My finish carpenter needs help estimating jobs more accurately. Does anyone have a spreadsheet (excel?) they would share that I could give to him to help him out. thanks, jim
Discussion Forum
Discussion Forum
Up Next
Video Shorts
Featured Story
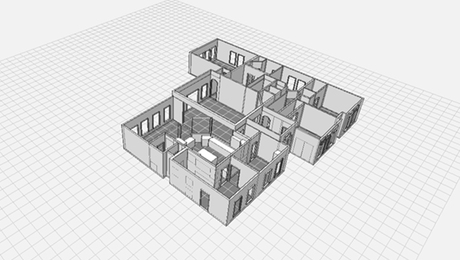
Hover's smartphone app offers an easier way to get precise 3D scans.
Featured Video
Video: Build a Fireplace, Brick by BrickHighlights
"I have learned so much thanks to the searchable articles on the FHB website. I can confidently say that I expect to be a life-long subscriber." - M.K.
Fine Homebuilding Magazine
- Home Group
- Antique Trader
- Arts & Crafts Homes
- Bank Note Reporter
- Cabin Life
- Cuisine at Home
- Fine Gardening
- Fine Woodworking
- Green Building Advisor
- Garden Gate
- Horticulture
- Keep Craft Alive
- Log Home Living
- Military Trader/Vehicles
- Numismatic News
- Numismaster
- Old Cars Weekly
- Old House Journal
- Period Homes
- Popular Woodworking
- Script
- ShopNotes
- Sports Collectors Digest
- Threads
- Timber Home Living
- Traditional Building
- Woodsmith
- World Coin News
- Writer's Digest
Replies
Hi Jim,
Look in the business folder-"how to speed up estimating". Cargin and others have posted lots of sample spread sheets. I would also suggest your carp post his first attempts. I recently learned excel and cargin reviewed a few of my spreadsheets and gave me some quick tricks.
I adapted a spreadsheet cargin posted for doing handrail estimates.
Also check the finish carpentry folder at JLC...apparently they have a
spreadsheet folder. The Oct 2006 issue of JLC also has a free online article about using excel spreadsheets.
cheers,
silver
Hi Jim
Just some questions. Maybe I can help.
What does he have trouble with? The Labor or the the Materials.
What is his hourly rate? What kinds of finish carpentry does he do?
Hang doors, trim windows, install base, stairs and handrails, built-ins, kitchens, crown molding, paint grade or stain grade?
Does he give you a price and then that is what goes in the bid?
I am a small remodeler, so I don't get into the subcontractor builder relationship stuff so I have to ask questions.
Rich
All
I am going to post to myself to see if the e-mail notification is up and working yet. I haven't gotten an e-mail from BT for quite a while.
Rich
Cargin where would I find this spreadsheet solution you've developed. I'd love to take a look at it and see what you've done.
View Image
Whoops, never mind I found the thread and worksheets.
View Image
Jerald
The spreadsheets are pretty simple. But I would love your comments. Don't worry you won't offend me. I know I've got alot to learn. And I have to change some of my methods of doing business.
I am trying to rethink my business. From what I gather you have spent alot of time figuring the costs.
I started making some spreadsheets so I could get estimates out quick. So that I could give a customer a quick yet accurate price as a preliminary estimate. Then If they are still interested then we can get specific.
I don't have the answer for the finish carpenter in question. But I do have simple spreadsheets that will help him organize his though process and do the math. I can't figure his labor for him. But if a guy has no idea how to price stuff then a cost book would at least give him a starting point.
But they are only as good, if you know how to see all the aspects of a job like you described in your earlier post.
Rich
cargin - "The spreadsheets are pretty simple. But I would love your comments. Don't worry you won't offend me. I know I've got alot to learn. And I have to change some of my methods of doing business."
Rich one of the
really good things I get out of looking at the spreadsheets that contractors set up for themselves is the insight you get on how they organize their thinking. I collect them wherever I find them. It's always good to throw out your work for constructive criticism. With the software and just about anything I create I always ask people to tell me 'what really sucks about it'. Sometimes I may not think they're correct in their criticisms but it always helps to hear it.
"I am trying to rethink my business..." That's a never ending process for sure. I'm in a major rethink period myself right now. The times, markets, and opportunities are always changing all around us, especially these last two years so you can't just sit back and stand pat.
"From what I gather you have spent alot of time figuring the costs." Well yeah, you can say that but it's not just solely figuring the costs out that good estimating practice is built on. You also need to build and understanding and sensitivity about what the specific tasks are and about the time the tasks take. And when you do that task again and the time it takes comes out differently than what you have experienced in the past you need to look at it and understand just why it was different.
"I started making some spreadsheets so I could get estimates out quick. So that I could give a customer a quick yet accurate price as a preliminary estimate. Then If they are still interested then we can get specific." That's certainly the right idea, the idea behind using a spreadsheet or a database solution is to automate the estimating process to speed it up and ultimately reduce errors.
