I want to build a new 2 stall garage in my back yard. It will sit on a floating slab with 3 courses of block on the sides and rear for grade. The concrete company that I talked to says that there is no way to pour the slab with a slope to the doors to get the water out with the concrete block. Is he correct, or should I talk to someone else.
Discussion Forum
Discussion Forum
Up Next
Video Shorts
Featured Story
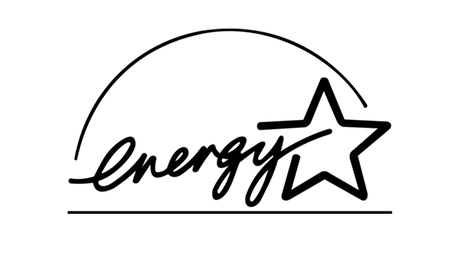
The end of this program will likely lead to higher energy bills and fewer business opportunities for the American people.
Featured Video
SawStop's Portable Tablesaw is Bigger and Better Than BeforeHighlights
"I have learned so much thanks to the searchable articles on the FHB website. I can confidently say that I expect to be a life-long subscriber." - M.K.
Fine Homebuilding Magazine
- Home Group
- Antique Trader
- Arts & Crafts Homes
- Bank Note Reporter
- Cabin Life
- Cuisine at Home
- Fine Gardening
- Fine Woodworking
- Green Building Advisor
- Garden Gate
- Horticulture
- Keep Craft Alive
- Log Home Living
- Military Trader/Vehicles
- Numismatic News
- Numismaster
- Old Cars Weekly
- Old House Journal
- Period Homes
- Popular Woodworking
- Script
- ShopNotes
- Sports Collectors Digest
- Threads
- Timber Home Living
- Traditional Building
- Woodsmith
- World Coin News
- Writer's Digest
Replies
talk to somebody who knows what they are doing. It is typical to slope slabs for drainage to garage doors.
Welcome to the
Taunton University of Knowledge FHB Campus at Breaktime.
where ...
Excellence is its own reward!
Kind of what I thought, thank you.
Just curious as to one aspect of this; when the op says a "floating slab" is it a case where the slab is being poured before the block? I agree, pretty much anyone who's ever held a trowel should be able to pitch a garage floor. I generally go a little less than Mike posted, around 3" in 24'. However, if the op is in an area (no profile info) where they can use a slab on grade, or a slab with a 12" haunch or some such, it WOULD be a b!@!ch for the mason to lay up 3 courses of block with pitch on the slab.....If that were the case, I'd be thinking along the lines of a footing, w/ block on top of that, then the pitched floor inside. I also put a 1" lip inside for the garage door to close in front of, eliminates wind-blown rain getting under the gasket.
Bing
I saw that too on the floating slab comment, but I chose to interpret it differently . I think he miss-used the term and that he is using block wall on footings, then pouring the slab over that with infill. Could be I'm wrong. If I read that wrong, then a totally sloped slab interpretation could explain why the foundation contractor gave him grief over the idea.
Welcome to the Taunton University of Knowledge FHB Campus at Breaktime. where ... Excellence is its own reward!
I think you read it wrong. What the OP was describing happens frequently in construction around here. Floating slabs are very common. Many times you have to use block on the sidewalls.
You pour the slab and then lay block where necessary, usually in steps. That's why almost all of the garages with that scenario have center sloping floor drains.
I'm familiar with the method. I've done several that way.But I had thought he said something about a sloped lot making three courses necessary, which is where I got the inmpression he was building up to the slab.But I guess he could as easily have been cutting back into the slope. I would have to review his OP, but I gotta get to work now.
Welcome to the Taunton University of Knowledge FHB Campus at Breaktime. where ... Excellence is its own reward!
Around here, a " floating slab" garage means the one with the 12" thick edges extending 24" in to the slab and then the floor area becomes 5" or 6" thick. That method is used on small garages or huge warehouses.
As I read some of the comments on BT, I can see that the term does not mean the same to everyone. Some people ask about the concept as if it just came down from Mars, so apparently it's not commonly used in some other areas.
These can't be used in garages that connect to a home with frostwalls or a basement because the slab literally floats up and down with the frost. Later building codes call for insulation under the slabs to limit any movement.
I'm prety sure he was talking about the type I'm used to.....at least that's the way I interpreted what he said.
i'll leave it to him to clarify rather than arguing because I don't know. I just figured he mis-used the term
Welcome to the Taunton University of Knowledge FHB Campus at Breaktime. where ... Excellence is its own reward!
the block has to be level for the building to set on. but there no reason they can slope the concrete to the door. they just dont want to finish slope concrete. you could always floor drain the center too.
The IRC REQUIRES the garage slab to be sloped:
"The area of floor used for parking of automobiles shall be sloped to facilitate the movement of liquids to a drain or towards the main vehicle entry door".
Runnerguy
I wouldn't say " there's no way to do it" , but I would say it is a PITA.
Consider this: As BB said, the top of the block must be level on the three side. You can accomplish this by running the concrete along the forms on those walls level out into the floor wide enough to lay the block and then tapering the floor. This involves a lot of precise handwork. This would be my first choice though.
Another way is to cut every bottom block on a taper....or you could install a poured concrete cap leveled out on top of the sloping block (which cause problems at corners)
None of these solutions are quick or easy and will certainly cost you more.
