I have a customer who requires 5500 square feet of 2×6 T&G South Yellow Pine flooring installed over sleepers over steel bar joists @ 4’ O.C. The underside is exposed as well; the top is a finished product. I am concerned that fastening only ever 4’ is going to be a major appearance issue. Other than drilling and screwing through the T&G to eliminate gaps between boards I was considering a clip similar to a blind nailing deck fastener but am concerned that this may be more trouble than it’s worth. Any thoughts?
Discussion Forum
Discussion Forum
Up Next
Video Shorts
Featured Story
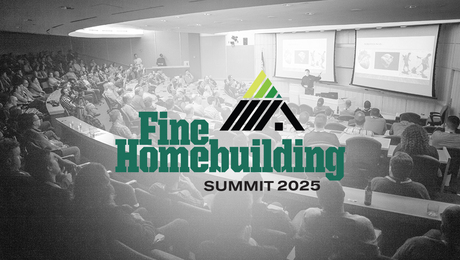
Join some of the most experienced and recognized building professionals for two days of presentations, panel discussions, networking, and more.
Featured Video
SawStop's Portable Tablesaw is Bigger and Better Than BeforeHighlights
"I have learned so much thanks to the searchable articles on the FHB website. I can confidently say that I expect to be a life-long subscriber." - M.K.
Fine Homebuilding Magazine
- Home Group
- Antique Trader
- Arts & Crafts Homes
- Bank Note Reporter
- Cabin Life
- Cuisine at Home
- Fine Gardening
- Fine Woodworking
- Green Building Advisor
- Garden Gate
- Horticulture
- Keep Craft Alive
- Log Home Living
- Military Trader/Vehicles
- Numismatic News
- Numismaster
- Old Cars Weekly
- Old House Journal
- Period Homes
- Popular Woodworking
- Script
- ShopNotes
- Sports Collectors Digest
- Threads
- Timber Home Living
- Traditional Building
- Woodsmith
- World Coin News
- Writer's Digest
Replies
I'm sure someone who knows more will come along and give a better answer but until then. When I lived up in VA centuries ago we called 2 X ^ tongue and groove garage decking and used it on spans up to 4 feet. As a matter of fact the house I lived in had it on the second floor. It sure sifted a lot sand down to the first floor though.
I have already informed the customer about “Raining Dirt”. I am not too concerned about the structural aspects of the span. I am however, very concerned about eliminating the gaps in the boards during installation?http://www.multichambernailgun.com/b2/
I have a couple of customers with houses built with 2x6 car decking floors. There is no way to make it perfectly tight but if you use straight, well-milled material it should be possible to get a very nice job. I would probably toe-screw it with #8 x 3 screws. You need to make sure your customer doesn't have unrealistic expectations.
Don't know about SYP but I have laid miles of 2x T&G Hem/Fir decking.
It always shrinks up more over time how much depends on humidity of the house and how dry it was to start with. Start with a sledge and a scrap of matching floor. Beat the boards together.
If the surface isn't exposed you can use a "Decking Puller" to pull the boards tight before nailing or screwing them. Decking pullers will ruin an exposed top surface however.
I know their is another tool out there that clamps to the joists and uses a lever and cam action to force the decking into place.
Can't recall who makes it but IIRC it is sometimes advertised in FHB print version. Oh yeah and don't let the decking get soaked after laying it or you will pry the building right apart. BTDT.EDIT: Just remembered that we also on occasion used wall jacks to literally jack the boards together. We used the type of wall jack that climbs a 2x4.
Edited 8/14/2009 2:02 am by dovetail97128
"I am not too concerned about the structural aspects of the span. I am however very concerned about eliminating the gaps in the boards during installation."
If you shorten up your spans, you needn't worry about gaps opening up. How difficult would it be? As for keeping your 2xs together for nail-up, use a bow-wrench tool...it should do the job.
Just curious, perhaps I misread something...but I thought you said you were laying your 2x6 T&G decking overtop sleepers, and that the sleepers were to be laid overtop bar joists; which happen to be spaced 4ft OC. What size are your sleepers? If you use 4x4s for sleepers and space them out every 2 ft OC over the bar joists, then you should have little to no sag and no worry about nailing the T&G tightly. Or...am I missing something here?
Davo
Thank you for your response.
The sleepers are 4x4's however they run parallel with the joists not perpendicular.
I am use to this system having only one exposed side and toe nailing through the face on the unexposed side. Having both sides exposed I am concern that fastening only ever 4' will not bring the boards tight. Drilling and screwing in between the bar joists through the T&G will solve this problem but will be very time consuming.
