Hello I have a question for the drywallers . Does anyone have a slick trick for mudding up a butt seam ?? Is there someway to make a tapered edge for the mud and tape to sit in? I always seem to get a slight raised mound that is noticable when color is applied to the wall .
Discussion Forum
Discussion Forum
Up Next
Video Shorts
Featured Story
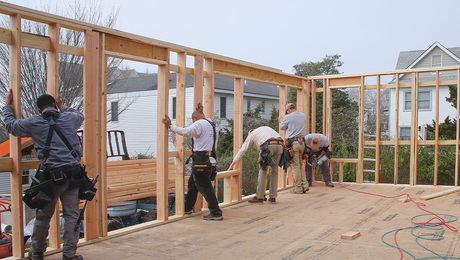
A rear addition provides a small-scale example of how to frame efficiently.
Featured Video
How to Install Cable Rail Around Wood-Post CornersHighlights
"I have learned so much thanks to the searchable articles on the FHB website. I can confidently say that I expect to be a life-long subscriber." - M.K.
Fine Homebuilding Magazine
- Home Group
- Antique Trader
- Arts & Crafts Homes
- Bank Note Reporter
- Cabin Life
- Cuisine at Home
- Fine Gardening
- Fine Woodworking
- Green Building Advisor
- Garden Gate
- Horticulture
- Keep Craft Alive
- Log Home Living
- Military Trader/Vehicles
- Numismatic News
- Numismaster
- Old Cars Weekly
- Old House Journal
- Period Homes
- Popular Woodworking
- Script
- ShopNotes
- Sports Collectors Digest
- Threads
- Timber Home Living
- Traditional Building
- Woodsmith
- World Coin News
- Writer's Digest
Replies
Google "butthanger." Go to the various sites, and see what it is about.
The trick is to land your endseam between studs or joists or trusses, and use one of these thingies to fasten to, which will pull the joint down into a mini-valley. Mud-up flush, and voila! No bumped endseams.
thanks for the info men (entertaining at the least) !! question: if you were to hang the drywall vertical and have a butt seam between the studs , (using a home made butt hanger) , would it make the joint weak ?? would it flex at all and crack if the brats were to run around and push on it ??
Hanging drywall vertically eliminates the need for any kind of "butthanger" device, as the beveled factory edge provides the "trough" for the tape and mud, and the seam is thus finished flush.
I don't know enough about hanging and taping to understand why there is an objection to hanging boards vertically on walls. For rooms with 8-foot wall heights it seems to me that the footage of taped joint is about equal, either way. Maybe it is the "bending over" factor, in that there is half of the footage to do at heights 48 inches to zero.
If you wish to go vertical, by all means do so, and place them joints right on the studs.
Edited 5/4/2005 9:51 pm ET by Gene Davis
Yes, that's why I always avoid this and simply use a full sheet, rather than 2 half sheets. Now, having said that....its the end of the day, you've got no more full sheets, only two partial sheets (full width) and you've got one more 4' stud bay to fill...and you need to have this done before you leave. Under this condition, you'd use the two half sheets with a butt joint. I'd back those butt joints (with 1X4 pine) for two reasons:
1. As you mention, later on if the finished wall is leaned into, the butt joint between the studs, if unbacked, with crack, and
2. To taper butt joints so that at finish, they will not be seen requires that the two butting sheets be at exactly the same height (be screwed to the same base).
As I say, the added work of doing this is most easily avoided by simply using a full sheet, so except for closets and other hidden spaces, this approach should only rarely be used.
BruceM
And most importantly, AVOID as many as you can. I examine with great care how to avoid them..even if it means an extra sheet or two..it is worth it.
Spheramid Enterprises Architectural Woodworks
Why look here?
Butts are a problem, I'd look at Genes suggestion, there are other products as well as do it yourself methods.
Nobody uses a curved trowel anymore. Not that is solves the problem but it gets the tape covered and creates a place to feather out to with a slick 16" straight finishing trowel.
I hate all those silly 12" putty knife thingees.
