Here in upstste NY, I’ve always installed my 1/2″ plywood exterior sheathing horizontally. There seems to be some question if this is the proper orientation. Any input? Also I’m thinking about using pt ply for the first 2′ of wall sheathing. It seems to me this is a good idea when the mud sill is only 8″ from grade. Also, since the sheating overlaps the foundation wall about 1″ it seems like this would be good practice to prevent any foundation wall moisture from wicking and rotting the sheathing where it is in contact with the concrete. Has anyone done this? Also OSB vs, exterior plywood? Any opinions? Thanks.
Discussion Forum
Discussion Forum
Up Next
Video Shorts
Featured Story
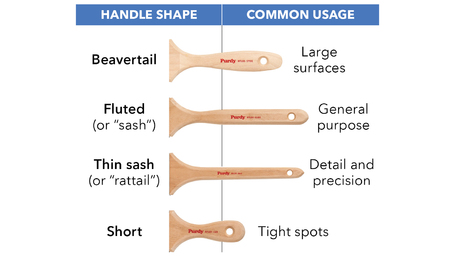
Tips for picking the right paintbrush based on paint type, surface, and personal comfort.
Featured Video
Video: Build a Fireplace, Brick by BrickHighlights
"I have learned so much thanks to the searchable articles on the FHB website. I can confidently say that I expect to be a life-long subscriber." - M.K.
Fine Homebuilding Magazine
- Home Group
- Antique Trader
- Arts & Crafts Homes
- Bank Note Reporter
- Cabin Life
- Cuisine at Home
- Fine Gardening
- Fine Woodworking
- Green Building Advisor
- Garden Gate
- Horticulture
- Keep Craft Alive
- Log Home Living
- Military Trader/Vehicles
- Numismatic News
- Numismaster
- Old Cars Weekly
- Old House Journal
- Period Homes
- Popular Woodworking
- Script
- ShopNotes
- Sports Collectors Digest
- Threads
- Timber Home Living
- Traditional Building
- Woodsmith
- World Coin News
- Writer's Digest
Replies
I'm pretty much in accord with you, but a lot, maybe even a majority of builders run the plywood vertically. According to the APA, either is OK, but since the strength axis of plywood is along its length, I prefer to install it horizontally since I live and work in a high wind zone and a seismic 4 zone. Intuitively, horizontal makes more since to me.
That being said, shear walls and portal walls often spell out blocking at all sheathing seams, so from a productivity standpoint, installing vertically can save a few bucks without really compromising the structure.
And I also support your use of PT plywood in the first course above grade. I've done that on the last few homes I've built, including my own. Even with good drainage, folks tend to landscape next to the house and, in my coastal climate, things grow fast and posies growing next to the house are a conduit for moisture, bugs, and limited ventilation. To me, a few extra bucks spent in that vulnerable area is worthwhile.
As far as sheathing material, I abandoned the use of OSB several years ago. Since I live in a region where Doug fir plywood is still manufactured and having worked in a plywood mill in the past, I'm a little fussy about quality and specify product from the plants that provide a consistent product (even CDX doesn't have to be total crap!).
And all structural plywood is layed up with exterior glue.
> I'm a little fussy about quality and specify product from the plants that provide a consistent product
How can I get the best Struct #1 half inch for sheathing? My house is in Los Angeles, and I'll need about 140 sheets of 4x8.
Thanks --
-- J.S.
John;
140 sheets is close to 3 units, which gives you a little leverage with suppliers. (and, usually, a price break).
I usually specify (insist on) manufacturers such as Roseburg Forest Products or Willamette Industries (now Weyerhaeuser). Both companies tend to be a little more attentive to quality control than some others.
Since plywood and framing lumber are commodities, most yards source their inventory from wholesalers who, in turn, get their inventory from wherever they can. Any given yard's inventory at any given time might have a broad array of stencils in the yard.
But the consumer, by planning ahead, can get a local yard (especially if you've got a contractor's sales guy that you have a history with) to specify what you want and from who you want it. You just may have to be a little patient.
In addition to doing most of my business with a well-managed local yard, I also have an account with Allied Building Products and the rep there has been very aggressive about getting me what I want.
Personally I wish more people would do this because I've seen some really shoddily made plywood (debris pressed into the faces, blows, delaminations, glue skips, excessive voids, broken edges, cut out of square, etc.) and yet, the price of that junk is the same as the product made by a responsible mill within APA specs.
