Discussion Forum
Discussion Forum
Up Next
Video Shorts
Featured Story
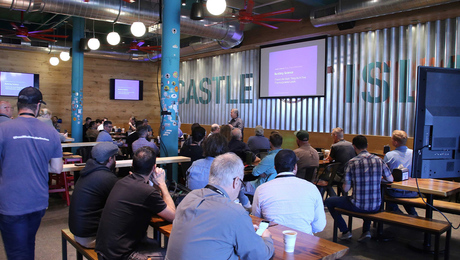
Listeners write in about shower panels and cordless tools and ask questions about old wiring, air leaks, and gutter covers.
Featured Video
Video: Build a Fireplace, Brick by BrickHighlights
"I have learned so much thanks to the searchable articles on the FHB website. I can confidently say that I expect to be a life-long subscriber." - M.K.
Fine Homebuilding Magazine
- Home Group
- Antique Trader
- Arts & Crafts Homes
- Bank Note Reporter
- Cabin Life
- Cuisine at Home
- Fine Gardening
- Fine Woodworking
- Green Building Advisor
- Garden Gate
- Horticulture
- Keep Craft Alive
- Log Home Living
- Military Trader/Vehicles
- Numismatic News
- Numismaster
- Old Cars Weekly
- Old House Journal
- Period Homes
- Popular Woodworking
- Script
- ShopNotes
- Sports Collectors Digest
- Threads
- Timber Home Living
- Traditional Building
- Woodsmith
- World Coin News
- Writer's Digest
Replies
Never heard of it. Sounds like good stuff though.
Dave
Looks fascinating. I wonder how much it costs?
"Education makes a people easy to lead, but difficult to drive; easy to govern but impossible to enslave." [Lord Brougham]
It's marketing hype.
Components in a wall system cannot be measured on their own. Add a finish wall product with a good quality paint and the results are completely different.
A vapour barrier with a perm rate greater than 0 is not a vapour barrier.
Gabe
Whoa!
Even PVC or EPDM roofing products have a miniscule premeability. The reason for ratings is that everything will eventually transmitt water. The rating says how much...
I would say that anything with a perm over .05 is not much of a VB.
Excellence is its own reward!
No, non, niet.
Many products have for all intensive purposes a 0 perm rate. Glass for example. So do many plastics and rubberized membranes.
Seams are another story.
In the ad they claim a perm rate of 1 to 10. This definitely not a vb.
Gabe
definitely not, I wouldn't use it.
Didn't think about glass.
Practical perm and actuall perm are two diferent things is the point I was making..
Excellence is its own reward!
Gabe:
Notice that the web page says "Vapor Retarder". I think that explains the perm ratings.
All:
I know this sounds corney, but I'd be interested to look at the material under a microscope. To me, the concept sounds good as IMO walls do need some breathability. I'll wait untill other people use if for a while first though...Matt
Let me start by saying that I'm not a "building scientist". I'm a 9 year intern architect and somebody who's interested in WHY not just IF things work. Therefore, the issues I'm about to lay out are quite likely to be questioned, and to me that's a good thing. If I can reach a different conclusion through an exhaustive discussion, I'll be more than satisfied - but the underlying problem in my mind is that there are some fuzzy issues floating around right now...
First off: I recall a few years back that Tyvek was NOT marketed as a water barrier... Now it is. I started this thread because the new product seems to address an important issue: seasonal changes & a vapor source that is not one directional. I've also come across another product that's not unlike the memBrain product - but this one is intended as a roofing underlayment. As far as I can see, it looks like another 'holy grail' type product: Roofshield, from the UK. Here's the website: http://www.proctorgroup.com/proctor.asp?op=products&top=14&left=71
As a perpetual skeptic, I'm keep coming back to the thesis that any vapor barrier might be a bad thing, except perhaps under a slab. Buildings for hundreds of years were able to breathe, and mold/moisture issues only existed where leaks were present (for the most part). Noteworthy to me is the fact that mold issues have mostly come about since the advent of AC, which coincides with the introduction of rules concerning vapor barriers. AC introduces a totally different atmospheric condition and invites moisture via dissimilar temperature/dew point issues - quite the opposite of nature. Trouble is, we seem to be blindly taking the advice of the fiberglass batt industry & placing an impervious barrier in what should be an escape route. No wonder we've got mold in every cavity of modern homes... it's trapped.
This is interesting to me, and the link above provided more interesting reading. Commentary invited!!
If you truly want to be objective in this research you have to divide moisture problems into two distinct catagories.