Eric
I Love A Hand That Meets My Own,
With A Hold That Causes Some Sensation.
[email protected]
Nobody uses a curved trowel anymore. Not that is solves the problem but it gets the tape covered and creates a place to feather out to with a slick 16" straight finishing trowel.
I use a curved trowel. I've seen Butthangars discussed here and other sites quite a lot over the past few years but I 've never actually seen one on the job. Maybe its a regional thing? The rockers here land the butts on the studs. I've never even considered that butt seams are a problem. Bad taping is the problem? Just my opinion.
Tom
How do the trim carps like to run base, crown, or chairrail over your butts? Ever ask 'em?
Well, since the Trim Carpenter on most of my projects is myself I can tell you that all complaints fall on deaf ears. I take your point though. Chair rail and crown are a bit of a rarity here. I love to install crown though and wish I could sell more of those jobs.
Gene,
I take exception to your view.........
And, I'm surprised to see anyone respond that uses a curved trowel. Those straight bladed things of various widths with the putty knife handles are just about useless for real taping, but(t) that's just my opinion.
Done correctly, unless a butt falls on a high stud, taping one fairly flat is no worse than an outside corner, using a cornerbead.
The big key is to have a minimum of compound under the tape while still having enough to assure proper adhesion.
I do the next coat with a 14" curved trowel prefferably using D Bond or similiar setting type material.
Third coat will be with a 16" flat trowel and it will feather out the butt that far from center on either side, so we all ready have a 32" wide spread.
Depending on how I feel I may go further than that with another coat.
As long as you don't bunch up the tape or the compound on the initial set or hit a high stud, the end result should be fairly flat. No worse than a high or low ceiling beam in the middle of a 12' board.
Corner beads are not much different by nature, they have that little bead on the corner that makes it just a little proud of the DW surface, you fill it, and then feather it.
I've never seen the devices other than in pictures. I'd probably use them if I tried them, like them, and they were easy to install. There has been much progress in taping methodology recently.
I'm not an expert by any means, and most of the work I did was "old school" taught.
Eric
I Love A Hand That Meets My Own,
With A Hold That Causes Some Sensation.
[email protected]
Edited 5/1/2005 7:28 pm ET by Eric Paulson
If your blades, or as you call them "putty knives", don't have a crown or curve..you're buying the wrong ones. Sight along the blade before you buy them.It depends on what you're used to I guess. I can feather a much better edge with a 12 or 16" blade then with a trowel
Barry E-Remodeler
Perhaps we are talking of different instruments. All the ones I have seen are flat, straight.
Some one posted a thread last week about a sale at Sears on a handful of them.
Tome, they are vitually useless, the blades are too short to clean off on a hawk anyway.
But who uses a hawk anymore, or knows what one is?
Hey, to each his own, whatever works for you.
EricI Love A Hand That Meets My Own,
With A Hold That Causes Some Sensation.
[email protected]
We're talking about the same thing. I saw the thread with the sale link and wondered who would buy one online. I usually have to go through half the rack to find one that doesn't have a bent corner or double crown. But a good blade does have a crown.
I have a hawk somewhere in my shop. haven't used it for 15 or 20 yrs. I prefer the pans for mud and the hawk for plaster. In the long run all that counts is the final results.
The only thing in this thread I'm totally against are the corner trowels. <!---->
Barry E-Remodeler
See the attached pic for the purist's own home-made butthanger.
The board is a piece of 7/16" OSB, 10" x 47-1/2". The edge shims are shown held back from the ends, but should be the same 47-1/2" length. Make them from anything, and just hot-glue them on. They are 1/8" thick by 3/4" wide.
Hang the end of your 48" board halfway into a bay, not on the bearing. Slip your homemade butthanger under the back, and fasten. Get out your spray water bottle and spray the edge of the sheet you just attached to the BH. Slam your next piece of rock on, and spray its edge after fastening to the BH. The water will soften things up and make the rock edges V right into a nice little shallow valley within 30 minutes or so.