Looking for a way to fasten the boards in a more efficient way.http://www.multichambernailgun.com/b2/
I have built several cabins called Panabodes with second floors built exactly as you describe. As long as you are able to get the boards tight over the beams the gaps between are not noticeably larger.
If you think about it, for the boards have appreciably larger gaps in between the fixed points they would have to bow so that soon you would be laying them in a series of curves - not something that 2"x6" material is inclined to do. The only gaps that have occurred in the ceilings in the 10 years since I built them are the result of shrinkage and are no worse between the beams than over them.
I also routinely use the same material and spans on roof overhangs and porches with the good results.
Edit: Here is a link to one of the cabins.
http://www.lodgingchannel.com/accountsImage/11979/wp001_20030313_105743.pjpeg
Edited 8/14/2009 6:32 pm ET by fingersandtoes
I'll bet most gaps will be from shrinkage, so the more you can dry the stuff before installing the better. Having said that "better" is a relative term and if your stuff is going to twist a lot as it dries you are causing more problems than it's worth. You might make some extra money caulking the grove so it won't rain dirt.
Beer was created so carpenters wouldn't rule the world.
Now is the worst possible time of the year to install car decking. During the summer even really dry car decking is swollen with absorbed humidity.. During the winter when left in a heated enviornment the wood dries out and shrinks so that if you do a middlin' job of nailing things tight during the summer they will tighten up enough to prevent dirt from sifting through. Only getting a little looser during the dry winters..
Install it now and no matter what they will open wide open during the winter..
Please remeber it's not heat that causes wood to shrink, it's humidity that causes it to swell and a lack of humidity that causes it to shrink..
Wouldn't it be a better idea to use a moisture meter to decide if it was dry enough rather than worry about the season?
Dry wood will still be swollen with humidity in the summer and shrink in the winter..
I've got wood that tested at 7% moisture I assembled it tight in the summer and during the winter real gaps show.
Right. Probably because for your location flooring should be closer to 6% during installation. There is nothing mysterious about wood in the summer that makes it bigger or "swollen". 7% wood in the winter is the same size as 7% wood in the summer.
Edited 8/15/2009 3:26 am ET by fingersandtoes
Except it doesn't stay 7% moisture in the summer unless it's in a climate controlled environment. Nor does it stay 7% in the winter during the heating season..
Let the wood sit in an unconditioned state for a couple weeks (like they recommend to acclimatize it to the site# and it will quickly absorb the humidity in the air and go up to something more like 12% moisture. #15% if it's really humid)
During the winter heating season I've tested wood as low as 3% moisture in my house.
That's a pretty broad swing for supposedly "dry" wood.. That is what causes the difference..
I found the easiest best compromise is to install wood flooring during the winter and don't take great pains to get it really, really, tite. Then during the summer it has enough room to allow for swelling caused by the increase in humidity. In the dead of the winter the floor still looks ok because you've removed all the big gaps when you installed it..
If you read the many recent discussions on laying wood flooring you will see that acclimatization in the way that you describe it is generally not recommended anymore and will result in the problems you describe.
Whatever the season the wood should be brought to the appropriate moisture content, which is different for each region. Once installed, the wood will fluctuate between its low and high moisture content along with the rest of the house as the seasons change.
It doesn't make a bit of difference if it swells to its summer level a day after it is put in or six months later. The important think is that it is at the right level when the fasteners are installed.
in my condo project... the lofts are 3.5 x 12 x 20ft finish grade glue-lams... supported only at one end and @ 15ft... with a a 5ft cantilever... no T & G just glued and one bolted to the next... on the steel 6x8 steel beam i welded a 2x2 angle iron that was punched on 3" centers where we used lag bolts going up... did the same thing to the 4" angle iron it rests on on the wall end...
wondering if you could use a Kreg jig and use pocket screws from the bottom ... might look kinda cool to boot
p
Aaagghh! You are driving me nuts again. I've wanted to do a loft out of glulams for years. BLO finished railings, glulam lofts - I may end up buying one of the d*mn things when you are done.