One is best described as ambiant with local conditions and the other is strickly man made as in lifestyles.
The one that confuses most applications is the lifestyle issue. Some families generate 10 times more moisture than others, regardless of the geographic location.
The one that has the ability to do the most damage to a conventionally built home is lifestyle generated.
Moisture from within must be expelled not transmitted to the outside.
Any questions about what I've writen so far?
Gabe
Hi Gabe,
Any dwelling that will be inhabited by people IMHO should be designed for worst case in "lifestyle". I doubt that you're suggesting otherwise. You say Moisture from within must be expelled not transmitted to the outside. I guess that means mechanical ventilation, but the only such ventilation I'm familiar with is exhausting bathrooms or kitchens. I'm familiar with scenarios where it's advantageous to replace stale air with fresh outside air, but otherwise I'm not sure what you're getting at. I'm sorta thick at times...
My contention [that conditioned indoor environments placed adjacent to drastically different temperature & humidity conditions, separated only by highly insulated but not necessarily well sealed walls, with a vapor barrier somewhere in the mix and quite often several partially successful vapor retarders (caulk, paint, tyvek, etc) - is asking for trouble] remains unchanged. Really, I'm dangling a stick to anybody in the "no VB is the best" camp to come up with some science to help their argument. I hope this vine does not wither & die, because I'm truly interested.
Absolutely correct in your first assumption.
Without going to whole house air exchange units we can dramatically reduce the moisture generated by lifestyles with properly balanced exhaust fans.
In moderate climates.
Bathrooms should have a unit large enough that with a 1" undercut space under the bathroom door, there should be enough exhaust power to pull a sheet of toilet paper under the door.
The kitchen exhaust must be a true exhaust and not a recycling fan through a filter. It should be strong enough to pull a tissue paper from at least 3 inches away. If you're constently having to wipe the front of the stove hood/exhaust unit then you need a better one.
The laundry room should have a bathroom exhaust fan as well with the same capacity as a large washroom would have.
In winter that's a fair amount of heat being kicked outside but without the extra humidity in the air the comfort level should still be improved even at a lower temperature.
Regarding the "no VB" camp.
It's an outdated theory that belongs in the age of plentiful and very cheap fuel. It has no place in today's world.
First you seal a house then you heat/cool it.
Gabe
My confusion with VBs is in climates like MN, where the warm/humid side of the house switches with the seasons.
As they do for the majority of North America.
The best rule of thumb is to install it as close to the inside of the of the envelope as possible.
Gabe
As they do for the majority of North America. The best rule of thumb is to install it as close to the inside of the of the envelope as possible.
I'm going to have to disagree with that statement Gabe unless you qualify it a little better. In the coastal south of USA, it's rarely cooler outside than inside, and for that reason I'm going to have to side with Joe L and say the VB should be placed on the outside in THAT climate region. (but I question whether TYVEK is suitable for that case).
And to further the topic, whether having TYVEK on a house + poly inside - in northern USA climates - equates to two vapor barriers (they used to say it wasn't WP but now say it is) and thereby creating a trap fo moisture & creating rampant mold problems.
??
Factoid..................What lies North of the Mason Dixon line make up the majority of North America :)
I would take on the role of devil's advocate and challenge both you and Joe L's theory. I will explain later on in this discussion but both of you are wrong.
Do you not think that the VB serves the occupants better on the inside (the zone that we want and can control) than it does on the outside (the zone that we can't control).
I have a question for you...............In the north country we have ice arenas that operate year round.............where should the vb located and why?
Gabe
Having only recently crossed the Mason Dixon line to work & live in New England, I still keep the SE Coast in mind when discussing this stuff... but now that you point it out you are absolutely correct in your geography
I wish you'd explain now rather than later about theories... I'm trying hard not to take a side thus far - so I'm not sure how you intend to explain that I'm wrong?? As for Joe, fire away - I like his scientific approach, but I don't consider anybody 100% right, always.
Maybe I've not been clear, but I have more questions than answers about VB's. I'm trying hard not to just accept "always did it that way" as a basis for doing something. Having said that, I'm fast taking a liking to Icynene - which may be part of what is clouding my thinking in the matter of the VB.. but truth be told, I've got a very large golf clubhouse under construction right now that will have high density R38 batts in the roof with vent channels above & carefully sealed poly below. If this is certain to fail, I'd like to hear about it now rather than after it's too late!!
If you can offer anything relative to my conjecture about VB inside a wall & sealed VR outside possibly trapping moisture, I'm all ears. If I'm wrong, please don't beat around the bush.