Years ago I tried a device similar to what you show. For me it was a disaster. Either the fasteners pulled through the paper, or the water softened the drywall too much and the edge of the sheet fell apart.
Fortunately the experiment was in a little noticed space. Since then I rely on my taper (If you are looking for one, I will give you his name.) to make these joints as invisible as possible. As for running the trim over these joints, if the finish carps didn't have something to complain about, we just wouldn't feel properly valued.
I have used Gene Davis' (Post 15) homemade butt hanger since I saw it some 10-12 years ago in FHB "Methods of Work".This is a very slick system, and results in a slight taper that is easy to tape/mud -- leaving an absolutely straight run (without the belly you normally get with a butt seam). Mine are just a little different than Gene's:1) For ceilings, I use 5/8" BCX cut into strips that are 9" X 47 1/2". I have used ply instead of OSB on the assumption it will hold screws better. 2) I use plain old poster board (available from any art supply house), which I rip to 1 1/2" strips on my TS, and staple to each long edge of the ply. This stuff is about 1/8" thick, and I have found anything thicker produces more of a taper than you want to deal with. 3) I have never wet the edge as Gene does.4) I screw one side of this board to the rock prior to hanging (with the poster board against the back of the rock).*****************Just recently I rocked a huge ceiling with a veteran rocker who was very skeptical of this technique. but after the ceiling was mudded, he agreed it was about the slickest system he had ever seen.
"I would never die for my beliefs because I might be wrong."
-- Bertrand Russell
That is , without a doubt, the dumbest thing I have ever seen!!!
Feather It !! There is no substitute excellence!!
From Myron Ferguson, over at the JLC site:
"A typical butt seam is a bump. All you can try to do is feather it out, but at certain times of the day under the right lighting you can still see the bump. Backblocking creats a recess that is filled just like a tapered edge seam. I did a clinic at a builders show in Febuary. I finish taped a butt seam 32" wide and everyone thought it was perfect. Looking at the seam and running your hand over it did seam perfect. Put a 4' level on the seam and it is a whole different story. Also butted seams are the first seams to ridge."
My NE Indiana drywall guy used site-made blackblocking when hanging the rock in a home we built in '96. His idea, not mine. The wall along the left in the attached pic has a plate height of 18 feet, with four row courses of 54" board. The morning sun shines right down that wall, not at it, but down it. Butted seams would have shown humps, but with the backblocked seams, the wall looks good and flat.
Well said.
I'm with you - feather it out
Welcome to the Taunton University of Knowledge FHB Campus at Breaktime. where ... Excellence is its own reward!
Thinkin' out loud here....
How about adding a nailer to the stud 3/16" back from the stud face. Hang one sheet edge on the stud. Hang the next sheet edge on the nailer.
Woila!
Oops. Forgot about the tape.
Never mind.you probably look like your DadI look like heck
The method that was used out west was to buy SR shims. They ae sold in bundles - cardborad about 1-1/2" wide and 48" long, to staple to the stud on either side of the joint. Also used to shim low spots here and there in bent studs. But I have not found them tio be available in the east.
Welcome to the Taunton University of Knowledge FHB Campus at Breaktime. where ... Excellence is its own reward!
Yeah. Seen 'em. Nowadays the studs are so crooked, how would you pick the ones to make the joint on?
I try not to make a butt joint on a high stud, and then I feather the joint. Not that big a deal.you probably look like your DadI look like heck
Nowadays...Yeah, that's true, that was then, this is now - you always have studs to choose from... but the same guy hanging ain't always the same guy taping
Welcome to the Taunton University of Knowledge FHB Campus at Breaktime. where ... Excellence is its own reward!
They are headin' East (DW shims I mean). When I moved from Colorado to Minnesota five years ago, none of the suppliers in my part of the Midwest knew what I was talking about when I asked for them. I had to special order them. People on most jobs had never seen them before. Now they are becoming common. I like to shim studs out on either side of my butt joints, as you mentioned.I also use DW shims to straighten kitchen and bathroom walls so the cabinets and countertops need much less shimming and scribing. Pay now or pay later.
