I am wanting to insulate and frame my basement walls to finish. My basement walls are cinder block and out of plumb about 1 1/4” leaning in at the top. The issue of a moving foundation has been mitigated. I was intending on using ridged foam glued to the cinder block and framing my walls tight against the foam. In order to do that I was going to use 2×6 studs and rip each one at an angle so that my framed wall is plumb. I don’t want an air gap between my insulation and framing and figured cutting the studs would be easier than trying to taper the foam in some way So my question is is the air gap as big of an issue as I’m thinking and is there a better solution to my problem?
Discussion Forum
Discussion Forum
Up Next
Video Shorts
Featured Story
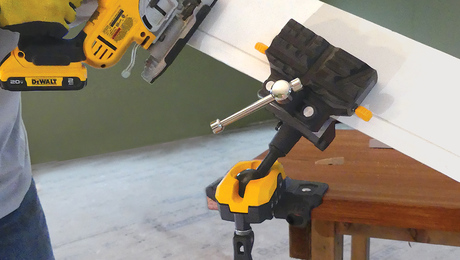
The IQ Vise has angled jaws, a simple locking mechanism, and solid holding power.
Featured Video
SawStop's Portable Tablesaw is Bigger and Better Than BeforeHighlights
"I have learned so much thanks to the searchable articles on the FHB website. I can confidently say that I expect to be a life-long subscriber." - M.K.
Fine Homebuilding Magazine
- Home Group
- Antique Trader
- Arts & Crafts Homes
- Bank Note Reporter
- Cabin Life
- Cuisine at Home
- Fine Gardening
- Fine Woodworking
- Green Building Advisor
- Garden Gate
- Horticulture
- Keep Craft Alive
- Log Home Living
- Military Trader/Vehicles
- Numismatic News
- Numismaster
- Old Cars Weekly
- Old House Journal
- Period Homes
- Popular Woodworking
- Script
- ShopNotes
- Sports Collectors Digest
- Threads
- Timber Home Living
- Traditional Building
- Woodsmith
- World Coin News
- Writer's Digest
Replies
Do you need 2X6 studs in a basement? I guess with the "out of plumb" that provides you with enough extra material to handle the taper. At the same time, getting your boards ripped and flush to the foam while keeping the wall plumb feels hard. And I'm guessing the 1-1/4 isn't "uniform" and varies around the perimeter.
I might consider simply running 2X4 studs true vertical inset far enough from the wall so that they're tight at the top at your "worst" condition and filling in the gaps between the studs and the wall with expandable foam. I'd then pack a bit more insulation into the walls and tolerate the insulation been in a bit over-compressed towards the top (or perhaps a slight gap at the bottom). It's a basement so you're going to have natural insulation from the earth to some extent. Caveat - I'm not an expert - that's just what I would do.
2x4 should be plenty. If you want more insulation in addition to the foam board panels you plan to use, fill the cavity with rock wool.
The important thing to do, however, is make sure you pay attention to fire blocking.
the cavity behind the block wall needs to be separated off to prevent hot fire gasses from spreading, at least every 10 feet along the wall, and at the top, to separate the cavity in the wall from those between floor joists above, and from interior of walls above. (including around pipes, wires and hvac ducts)
Thanks for the responses. Yes the 2x6 was mostly to have enough lumber for fastening at the top after ripping the boards not for added room for insulation. But I agree the uniformness or lack there of in the cinder block would be too much to get that tight of fit anyway. The insulation is mostly for concern of preventing condensation. I like the idea of running my wall plumb and filling the gap toward the bottoms with spray foam or rock wool.
Wanted to add another question about insulation but maybe should start another thread. Part of the remediation for the failing foundation was fastening a ledger to the bottom of the floor joists tight to the cinder block wall to prevent further lateral movement. From what I understand, when finishing a basement the ridged foam is to act as a barrier between a warmed conditioned space and a cold cinderblock wall to prevent condensation. Any thoughts on how I can insulate or prevent moisture/rot from the ledger in direct contact with the cinderblock wall. Removing and replacing the ledger to add something is definitely an option as the person who installed the ledger did so poorly and should be redone anyway
Put flashing tape on the back of the ledger so it doesn't wick water from the masonry.
I want to guess you are talking about rigid foam board, not boards with ridges. ( I suspect an out-of control spell checker)
The joists and rim joists look like they are directly supported by the block wall. The ledger should be treated as an extension of these elements.
The concrete blocks will wick some water from the ground, but also allow air to carry some of this water away from the part of the wall above the ground level. The bottom course of block will have a different moisture and temperature situation than the top course.
If it was my house, I would use the foam board on the wall, and carry it below and around the ledger, and apply a similar treatment to the rim joist, and the top of the wall and ledger to continue the seal and insulation from the rim joist to the inside of the ledger board. (using foam from a pro gun to seal the foam to the joists to stop air flow.)
The goal is to allow the rim joist and ends of the joists, as well as the ledger, all of which are in contact with the top of the block wall, to exchange air and moisture with the outside, while preventing interior air from reaching these surfaces and having heating season moisture condense at the surface. Sealing of the air flow and insulation will also improve comfort and reduce heating bills.
The use of foam boards to insulate basement walls is a mixed bag. You can get good R values and with care for sealing, get pretty good air blocking and vapor control. But if you plan for more insulation, the vapor control of the foam is on the wrong side of the insulation during the heating season, so you want to make sure the R value sandwich keeps the temperature at the inside of the foam above the dew point. You want to make sure you avoid a second vapor barrier inside the wall assembly, to let any moisture inside the wall inside your foam board to exit to the inside of the basement.
I did similar and checked these for leaks by turning on the dryer and exhaust fans on a cold day and checking for leaks by temperature and feeling for the draft. (then sealing these up whenever identified)
Then for the wall framing, you could use a treated bottom plate, and a top plate for the wall that matches the studs. The top plate would be separated from the ledger by the rigid insulation board.
All this needs to consider your heating zone and local codes.
This guide is provided for basement finishing where I live.
https://www.fairfaxcounty.gov/landdevelopment/sites/landdevelopment/files/assets/documents/pdf/publications/basement-details.pdf
In my humble opinion I would advise against ripping the studs. You are only talking about loosing 1.25". That is very little space in the overall scheme of things. Besides I like the idea that air can flow to a certain extent behind the studs so if there is any moisture it's not confined to one stud cavity. Personally I would also skip the foam. Basic basement insulation is R-10, to 15 for the far north. A 2x4 wall meets that. I'd use mineral wool because of its fire blocking attributes and it's paper free. If you are really designing something to last and be mold free forever the exterior basement walls better be well waterproofed and drainage tight, or bust up the floor on the inside and run a drain there.
I did a bit more research and this site says that it is important to construct the stud walls 1-2 inches AWAY from the foundation walls. Is that typical?
https://www.hgtv.com/design/remodel/interior-remodel/finishing-basement-walls
They explain the logic early.
Separation of untreated framing lumber from a concrete wall.
But not all installations will need or want this.
If you have more basement than you need space, this is an option, but it would come with a need for fire blocking to break up the space behind the wall.