We are constructing a large custom home in which there are several radius wall sections. The radii are of various dimension ranges. The ones causing the headscratching are those with less than 6′ diameters. The base selected is solid cherry wood and is 6″ tall with a fairly typical colonial milling. We are looking for any ideas short of making the turn with a number of small vertical cut pieces glued together in a series of joints around the radius. The trim package will be custom stained and we fear what all those joints will end up looking like. If a tool or invention is needed the project is large enough that the investment would be justified. We have already tried to create relief cuts with saw kerfs in the back of the piece. That worked great for the area of the base that is flat. The milled upper part wouldn’t make the turn at all and snapped under any force. Any ideas will be appreciated.
Discussion Forum
Discussion Forum
Up Next
Video Shorts
Featured Story
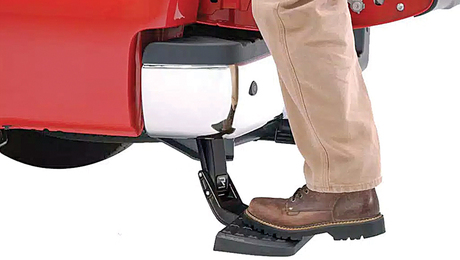
The RealTruck AMP Research Bedsteps give you easy access to your truck-bed storage.
Featured Video
SawStop's Portable Tablesaw is Bigger and Better Than BeforeHighlights
"I have learned so much thanks to the searchable articles on the FHB website. I can confidently say that I expect to be a life-long subscriber." - M.K.
Replies
Can you post a picture or sketch of the profile?
I am brand new to this message board thing but a real techy so I'll figure it out but for now here's a link to a page. The base we are using is the F2800 at the bottom of the page.
Go to http://www.ferche.com/base.htm
Kelly is this the kind of thing you are trying to achive? (click for the big
picture)
View Image
I posted this as part of a dicussion Making
curved base-caps back in March. I had asked the fellow that started that
dicsussion whether he was looking to make #1-Tight Radius Turns or #2 Large
Radius Turns and he needed Large Radius Turns so I showed him one of the techniques
we used for that but never explained the Tight Radius Turn technique. It'll
take me a little while to write it all out but I work on it and get it to you
asap.
Hopefully some other people here will have some neat techniques too.
We have already tried to create relief cuts with saw
kerfs in the back of the piece. Forget about that you are just making
firewood trying that on such a tight turn. Until later...
Profit is like oxygen,
food, water, and blood for the body; they are
not the point of life, but without
them there is no life. Jim Collins
& Jerry PorasBuilt to Last
Basically that is what we are attempting. We have about 5 different areas where we will install base, two of which will be what I would call an inside radius and the rest would be outside radii, like you picture here. I'll read the link and rest of the posting and let you know later today or tomorrow. I'll also check out at the site tonight and post what we really have to tackle.
Edited 7/15/2002 11:13:36 PM ET by Kelly
Kelly, unfortunately I don't think I have any photos of the Tight Radius Curved
Base we've done in cherry or at least I can't find them right now. The project
photo I posted above was white oak.
When you wrote "We are looking for any ideas short
of making the turn with a number of small vertical cut pieces glued together
in a series of joints around the radius." That's actually the answer
but only part of it. The very top in fact.
The lower section solid looking 1x base of the molding is made that same way
I described for the Large Radius Turns in Making
curved base-caps. We wrapped the turn with two layers of 3/8 flexible plywood
and then applied a foil back veneer to match our existing wood trim.
Unlike the drawing in the the Making
curved base-caps post on the tight turns the top base cap was not staged
or staggered. The top was level and then the whole base cap was applied.
We would take a piece of solid 8/4 cherry stock (selected for it grain agreeing
and working with the veneer we had used to cover the base) and cut it up in
to wedges like below.
View Image
We then glue them together into a blank (polyurethane so we don't
get any glue lines when it stained) as per the drawing below
View Image
We then band saw cut the outer radius and then rout our profile. Then we would
go back and band saw out the rest of the inside of the curve leaving us with
a 3/4" x 1-7/8" curved molding cap profile.
The key I think is that because the lower body looks continuous and solid because
it was done in veneer the joints in the molding cap are noticeable unless you
look for them.
