Deflection in subfloor from point load
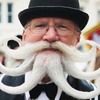
I’ve got a deflection in the subfloor from a poorly placed point load. I drew it out as best as possible and attached a sketch of it if my description is confusing. Basically the point load is roughly centered between two floor joists, so the subfloor has deflected with the weight. I’d like to remove as much of the deflection as possible, but mainly just stabilize it from any further problems. I have fairly decent access from below, but I can’t figure out any way to push it back up since the carrying beam is directly underneath it. Any ideas?
Replies
Bottle jack. I have one small enough that would fit in a 2x10 joist bay. or even your cars scissors jack both with a 2x on top to spread the force of the jack
I have a jack that will fit there, but how do I get it back out and fixed once it is jacked?
Piece of 2x (whatever will fit)and shims or cut some wedges and pound them in to force it up.
Joe H
What is the point load? I'll
What is the point load? I'll assume it cannot be moved.
Would a block of say 6x6 placed on top of the beam provide enough "post" to help?
Perhaps cut a block of 6x6 an inch or so shorter than the present hieght of the available space above the beam. Then pound in a pair of opposing shims / wedges between the top of the block and the bottom of the sub-floor. Probably easier to do if you had a helper to drive the opposing wedge. A pair of inclined planes....a very basic machine with vast power.
6x6 could be softwood but, I would consider making some hardwood wedges for this task. Oak, maple, cherry....
Even if you cannot not raise / remove the current deflection, due to "hammering access" problems, it would certainly stabilize the area. My guess is that you will be able to remove the deflection with relative ease.....don't go too far.
Only slightly more recently than "when men were iron and ships were wood" ..... they used to raise entire ships in drydock by driving wedges under the chines at every rib.
Hundreds of men driving wedges with sledge hammers in cadence to shipyard songs. Up a few thousanths of an inch for each synchronized hammer blow. Cribbing added and the wedge driving / cribbing process repeated until the needed height was obtained. The ship would float off of the cribbing when the drydock was flooded - then they chased their cribbing all over the now flooded drydock to use again for the next ship.
Does a flooded drydock become a wetdock? Dunno.....
Good luck!
Jim
PS: I type more and slower than JoeH
If it were me? I would put a 2x6 on top of my bottle jack perpendicular to the joists (running from one joist to the other) with the jack in the middle. I would jack it up to where I wanted it and then put two cripples underneath the 2x6 on each end sistered to the joists. Then I would turn the knob on the jack to relieve the pressure and take the jack out. If for some reason this wouldn't work, you could just go get a Wally World bottle jack for less than $20 and just leave it in there.
BTW, with a 1.5 inch deflection, I would be somewhat concerned about cauing the opposite problem should I jack up the low spot. In other words, if you start moving the low will the subfloor separate from the joists and cause a hump on the floor rather than a dip?
Might be something you have to jack up an 1/8 at a time over the course of many days.