Do you shim the entire length of the stud, floor to ceiling?
I Love A Hand That Meets My Own,
With A Hold That Causes Some Sensation.
[email protected]
I would not think so, unless stacking one butt on top of another, which would not be a good idea.
I think I took the tread off course.I do stagger butt joints, so then the shimming of studs either side of the butt joints is staggered too.My tangent was referring to straighting walls with the DW shims, on walls with or without butt joints--so all of the finish work--walls washed with light by a sconce or a tile backsplash, counter, cabinets, everything installs easier &looks better.Your butthanger would actually result in a slightly straighter wall than my shimming of butt joints. I just always have the DW shims on hand and it works pretty well to use them or mark the "low studs" with a Sharpie and put the butt joint there.
"Do you shim the entire length of the stud, floor to ceiling?"Sometimes. Of course the studs are usually farthest out-of-line about halfway between the plates. I put a long straight edge or 6' level against the studs near the floor, at counter ht., and near the top of wall. The shims are about 1/16" thick and about 36" long. I just slip as many shims as will fit behind the straight edge (to fill a "low spot"), and hammer tack them on. The shims easily fold to make a "tapered shim" (single thickness to double) or fold and tear to any length. If I have to stack them more than 3 deep the framing lumber is pretty lousy and I switch to my narrow crown pneumatic stapler for the longer staples(my hammer tacker only goes to 1/2"). It only takes about 10 minutes to shim most walls and then they are amazingly straight. Drywall, cabinets and counter tops all go in easier and faster.
I've seen the shims at Menards in Michigan, so their this far east.
Mike
"I've never even considered that butt seams are a problem."
I'm with you - never knew butt seams were a problem. I've yet to see anything other than joints on a stud, with a feathered seam. A friend of mine who is a drywall contractor did some volunteer work in Ireland - he said all the sheets were hung vertical, so no butt joints. He tried to tell them thats not how its done, but they weren't having any of it.
I'm a finish carpenter, not a taper, but I use a curved trowel when I have to spackle.
I have a 12" and 14" .
I also use a corner trowel for inside corners, putting me even more in the minority.
I also use a corner trowel for inside corners, putting me even more in the minority.
Now that's something I never tried.
Does it actually work well?
I use a six, set, coat one side, let dry, then the next, then fill and feather.
And please, spackling is something homeowners do, WE do TAPING!
EricI Love A Hand That Meets My Own,
With A Hold That Causes Some Sensation.
[email protected]
OK, when I "tape", I bed and set the paper tape in the corner, and when that dries, I use the corner trowel and finish both sides in one pass. The only drawback someone might find is that it leaves a very small cove in the corner; its not a perfectly sharp corner. I happen to like it, tho.
I have a rubber coved-corner "knife". Like a big rubber kitchen spatula that I sometimes use in inside corners. Creates from a 1/2" to 2" radius cove--depending on the amout of mud and how much pressure you apply. Looks great and matches bullnosed outside corners. Creates problems for some corner cabinets (most cabinets don't really go all the way into the corner--they "cut the corner" to avoid corner irregularities). The cove also makes running baseboards more fun (similar to bullnose o/s corner issues).
Sanding also takes some getting used to, curve a sanding sponge over onto itself to match the radius and wha lah. Sounds like a lot of trouble I know, but it can be a very cool custom look.It works fantastic for wall to rafter transitions in dormers or 1-1/2 story homes.
Bass,
My inquiry about shimming the entire length of the stud WAS in reference to drywall.
I'm thinking; if he only shims the stud 48", when the next sheet below is applied it will not flush with the sheet above on the studs that are shimmed.
? Right?
EricI Love A Hand That Meets My Own,
With A Hold That Causes Some Sensation.
