Hi,
I’m just going through the initial stages of finding a plot of land here in N. FL to build a home on. I have been looking at the SIPS system and I think I will go that route. My questions are, can I select a plan from a house plan internet site and have it reworked to use the SIPS system?
Will I need an architect? How would I find a builder that has experiance useing this type of construction technique, Any help and advice truely appreciated.
Mike
Discussion Forum
Discussion Forum
Up Next
Video Shorts
Featured Story
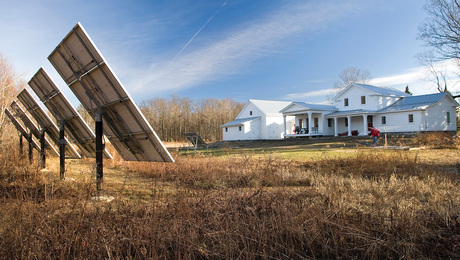
Efficiency, solar power, and a sensitive kitchen for an 1830s house in New York.
Highlights
"I have learned so much thanks to the searchable articles on the FHB website. I can confidently say that I expect to be a life-long subscriber." - M.K.
Fine Homebuilding Magazine
- Home Group
- Antique Trader
- Arts & Crafts Homes
- Bank Note Reporter
- Cabin Life
- Cuisine at Home
- Fine Gardening
- Fine Woodworking
- Green Building Advisor
- Garden Gate
- Horticulture
- Keep Craft Alive
- Log Home Living
- Military Trader/Vehicles
- Numismatic News
- Numismaster
- Old Cars Weekly
- Old House Journal
- Period Homes
- Popular Woodworking
- Script
- ShopNotes
- Sports Collectors Digest
- Threads
- Timber Home Living
- Traditional Building
- Woodsmith
- World Coin News
- Writer's Digest
Replies
Insulspan is a well-known SIP maker, and they and their like competitors are happy to oblige you, in converting a stock plan to SIP construction.
They probably can supply you with a signed and sealed (Florida P.E.) set of for-construction plans, as part of the package they supply.
I am in far upstate NY, and Insulspan sent an erection crew to put up the entire shell, on a house down the road from me, and the guys all came from Michigan.
You will need a GC with experience in SIP construction, or at least a well-qualified GC that is willing to tackle one for the first time. "Willing" is the key word.
You likely won't need an architect, unless the stock plan you pick only meets half of your program, and you need extensive changes. Modest changes such as little non-bearing wall moves can likely be handled by your SIP supplier.
The best place to start, once you have your land secured, is with the local building department, then the SIP manufacturers themselves. They can likely tell you who is in the territory that's capable of GCing the job for you.
The SIP suppliers are usually happy to work up the plans for SIPs and/or comment if changes need to be made. They are usually also happy to recommend builders.
I made my design SIP-friendly from the get go, and ACH Foam recommended a builder well suited to my "I wanna help" mentality.
You can find a link along the left side of my blog to the ACH website.
Good luck.
Adventures in Home Building
An online journal covering the preparation and construction of our new home.
MBaybut
As a long time advocate of SIP's this will shock you, buT I would look carefully at building it with ICF's rather than SIP's (In Florida) I suspect you could actually build it cheaper as an ICF and get the benefits of an ICF for Florida's climate..
Thank you,
The main reason I was considering sips as opposed to ICF is that I want to have the exterior cement board siding. My real goal is to be able to sit on the front porch with family and friends sipping a cool one and not be concerned about maintenance issues in the years to come. What are the advantages of ICF over sips in FL?
Mike
MBaybut,
In florida the lack of wood in a ICF is a real cost savings you can simply smile at termite inspection companies, rather than fork over money every year. You can have the same benefit with an ICF (no exterior maintinace) either by going to stucco or one of the stucco derivatives like Dyvit.
Stucco has a bad name here in the uppermidwest due to the wood underneath rotting because of a poor installation job. However several homes I have inspected built with Stucco over ICF's have been really remarkable with the absolute lack of maintinace..
If you want something othr than stucco you can still install Hardie board over the ICF, it's screwed rather than nailed so there is a increase in labor costs.. You can also put cultured stone or other finishes over the ICF
Interior you can do either with sheetrock or stucco or several other wall treatments.
Since there is a place to attach wood every few inches if you want a solid wood paneled room you simply screw a sheet of plywood to the wall and go ahead and nail your paneling to it.. or you can screw paneling to the ICF and cover the screw heads up with a decorative strip of metal..
The thermal efficency of an ICF is high extremely high, I don't accept their premise of thermal mass gains because it works both ways, however a stable inside tempurature is most definately part of their charcteristic of ICF's That plus quiet!