Personally, I don't like floors sloped toward the door anyway. The runoff from the cars flows to the door and often freezes the doors to the floor, causing a lot of unnecessary door damage.
It takes me maybe an extra 5-10 minutes to form for slope at doors. The bigger work is the screeding and there is more hand finish work, less power troweling.Sounded to me like the outfit saying can't be done uses all power stuff and they are'nt interested or skilled enough to get down on it.
Welcome to the Taunton University of Knowledge FHB Campus at Breaktime. where ... Excellence is its own reward!
Sounded to me like the outfit saying can't be done uses all power stuff and they are'nt interested or skilled enough to get down on it
That's certainly a possibility! But aside from that, I think a floor sloping toward the doors in a freezing climate is a bad idea. In fact, there are areas we work where they are prohibited by local building codes.
It really doesn't matter if he uses blocks or not. You have exactly the same problem to deal with. The perimeter of the slab where the walls sit has to be level, period.
I wonder what the guy would do if somebody came to him and wanted a plain floating slab floor pitched to the door?? Would he tilt the forms toward the door so the whole building was leaning?
Edited 3/18/2009 3:38 pm ET by BoJangles
Your last sentence is what I was talking about when I said it takes me only an extra few minutes to form lower at the door. The edge stays level all around, and even at the short wall section(s) between two doors and drops about 1-1/2" at door opennings.it is not a matter of CAN be done, only of WANT to do it. I don't even see it as that hard to do.
Welcome to the Taunton University of Knowledge FHB Campus at Breaktime. where ... Excellence is its own reward!
only thing you do is pour flat and then let the bull float dig a little toward the door. no forming at all.
that works fine for a modest incline just fine
Welcome to the Taunton University of Knowledge FHB Campus at Breaktime. where ... Excellence is its own reward!
If you like flat floors as much as I do, you can shoot PT form boards into the block, and screed off a flat, but sloping floor.
Make it higher in the back, but put a slight V-shape in it, with a continuous floor drain a foot or two inside the door.
If you're not worried about flat, you can dish the floor as Piffin describes. Just make sure that the floor/door juncture is straight across -- I've seen some messes where this joint is ugly, and hard to seal, because the opening itself is dished.
AitchKay
I'd call it more of a wedge than a dish
Welcome to the Taunton University of Knowledge FHB Campus at Breaktime. where ... Excellence is its own reward!
Hey, how much slope do you like to achieve, and at what point do you think that the slope is too gentle to actually function?Obviously, a polished epoxy coat or the equivalent would help you minimize the slope, so let's assume that for this question.With my flat-but-sloped scenario, 1/8" per foot would add up to several inches of height differential.AitchKay
>Hey, how much slope do you like to achieve, and at what point do you think that the slope is too gentle to actually function?
In my 36' deep garage, I left the back half flat, and sloped the front half (18') 1" towards the door. I didn't want a large amount of slope.
Should have sloped more - 2" anyway. Snow melt off the car tends to go sideways as much as towards the door, so I wind up getting out the squeegee.
A lot probably depends on the floor finisher - mine was an experienced guy, but worked to what is probably standard practice around here. He recommended I increase the slope, but I decided to stick with 1" (I did all the prep work & helped with the pour).
Don
we pitch all our 24' garages 4" from back to front
and then we pitch the apron outside the door even more...
doors frozen in doesn't seem to be much of an issue.... i would think flat slabs would have more of a problem with thatMike Hussein Smith Rhode Island : Design / Build / Repair / Restore
doors frozen in doesn't seem to be much of an issue....
A couple of comments: We live in an area that gets lots of snow and this is definitely a problem here. You come in to the garage with a vehicle covered with snow, it melts and runs toward the doors. The doors are sealed well enough so the water from the outside doesn't run in & therefore the water from the inside doesn't run out. Soon it ends up freezing the door to the floor. When that happens, you either wreck the weatherstrip or the door when you try to open it.
In my opinion, the only way to handle that problem is to install the strip drains near the doors. That works well, especially with heated floors. I do like flat/sloped floors a lot better than center drain setups.
Last week, a lady called me in a panic with a garage door problem. It was a brand new house with a garage floor sloping toward the doors. I didn't know her, but somebody told her to call me. I arrived at the house to find one of her garage doors bent vertically in the middle where the opener arm was attached. It was reinforced, but the opener had bent it in half like a piece of tin. I commented that I had never seen one bent that bad and asked just how it happened. She proceeded to push the button for the other door as she was telling me what she did, and ripped that one in half too! Both doors had heavy bottom weatherstrips and were frozen to the floor. Obviously the force adjustment on the opener needed twinking too.
couldn't help chuckling at your storysounds like the punch line where the doctor is talking to the patient"hey, doc... it hurts when i do this !""well, don't do it"so... " how did you do tat to your garage door ?"wait ... stop !Mike Hussein Smith Rhode Island : Design / Build / Repair / Restore
"Obviously the force adjustment on the opener needed twinking too."Running in my head thru the whole storyThe brain of the guy who installed might have needed a "twnkling" too
Welcome to the Taunton University of Knowledge FHB Campus at Breaktime. where ... Excellence is its own reward!
Ideally I want the drop 1-1/2" tapering back about 8' or so which works out to about 1/8" pitch
Welcome to the Taunton University of Knowledge FHB Campus at Breaktime. where ... Excellence is its own reward!