*
This is a freestanding stairway I built in my shop earlier this year. Normally I haul my stairs to the jobsite in one piece. This one is the largest stairs and most expensive stairs I have ever built. It turns 180 degrees and had a floor to floor height of 153 inches. I had to build it in my shop, disassemble it and reassemble on the jobsite. The outside stringer is 29 feet long. It is made of ten 1/4 inch thick solid laminates of poplar that were scarfjointed to make the 29 foot long laminates in one length and of course the joints were staggered. It has poplar risers and stringers, pecan treads, mahogany newels and railing. It is freestanding and has had 20 people on it for a load test that it passed. This stairway went into the home of the person who designed and wrote the “Windows” program for Bill Gates.
Discussion Forum
Discussion Forum
Up Next
Video Shorts
Featured Story
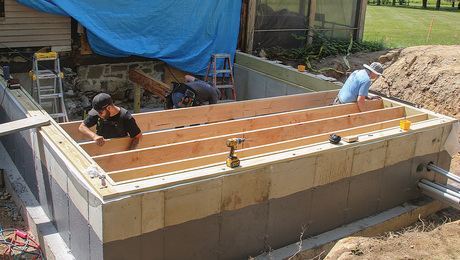
Framing the floor inside a crawlspace foundation keeps a gable-end addition close to grade.
Featured Video
How to Install Cable Rail Around Wood-Post CornersHighlights
"I have learned so much thanks to the searchable articles on the FHB website. I can confidently say that I expect to be a life-long subscriber." - M.K.
Fine Homebuilding Magazine
- Home Group
- Antique Trader
- Arts & Crafts Homes
- Bank Note Reporter
- Cabin Life
- Cuisine at Home
- Fine Gardening
- Fine Woodworking
- Green Building Advisor
- Garden Gate
- Horticulture
- Keep Craft Alive
- Log Home Living
- Military Trader/Vehicles
- Numismatic News
- Numismaster
- Old Cars Weekly
- Old House Journal
- Period Homes
- Popular Woodworking
- Script
- ShopNotes
- Sports Collectors Digest
- Threads
- Timber Home Living
- Traditional Building
- Woodsmith
- World Coin News
- Writer's Digest
Replies
*
more views:
*more views
*more views
*more views
*more views
*This is the same stairs assembled in my shop. It is a long download
*This is the inside stringer after it was removed from its glue up, cut and mitered
*stringer forms
*assembled in my shop
*last view looking down. Poor picture, stairs is all wrapped in paper
*Stan,Awesome work as usual, did that inside stringer spring much when you took it of the rack?
*Stan, this is an eyecatcher of a project, how long did the entire job take. Can you in a nutshell explain how you fastened the stringers at the top header to be able to take the load? I inbed a steel weldment(2 feet long section or more) into the stringers and bolt it to the LVL header. This works great but it sure adds to the headache list.
*Allen, I can't speak for Stan but mine spring back all most nothing,the key is to use enough plys. I use anywhere from 12 to 25 plys depending on thickness. The skin is usually 1/8 and the core plys 3/16, a real tight radius may use 3/32 plys through out, hence the 25 plys. Glue choice also determines springback.
*Stan- absolutley beautiful-Beyond my comprehension as to how you guys figure out the tread width on the inside radius,or how you match the inside to the outside.As I said before, I would love to watch this process from start to finish. You should make and sell a video. "a step above the rest" Bob
*Allen,Armin,Pro, thanks for the compliments. This stairs is nothing more than a few more steps, no pun. Allen: Like Armin said on the springback, harldy none. I take it off the bending forms to rabbet miter the stringers, and drill all the pocket screws. Then I place the stringers right back in the forms and start building from the top down, stripping the forms as I go. This assures absolutely no springback as everything is holding itself as the forms are being gradually stripped away from it as I continue adding treads and risers.Armin: This project started last September, and I worked on it steady for about 2 months, then I disassmbled it and reassembled it on the jobsite. It took around 3 1/2 months for me to build it. I had only minimal help in the shop, and that was on the glue up days. It took three people to wrestle those 29 foot laminates around the forms. I had channel irons cantilevered out of the second floor system going down inside the stairway. I also had channel irons coming up out of the first floor. It ended up very stout, as we put 20 people on it scattered on every tread. Pro: The math for circular work isnt really that difficult. I have seen all your decks with all the various landings etc. To me, those are just as hard, if not harder to lay out. I personally find it much easier to layout a circular stairway than an l-shaped stairs with two straight sections.
*Armin: I didnt quite finish the answer to your question how I fastened the stringers at the top. This stairs had huge 7.25 inch Enkeboll newels. I had these newels internally bolted to the second floor, and the stringers were mortised into the newels. The channel irons were used as just a convenient way of overkilling the structural integrity of this stairway. I had a perfect situation where I could cantilever them out of the floor system.
*Stan, 31/2 months, man you did good. Do you prefit the rail and fittings in the shop or do you do all of that on site? Does this include the finishing or do you sub that out. To my knowledge there are not many who use steel in the stair system for support, I think it's a great idea and use it where ever possible, in my opinion there is no such thing as overkill when it comes to supporting a free standing unit.
*Armin: I had the volutes attached in the shop. I prefit the goosenecks. I do not ever put the finish on a stairway. As far as the steel, this was only the second freestander that had steel in it. But as particular as these clients are, I overkilled for an extra insurance policy. When I saw the owner have 20 people get on the stairway and all bounce up and down, I was glad there was steel in it. He wanted this thing to be able to load elephants.