I take a look at all those worksheets you posted over the next week or so and give you some feedback. It a little bit hectic being Christmas time and I've got a couple of other things I have to deal with in addition to that but I will look at them and comment as soon as I can. Like I said it's always interesting to learn how people organize their thinking.
View Image
Jerrald
I'm looking forward to your reply.
Thanks for your comments.
I know you have a website and a business helping people in construction. Some of it is over my head.
Rich one of the really good things I get out of looking at the spreadsheets that contractors set up for themselves is the insight you get on how they organize their thinking. I collect them wherever I find them. It's always good to throw out your work for constructive criticism. With the software and just about anything I create I always ask people to tell me 'what really sucks about it'. Sometimes I may not think they're correct in their criticisms but it always helps to hear it.
Me too. I just haven't seen too many other people's spreadsheets.
Rich
Jerrald
I will post my latest evolution in spreadsheet design.
These are for my own use, so some of the design would have to be different if it was intended for use by others.
I have the materials in the left hand column and the labor in the right hand column.
The labor rate is for / crew hours. But usually if a task takes 1 hour for 1 person I still estimate it as 1 crew hour.
I work mostly remodeling and repair. Most jobs are $1,000 to $10,000. I work with my 2 sons ages 21 and 25. We live in a small rural town of 10,000. When we come to do a job we do every phase of the job.
The worksheet I will post is for basement remodeling. I also have worksheets for roofing, barn steel, bathrooms, garages, additions, replacement doors, decks, vinyl siding and a blank worksheet for jobs that don't fit into a category.
Prices on materials have to be continually updated. Some things like deck materials move around alot and some like 2x4, drywall and insulation really don't have much movement. I started doing this so I wouldn't have to call the lumberyard for every 2x4 I wanted to price out. All prices are for over the counter. If I have a bigger job I will have them qoute the job and the prices are usually lower than the over the counter price.
The latest worksheet concept is to do a estimate maunally and have sheet # 2 working along side it with the SF numbers from Craftman's Nat. Insurance Remodeling and Repair cost book. I am working at getting the SF numbers out of Craftman and into the worksheet and any value or quanity that I enter in the manual worksheet to automatically transfer to worksheet #2.
I did a search in BT and you mentioned it as a cost book in which you mined alot of data. And it was only $25 to download.
Does that make sense to you.
You are right no cost book can replace a experienced eye for breaking down a job.
Materials are relatively easy to figure, it's the labor that I would like to tap into a cost book for input. Then use the highest number.
To use the worksheet, yellow cells require data from the user. Gray cells have formulas in them. Fill in the yellow cells with lengths of walls or quanities. The other colors are just for looks. Green is for labor. The gray cells in column C are automatically filled in by entering data in the yellow cells.
I have the bathroom worksheet below and the subtotals automatically are entered in the worksheet above. ( I built this aspect before I figured out how to use different sheets).
This is still a work in progress and I am not done with it. Nearly everytime I use a worksheet I see improvements that could be made.
A basement worksheet is different than all the rest because some walls are existing, some have sheetrock only on 1 side and some have sheetrock on both sides.
I have yet to take the totals from Nat. Ins. estimator and enter them along side my manual for a side by side comparison (sheet #1 vs sheet #2). I did that on the last vinyl siding worksheet that I posted to Silver.
I would like to clean up the beginning of the worksheet to make it more understandable to others, maybe a question and answer format, but that will change all the formulas. Someday.
This a hypothetical basement all labor #s are just punched in quickly without regard to reality. I haven't done the Nat. Insurance part for the bathroom section yet.
Where is my thinking flawed. Where could I use improvement. Thank you for your input.
About the finish carpenter. Like the guy in another post (Pricing- I have no concept of pricing), it sounds like this guy needs some very basic help. A simple spreadsheet to help him organize his thoughts would be helpful. He is not going to go from where he is at to being another Mike Smith or Jerrald Haynes over night.
Rich
Cargin, I love your spread sheet and desperately need something like the one you have come up with. Is there a chance that you could e-mail yours so I can save it and use it.
Thanks Ron
ZZZZ
All you have to do is have an open excel sheet ready.
Highlight the whole spreadsheet, press control C go back to your open Excel sheet and press control V.
Then you have it.
If you have problems just post to me and I'll e-mail it.
Let me know how it works for you.
I have posted other stuff at "How do you speed up estimating"
But it's not finished. Keep that in mind.
Rich
Edited 12/20/2007 10:01 pm ET by cargin
Ron
Just curious how you are doing with spreadsheet estimating.
Were you able to copy the spreadsheet?
How is it working for you?
Thanks
Rich
I do not know all that much about business. Tried and failed, will try again when I have the money.