Looking at the profile you're working with that little chevron at the base
of the ogee cap means you have to careful to make sure you left enough material
at the bottom to overlap the base. If anything let the cap be slightly proud
and lightly sand it back flush to the veneer.
View Image
Doing this is not at all easy. It take a while to get the hang
of it. It's a lot like fine furniture making but it is a unique detail that
people notice. You also might want to build the corner assemblies around a form
and then install them as a single unit and then fair the wall to fit above it.
That's what one of my guys did on one project and he prefers doing it that way
now. It let him do all that forming, fitting, and shaping standing up at a bench
where it a lot easier.
I was just sort of wondering along the lines of the topic that
I started the other day Pricing
for ‘perceived value’ just how do you value and price something
like this? This is just the kind of work that I have been saying calls out for
premium pricing.
Profit is like oxygen,
food, water, and blood for the body; they are
not the point of life, but without
them there is no life. —Jim Collins
& Jerry Poras—Built to Last
Kelly,
We have done curved ahrdwood base with the steaming technique and it worked pretty well. We built a form to the shape of each curve and used clamps to attach the base when steamed to the proper flacidity. (is that a word?)
Yup Roger it's a word and I even used it myself once talking about steaming and my guys made fun of me for it. It's spelled flaccidity though (spell checker here, I would have spelled it wrong too). Anyway what did you use to steam your trim? We've found that while cherry is steam bendable it cetainly not the best one for it. What do like you as far as steaming?
Profit is like oxygen,
food, water, and blood for the body; they are
not the point of life, but without
them there is no life. —Jim Collins
& Jerry Poras—Built to Last
You mentioned that you have several radii to make, how many and approx. what is the radius?
We have done curved base by making jigs to bend the pieces in. If you have like radii and not to many it may be feasible but if you have to many different radiuses than you may not want to spend the time doing it, we have done it for entire houses and you don't see any splices in the wood because it is laminated as opposed to segmented. I admire Mr. Hayes ability to show you some pics, my woodworking skills are far better then my computer, but if your interested I can explain better and probably get some pics for you.
Doug
Doug I'm certainly intersted. We're always looking for altenative or better techniques and methods. You should call me Jerry or Jerrald too.
Profit is like oxygen,
food, water, and blood for the body; they are
not the point of life, but without
them there is no life. —Jim Collins
& Jerry Poras—Built to Last
Jerry
Just giving some respect, am always interested in what you have to say,
In a quick explanation, if we had a piece of base or any other curved mouldings, that had to be applied like base, knowing the radius we would swing an arc in a piece of ply or MDF, make a copy of that and then if the base for instance was say 5" high, and using 3/4"MDF and two arcs=1 1/2" then cut plywood spacers about 4" long and nail and glue them making a sort of curved looking ladder, you can make a concave or convex depending on which you need and adding or subtracting the thickness of the base make the other curved piece to complement the one already made you have a jig, then depending on the radius you resaw your wood to a thickness that will bend cold, we never use steam, for the example given I would cut wood about 5 1/2" tall, liberally glue up the laminates and put in the jig and clamp the hell out of it, the reason to oversize the wood is so that when you take it out of the jig you can joint it to size. Then route or shape to what ever profile you desire.
I am terrible at explaining something, its the artist in me, left side right side brain thing, anyhow that's the excuse I've become accustomed to using.
I can try to snap some digitals of one in the shop but that will require me to learn how to run the damn camera and then load onto the net. I think that you probably get what I'm saying you seem to have done most of the stuff that we do in our shop and then some. I'm not sure that others will follow it though.
It is time consuming but we work in high end homes and usually money is not as big as a concern as results.
If what I've tried to explain is not clear, and I'm not sure it is even to me, I can try something different.
Doug
I went by the site tonight after I had to play dad with my little boy for a while and here's what we have. Two (inside and outside) 4', Two (inside and outside) 3', Two (inside and outside) 18", and Two (outside only) 20" radii.
Kelly
Read my post to Jerry, as I said I cant explain very well if your in Iowa I can show you in about 1/2 hour. Anyhow I can try to get some pics and maybe that would help.
Doug
Kelly,
View Image