My SIP home is deathly quiet inside, I no longer hear anything my immediate neighbors do except thru windows, however every ICF home I have visited is several orders of quiet, quieter than my SIP home. (The mass of those concrete walls..)
Finally for the possiblity of severe winds all other things being equal the ICF home is several times stronger than a SIP home. Attach your roof with decent hurricane clips and you won't have to worry about structural damage..
Good answer. I have visited Florida a few times and am amazed at the pesticides used to control termites in wood structures. ICFs would solve that problem.
Here in B.C., Canada we usually use ICFs only for basements, but I have found them quite easy to work with. Window and door openings are easily handled. I toured one project where they were use for upper story. Seemed to work fine. Very quiet and about R22. Great air sealing.
Attaching most any siding would not be a problem, Just screw into the hard plastic ties in the ICFs.
Goldenboy,
I've used ICF's for my basement and choose SIP's for the walls because of the extreme cold weather we get around here and the slight gain of R rating of SIP's over ICF's made the differance..
I priced walls both ways and found that the ICF's were a tiny bit cheaper. However that advantage was offset by the greater time required to install sheetrock. (I've done everything myself so there is no labor costs to compare, however If I were paying for it the sheetrock would cost more to install in ICF's by a bit..)
Since do-it-yourself is my theme I looked at the difficulty of each to build and both SIP's and ICF's were incredibly easy to assemble..
IN fact I wrenched my back* (Bad car seat) and was bedridden, my sister-in-law assembled the remaining blocks with absolutely no prior experiance.. That was easily 3/4 of the blocks.. So if you are looking for difficulty of assembly ICF's aren't it..
Frenchy,
Did you invest in the bracing jacks for your project?
Mike
If I buy an ICF package for my project, the supplier "lends" me all the bracing we need to get the package erected and poured. I think this is common in most places.
Gene,
Thanks. I'm still in the early stages of reviewing this sysytem but it looks very intresting. How big of a crew would you need to assemble these forms. Do you know anything about whats need about site prep? Any info and direction you have would be appreciated.
Mike
One person can do all the work, without help. I cannot advise about site prep, as that is a local situation.
On the day of the pour, you might need a couple helpers.
The web is full of information on ICF systems. Go search and learn.
mbaybut
same here, the supplier provided the bracing and I returned it when finished..
That's part of what you need to check when looking at prices, Not only costs but support and information plus If you are a total do-it-yourselfer like I was, the rest of the package, can they supply pump trucks and give you the recommended concrete mix..
I was a total novice when it came to ICF's I made a few calls and as things turned out the guy who was the most helpfull also had decent prices.. Not the cheapest raw cost, but when the project was done it would have been within a percent of the absolute cheapest everything considered..
When they gave me was a sense that I wouldn't be overwhelmed and that it was something that I could do myself..
It helped that I watched a couple of homes being built/ poured so please don't skip that step. If I listened to contractors who tried to sell me their services they made it sound like some disaster waiting to happen. Horror stories about blowouts and mistakes really can scare a person.. However I talked to several pump operators and they told me they wouldn't pump if the site didn't seem ready.
I'll tell you my experiance is that when they say don't pump it to the top in one section and then move on they are absolutely correct.. Walk the walls and pour in only a little at a time, that does two things.. first it helps to prevent air bubbles and second it prevents the forms from being overloaded.
I was pretty feeble when I went to do my pour, sore back and everything. However I hired a couple of college guys with no experiance to help me, told them what I wanted and had them do the actaul grunt work.. The process was orderly and not hurried I told the pump operator to slow down anytime it seemed like the guys holding the hose were in danger of being rushed..
My oldest daughter used a sawzall without a blade to vibrate the forms as we poured. and withing a little over an hour we were done.. I then went back leveled off the tops of the forms and checked everything. The concrete was already settling by the time we would get back to pump the next 12 inch high layer in so I never felt at risk of a blow out..
Frenchy,
Your experiance sounds encouraging. I was thinking of trying my project out on a small simple 600-700 sqft workshop with a living space above. Then use that space to live in while the main home gets built so i can stay on site. The web truely is great for researching. Thank you for your direction. That goes to all the others to. Thanks.
Mike.
We build with ARXX icfs and I'd recommend the system for a trouble free installation. ARXX braces are easy to use and the documentation for installation is tops. Also, the distributor can either provide a person to help get you started or can recommend someone that would help inspect your progress and solve any problems you run into.
