framing a bay window-like cantilevered bump out in shower
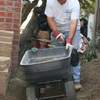
hi,
i’m trying to expand my shower (currently a 30″x30″ stall). i’d like to increase it to 32″x45″, and make it feel even bigger by pushing out an exterior wall to form an 18″x45″ bench. the bump-out would be like a bay or garden window, providing seating 18″ high. i’d like to install a glass block window in this bay as well, to let in light with some privacy.
what i’m wondering is, would it be sufficient to frame it basically like a bay window, with some brackets underneath? or, do i __need__ to extend the floor joists for additional support under the thing, or instead put in some posts to support it like a deck? the extension would be a bit heavy, including the window, cement board, tile, exterior stucco, and the framing lumber.
i got a couple bids for the work, and both contractors seemed to think the brackets would be sufficient. i’m a little paranoid right now.
i’ve got some good recommendations to tie the sheathing of the sides of the bay window into the wall studs. seems like it would add stability.
thanks for any advice,
james
Replies
jameskim
I imagine someone could engineer this thing knowing all the weights added and come up with ideas on how to make it work. It will be important to be sure of the fix to keep this from moving just a bit and cracking both the stucco and the tile joints. I think I would feel more confident with keeping the support part of the existing structure rather than posting below. Treating the tie back of the sheeting more like a box beam might be the simplest answer if there's plumbing/heating/electrical below in the joist cavities that inhibit running new cantelevered joists well back into the structure. Brackets only below? I like that one the least.
Interesting project, make sure you fill in the blanks once a decision is made.
I'm thinking this needs to be engineered. You're talking about A LOT of weight,with tile shower, glass blocks, and stucco, and any motion at all in the supports will fracture the tile and cause serious leaks.
I also wonder about the wisdom of doing this from a insulation point of view. You don't say where you are, but if it's some place cold then it will be hard to insulate this bump-out adequately.
Extending floor joists
Extending the floor joists is the way to go. Sister them with the same size joists inside for 4' minimum and then extend outside for a 2' maximum.
No brackets, that's the worst thing to do.
I like to add a bit in favor of brackets, but with changes in your plan in mind. First, brackets, made with PT 4x4 minimum, would be a good way to support the weight as long as they are attached to the addition and the weight bearing points in proper way. This means both points of attachments must be to the structural parts of the addition and the house. Also these points of attachments must be protected so that any point of water entry is eliminated. This means planned and thoughtful ways and means of flashing.
As long as you can get the drawn and described plans of brackets and flashing, and verifying the work done (if you can't be at home to verify, ask for step by step photos of the work done - make this condition of the payment), then I don't see any problem with using brackets.
Now you may not like my next comment. Instead of tying the addition to the house with stucco, consider lighter siding material such as cedar T&G stained to match the stucco. Instead of glass blocks, which are not insulated, consider having a frosted glass double pane window made. If you can fit half of sliding glass door, you can even have one with argon gas in it, and probably cheaper.
Whatever happens, don't rely on caulk for flashing details for the addition roof or the window. Having said that, I have used urethane and polymer caulk (such as Quad) to connect the joint between building materials and glass, but in each case the bottom had positive drain not relying on the caulk. The roof flashing must be cut into the siding, not just nailed to the siding and caulked. Search for diagrams of how chimney and sidings are flashed so that water drains over the flashing and you'll get a general idea of it. This will give you better position to judge the bids. Hope it helps.
hey k1c, thanks for the advice. i was wondering if i could ping a few particular questions off of you (or anyone else reading)?
1) how does a PT 4x4 compare with redwood 4x4?
2) at a 45degree angle, the brackets would hit at the union of the 2x6 T&G subfloor and the 2x6 rim joist. would it improve the connection to install a ledger board at the point the where the bottom of the brackets hit the house?
3) any metal connectors needed on the bracket?
4) the attached image shows a few different types of brackets. is the extra material on the "knee brace" decorative, or does it improve the strength?
5) the stucco has to be broken for the addition, any advice on tucking building paper or metal flashing under the existing stucco? the old paper will be a bit torn up, and hard to get under.
i've been thinking about ways of lightening the load. the glass blocks did weigh a ton. i think we're willing to go with an acrylic block window, which is pretty light. not sure about how an actual glass window would look, need to think about that. :-) for the tile underlayment, i'm looking into kerdi-board, instead of cement board. it's very light, and i was planning a kerdi shower anyway.
thanks!
james
If you use a bracket you want one with a straight diagonal, not curved like in your picture. Those in the picture are mostly decorative -- not designed to carry much load.