I do the same thing with lumber. That's a little easier up here because there are still quite a few sawmills around. Aside from just QC, I try to source from those sawmills that are generally cutting logs from slower growing stands (tighter growth rings) rather than those cutting 20-30 year-old thinnings with 1/4" rings. And, with a couple of old-growth mills around, framing lumber from those mills is usually heartwood, is stable and seldom has much wane.
Some recommendations: Seneca Sawmill, Eugene, Or.; cuts small timber, but mostly from higher altitude stands in the coastal mtns or lower Cascades.
Rough-and-Ready Sawmill, Cave Junction, Or.; family owned, mostly old-growth or older 2nd and 3rd growth from the Siskiyou and Rogue River areas.
Roseboro Lumber, Springfield, Or.; mills small timber like Seneca and some old growth; also supplier of laminated beams.
Thanks, that's very helpful.
-- J.S.
If this is an "under-course" ( not the final exterior finish layer) this is a great idea. alternating directions of materials in sucsessive courses adds strength to the srtucture by the 3rd power on each layer, however what you must pay gravest attention to in such a case is drainage and ventilation and "papering" or felting, between layers... another man,say maybe Sphere on this site could fill you in on the spec's for your geogr. area...
Scribe once, cut once!
I think the reason people apply it vertically is that all four edges land on the framing. If you install it horizontally, you have that free edge floating between studs, and some jurisdisdictions require blocking if you do that.
I agree with most of what was said above including the need for all edges of structural sheathing to be supported (blocking) in areas where structural panels are required (corners, etc). Really though, most people, at least in my state, install their sheets vertically. If you do decide to use OSB and you want to install it horizontally, you need OSB specifically designed for this application.
I do have one question: you said "sheating overlaps the foundation wall about 1" - Is this standard practice where you or other's live? We set the mud sills in 1/2" from the outside of the masonry (assuming ~1/2" sheathing) and that way the sheathing surface comes out pretty close to flush with the masonry. Then the siding hangs down 1" - or whatever. BTW - using this method, it is important that the sheathing does not touch the masonry because as you say, it will wick up the moisture form the foundation.
I follow your thinking to some degree, but personally, I'd probably just wrap the floor system with the PT plywood, and then stand sheathing vertically for the walls. That way there would be no blocking to interfere with the wall insulation. Also, having horizontal seams makes for more air leaks.
BTW - is the house to have 8', 9' or what height ceilings?
I'm no expert but I do know that some codes for hurricane resistance, not sure if it was adopted or stayed proposed, insisted on plywood, the one I saw said 5/8", laid horizontally across the studs and all the joints blocked. They also speced #10 at 4,6 and 12"
From a theoretical stand horizontally would seem substantially stronger. With blocking preventing buckling and horizontal shear when racking.
Of course the question is: How strong does it have to be? Stronger is better but at what cost and, given a set price for a home, is the wall the best place to sink extra money to benefit the design the most? You could sheath in sheet titanium and have a stronger wall but is it wise or necessary.
Even in a hurricane it is failure of the openings, roof systems and fastening between major planes that causes loss of houses. Seldom do walls buckle under wind forces. Earthquake forces are another thing but here again, for moderately sized single family homes, connections seem more problematic than rack strength.
I have been told that, I also did some rough calculations that seems to support the point, standard walls of 2by4s at 16"OC sheathed with real plywood and nailed well are overbuilt for just holding up the roof, second floor loads and with a relatively generous allowance for violent natural forces.
Not to counter my own point but I, assuming I design and build my own home, intend to use 5/8" ply and install it horizontally with blocking at the joints. You never know when a hurricane will sneak up on you in sunny Florida. It will take a little longer and cost a bit more but it seems, IMHO, to provide a fair return for the extra investment.
When I helped a friend build his addition, he had 2x8 studs @ 16" o.c. for the less than 2' between a concrete block wall and the floor joists for the second floor. We put the plywood on horizontally on this section only and the building inspector made us rip it off and put it on vertically!
Here in earthquake country, they want 1/2" Struct #1 for shearwalls. Nailing is 8d, 6" on the edges, 12" in the field. They don't say whether horizontal or vertical is preferred. That's per the Los Angeles "Type V" sheet.
-- J.S.
ply is a better nail base for siding than osb see some guys upgrade to 5/8" on roof check w inspector about the run, most want it horizontal w staggered seams to next course check w him about pt, may not allow it