I am currently designing a new home with radiant heated floors via a heated slab. I want to put hardwood floors in the house. I have looked at engineered wood floors but feel like they are too hard and do not give that “springy” feel like hardwood. The house is an upscale custom home and the finishes are top of the line. Anybody have experience with hardwood on radiant floors? Any suggestions would help. The home is located in Santa Barbara, CA and the average coldest nights in winter are in the low 40s. Thanks, Larame
Discussion Forum
Discussion Forum
Up Next
Video Shorts
Featured Story
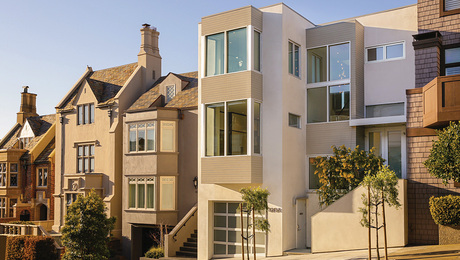
A sleek, modern redesign maximizes space and light while preserving the building's historical charm.
Featured Video
How to Install Cable Rail Around Wood-Post CornersHighlights
"I have learned so much thanks to the searchable articles on the FHB website. I can confidently say that I expect to be a life-long subscriber." - M.K.
Fine Homebuilding Magazine
- Home Group
- Antique Trader
- Arts & Crafts Homes
- Bank Note Reporter
- Cabin Life
- Cuisine at Home
- Fine Gardening
- Fine Woodworking
- Green Building Advisor
- Garden Gate
- Horticulture
- Keep Craft Alive
- Log Home Living
- Military Trader/Vehicles
- Numismatic News
- Numismaster
- Old Cars Weekly
- Old House Journal
- Period Homes
- Popular Woodworking
- Script
- ShopNotes
- Sports Collectors Digest
- Threads
- Timber Home Living
- Traditional Building
- Woodsmith
- World Coin News
- Writer's Digest
Replies
Here is what worked well for me.
3/4" CDX plywood was glued to the slab, then 2.25" wide longstrip hardwood flooring was put atop the ply, using 1-3/4" flooring cleats, driven with an air-assisted flooring nailer. Total thickness build atop the slab was 1.5 inches.
The flooring was 3/4" solid white oak, quartersawn with some riftsawn allowed. Be sure to use a species such as this, one with demonstrably low shrinkage when seasonal changes in humidity occur.
The ply began as 4x8 sheets, and was then ripped to 2x8 sheets, and crosscut kerfed with a skilsaw on about 18" centers. The saw was set to cut a kerf about 1/2" deep. This rendered each 24 x 96 panel flexible, so as to bed well into the adhesive.
We used an adhesive product called Bostiks Best, a moisture curing polyurethane glue, that goes on with a notched trowel.
A small supply of concrete blocks, or big stones, or pails filled with water, are good to have on hand, to weight down any panels that might want to give a little curl, when gluing.
Gene, what if any provisions were made for dealing with moisture coming up thru the slab? I assume you have 6 mil below, but won't the concrete itself continue to give off moisture for a significant period after the pour? I know here in the Seattle area it's said to be years, whereas in San Diego it's much less.
I have a house coming up where the owner wants bamboo flooring throughout the first floor and the designer wants to use a slab on grade detail with RFH because of difficult excavation conditions at the site. They've been talking to me about Warmboard, which I have no experience with... aside from my deep suspicions of everything new.
No provisions, David. The slab was poured atop a prepared bed of compacted gravel fill, with 2 inches of rigid foam directly bearing on the gravel.
Poured in June, roofed over by August 1, radiant heat cooking it by October 15, we went ahead and did the glue-ply work in early November, brought in the oak, and floored it right after Thanksgiving.
No problems.
Gene, I'm curious to know where (state) that site was located? Also how thick was the slab? Has it gone thru a couple of years of use? Reason I ask is that as David mentioned, concrete takes a long time to dry and not having it bone dry will cause the hardwood to buckle at some point. Seen it happen myself. Maybe your adhesive is a moisture barrier? My test for concrete dryness is to leave a piece of 6-mil poly on the slab with a weight on it. If in two or three weeks you still have dry concrete under the poly, it should be dry enough. Also as with all hardwood, it should be acclimatized to the house for as long as you can before nailing it.BTW Larame, I have walked on our 12" slab in bare feet at -20° outside. There is something about a heated floor that gives the illusion that it is softer than a cold floor. As a result, we have decided to put tile on the slab floor. That slab holds a lot of heat, you might want to consider doing something passive, increasing the thickness, or get some solar hot water panels as we have. We pay for heat 3 months in winter tho that is mostly for domestic use. Our solar panel system ($4K) paid for itself, amortized over 8.4 years. (We planned on 17, but that was 1998 fuel prices.) Since then we have all the hot water we can use from May to October, and all of our heat in some of Dec and Apr, and some of it the rest of the winter. At the cost of fuel and you living in SB, you'd have to be rich to not include solar.
