trench is dug, starting the forms tomorrow. Any helpful tips would be appreciated. 70 feet long, 6″ at top, 9″ at bottom, 18″ high. Using 2x lumber with plywood gussets for connecting the boards.
Discussion Forum
Discussion Forum
Up Next
Video Shorts
Featured Story
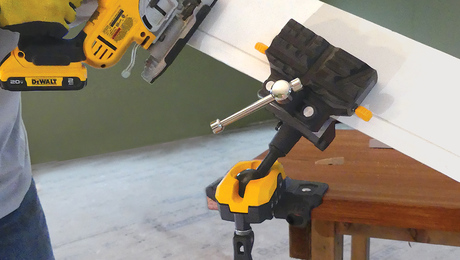
The IQ Vise has angled jaws, a simple locking mechanism, and solid holding power.
Featured Video
Builder’s Advocate: An Interview With ViewrailHighlights
"I have learned so much thanks to the searchable articles on the FHB website. I can confidently say that I expect to be a life-long subscriber." - M.K.
Fine Homebuilding Magazine
- Home Group
- Antique Trader
- Arts & Crafts Homes
- Bank Note Reporter
- Cabin Life
- Cuisine at Home
- Fine Gardening
- Fine Woodworking
- Green Building Advisor
- Garden Gate
- Horticulture
- Keep Craft Alive
- Log Home Living
- Military Trader/Vehicles
- Numismatic News
- Numismaster
- Old Cars Weekly
- Old House Journal
- Period Homes
- Popular Woodworking
- Script
- ShopNotes
- Sports Collectors Digest
- Threads
- Timber Home Living
- Traditional Building
- Woodsmith
- World Coin News
- Writer's Digest
Replies
how much is underground?
how far apart are the stakes?
rebar?
plywood vs 2x?
bobl Volo, non valeo
Baloney detecter WFR
"But when you're a kibbutzer and have no responsibility to decide the facts and apply the law, you can reach any conclusion you want because it doesn't matter." SHG
how much is underground? 12" except where the driveway opening is, than 16"
how far apart are the stakes? Whatever I set them at, I was figuring every 3-4'
rebar? none
plywood vs 2x? I have some salvaged 2x8's from the porch tear off. The trench itself could be the bulk of the form, with lumber used above grade. This would result in more concrete being used. If I form in the trench, I'll use plywood below grade, 5/8 since it allows me more room to work.
Concrete contractors use special U-shaped bars to form curbs, driven into the excavated ground a few inches.
The form material is oiled flexible stuff, maybe 1/4" plywood, so that the curb can be given a fairly tight radius. It rests inside the bars.
The concrete is poured fairly stiff, finished quickly with a wood float, then an edging trowel.
Depending on soil conditions, you can get the same result using 2X4 or rebar for stakes, 2X4 for speaders.
There's not much pressure on the bottom of the form so you don't have to get carried away, driving the stakes deep.
It's more important to keep the form as straight as possible because the curb draws it's own line when done.
Edited 5/7/2008 1:34 pm by Hudson Valley Carpenter
soil is sand on one side, compacted stone/sand on road side. The curb is one straight line, no need to make any curves. I felt the 2x, being twice as thick as plywood, would hold the line better. Thought about making plywood u shaped thingamajigs in place of the metal ones if I feel the stakes are not going to hold the form. 35 -37 of them made quickly, gang cut style, screw through them into 2x, toenail sort of thing. Using screws everwhere so I can disassemble easily.
I was thinking I would remove the forms pretty soon, so I can get a nice finish with masons brush while concrete is still workable. Any thoughts on timeframe for removing them?
You don't need to make up the plywood thingamajigs. Just nail a spreader (short 2X4) across the top of the form every three feet or thereabouts, to hold the form firmly together at the proper spread measurement.
Using stacked 2X8s should work well, just stagger the top and bottom joints and stake each joint, adding a speader whenever there's a joint on the top course.
It's common practice to use 16d common duplex (double headed) nails for form work. Makes it much easier to remove the nails.
You can remove the forms the morning after the pour.
