a lot easier to learn. If you want to read a good book on the subject get "The Welders Handbook" by Richard Finch and Tom MOnroe. It is an HP book and usually available at Borders. If not Amazon.com should have it. It does a nice job of explaining welding, from the bare basics to aircraft TIG welding.
Hope this helps,
Bill Koustenis
Advanced Automotive Machine
Waldorf Md
Edited 12/21/2003 10:22:54 PM ET by MrBill
I think the best way to get started is with wire feed flux core. mig is also very nice, but the gas can get expensive. the only thing you want to use an oxy-acetylene for is cutting and brazing. welding with oxy-acet takes much practice/time.
most of the apprenticeships teach stick welding first, it is simpler to set the welder to stick weld but more difficult to manipulate. then they move to wire feed flux core-this is easy to weld with once you have it set correctly. there are many variables as to correct setting, ie thickness of material, welding position, type of wire, wire speed, and volts/amps, so more complicated, but once your dialed in very fast.
you can get a 110 volt wire feeder and be welding on mild steel in an afternoon, within a couple weeks you can be making decent looking welds that will actually hold if you can watch/take classes from someone experienced. these are relatively inexpensive and great for welding light gauge metal to 1/4 inch stock. you will quickly build skills that will transfer to other types of welding with this practice.
oxy-acetylene equipment can be a most dangerous tool! do not attempt to play with it or learn on your own. get proper training/instruction. it can kill you or worse, make you wish you were dead! just mixing it together under pressure will cause explosion without ignition. very dangerous
Which?
Metal cutting, brazing or actual welding?
Stick, wire or gas?
All the above?
Who ever invented work didn't know how to fish....
All of the Above.
Check with the EAA - Experimental Aircraft Association. They give a good 1 or 2 day course on oxy welding for people who build their own airplanes. It'a a traveling class, so it may be coming to an airport near you. I took it and it was worth the money - about $200.
PaulBen
Loudoun County offers welding classes in the evenings at the Monroe VoTech school which is in or near Leesburg. Ox acetelyne welding is difficult to learn and can be VERY dangerous. I agree with the others that wire-feed is the easist to learn- one or two steps above a hot glue gun. Do a lot of reading but also take a course due to the less obvious dangers involved in welding. MIG, TIG, and stick welding involve exposure to High levels of UV radiation, inert gasses, vaporized compounds, electric shock, High heat and fire. With oxy you're dealing with expolsive gasses. Read some books, take some classes, and enjoy. Metal fabrication is very different than woodworking but can produce the same level of beautiful products. Good luck and have fun.
The pproblem here with tech colege is an average class run $450 with $100 books. Then you have to take 3 or 4 prequis class before you can start welding. so to learn to stick will cost about $1500. Its way cheaper to buy a use cracker box , 50 lbs of 7018 or 6014 and burn some rods. That all the class is going to do, let you burn some rods. You cannot really teach someone to weld, just give them the basic and let them burn, burn, burn some rods. Beside think of all the night travel back and forth to class.
The best employee you can have but you wouldn't want him as a neighbor " He the shifty type"
Your right but I live somewhere near the originator of this thread and I was refering to the adult ed classes thru the local school district. The cost is about $80 + the cost of the text book and the class is 8-12 weeks long one night a week. I think it's a pretty good deal.
"Its way cheaper to buy a use cracker box , 50 lbs of 7018 or 6014 and burn some rods. That all the class is going to do, let you burn some rods. You cannot really teach someone to weld, just give them the basic and let them burn, burn, burn some rods."
BROWNBAGG,
Well said, though I think you are referring to [arc] stick welding (not gas as the original poster was inquiring about). As for MIG, same thing I think, though I would personally stay away from flux core wire. The only thing it has going for it is that it is cheaper, but makes for a dirty weld.
Gas welding I think is something you need someone experienced to learn from however. Too many variables for the novice to figure out on their own.
Jon
Unfortunately, "Cracker Boxes" are not noted for good regulation which can result in some pretty ugly welds. But they are cheap and one can learn the basics of stick welding.
One slight advantage of flux core is that you can use it in windy situations that prevent the gas from enveloping the weld. But, as you note, the using the MIG welder with a shielding gas does allow for a much cleaner weld than using flux core wire.
I think I enjoy gas welding more than MIG welding, but I have lately done more MIG because it seems more practical for what I need. One problem with gas welding is that it normally creates a larger hot spot which can lead to more distortion of the metal being welded.
Check out this site for everything you want to know about welding.
http://www.hobartwelders.com/mboard/index.php?s=
Not limited to Hobart or mig, Post your question there and you will get some good infor. ( not that the info here is not good)
A torch is ok for cutting, but you would be better off investing in a nice MIG set-up. Nicer job, easier, and less dangerous.
I am a DIYer, never will be a pro. My equipment are. Miller 135 mig, ( I really wish was bigger) lincoln ac/dc 225 ( I will never weld ac again) large tank cutting torch, small 5 lb refrigerate torch, 10 lb propane plummer torch. If I can ever find a good deal on a disel lincoln truck mounted rig, I buy it. You haven't welded till you use a big rig, smoooooth.
The best employee you can have but you wouldn't want him as a neighbor " He the shifty type"
I have an old 250 amp Hobart MIG that I got at a bankruptcy sale. It ain't small and it ain't portable. When my local welding retailer had a sale on the new Hobart 135 that ran on 110v and that I could just pick up and run with, I grabbed the last one and headed home. Unfortunately, I didn't read the specs - the thing has an 8% duty cycle at 135 amps. Of course, I wanted to weld 1/4" on my trailer, so I wanted to run it wide open. An 8% duty cycle, however, means that you can weld for 48 seconds out of each 10 minute cycle. So weld for less than a minute and then drink coffee for another 9+ minutes while the machine cools down for another cycle... I happened by a Lincoln 130 the other day and read on the front that it has a 30% duty cycle at 130 amps - so you can weld for 3 minutes out of each 10 minute cycle and only have to guzzle coffee for 7 minutes... Oh well, when I finish my welding shop, hopefully in a couple of months, and get my big machines set up, my little Hobart will only see rare action.
the 135 are small machine, yes, but mainly as a maintance item, I can hook it to the generator and weld out in the woods without dragging a big unit. Like fence posts or on the jeep. I use mine mainly for sheetmetal.
The best employee you can have but you wouldn't want him as a neighbor " He the shifty type"
Look into the Corcoran school ,if you're in DC.They have welding classes- a little more $ than NoVa, but highly rated, with a lower teacher -to-student ratio.
My experience was different. I first tried AC arc welding, and found it to be very difficult, as you have to keep the distance between the rod and the work just right to not break the arc or stick the rod to the work piece.
Then I went to oxy-acetylene, which was a piece of cake by comparison. I learned it at a junior college body shop class. It's also more versatile, as you can cut, braze, and silver solder in addition to welding with gas.
The limitation to gas welding is that it's not good for large work, figure half inch thick is about the max.
Whichever way you go, get the necessary training to do it safely.
-- J.S.
your problem was the AC, DC stick welding is so simple anybody can master in hours.
DC is a constant voltage while AC will switch frequency with 60 cycle so that where the splatter come from creating difficult
The best employee you can have but you wouldn't want him as a neighbor " He the shifty type"