Let’s have this go-round one more time. Hydronic heat in-slab, foamboard insulation underneath. Didn’t someone tell me once here in this forum that we are throwing away our money putting foamboard any further than 4 feet in from the perimeter? My 4-foot perimeter is clean, but inboard from that, we encounter plumbing, column piers, thickened slab at bearing walls, etc. I am not looking at just material savings here, but also the labor and hassle of cutouts, detailing, and so forth.
Discussion Forum
Discussion Forum
Up Next
Video Shorts
Featured Story
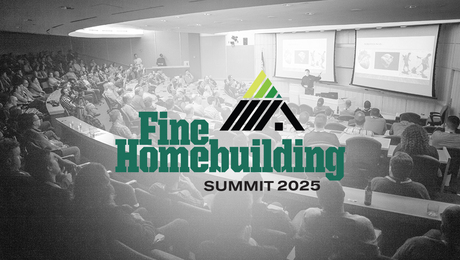
Join some of the most experienced and recognized building professionals for two days of presentations, panel discussions, networking, and more.
Featured Video
SawStop's Portable Tablesaw is Bigger and Better Than BeforeHighlights
"I have learned so much thanks to the searchable articles on the FHB website. I can confidently say that I expect to be a life-long subscriber." - M.K.
Fine Homebuilding Magazine
- Home Group
- Antique Trader
- Arts & Crafts Homes
- Bank Note Reporter
- Cabin Life
- Cuisine at Home
- Fine Gardening
- Fine Woodworking
- Green Building Advisor
- Garden Gate
- Horticulture
- Keep Craft Alive
- Log Home Living
- Military Trader/Vehicles
- Numismatic News
- Numismaster
- Old Cars Weekly
- Old House Journal
- Period Homes
- Popular Woodworking
- Script
- ShopNotes
- Sports Collectors Digest
- Threads
- Timber Home Living
- Traditional Building
- Woodsmith
- World Coin News
- Writer's Digest
Replies
I am building a 24 x 36 detached garage with radiant tubing in the slab, and put the foamboard under the whole floor. If there is any compression or settling, I wanted it to be even. I realize that the perimeter insulation is more cost-effective than the insulation in the center, but my hot water temperature will be a lot warmer than the natural soil temperature and I want my heat to stay in the garage. (The idea that "warm rises" applies only in convection, not conduction.)
Good luck!
I am just finishing framing a basement that we put radiant heat in the slab. 3500 sq. ft. basement. I put vapor barrier (3 mil plastic) over compacted dirt and 2" foam (R10) across the entire basement floor. I also put 2" by 4" rips around the perimeter of the basement which I took out after the floor was poured. This acts as a channel for any moisture that may find its way through the walls and also acts as a thermal break to the outside walls. Then we layed down 4" X 4" mesh and tied the pex to that with nylon tie locks. As we were pouring the floor one guys job was to lift the mesh with the pex to midway through the slab. I fashioned a hook out of rebar to do this.
Also you should pressurize the pex to 40 lbs during the pour.
Alex
http://oikos.com/esb/45/radiant.html ?
some links at the bottom.
Phill Giles
The Unionville Woodwright
Unionville, Ontario
The greatest losses will be around the perimeter but (north of Mexico) you do continue to lose heat into the ground. The biggest losses will be initially (first few weeks) as you bring the upper several feet of soil up to RFH temperatures. But the losses do continue after that.
The other downside to not insulating everywhere is one of responsiveness. Since you will be heating a larger mass, it will take a bit longer for the RFH to respond to heating demands and you will experience slightly greater overshoots and undershoots from your thermostat setpoint.
But skipping a few square feet? Not a big deal. Rip some blue board to a width so that you can butt it up against your wet-wall stub-outs on each side. Then fill the gaps with sand (or concrete).
Merry Christmas David,
I would challenge the first theory..
but (north of Mexico) you do continue to lose heat into the ground. The biggest losses will be initially (first few weeks) as you bring the upper several feet of soil up to RFH temperatures. But the losses do continue after that.
I believe that not one qantifiably degree is lost in the central part of the slab. Once you have excavated a few feet below grade, it becomes part of the building's constant.
Gabe
So you are saying, Gabe, that I don't lose much heat by NOT insulating the central portion of the slab? My area is a 28 x 56 foot rectangle, and by just insulating the 4-foot of perimeter, that leaves me an uninsulated area at the center, a 20 x 48 foot rectangle, a savings of 40 sheets of 2-inch foamboard. Real $.