BTW, in order to get a clean finish without honeycomb voids, you might want to bang on the form with a framing hammer as the concrete is poured. That usually causes just enough vibration to make the concrete settle nicely.
used double head nails for the foundation pour, woked well. Did you happen to read Bings idea, seemed like a real nice system, and I have loads of plywood left from the foundation forms. You don't think I should take the forms off while the concrete can still be worked?
This is about as simple a concrete form as can be built so...were I in your shoes as an intelligent gent who embraces this kind of challenge...I'd just use the materials at hand and make everything just a little bit stronger than seems necessary. Go about it however you like, it won't be bad.
Just make sure that it's dead straight because your eye will pick up any variation. If it's in a visible place, as most curbs are, that could irk you for years.
If you pour in the morning, you can pull the forms in the afternoon...whenever the concrete has set up firm. You be the judge. It's not difficult to tell. Be prepared to fill voids with a bag or two of Sacrete motar mix and a wooden float or similar tool.
better to dress it up later than risk other problems by pulling forms early. thanks for all your help!
wow, you got my attention here.
in all of the curb forming i have done, i've never used anything other than our company's steel curb forms.
never even considered doing it with wood.
carpenter in transition
got a buddy in the concrete business, said I could use his forms, steel like yours. They are too long to haul down there in my truck, so I passed on them, got a lot of wood laying around, allready on site.
One usually doesn't pull the forms till the next day.
Not to say their aren't exceptions. But You can end up with problems
if the concrete is still bonded to the forms.
On this type of thing, I resort to some stuff I learned fromn my mentor.... All the pressure on this pour ( like any ) is at the bottom. I'd say an 18" tall curb from 9 to 6" still has a little push.
Metal straps are what I'd use. Steel bridging, lumber bands, whatever. Build your form 8' at a time, using the band to lock it together at the 9" point, every 3' or so. Flip it over, set the width at 6". Lock the seams with 2x stock overlapped a foot or so. The bands on the bottom, wrap a couple inches up the ply....you won't need stakes to do anything more than lock the whole thing straight. The bands keep the bottom from spreading. The concrete weighs on the bands and prevents uplift.
Good luck.
Bing
a simple and effective solution. you would use ply, cut 18" for one side, and length to reach level on the diagonal side, slightly more than 18". as for the metal straps, what do you use, Simpson or plumbers strapping?How do you transition to the deeper part where the driveway will be? I figure I can make two of the 8' sections for that area, but wonder how you would connect it to the other sections sitting 4 1/2" higher, right and left of the driveway.
Edited 5/7/2008 7:04 pm ET by dockelly
I don't generally buy straps. Usually have lumber bands laying around in a pile ready to go to the dumpster,( or lately, to whomever is picking for scrap metal). cut to length. punch a hole in each end w/ nail set or center punch. If I have 'em I've used steel bridging since I use hardly any anymore for what they're made for, although I do keep a box around for hingeing walls when standing. I guess plumbers stapping would work fine, as long as the holes weren't to big. I would typically pour a footing in the am., and could strip next am, with no conc sticking to the form to speak of. When I built my own house, I used this method, but using furring strips every 4', 2x12s, and scraped each one ( minimally ) after, used every one for header stock in the house.6d common is what I've used with the straps, I agree the duplex nails are easier to pull, but I just walk around with a cane bar and pry up on the straps; usually pops both out. Remember, the fasteners are in shear, not tension, so length not AS important.
Ya lost me on the transition question. Can you re-phrase so my sometimes feeble mind can get around it?
Bing
transition question. The curb dips down to allow the car to go over it into the driveway. The engineer for the town spec'd the total concrete be 18" in depth, even when the curb drops down. So the trench does drop as well.
In other words, the majority of the curb is 12" below grade and 6" above. The dip for the driveway is going to be 16 1/2" below grade and 1 1/2" above.
I just threw out a bunch of that lumber strapping, darn it.
just an update on the curb, turned out pretty good. Actually had 4 people ask if I would do theirs. Not sure I need a second job just yet, but I get their frustration. It seems to take forever to get guys to do work on the island.
just an update on the curb, turned out pretty good.