[email protected]
Ok, I understand what you are asking.I think that is why the shims are only 36" long not 48" so you can shim out the middle of a butt joint to make a valley and still draw the tapered edges together on the long axis.I know it sounds like a compromise, but it works pretty well.When I worked out west, there were about a dozen drywall hanging crews that worked for the builder I worked for. Most used DW shims if walls were really crooked to straighten things out. Only one crew shimmed the studs or joists on either side of the butt joints. That was the crew the tapers liked to follow.I do my own taping on small projects or when the schedule demands it and have two DW finishers I hire. One really appreciates the shimed butt joints and the other doesn't really care. I do it because l think it helps produce a better final result (than doing nothing, though not as perfect as the "butthanger method").You may prefer the butthanger (I haven't tried it yet--my van is already full).
Edited 5/2/2005 9:15 pm ET by basswood
Hah!!!....just used my curved trowel tday....
Getting ready to paint MIL's porch ceiling, tape & nails showing in the original 20yr old mud job....hammered the nails back in, started spot filling, said nuts & went to work with the curved trowel.....use it once you'll never mess with a 12" knife again...
the butt taper,
http://butttaper.com/home.htm
butt hangers have been mentioned, or make your own. many methods
One way to avoid bad butt joints is to make sure you never break on a stud that is bowed out into the room. You can usually find a stud that is back a little from the plane of the wall to break on. This will create a recessed butt joint. If you break on a stud that is bowed out you may never be able to hide the joint.
hang your board vertical....
Gag me
Welcome to the Taunton University of Knowledge FHB Campus at Breaktime. where ... Excellence is its own reward!
Is there someway to make a tapered edge for the mud and tape to sit in?
Someone mentioned the ButtTaper..it does just that. Total working time of 1 minute and 18 seconds from the finishing beginning to the sanding resulting in flat butt joint that is maybe 5 inches wide. Little mud is used..on a mud pan one inch from the end to the top of the mud pan. Only method tested by the NAHB.
A few observations from this thread:
- Anyone who accepts the curvature of the butt joint is not a craftsman!
- Using the buttboards, you don't wet the butt joint.
- Using a double sided knife that leaves a small cove in the angle will result in the cracking of that angle.
- Butt joints are not a problem in the "Fred Flintstone House" as the texture pretty well hides it. Unless of course in time when it's on a stud it ridges or cracks.
Okay, the answers have run the gamut and as usual I'm along late. But here's my 15 cents worth.
1. Hang vertical. If the rock makers wanted ya to hang horizontal, they'd-a tapered the other two edges. Duh. (that oughta get this old argument goin' again, :-) LOL).
2. When you get stuck with a butt anyway, land it on a stud. Obviously, if you want a good job, you've stringlined the studs first and have faired them flat with a combination of planing and shims. I can't get gyprock shims; I gotta use cheerios boxes. PITA, but there ya go....
3. Run a bead of mud down the seam with a 5" knife. Pull your tape and screed it in with the same knife. Now change to a 14" trowel and feather it out on both sides best you can. Use enough mud to fill the whole 14" each side. That's first coat.
4. Second coat, first knock off the tits and flyspecks, then get out the 16" trowel and feather each side again. Now you're past the next stud on both sides, and you shouldn't be more than 3/32 thick at the very middle. Second feathering oughta be as smooth as you can make it.
5. Third coat, sand lightly first, then use a 5" or 8" knife to fill in any pinholes. Do a final feathering on each side with the knife; you shouldn't need the trowel for this.
6. Sand, prime, and paint. You won't see the joint. 3/32 over 36-odd inches comes out to a ratio of 1:0.00026 or something close to it.
And, yeah, I have some curved trowels. And I have some straight trowels. The straight ones are for concrete work. I use a 5" and an 8" knife, and a 12", 14", and 16" trowel. And a hawk. Can't imagine working without the hawk. And the inside-corner knife works well, especially if you use a metal-beaded paper tape with it, which is what I do.
I hate gyprock work.
Hang vertical, dang it! (Hee, hee, hee)
Dinosaur
'Y-a-tu de la justice dans ce maudit monde?