Does anybody cost code? I spend about 1 hr a day filling out cost code time sheets for the company I work for. Each task is assigned a number and than man hrs are filled in under that number. Doing this allows the company to keep track of where the money is being spent. And how to bid the next job.
EX 200 form work
300 pour concrete
400 site prep
400 3hr, 200 5hr, 300 6hr
Now we know where the money was spent. Instead of saying it took 14 hrs to complete the task. Maybe 5 hr was over budget for the form work and we now know we need to tighten up or use a different system.
I like the idea. Do you have a master list of codes to share? Bob's next test date: 12/10/07
Yes I do, I just have to figure out how to get to my computer. All the codes have to do with the bridge I am working on, but they will give a general idea of how they are used. They are used in conjunction with estimating software. I work for a big corporation and they won't apply to a small residential business. Still, it may give you an idea for your situation. Let me work on it I'll get back to you.
Don't reveal anything that could get you in trouble. Bob's next test date: 12/10/07
I am already in trouble. That is why I am sitting home right now. I got suspended for 2 wks. Corprate politics. Funny thing is I am going back with a raise. Go figure.
Jim with all due repect to cargin's and silver's generous advice I not always convinced that having a spreadsheet or database tool necessarily makes finsih carpentry or any kind of estimating more accurate. They often just allow the contractor using them to make the typical estimating mistakes faster. Is his problem really in just getting the numbers to add up or is the problem in the development of his Work Breakdown Structure?
In other words is he missing the time for things such as the set-ups for specific tasks such scaffolding, temporary railings, or a work station? Just the other week I watched two of my guys spend about an hour setting up scaffolding for a task they got done in about fifteen minutes time.
Is he missing or making mistakes in his material haulage and distribution estimates. Sometimes the time and cost of just getting the materials to where they're going to be used is very significant.
Are his estimates taking into account it takes longer installation times (due to the care involved protecting existing surfaces and finishes) to install woodword in remodeling situations than it does for new construction ?
Some task you don't know if it going to take an thirty minutes to install each widget or and hour and a half so you need properly size a cost buffer to account for the variation. Is his contingency planning realistic? And watch out for that too in that it is just as common, in fact I'm thinking even more so, to over estimate contingencies.
And does he have a corrctly calculated labor rate in place that he basing his estimating on in the first place?
View Image
His starting point should be a detailed log of his work. It should account for the amount of time and materials required for every task. This includes set-up/tear down, material order (if required), measuring, cutting, installation. And he should take notes on how he does it (does he measure or does he scribe?).
After doing this for a few jobs, look at his log together. See if there is anything that could be eliminated or re-arranged to make it more efficient.
Once you know this, estimating should come easily.
Bryan
Can you post a log that you keep?
How do you track this information?
We have discussed this before, yet I haven't figured a good way to keep this data organized.
Rich
You would not like any log I keep, unless you are into life tables, mortality data, and digestive diseases. I don't build for a living. I am a project manager however.But by log I just mean write down the start time and end time for each activity. After that, most things should come together.
Hey Cargin,There was a discussion not too long ago where Mike Smith posted his daily logs and I picked up his mobilization/demobilization which is similar to my set-up/tear down but more encompassing I think...I'll see if I can find it...silver
Phil
I saw that post and I saved a copy of the log.
My question is how do you use that data? How do you track the jobs so that on Job #1 it took you 5 hours to install 5 newel posts.
On # 2 it took you 3 hours to install 5 newel posts with different variables.
And on #3 it took you 10 hours to install 5 newel posts.
Then you have drywall, old plaster and lathe, PITA situations and people, travel, vanities, cabinets, trim, rotten wood and the list goes on and on. We are all over the house inside and out.
Yesterday the boys spent several hours reinstalling pink plastic wall tiles 4"x4" in a door widening job, while I trimmed and cleaned up. Don't want to do pink plastic tiles again.
I don't think I am that anal that I can keep a log of every activity and then enter the data in a format I can decipher.
I think you will see trends like how much time you spend on mobilization and tear down.
I am thinking about adding a category like That Last 1/2 of a Day that took all day and then some.
Rich
"I am thinking about adding a category like That Last 1/2 of a Day that took all day and then some". Hi Rich,I do what Jim described as an early approach of his...I do lots of custom work so each project is unique... I go through each project mentally, listing the major tasks and then put a number down from my mental database given the known givens-PITA customer?/dogs/kids/problems...and when I need to I add fudge margins to each task...Not scientific but what has been an eye opener has been tracking jobs.
I have not been estimating enough labour and keep trying to add more labour, to the point that I have shocked several customers and had to renegotiate the scope of the project.I also agree with blue that people tend to have a number and in any given situation there is a magic number...below that you leave money
on the table...above that you risk not selling the job...so for me a lot of subjective factors as well...any red flags on the play? do I want to work for these people. And I'm trying to avoid the
sell-when I'm hungry-approach cuz it always bites me in the ####.Phil