It would be a lot more edifying to see some photos of your (our) job. ;-)
I'll put some together soon, maybe this weekend. This way you can see what a good job your doing:)
To paraphrase what they used to say about the yellow pages, I'm letting my fingers do my work.
By the way, I found a couple of good books on the subject at Amazon. Searched "concrete forms" there. One of them's a Taunton book.
I didn't buy either one, just read the descriptions and reviews. But I'll probably get the Taunton book, as a ready reference.
Edited 5/22/2008 9:13 am by Hudson Valley Carpenter
pics as promised:
you do your curbs different from we do, we incorporate a gutter too, to keep water from running bewteen the curb and pavement, weaking the subsoil
Edited 5/26/2008 4:34 pm by brownbagg
Yes, you would not get away with making a curb like that around here. Besides the fact that the water wants to run down the crack, the vehicles parking next to the curb eventually break the edge of the blacktop.
The curb job looks nice, but wouldn't pass here.
it would have been so much easier to incorporate a gutter with the curb, but what you see is what the town wants. All in all I'm pleased with how it turned out, my first curb and all.
Fine Job! Now you can get a part time job with the local street dept finishing up the curbs along the rest of the street. ;-)
They can't get your Goat if you don't tell them where it is hidden.
had 4 people stop me while I was working to see if I would do theirs. All have the same complaint, price wasn't the problem, getting a guy to do it, was. As one neighbor said, " I have this guy who I gave the job to and he's been promising me for months. I ask him when does he think he'll get to it and he says "he's busy and If I don't like it find someone else."" Had to post a $5000 bond to get a temp CO so he can use the house he just renovated, final is only waiting on the curb. I've actually started to think of setting my cousin up in some sort of curb business, he's a good guy but needs direction.
I hope that speed walker appreciates your hard work.
Look at my post with the pics, accidentally replied to myself. Think it's #22.
Better than your average curb crew, Booboo. Straight by eye and nicely finished too. Even your cold patch job looks professional. Congrats.
You're right. It would make a nice little business...for someone who likes the many small daily challenges and wants to be self employed. I wouldn't suggest it for anyone who isn't a self starter and willing to do some daily pick and shovel work.
Edited 5/26/2008 9:30 pm by Hudson Valley Carpenter
Thanks for the kind words. If I had to name one thing that came as a surprise with this project, it would be the amount of shoveling. 110' by 2' by2' footing was expected. 20 yards shoveled under house, and 20 more against house, 70 ' curb trench, and more to come with the landscape, didn't expect that much. I kind of like the workout though, I know, I'm sick.
Now ( if you didn't before) know why they have Chiros in this world!
They can't get your Goat if you don't tell them where it is hidden.
I started going to a chiropractor when I was in the fifth grade. My dad went for a specific problem, than the whole family went for preventative reasons. I personally don't push that in my practice, I tend to treat injured people. But, at the age of 48, I've never been a bigger believer in chiropractic. Following an adjustment I feel so much better. Especially after the hard work of digging, etc.
Just so you know, I've been hands on with big projects forever, long before I bought the beach house. But I'm old now, how'd that happen. One day of serious digging, two days to recover. Oh well.
You aren't old, just in the prime! I have a favorite Chiro I see here when needed. I agree I feel much better afterwards.
They can't get your Goat if you don't tell them where it is hidden.
I used to enjoy pick and shovel work too, when I was self employed installing in ground pools. But I knew it was earning me some serious money so that made it pleasant. Similar to working on your own place, it's an investment in yourself.
saw an interview of Jodie Foster once, she said she cleaned her own house, cooked her own meals, etc. When asked why she didn'y pay someone to do that work, she responded, "Why should I pay someone else to live my life?" That's how I view it. When I don't enjoy it, than I'll stop doing it.
Ive never poured any concrete in my life, but I've found Gates concrete forms (their catalog) and their website to be fairly helpfull in putting my brain around certain situations, especially like the one you are in.
They mostly have pictures of steel forms on their website (I found by typing in "gates concrete forms" into Yahoo) but the pricipals are the same.
Overall, its looks like you got some top-notch advice from the other posts, but if this helps its all about working smarter not harder
Have fun and good luck.