To get back to basics, drywall consists of some chalk between two pieces of paper. A piece of sheetrock 1/2" thick would have two pieces of paper each 0.030" thick with a slab of gypsum 0.440" thick in between them. The idea is to create a perfectly flat surface. You cover the butt joint with a strip of paper 0.020" thick and then cover that with layers of joint compound. You cannot avoid having a bulge.*
What you want to do is create a splice between your two butted sheets. You make two shallow cuts 1" on either side of the seam and remove the paper [two 1" strips]. Fill the gap in the gypsum with joint compound. You now have a "canal" 0.030" deep and you fill this with a strip of 2" wide paper which you glue in place. The paper can be either 0.020" or 0.030" thick. It doesn't matter but you fill in the narrow seams with a coat of compund and you have a totally flat surface with no bulges.
~Peter
*0.030" + -/440" + 0.030 + 0.020" = 0.502" = bulge
I won't say you couldn't do it your way, but I will say it sounds like more work than it's worth. The 'bulge' you refer to in the standard method of going wide is there, yes--but the slope of that bulge is so low that it becomes virtually invisible to the eye...and to the hand (with your eyes closed), which is what I use as my final gauge. It's not going to bother the woodwork, either.
You have to remember that homeowners don't routinely walk around their living quarters holding a 7-foot long, DFS milled-steel straight-edge up to their walls to see if light squeaks behind it anywhere....
Still, the best way is to hang vertical and don't be shy to use an extra sheet now and then to avoid butts in the first place.
Dinosaur
'Y-a-tu de la justice dans ce maudit monde?
"*0.030" + -/440" + 0.030 + 0.020" = 0.502" = bulge"
Wow, a half-inch bulge from taping a butt joint! No wonder you're concerned about it showing up!
It is a bulge of 0.020" from the nominal thickness of 0.500" [1/2"] DW or sheetrock or gypsum board. [I am guessing on the thickness of the paper on the surface of the DW].
There are other refinements possible. For instance, electrical boxes with mud rings [metal] are attached with round head screws. Divots in the backside of the drywall should be created for them. In fact, in steel stud work, all of the wafer head screws should have divots created. The suggestions for planing/shimming wood studs are valid.
I agree with post 57704.44 that the manufactures of this stuff should put beveled edges on all sides. It is amazing that no one has figured this out yet.
~Peter
I've thought that rock makers should put out a sheet that tapers on all sides- an 8'er would be all that's needed for just about anywhere.
Problem is, then we wouldn't be able to have all these discussions on the proper way to deal with the butt joints. :)
Yeah, now that I think about it, it's a mystery to me why they don't do it.
Of course, a long time ago, a wise man told me: "The answer to any question that starts with 'Why don't they...?' is always "$$$$$$."
Dinosaur
'Y-a-tu de la justice dans ce maudit monde?
It is because they make the stuff 4' wide and about a mile long at the plant and then cut all those butt joints out of that really long piece.
Yeah, I actually knew that. But that just proves that the wise old man was right.
Figure: How much more would it cost to manufacture if they had to mold the stuff one sheet at a time instead of just whacking off pieces from the end of an endless extrusion?
"$$$$$$$$$$"
Dinosaur
'Y-a-tu de la justice dans ce maudit monde?
I still think they could make a sheet with 4 tapers pretty easily, even with running miles of it, if they wanted to.
They'd just have to make the taper across the sheet before it fully hardens, and then allow enough paper to wrap around the end when its cut.
I'm sure there's more involved, but I bet it wouldn't be all that difficult to incorporate into existing plants.
Where did you get your 16" trowel? Brand? I have an 11" featherlite curved Marshalltown that is a joy to use.
I'd love to get a Richard 16" or 18" knife, if there is such a beast. Richard's wide knives are so springy and responsive, I can work miracles on a good day.
edit: well, that might be a slight exageration!
Edited 5/4/2005 12:55 am ET by Pierre1
I think all my gyprock knives and trowels are Richard. The flat Marshalltowns are for concrete work, although I've got quite a few small mason's trowels and striking tools by Richard, also.