That's correct Gene.
Do spend a little time making sure that your vb is perfect and without tears or open seams and that will have more of a positive effect than buying sm for the middle area.
Gabe
maybe checkout http://oikos.com/esb/45/hydronics.html - might be in the library.
Phill Giles
The Unionville Woodwright
Unionville, Ontario
As a plumber in British Columbia I will not install a RFH system if the contractor or homeowner has not insulated under the whole slab. I have been called out to jobs that others have done where the homeowner is complaining heating costs are extreme. In all of these cases the slab was either not insulated at all or only the perimeter was insulated. The homes with the highest heating costs were the ones with watertable passing under the home taking the heat away.
That would be a lot of bs. You're a plumber, remember your place. I don't unplug toilets and you don't design.
Gabe
Gabe: So your arguement is that 4 feet of dirt (if 4' of perimeter is insulated) is a lot of insulation? I would agree. About as much as 4" of foam. But just as there are clearly loses through 2 or 4 inches of foam, there are loses to the side and below even through many feet of soil. Enough to effect boiler sizing? No. Maybe 5% or so more BTU/hour would do it so the design isn't effected in that way.
But it can effect system design more so because of the larger thermal mass and therefore the need to have smarter controls (PID, outdoor reset, etc) than in a lower mass system.
Your hydrology is not totally correct, but you are right in almost all cases - it would be unusual for groundwater flow to effect heat losses significantly. It would take a very shallow water table to convect much heat away. But some people actually build houses that require active sump pumps 6" to 18" before the basement floor. That combined with a moderate groundwater flow velocity (i.e. sands and gravels) would move a lot a BTUs. For those people who believe a proper basement is just shy of being a functioning well, groundwater could conduct and convect away a lot of heat.
(I unplug toilets, do hydrology, AND design.)
David Thomas Overlooking Cook Inlet in Kenai, Alaska
Hi David,
I believe it all comes down to dollars and sense.
(And you're right about the toilets...I unplug them too but I wouldn't call myself a plumber.)
It's always a site call as to bring the mass into the envelope or keep it out. Every situation demands some thought. Building at or below the high point of the water table would require some head scratching. I don't encourage it but if I had no choice and wanted to heat efficiently...I would heat above the slab and inside the walls. SM that's under water isn't worth much.
It's not unlike when I build an arena for year round use. We have 4 inches of hd sm directly under the concrete slab but we also have heating lines buried in the sand below the sm. If we didn't have the heating lines, eventually we would have a permafrost situation under the slab and heaving could become a real threat.
I think that in our climate, the slab area conducts more cold from the upper perimeter walls that are exposed to the elements than from the middle slab area. The ground effect is constant in that it requires reduced energy to heat in winter and let's not forget cool in the summer as well.
An efficient energy program takes what is already there and improves on it, not ignore it by working independently.
Gabe
c'mon gabe... the earth is an infinite source of temperature... in our area if you go down below the frost line it is a constant 45 deg F.
if his slab has a design temp of 70 and the earth below the slab is 45.. then he has a delta -T of 25 deg F. ...... 24 hours a day for the entire heating season..
this is a big deal.. especially is he has taken the pains to tighten up all of his other insulation specs and especially if he has a radiant floor feat ..
there is no suce thing as " once he has heated up the area to an equilibrium"
all you have to do is turn off the heat , and the below slab temp will return to 45 or what ever it was before he turned the heat on..
the only way to maintain an equilibrium temp of 70 below the slab is to lose heat into the ground to overcome the temp. of the earth below the equilibrium point
course , i still stand by my ..
but hey, whadda i no ?Mike Smith Rhode Island : Design / Build / Repair / Restore
Ahh, but the slab will still go to 45F even if you insulate, right? Even if you put, let's say, 12" of rigid foam under the slab, it will still lose some heat and eventually go the ambient soil temperature. So how much is enough? 2"? 4"? 0"? Everyone agress that it is most important at the perimeter. And least important at the center. So should we start at 6" at the perimeter and taper smoothly to 1" at the center? It would maximize the use of materials but spend a lot more labor dollars. So 2" stepping down to 0" or 4" stepping down to 2" seem like a reasonable approach to me.