Whatever wood you use should be well-seasoned. If you use either new treated or new redwood the shrinkage will result in sag within a year.
James.
While I still don't sign on to the angle bracket, I think I should suggest you take a look at the way timberframers use these to hold timbers square. They are let in and pinned to resist slide, pullout and racking. The connections are VERY important.
Your not building a tank here...
Just a thought here....this is 3' x 18" +/- ??? while there is weight involved, it is a dead load. Personally? I would cantilever 4 joists & be done with it. Why wonder if a bracket will work, fit, aesthetically work, be seasoned, etc, etc. Put in (4) 2 x 10's/8's insulate, build your walls, and don't look back, and know it will hold. Cantilver 1:2 Everything else seems to be an easier way out, WITH a chance of failure or lots of overkill, which in the long run, makes you wonder why not just go to the cantilever? Remember it's a shower stall, not a gymnasium, and you're bumping out basically a seat.
I agree on the not building a tank. "Extend the floor joists" Cantilever joists are the easiest, 2/1 ratio, do you have the access and room to insert>
"or instead put in some posts to support it like a deck?" Much different engineering than a deck, plus you must deal with foundation codes. A deck is a single plane structure and to some extent can hinge somewhat from the house. In your case that would be the exact issue you are trying to isolate.
In absence of extended joists, sufficient transfer of sheer, lateral and vertical loads could be designed through a combination of appropriately sized brackets, sheer box walls and other load transferring techniques, provided the loads are transferred to structures' capable of supporting them. For instance, you can build the strongest bracket you want but it is only as strong as the attachment method's ability to transfer load to structure that can withstand the size and direction of the loads. Often this is an area where under engineered solutions are the real cause of blame for a brackets failure and many have almost no real value from the start. While you are not building a tank, it is not a flower box either.,
As far as walls, they are not designed to simply hang loads off of either. I would like to see perpendicular interior sheer walls that would counteract the loads, assist in keeping the walls in column, and aid in transferring and dispersing the load to the main structure of the house. (existing walls might be entirely sufficient depending on placement)
cantilever floor joists
thanks for all the advice, guys. i was wondering if i could get a little extra advice on cantilvering the floor joists. i was trying to avoid this because i'd run into some plumbing below, and working in the space seemed awkward, but looks like it's the right thing to do.
attached is a drawing of the bathroom layout. i added a purple rectangle to show the existing floor joists. the house is 50 years old, the floor joists are 4x6 spaced 4' o.c., with piers (i didn't count or measure the pier spacing).
the shower inside dimension is 45", with 2x4 walls on either side, i get a box bumpout that is 52" wide. i was thinking that i would use double 2x6 floor joists, simpson hangers off the existing 4x6 joist. the existing 4x6 is actually 5-3/8", which i think is a little shorter than today's 2x6's, so i would have to rip 1/8" off the 2x6's to be able to get them to slide in the rectangular opening i'd have to cut in the existing rim joist. i've got a concrete foundation, with a 2x6 mudsill, then a 2x6 rim joist, 2x6 T&G subfloor.
the left shower wall has my plumbing running through it, which presents a bit of a problem if trying to run the new floor joists under it. i was thinking i would run the new floor joists a 2" to the left of the shower wall, which would give me an extra thick exterior wall on the bumpout (not shown in figure). that would make my spacing a bit wider than 16" o.c. also on the right side of the shower, i've got a pony wall, and i can drop the last (bottom in picture) vertical stud below the subfloor and attach it to the new floor joist.
if i use double 2x6's, the span from foundation to joist is 4', and the cantilever is only 18". is that enough overdesign margin? that meets the 2:1 cantilever ratio also.
i'm assuming i toe-nail the remaining rim joist blocking to the new floor joists (green) that i add. perhaps there's some simpson bracket for that as well?