I thought of getting an 18" gyprock trowel being a good tool whore, but resisted the urge as money was a bit tight....
Just to make sure we're using the same terminology: What I call a 'knife' is the gizmo that looks like an oversized pancake turner. A trowel is the rectangular thingy with the handle on the face.
Pis, en français, ils sont tous des taloches!
Dinosaur
'Y-a-tu de la justice dans ce maudit monde?
Love it! Dino-dictionary
knife ('nIf) noun, plural knives /'nIvz/ Usage: often attributive
Etymology: Middle English knif, from Old English cnIf, perhaps from Old Norse knIfr; akin to Middle Low German knIf knife: the gizmo that looks like an oversized pancake turner.
trow·el ('trau(-&)l) noun, Etymology: Middle English truel, from Middle French truelle, from Late Latin truella, from Latin trulla ladle: the rectangular thingy with the handle on the face.
Bang on with the definitions.
In contemporary French, a pocket knife is a 'canif'. Pretty close to the ME's 'knif' isn't it?
We still call the trowel a 'truelle', unless you're smoothing concrete in Dino's neighbourhood where they call it a 'taloche', which is joual French.
Joual is old-fashioned Québéçois french drawn from the 1700s-1800s-1900s, and adapted to modern circumstances, sometimes blended with old English expressions. Very colourful and full of sound-plays.
From the get-go I've been amazed at Dino's joual. His joual is 100x better than mine. At first, I thought he was a fellow Québéçois, and you know where he's from! That's the Canadian melting pot at work for you.
Edited 5/4/2005 2:13 am ET by Pierre1
Edited 5/4/2005 2:39 am ET by Pierre1
'Melting Pot??!' Wo, bro, yer on da wrong side of the border. Its the 'murricans who're spozed to melt everyone together to make a single culture.
Canada is officially 'multi-cultural'. Way too cold to melt anything....
BTW, you probably know this but just in case and fer the general edification--the word joual comes from the way the word for 'horse' (cheval) is pronounced by people who speak it. And for those who can't hear the sound by looking at a word with three vowels in a row, here's a phonetic version of joual: joo-wahl. Okay, now that's still hard unless you know how the j is pronounced. Lemme see...the j in French is pronounced like a combination of a soft g with a blending of a z and an sh sound. Sort of like the last sound in the word Taj (as in 'Taj Mahal')....
Dinosaur
'Y-a-tu de la justice dans ce maudit monde?
And BTW, Mon-sieur, last time I looked I was a 'fellow Québecois'. The fact there's a bit of polyester mixed in with the pure wool doesn't take that away ;-) <G>Dinosaur
'Y-a-tu de la justice dans ce maudit monde?
ouin, j'use la même terminologie su la job.
Those Richards are great value for the $. Their stainless is best imho. I'm gonna get their 18" couteau (knife), I think it will pay for itself on the first job.
Just finished a bunch of butt joints...ceiling and walls. I run vertical to minimize them...but always seem to get a few anyway.
First rule I follow is to never butt over a 1 1/2" stud edge...tooooo narrow. I run my butt between studs, using a piece of 3/4" pine behind the joint usually 2.5 to 3" wide, so each butt overlaps it by at least 1"....1 1/2" overlap is better.
Set the drywall screws back 3/4" to 1" from the joint.
Then with a very sharp utility knife, draw down about 3/4" back from the butt edge on each side, cutting a 45 degree bevel. Make sure the top layer of the paper is beveled. A dull knife will tend to pull the paper back...and this won't work.
Then with this 1 to 1 1/2" bevel, cut a narrow piece of paper tape or nylon mesh to fit into this V-groove. Mud in place and finish as normal.
And I cannot fathom putting tape over the top of a joint, muding over that and tapering that out. Although I'm sure this is a fast method, it'll definitely stand out in a smooth wall. Tacky.
This weekend I finished my primer coat over a dozen of these kinds of butt joints...and under any lite, you cannot see them.
BruceM