But the particulars will depend on current and future energy costs, local practice (I avoid swimming too far upstream when I can), and HO's budget. Heck, you can't get people to spend $6 (compact flourscents) or $100 (weather stripping) when there is huge, short and repeated payback.
David Thomas Overlooking Cook Inlet in Kenai, Alaska
pretty easy when you do a heat loss analysis.. you button up the attic insulation, upgrade the windows, put some foam in the walls.. insulate the perimeter.. and then run the numbers.. all of a sudden there is this gaping hole in the fuel budget.. right in the middle of the slab...
in Kenai.. i don't have a clue..
but here in RI ( with a 6000 DD. design ).. i settled on 2" under the entire slab as our standard...we've used that since about '84..
also when detailing... the subgrade gets all of the utilities installed , gravel base compacted, vapor barrier installed.. then the 2" foam .. if you don't detail it continuous.. you have to change the slab thickness where you leave off the foam...
what do you do.. use a 4" slab ... then change to a 6" slab ? or do you taper it ? no... if labor and control are important.. just maintain the same detail across the entire slab..
is it cost effective ?... depends , don't it ? the only thing i know is that most of the energy conservation decisions we made in the past proved to be well worth it as time went on..
AND..if you set the room thermostat to the same temp, there is no doubt that a slab with 2" of foam under it will be more comfortable, as far as temperature goes, when compared to the same slab without the foam.
but that has just been my observation.. along with a lot of other things i've read and studied over the years... one energy / cost analysis will always be different from someone elses.. when i mentally factor in the investment of money in the structure ( with tax supported mortgage ) vs. operating heating costs.. (no tax support ).. and add in the increased comfort level.. it seems like a no-brainer to me..
someone else may want to put their mortgage money in a jaccuzzi.. or something else... i like warm houses that are easy & comfortable to heat
Mike Smith Rhode Island : Design / Build / Repair / Restore
Hi Mike,
Seeing that we're discussing no brainers, here's a question for you.
What would be the difference in energy costs of a basement in a typical 1200 square foot bungalow in Rhode Island, if the entire slab is over 2" sm as compared to one that has only the 4ft. perimeter installation, over the entire year cycle?
What would be the cost difference between the two at time of construction?
How many years would it take for payback, taking into account interest payments on the extra costs and conversely interest benefits from investing the saved dollars?
Bottom line Mike is that you're wasting client's money by putting sm where it's not having a measurable effect.
Gabe
gabe.. what's a measurable effect ?.. how's about.. "the floor feels cold over here in the middle " vs.
" man , i love this house, no cold spots "
oh , yeah.. and what are the other parameters ?
you know. r-value of attic , r-value of windows , walls, ? blah, blah, blah.. when you get down to it...if you build an energy efficient house and leave an uninsulated oasis right in the middle of the living room ... what good is that ?
you build yours .... & i'll build mine...
but hey, whadda i no ?Mike Smith Rhode Island : Design / Build / Repair / Restore
Come on Mike, we're not playing dodge ball here.
We're supposed to be discussing the need for insulation in the middle of a basement or slab when you use infloor heating. Regardless of the method used, there will be no cold spots so don't bring that into the discussion to confuse things.
What we were discussion until your train ran off the track was whether the difference was measurable.
And now we both agree that it's not.
To which the logical conclusion is why waste the money.
Gabe
Gabe, Baby, I'm going to disagree with you on this one too, not only because the theroy Mike is explaining logical, but also because I once heard a radio discussion around a study that our University in Maine had done. I don't have a link so if you want to deny it, that's fine but it does exist. They had done thermal loss studies by placing sensors under slabs in identical homes with and without the foam. They didn't build the homes but had permission to insert these while a subdivision was being built. The conclusion was that there was indeed extra BTUs lost where no foam was placed, and that the loss was greater where the water table was closer to the surface, something that is common in this state.
My own subjective experience is that the foam does help. I did get talked into placing crete with radiant several years back over some of that astrofoil instead of the 2" of foam that I normally use. comments I hear from that homeowner are that the system runs regularly to heat that wing while the other wing of the house does not keep calling for heat as often. It is over foam.
If you are sleeping outside in the winter, would you like to have a slice of foam under you or would you just as soon sleep on bare ground with the foam spread four feet around you? I'll take the foam, even in summer because the ground rarely gets over 55° on the surface in the summer. it is 45° and less in winter. 53° is our ambiant temp a few feet down. The diff between 53 and 73 is obvious. I want a barrier.