*Stan,That one pic of the stringer looked like a dragon tail. Also, why were the first few treads so short on the outside stringer, or was that an illusion?Rick Louquet
*Rick: The first four treads were straight and had an 11 inch run. The stairs then went circular for 180 degrees and then the top four treads were also straight with an 11 inch run. The outside tread width on the curved section was around 29 inches if I remember correctly. I personally wanted to make the whole stairs circular. I do not like the change of pitch that the stringers and railing have to make when going from straight to curved.
*Wow! Awesome work. I'm glad to see some of that fantastically rich microsoft money is going to a good cause in the beauty you produce. At least that guy has good taste.Mary
*Mary: Thanks.
*WOW $$$$$$$$$$$$ incredible job. Really consider doing a video. I have video editing software/card and produce a low budget promotional video. Do it yourself or send me enough video and I'll put it together for you. I Want To Watch This Being Done.
*Dale: I appreciate the compliment. Thanks
*What about that video???
*Dale, I made a vidio once, turned out pretty good, sent it to a friend to have it cleaned up and copies made,It was destroyed in the mail. The darn thing took so much time to make I didn't have the ambition to do another one. The worst part about it my client and her 3 pretty daughters posed on the finished product.
*Dale: I am just a one man stairshop. I am turning away work now as it is without advertising my services. A video would just probably cause me to have to turn down even more work. Thanks for the offer anyway.
*Stan, I might have ask you this before but do you bend and shape your own rail? How 'bout your newels?
*Allen: That particular stairway had Enkeboll railing, balusters and newels. I do farm out custom made newels on occasion. The rail in that stairway had 13 laminates and I glued it up in three different sessions. I usually glue up bending rail for all my stairways as there are so many profiles available. I have on occasion had to shape the rail profile, but I try to steer clear of those jobs.
*A naive question from a relative newbie: Where do you get your laminates? Do you mill them yourself? Is this something I would be doing with my little Makita thickness planer?
*Anthony: I mill down 1 x 12s to the thickness I need. This depends on the radius of the stairs and the desired thickness of the stringer. You could mill these dwon with your thickness planer. I happen to have one that I can run 20 inch wide stuff through. Most of my stairs have 11.25 inch stringers, but occasionally the circumstance calls for say a 16 wide stringer. I just glue up some 1xs to the desired width and mill them down. This particular stairs was freestanding and I also made sure that the stringers had every laminate out od solid wood. Since the outside stringer was 29 feet long, I also scarf jointed the laminates on their ends. This made for a real fun glue up wrestling those long laminates into the bending forms.
*This is the freestanding stairs as it was being formed.
*Stan, do you resaw the stock first or do you mill a full 3/4 board down to the laminate thickness? What kind of wood do you use for the core and what kind of glue do you use. ?
*Armin: On this particular stairway, I milled down 1x12 poplar to 5/16 inch thickness. I then scarf jointed the end joints and staggered these joints. I use titebond glue to glue the laminates together. This whole stringer was solid poplar clear through. It is a freestanding stairway and I wanted it as solid as I knew how to make it. Actually, each stringer consists of the notched stringer for the treads and risers plus another full width support stringer. Each stringer had ten laminates for a total thickness of 2.5 inches.
*Stan, you mentioned scarfe jointing the ends of each laminate together, and here comes the probable 'really' silly question, but how do you get a really good accurate matched scarfe joints? Circular saw comes to mind (45 degrees)?BTW: Brilliant job as usual, it takes some tenacity to take on some of your jobs!
*Francis: I have a jig that guides my router to cut my scarf joints. I usually cut an 8:1 joint meaning the width of the glued area is 8 times the thickness of the laminate. The laminates in this case were 5/16 of an inch in thickness, and the actual lap was 2 1/2 inches. This makes a very strong joint, much more than if it was just a 45 degree joint. A 45 degree joint on a 5/16 laminate is just a hair over 7/16 for the glue joint. I have also hand planed these joints and even belt sanded them with success. Whichever way I have cut these, I just put some clamping cauls over the joint and glue them up over night. One has to sight or use a long straight edge to assure that the glued laminate is straight.
*Stan, do you ever have a problem with cold creep using titebond. My earler stairs used titebond and after a year the laminates would show slight ridges or steps, I switched to a two part resin powder mix about 15 years ago and never had a problem. I keep a cutoff section of every laminated handrail I build, name and date the piece. So far not one of them has shown any sign of problems, the titebods rails stabilize after time but once the glue ridges are in the finished rail short of sanding everything down there is not much you can do. I do still use titebond for non stressed joints.
*Armin: I have never had any problem so far. I have considered trying a different glue to minimize springback. I will be gluing up one shortly and I think I will try the resin powder mix. Do you notice less springback with this glue? I assume it sets glass hard also.
*Stan, yes I feel there is less spring back, its very noticable on tight bends of 24 in radius. It drys rock hard and sands very well, I never have to worry about that little spot of glue that doesn't show up untill after everything is stained. The plus side of using yellow glue is the wood fibers absorb the water from the glue thus making the wood more pliable. Have you ever gone back and checked your work after several years? The yellow glue problem takes a while to show up.
*I have revisited several of my stairs and have not noticed any laminate creep. I am always also looking at my tread and riser mortises to see if they are still tight.
*Stan,EXCELLENT job i'm new to the site tonight a subscriber to the mag,(2yrs.).I grew up a framer and remodeler since the mid 70's,now 5yrs. a new home construction manager.By far the most enjoyable article i've seen at FHB.
*Stan the stair meister, we are not worthy, but we have a target, and endevour to learn,thanks.
*Phil: Thanks, but there many stair meisters around here. I am still in my learning phase, and I will be the first to admit that I have a lot to learn yet. Acquiring that new knowledge keeps it interesting for me.
*Amen to that!