From the discription of your project (small shop with living space above) you'll find ICFs even faster to build with than you'd think. After the first level is poured, the bracing is simply raised up and the blocks just continue stacking where they left off. ARXX has great examples in the technical documents section of their website.
With ICF walls there are many ways to connect the upper floor ledger, but I'd highly recommend the ledger brackets made by Simpson that are simply inserted through the foam and cast in the concrete. The time and hastle saved is significant over j-bolts.
For a slab on grade building we like to pour separate footers and start stacking the block up from there with the floor unattached to the walls or footer. Concrete walls are quite heavy, especially when multiple floors are involved so there is a very real chance that the footers (even properly sized) will settle a bit more than your floor and separating the two will reduce slab cracks.
When I was an employee of an ARXX distributor every form of builder bought our icfs and had every imaginable result. The best results, even better than most experienced contractors, came from detail oriented DIY homeowners who spent the time ensuring all the details are taken care of prior to the concrete placement.
We'd send a good ARXX installer to meet with the clients on the first day and he would work with them and show how the first few courses go together. Then he'd stop by a few times each week to inspect the work, mark trouble spots and go over any questions. Then on the final day it was cheap insurance for clients to have two or three of our experienced guys actually direct the pour and ensure details are taken care of. At the very least I'd sweat it if there wasn't one person there who has actually done it.
If you had to fly with either a student pilot-to-be who has never set foot in a plane, but read and passed all the written tests, or someone who has actually piloted a plane but never gone to school who would you fly with?
Fortunately, an ARXX installer is usually certified as such, or at least I'd trust them more if they were.
You will hear a wide range of contradictory information on the type of concrete to use and all if it is partly right and partly wrong.
Small 3/8" agregate is only a requirement for 4" forms, nice but not neccesary for 6", and probably a waste of time for 8" or 10" forms.
Admixtures allowing the concrete to flow better are nice to have on the smaller forms, but again probably a waste on the larger forms.
I prefer to pour a stiff mix (slump of 5) with large (3/4") agregate and fully consolidate it with a concrete vibrator. Consolidation is the most dangerous part of the pour since underconsolidation will result in walls that are honeycombed and not strong while over consolidation will blow out the form or at least stretch the forms and make sheetrock a bit harder to install.
Those that use a more runny mix and water reducing admix will pour at a concrete slump of 6 to 6-1/2 and have to worry much less about consolidation since the soup will form around most of the internal obstacles with very little outside help.
However, this does greatly increase the odds of form failures unless care is taken to pour a couple feet, let it take a set, pour another couple feet, etc. Consolidation down to the top of the previous pour gards against a cold joint there.
If you do use a system other than ARXX and the recommended installation procedures, don't skimp on the bracing. Bracing is really key to straight walls and locally we hear about other contractors with really bad icf walls.
We've also been hired to clean up other contractor's total failures and it's a real mess. Typically a grossly underbraced wall will tilt inward until it toples over, pulling the adjoining walls in with it, leaving the far side more or less intact. The block is essentially a total waste.
Be careful of using a vibration source other than a concrete vibrator since it's impossible to see if it's working properly and a honeycombed wall is very hard to fix properly.
I was called to inspect an icf wall under a quite heavy log house that was allowing a large amount of water to pass through it. Unfortunately the only option was total replacment since waterproofing over a honeycomb foundation would solve the water problem, but just continue to cover up the real structural problem.
I'd also recommend a Simpson bracket that gets set in concrete for attaching your roof trusses. Ice and water sheild is used as a waterproof membrane separating the wood from the concrete.
The day after pouring your footers it's possible to start stacking the first floor block, which on a small project like yours would only take two experienced installers the better part of a week to stack, build wood bucks for doors and windows, and reinforce with rebar.
We'd pour on thursday or friday and let it harden a week before building the second story floor and resetting the bracing for the second level. Pour the second floor as soon as it's stacked, let it sit a week and install the roof trusses.
While it's possible to pour gable end walls, we only do that if stick building a cathedral ceiling.
You'll love a total ICF house!
Best of luck,
Thanks Don,
I went to their web site which has a ton of useful info. Do they have people in N.FL?
Mike
That's a good question. There is probably a distributor for your area, but they may not be real close.
Beer was created so carpenters wouldn't rule the world.
I would strongly suggest you avoid plans from the internet sites. I think you would be much better off getting something through the SIP company or looking through the plans of local architects that are already built (these stock plans will be very reasonable since the design time has already been done. The internet plans can be a PITA and you might have to do some significant changes. The local people know your area, the styles, features, etc. people want. The cost will be about the same or similar.