You criticized a plumber for his 2cents but the plumbers I use who do heating install according to specs from a heating engineer. He will not design a system without doing a heatloss study first. Knowing that the foam is under the slab is part of his study because he inputs all this to formulae that calculate makeup heat. With no insulation, he needs to supply more heat with his design.
.
Excellence is its own reward!
oh , and so as not to avoid the questions <<<<<
What would be the difference in energy costs of a basement in a typical 1200 square foot bungalow in Rhode Island, if the entire slab is over 2" sm as compared to one that has only the 4ft. perimeter installation, over the entire year cycle?
What would be the cost difference between the two at time of construction? >>>>>
(1) we were not talking about a basement, were we ? we were talking about a first floor slab.. the main living space...
.lets say a 32 x42 ranch...ok ? the difference is 816 sf.. the difference in r-val is about 10 vs 1, the delta -T is the same.. so the difference in BTUH is about 18,000 more or less.. you plug in your own energy values..
i stopped doing payback analysis about 20 years ago.. either people believe or they don't ...but if you want to do a payback analysis , i'm all ears
the difference in cost would be about 2 guys @ 4 hours plus the cost of 816 sf of 2" foam.. again , you supply the numbers.. and i know you put foam under the entire surface of some of your skating rinks.. so why not under someone's house..
and yes , i do have 2" of foam under MY basement slab.. right under the 480 CRF rock storage bin for our hot air solar heat system... guess what.. i've got a warm basement..
Mike Smith Rhode Island : Design / Build / Repair / Restore
Mike,
We'll continue when and if you start being smart instead of smartasssed.
I don't like made up numbers.
Gabe
gabe.. if we're talking about radiant floor heating.. then you're really off track.. any one who would spec a radiant floor slab without the insulation is just not giving their customer a good job.. it would be a substandard job..it would be against any decent RFH spec
my jobs are not even for radiant floor.. just standard slab construction in a cold climate.. so make up your own numbers....
better a smart #### than a cold ####... hah, hah, hahMike Smith Rhode Island : Design / Build / Repair / Restore
So Mike,
What's the dollar advantage in wasting sm?
I don't do substandard work but just as important, I don't waste other people's money either.
And that's what it boils down to Mike, ther people's money, giving value, knowing what's needed and what's a waste. If you want to sell sm then sell sm but don't expect me to endorse the waste of material.
If you can't calculate the real benefits then you can justify the use of it.
Gabe
i did calc. them... but you labeled it as "made up numbers"... so make up some of your own..
if you don't like my numbers show me where they are wrong..
your take is i'm wasting money.. my take is you're trying to bully your way into supporting your position..
your insulation for the 816 sf area is 4' of soil... and how did you get the 4' of soil raised to the point where it is not sucking heat out with a delta-t of 25 ? i think you ran your boiler and pumped some btu's into the dirt...
the loss is still the same... 18,000 btuh...constant .. 24 hours a day.. as long as your heating system runs... cone of influence or whatever you want to call it..
yup... the edge loss is worse.. because you have moving cold air... and the abutting soil is at a lower temp... but the earth beneath the slab is still 45.. and the only way to change that is to pump some btus into it and keep pumping them in...
mine is 1/10 of that.. because my insulation is R-10... your insulation is what ? R-1 ?
unless.. wait .. you didn't finally break thru on the old conservation of energy thing , did you ?....... my , god , man... that's great.!... do tell ! hah, hah, hahMike Smith Rhode Island : Design / Build / Repair / Restore
Not so fast Mike.
You haven't advanced to metric so you'll have to use your head a little to understand the numbers but it will give you an insight into the dynamics of slab edge temps.
View Image
The emphasis has to be on edge protection in cold climate slab construction. We have to build to protect houses from frost damage, therefore we normally install frost footings around our slabs and if you're going to go down below frost levels with a wall you may as well install a full basement.
Having a small heat loss into the ground also has the added bonus of preventing frost forming under the exterior edge and doing damage to the slab.
We've also noted that in a year round calculation of energy cost, the ground constant does balance out.
Gabe
gabe... whoa now.. are we talkin frost protection or heating comfort and fuel use ?
notice the cute little metric numbers start to increase s you go to the interior of the slab ? notice that ... do ya , huh ?
that's cause the little 20 deg. C. in the interior is losing heat to the ground and raising it's cute little number btu by btu..
hah, hah, hah.... yur so easssssyMike Smith Rhode Island : Design / Build / Repair / Restore
We're taking both, Mike.