We have hardwood on the second floor with 1 1/2" sleepers 10" OC, radiant tubes snaking around the floor cutting thru the sleepers, and handmade concrete filling the spaces. (It's handmade because it was too fiddly to have a truck waiting while we filled the spaces, doesn't take that much concrete, and as it was on the second floor we would have had to have a pumper.) Even that concrete took two or three weeks to dry so that there was no moisture under the poly test sheet.
Gomer, the house is in upstate NY, Adirondack mountains region, elevation 2000 feet, probably around 7500 degree days of heating, winter lows as bad as minus 50.
Since installed, the heating system has performed through three winters, including its first, during the completion of interior construction finish and trim. T'stats were all set to only 55 or so the first winter.
No problems at all.
Is the slab predetermined as a structural element, or included specifically for floor heat?
If the latter, you should really do more research on the wide variety of light-weight or "dry" systems for RFH, versus the slab. These use one form or another of layers of aluminum in close contact with the PEX tubing and are really much more adaptive to hardwood flooring than concrete or gypcrete.
Be aware that in such a warm climate, the floor may do the job of raising the ambient temperature of the living space WITHOUT ever "feeling warm". So you'll have to have a bullet proof control strategy.
Slabs work best in a climate that is consistently cold for fairly long periods of time, as they take some time to ramp up...with an associated long time to ramp down.
The slab is predetermined as a structural element. I am not overly concerned about the floor actually feeling warm. I am more interested in the quality of heat and the lack of forced air blowing around. On another note, what types of heaters does everyone like (electric or gas or solar, types of brands)?
I take it from your post that you are a design professional, paid by your customer/client to design this home. I would suggest that you find and hire (or pay for consultation), a design professional in the field of radiant heating systems design. Additionally, you will need a professional for the air conditioning and ventilation systems. These will very likely be one in the same, but not necessarily.
For a house that is an "upscale custom home and the finishes are top of the line..", paying professionals for their expertise in design is the minimum expectation for a home that truly meets that description. Anything less fall into the McMansion category.
BTW, radiant floor heating under hardwood is common and easily designed by those that know what they're doing.
I am the homeowner. I post to the message board to get a greater amount of ideas/expertise on the question at hand. Yes, I am in the process of talking to professionals in my area. However, one person's opinion & experience is not all that I want. Possibly, by posting here, I will come upon another way to tackle the issue that yields a better and/or least expensive end product. Thank you for your concern. If you have any experience, be it good or bad, with the original question, I would love to hear about it.
You have come to a good place. I do have limited design experience in this area. I also know many that have much more. There is a website that is dedicated to steam and hot water (hydronic) heating, and of that a good portion is on radiant floor heating. There are people there that know far more than I. http://www.heatinghelp.com/ is the place to go.
The primary issue with wood flooring as a radiator, is over-heating it and subsequent drying, cracking and shrinking. The limiting design parameter is that the wood surface temperature be limited to 85 degrees. Depending on the installation method for the distribution tubing, (and the heat loss of the space) the designer can establish the required tube spacing, diameter, loop length and water supply temperature, temperature drop and control strategy. Overall heating needs and domestic hot water need should be accounted for at this time. One properly selected appliance will be more efficient and cost effective than several.
Then what are the options for installation methods? 1-imbed the tubing in the poured slab, 2-use a product like WarmBoard or RauPanel between slab and the flooring. Personally, I prefer the second method for wood floors, whether over a slab or a wood framed floor structure. The glued subfloor as posted by another is the way to go, under the RauPanels. Then you can see the tubes and avoid putting a floor nail through one and you get the most heat for the lowest temperature (the most efficient way to heat with water is at the lowest water supply temperature possibe).
I work and am most familiar with the specific design considerations in a very different environment than yours (northern IL), as do most of the people that are most familiar with these types of heating systems. In my area the additional problems with wood floors in RFH applications is limiting the surface temps limits the output and in some cases requires supplmental heat to meet worst case conditions. Probably not a concern in SoCal.
You will need details of construction, siting, floor finishes, insulation, window and shades/awnings information for a designer to work out the details.