LOL... no one can say i don't have fun...the glue-lam thing was the only option i could come up with ... ceiling height at the lowest point was just over 16ft... off the finished floor... then with the rise of the roof over 75ft... it was just under 18ft...I had to span 16ft... which would have called for 12" framing plus decking.. plus sheet rock below and a wood floor above... I just didn't have that much space to give up... and still call it living space...I found a factory in Brazil that would make what i wanted... ie... most glue-lams are not apperence grade.. and are manufactured with a bow to carry the weight... They made mine true & square without voids... in hindsite I should have ordered them with groves and then used splines on the joints... I could have also had them mill the bottom to look like beaded or V-grove ceiling... but i was in a hurry for them... ends up they got caught in Katrina... then went to TX where the next storm got em... added almost a month to delivery...But what i got was... a second level that installed in several hours per unit... a finished ceiling... and a ready to sand and finish floor... the floor BTW took my home brew finish very well and looks like a million dollars... and they are GREEN (hate that word)... farm raised long leaf pine... material cost... less than $5sf... I purchased a container load... and have 4 left that will become my 4ft x 20ft dinning table
p
my 4ft x 20ft dinning table>>>>>>>>>>>>>>>>.
There you finally have a table that will be big enough!
When is the invitation for Memphis BBQ coming??
..... Man... when I finish this project... there will be music... food...Drink....and naked women... or at least 3 out of the 4....I'm close... real close...it's sunday and i'm off to work now... the cool thing about have'n a job site dog... is you are forced to spend at least a little time on the job everyday... sunday lets me get my course ready for monday... even did some landscape work yesterday... scored the one patio i didn't stamp..the BBQ is on the way
P
I feal like making a road trip!
My sister-in-law is over the border from you in Mississippi!
Haven't been in your hometown in at least 10 yrs!
most folks from memphis have moved over the border to mississippi or arkansas ... our politics aren't good and property taxes are worse... so they flee... :) I have a shopping center in southaven... (in mississippi just outside of memphis... and it's the best property i own)wish everything i had was in mississippi :) besides my wife is from mississippi :)p
"I have a shopping center in southaven... in mississippi just outside of memphis... "
I have to say that evokes certain images. I see shops selling old guns, animals that shouldn't be eaten served barbecued and pointy boots like Tom Waits might wear. Hows that for closed minded?
Then again you probably think our shops are full of chainsaws, lava lamps, paddles, bongs and cookies. Hmmm... you'd be right!
LOL... Southaven Mississippi... in desoto county... one of the fastest growing counties in the country... fueled by many things... it's just outside of memphis... but with maybe 20% of the crime and 50% of the taxes... The former Mayor of memphis was given "Realtor of the year" awards for selling so many homes in Mississippi...ie he ran em out of memphis... so they fled to Mississippi.. It's also next to Tunica County which has casinos... anyway... huge growth... good schools... good jobs... tons of building... My center is vintage 1970's before the town was even a city... but it's well kept and located well... and I'm at 50% of the rent of the new centers in the area... i have a dominos, a subway, a church, a hispanic grocery, a barbershop... ect... it has 27 bays and it's FULL... thank god... think I've owned it about 10 years...
p
See that's exactly what's wrong with the world today. Your mall has a Subway and Dominos and so does mine. Aren't the shopping centers as I described them more interesting?
I'd put in a casino and a whore house but ......
p:)
You might think about a second hand accordion store and maybe a parts depot for travelling carnival rides.
The church I grew up in used pole barn nails to pull the decking together between supports.
My guess is drill through edge of new board, then drive nail into fastened deck. Faster than screws?
I installed T&G 2"x6" maple flooring on 4'-0" centers years ago. The tongue was drilled and a 6" nail was handdriven to connect the boards. I do not recall how the boards were installed to the joists. I do remember the joists were steel members.
The 4'-0 span was not a problem,the floors were less bouncy then thinner decks on 16" centers.As far as shrinkage in the winter,we installed it in the winter and no problems that I am aware of.
mike
Thank you everyone for your input. I truly appreciate your thoughts.
Hope it's not too late for this info, but you nail down 2x6 roof decking with a pneumatic framing gun, shooting a 3½" clipped-head nail on an angle through the tongue just like installing standard 1x T&G with a finishing nailer.
Reef in the boards tight to each other with a big old beater of a chisel.
And Frenchy was right--summer is a bad time to lay this stuff if you care about gaps appearing during the winter. However--if you lay 2x6 decking nice and tight in winter when it's bone dry, you must leave expansion gaps on both sides of the room or the next summer the flooring will shove the walls apart or buckle or both. Figure 3/64" per plank expansion in a temperate region that sees cold dry winters and hot humid summers.
Cover the expansion gaps with baseboard and shoe moulding but nail the shoe only to the base, not to the flooring.
Dinosaur
How now, Mighty Sauron, that thou art not broughtlow by this? For thine evil pales before that whichfoolish men call Justice....