The graphics show the effects of insulation at the slab edge where it belongs. The inside temperature indicated is the benchmark most often used in studies.
BTW the reason that I know you don't have figures to back up your claim is that they don't exist. No one has ever really done an analysis that could be used to create a universal formula. The so called short formula was found to be too inaccurate to use in studies.
NRC here is trying to develop one but it's still not accurate enough for dependable field use.
The Scandinavian way of doing slabs on grade has some of the elements of what you like. That is, the use of SM over the entire area, but they also use 6 inch minimum slabs with steel around the perimeter and mesh in the center area. However they put the SM under 6 inches of sand for a total of 12 inches of cover over it.
Heating is also different. Apples and oranges but interesting never the less.
Bottom line, you do it your way and I'll do it as good and cheaper.
I'm in a good mood, my hockey team won in overtime and the ice is good on the lake.
Gabe
ok, buddy.... yur all right in my book.... just don't let my customers know i'm wingin it...
and let's be careful out there.. watch out for open waterMike Smith Rhode Island : Design / Build / Repair / Restore
Come on up Mike, I'll keep an extra hole open for you and even put a small piece of SM on the seat just for your comfort.
If you can't do it on ice at least have some ice in what your having.
Gabe
lessee... the frozen noath fer some ice fishin. ?..
'er ah, Charlotte , NC fer some golf with my son-in -law. ?.... damn... decisions, decisions...
thanks for the offer... best to you in '03 ...
by way of nothin in particular.....didn't you use to wonder how they referred to time at the turn of the last century ? and now , here we are.... just rolls off the tongue ... my great grandfather should see me now... my , oh my... do we live in wondrous times or what ?Mike Smith Rhode Island : Design / Build / Repair / Restore
Can't understand why you would rather spend the day wacking a ball into a hole when you can have a ball wacking what comes out of a hole.
Oh well, have a safe trip and a prosperous new year!
Gabe
BTW.... great graphics !Mike Smith Rhode Island : Design / Build / Repair / Restore
If you liked the last one, you'll love this one.
Here's a sketch of an adaptation of the scandinavian model to northern rural applications.
View Image
As you can see the emphasis is still on the slab edge and uses conventional heating. Ideally here, heating pipes in the sand at a moderate temperature would be best in harmony with conventional heating.
Gabe
I'll jump in here with another observation.
Almost everything I build is slab on grade, radiant (hydronic, in the slab) heat.
I went away from foam board under the slab for several reasons; cost, the irritation of working with all this foam board, the general impression that it really wasn't doing as much in the middle of the building as it was at the edges, and a strong concern for the quality of slab I was ending up with where the foam stopped. (It cures differently over the foam than over the dirt.) Besides, I always insulate the vertical surface of the perimeter really well. Anytime I can use ICF stemwalls, we're at R-22, which is about twice what's required for our 6001 DD climate.
In anticipation of any objection of how the foam is any different from a vapor barrier, it is generally recognized by concrete contractors, code officials, and the ACI that in these hot dry climates a vapor barrier is not a good idea unles it is covered with a few inches of sand. Try covering foam board laying on a dirt subgrade with sand some time. Or don't. It's miserable.
Anyway, we started using R-Foil with an inch or two of sand over it. The radiant heat works really well, the house stays amazingly comfortable, and the slab doesn't curl.
So I don't know a thing about the theory of this stuff. All I can say is it works. Just another option.
DRC
What's this R-Foil you're referring to?
It looks like bubble wrap with aluminum foil inside.
When you first look at it, intuition tells you there's no way it can work. Like maybe we just got BS'd at 60 cents a square foot.
Then you turn the heat on an it responds about three times faster than you think it should.
One of those many things that work in practice but not in theory. I'm getting used to it. <VBG>
DRC
Dave: You touched on something which I've wondered about.....how does the foam hold up to being trampled while you're doing the pour? It seems to me it'd get broken up some in that process.......
couple things... if the subbase UNDER the foam is well graded and compacted, and the foam is at least two inches thick.. you won't have a lot of trouble with the foam breaking up...
we like to broadcast about an inch of sand to help hold it in place and help with the wear and tear during the pour...
as in all things , haste makes waste.... and you have to have everyone treat the foam with a little TLCMike Smith Rhode Island : Design / Build / Repair / Restore