Edited 9/15/2006 5:41 pm by Tim
Not always true Tim. For my home I got two quotes, one from people who specialize in radiant floors, and the other from a heating guy. The specialists quoted me $6K for the system not counting installation - lots of bells and whistles. The heating guy quoted me $12K. I bought the whole system for $1900 from Radiantec in Vermont. I made a few modifications to their configuration, and did the plumbing myself. Anyone can learn to solder joints, so you don't need a professional. Just some common sense, and patience. Oh yeh, you have to know how to read.I was curious about why it cost so much. When I asked them for the math on how much heat I would need to heat the place, neither could tell me. The specialists just have a formula based on the footprint. The heating guy guessed that the house would need x number of btus from what he knows about baseboard hot water. When I did the math, I found that a 50 gal (45K btu) hot water heater was all that was necessary to heat the house because it is well insulated. John Siegenthaler wrote a book on Hydronic systems and there was a little paragraph saying a hot water heater could also be used at the end of the chapter on boilers. That's where I got the idea from. The heating guy insisted that I needed a boiler. That meant that I would have to heat the radiant water to 200° plus, then cool it to 120° to use in the floor. The return water would then be lower than the recommended 180° that makes for efficient boiler working.My neighbor just built a house with radiant (Pity cause he has a huge south facing roof) and a big expensive boiler with all the mixing valves etc. Big bucks too.BTW, we were paranoid that just maybe that water heater might not be quite enough to heat the house (2400 sqft on 3 floors) so we framed in a fireplace to put in a gas unit if needed. We call it a candleplace now because my wife puts in candles. We have so much solar gain that we sometimes have to open the windows on a sunny winter afternoon, and then we decided to invest in 4 solar hot water panels on the roof because of the price of fuel. Now we hardly use any gas for heating, mostly for domestic, and we have free hot water for 8 months. Also, the specialists wanted to sell us all this fancy electronics for watching the temp. We found that we leave the thermostat on 67° all year and never touch it. Haven't for 4 years.My long winded point is that lots of professionals are like that in name only. Bucky Fuller said that the building trades are always 50 years or more behind the technology because the guys who do the work learn what they do on the job and then stick with it. I come from a long line of carpenters and contractors often looked at me like I was nuts for the way I built my own home. Lots of discussions with my dad before he died as we hashed out a better way to do things. I designed an exterior wall for my house and some years later FH had an article calling "my" design a "rainwall". If I had listened to my fellow carpenters I would have used cedar on housewrap. They came back to their jobs to deal with moisture problems from the housewrap interacting with the cedar and if they read the FH article in 2000 they started using "my" rainwall. But then the old man used to say, "Common sense, Ain't common."
I agree there are people in all trades that shame the real professionals in that trade. That cannot be avoided. You have definitely met some incompetents. Depending on the particulars of the installation, ignorant "professionals" can get away with being clueless more often than they should in hyrdonic systems.
Your post actually proves my point in your statement ".... I would have to heat the radiant water to 200° plus, then cool it to 120° to use in the floor. The return water would then be lower than the recommended 180° that makes for efficient boiler working..." is just plain, technically incorrect.
The "professional" that gave you this information is not a competent radiant floor system designer or installer. And sounds pretty weak on boilers in general. A high efficiency, modulating, condesing boiler is most efficient at coldest return temperatures possible. All hot water boilers for that matter, all other things being equal, are more efficient at lower (supply and) return water temperatures. This is simple thermodynamics. OTOH, a non-condesning boiler requires only 140 degree return water to prevent flue gas condensation and typically that would be with a 160 degree supply and a 20 degree temperature drop. A competent "boiler pro" would both know how to supply low temperature water from a high temperature boiler and how to do so without harming the boiler. They would also know that a properly selected boiler for your house would operate around 97 to 98% AFUE, where your 50 gallon water heaterprobably operates at about 67% AFUE. A professional would have explained these tradeoffs to you. Well, it sounds like you don't need it much anyways with your solar collectors. Good for you.
Real, competent specialists in this field would perform a room by room heat loss calculation to determine the size of the equipment, the amount of heat required for each space and the best way to do so as efficiently as possible. None of the people you spoke with did this or, it seems, even knew how to do this.
Edited 9/15/2006 5:47 pm by Tim
Your point is well taken Tim, but in his defense, this was about 10-11 years ago, before these new "high efficiency, modulating, condesing boiler" were on the market. I won't argue with you abut AFUE being better with the newest boilers, but I think my heater was rated at about 82% which was good at the time. Newer water heaters are already better than that now. Next time I have to replace it, I will compare. Check with me then. :)"Real, competent specialists in this field would perform a room by room heat loss calculation to determine the size of the equipment, the amount of heat required for each space and the best way to do so as efficiently as possible. None of the people you spoke with did this or, it seems, even knew how to do this."
You are so right there, but that was my point as well. When I talked about this to other people over the years, I have heard lots of stories, but the best was my next door neighbor who built his house about twenty years ago, then later added on an enclosed swimming pool for his physical therapist wife. He heated the room by wood, and then for some reason decided to see if his heating system (put in by a heating contractor) could heat both the house, and pool room (20 x36),just enough to keep pool room at 40° during the winter. His heating system was so overbuilt that it was able to keep the room at 68° even in the dead of winter without any loss of heat in the house.Again, my point is just that the *average* person is hard pressed to know if someone is actually doing the job well, and seldom knows what questions (heat loss calcs? what are they?) to ask to find out if the person is capable. Sometimes, you can do very well on your own if you are willing to take the time to learn. OTOH, few people have that time. The neighbor who just built his home with radiant I mentioned above, actually built the house, but hired the heating out to someone else. He was shocked when he compared his costs to mine, and wishes he had not been in such a hurry to get it done.