i'm planning on ripping up the 2x6 T&G subfloor in this area, to make life easier. it's got some dryrot that needs replacing, and my crawl space is very much a "crawl" space. i'd like to replace with 3/4" ply, and then a layer of 1/2" over the entire bathroom subfloor (followed by schluter ditra). to get the top of the 3/4" ply to be flush with the existing 2x6 subfloor, i was thinking i would add "lot's" of blocking (a few shown in orange) between the new (green) joists, and this blocking would be raised up enough to bridge the gap.
i found some diagrams of bump out with cantilevered walls without extending floor joists in
Graphic guide to frame construction: details for builders and designers
By Rob Thallon (pictures attached). my bump out is smaller than the listed dimensions, but i have some issue of loading. i replaced the glass block window with acrylic, but i still would like to stick with stucco siding, and i will be tiling the inside also. i was planning (until yesterday), to extend the side sheathing inside the bathroom (along the shower walls), and also to add 4 brackets below.
am i crazy?
Thanks for coming back...........
and providing those drawings. Excellent way of explanation-way easier to see than trying to interpret words.
Nice work by Thallon also-shows quite well the "box beam" way to support the load.
If you do the cantelever, the boxing back to the house frame.............I think it'll hold up the brackets you might install.
After hearing about the existing frame, I'm almost more concerned now with the possible flex in the 2x6 subfloor...............but if glued and screwed 1/2" on top of the sub, I don't believe you'll have any problems.
Matter of fact-if you excavate some of that crawl, I'd go down there in a tornado.
Best of luck.
sorry for the long hiatus
sorry, for the long break in the thread. had some issues to deal with.
question about adding another 1/2" ply on top of the current subfloor. i should "glue" in addition to screwing? does the gluing prevent any sort of expansion that the ply and underlying subfloor would want to do in different directions?
btw, i'm thinking it'd be nice to have a framing nailer. it's a pain getting the wood not to move when toe-nailing, plus i like tools. i don't care about tool capacity, so i think i'd get a stick nail gun. but, i'm curious about nail lengths. i see a lot of call for 10d 1-1/2" nails, but it seems a lot of nail guns don't support nails that short, and people use 2+" nails instead. does it matter?
thanks!
james
james
The couple times I've overlayed a board floor (1x6 t&g diagonals) for tile I've glued and screwed the plywood after screwing the boards to the joists. I have not had a problem nor really gave much thought of independant movement. The idea was to thcken the floor, make it as one. With tile you don't want ANY movement. I certainly could be mistaken.
4d are 1-1/2
10's are more like 3+" long.
I have a framing nailer that handles 8's-2-1/2" (and I presume 6's) @ 2", up to 12's 3-1/4". Pretty utilitarian gun for general framing. The guns tend to overdrive (unless you get something more modern than my antiques which will have depth of drive adjustment) The overdrive can make a 16 out of a 12 pretty easily.
thanks, calvin.
seemed like the simpson catalog references 10d 1-1/2" nails quite a bit. same diameter as a 10d, but shorter. i suppose, unless you're nailing into the 1-1/2" dimension of a 2x4, it's okay to use the longer nail? any recommendation on a particular adhesive?
http://www.strongtie.com/products/connectors/nails.asp
http://www.strongtie.com/products/connectors/LUS-HUS.asp
http://www.strongtie.com/products/connectors/hangertables/face_ss-df1.asp
James
Joist hanger nails come short with the same shank diam. as the longer framing nails. Shear strength. Some of simpsons hardware is spec'd for longer nails - beam hangers for example. Either simpson or other hanger manufacturers stamp the nail recommendation on the hardware. Some of the hangers are set up for a toenail application, so the longer nail becomes more necessary.
Nothing beats PL Premium. It seems to glue pretty permanently anything to anything. CAUTION: protect your surroundings from oooze out. Comes big tube and small and both big box stores seem to carry it. Pity the next guy that tries to tear out your work.
Those are "Special Nails" --
Those are "Special Nails" -- hanger nails. Readily available even at HD, if you know where to look. Not commonly available at the corner HW store, though (if there is such a thing anymore). It's OK to use longer nails if they don't poke through too much -- generally you want a nail that will make use of whatever thickness you have, but not project much beyond (ugly, and a hazard to folks working in the area).
DO NOT use roofing nails -- they are not rated for the loads a hanger could put on them.
How did it turn out?
Hi - We have the same idea and wanted to know how your shower with the bump out worked. Please let us know if you have any tips and we would love to see some pictures.
THANKS!!!!