Thanks
ps: As for the ice arena: I'd just use icynene
What I was challenging was the old theory that in cold climates you put the vb on the inside and in warm climates you do the opposite.
What I say is that in all climates, you put the vb on the inside and you let the exterior breath.
The danger with tyvek type products is that they have the capacity to seal on the outside as well and thereby creating an incubator effect between the walls and greatly accelerating the deteoriation of any organic products between the two.
The last golf course that I work on was designed by Trent Jones Sr. and Jr. but the club house was designed by another firm.
I've done a large post and beam structure that had open cathedral ceilings with great success using foam.
But I digress.
ps: As for the ice arena: I'd just use icynene
PS: That wasn't the question.
but truth be told, I've got a very large golf clubhouse under construction right now that will have high density R38 batts in the roof with vent channels above & carefully sealed poly below. If this is certain to fail, I'd like to hear about it now rather than after it's too late!!
What's the purpose of the ventilation in your roof design?
Gabe
purpose of vent in roof assy. is to vent cavity, and in turn lengthen the life of the shingles which are red cedar on ben obdyke cedar breather...
thoughts?
Don't know how to tell you this but you won't add a month to the life of the shingles by going through the trouble of venting.
Ventilation is another abused and misunderstood practices that has been carried over from the "I do it because my dad did it" era.
Even asphalt shingle manufacturers have started to drop the ventilation requirements for warranty purposes.
It was an acceptable practice that allowed moist air from within to escape into the wild blue yonder from improperly sealed homes a la balloon construction era.
Gabe
Gabe: So you don't know how to tell me? You just did...
I'm heading out for vacation in the morning, hope to keep this alive next week.
I dodged the hockey arena question because I don't know how I'd do it. Care to offer a recommendation? There was a hockey arena in Charleston SC (converted kmart building where they removed a row of columns which was slick in & of itself) but I'm not sure how they tackled it down there either!
Finally, what do you think of Icynene?
We used to use icynene but found that Polyurethane foam selection better for our application. Probably use anywhere from 25,000 to 100,000 cu. ft. a year.
We use it on just about every project that we do.
Gabe
Gabe, I think you and just agreed on something (other than politics) <G>. Andy Engel, The Former Accidental Moderator
I tend to say a lot with few words........does that mean you agreed with everything I said on this post?
BTW didn't know there was anything discussed on this board other than vb, ventilation and politics.
Gabe
I didn't agree with everything you said re vapor diffusion retarders, but I am with you on the foam. Andy Engel, The Former Accidental Moderator
Good to hear you didn't agree with everything that I said about vapor diffusion retarders but what exactly did you not agree with?
I would like a chance to change your mind.
Gabe
You're baiting me. <G> I think you're wrong saying that VDRs should be placed at the inside in southern construction. I do agree that walls should be built so that they can dry, but in the humid south, in the summer, in an air-conditioned building, the drying is more likely to occur to the inside. Of course, we could avoid this entire conversation by insulating this theoretical house with foam.Andy Engel, The Former Accidental Moderator
Baiting, who me? You must be referring to my fishing prowess.
Your last paragraph made half my point.
Foam insulation is a type II vb and as such is installed in the center of the wall system dividing interior sheeting components from exterior sheeting components with only the studs bridging the two.
By installing any conventional vb on the outside the theoretical house, you effectively defeat it's intended purpose by sheeting, taping and painting the inside layer.
The paint we typically use in kitchens and bathrooms is a very effective vb.
We install ceramic tiles in the bathrooms or tub surrounds. All effective vbs.
Many wallpapers are coated with vinyl like layers for washability.
We install a load of vbs all over our homes without much thought as to effect.
What if I was to state that it makes absolutely no difference whatsoever where you install the vb? What counts is that you have absolute continuity ensuring a perfect seal on only one layer of your wall composition.
I think we've been sold a bill of goods when in comes to the proper location of the vb in the wall systems of homes located in the south vs the north.
Back to you Andy
Gabe
What if I was to state that it makes absolutely no difference whatsoever where you install the vb? What counts is that you have absolute continuity ensuring a perfect seal on only one layer of your wall composition.
The Devil must be shivering. I would add, however, that it does matter that the VB be on the warm side of the first condensing surface. If you'll give me that, we can both take the rest of the day off.Andy Engel, The Former Accidental Moderator
You guys sure would make good SIP salesmen... :-)>Kevin Halliburton
"I believe that architecture is a pragmatic art. To become art it must be built on a foundation of necessity." - I.M. Pei -
Yeah, except on a visceral level, I don't trust their longevity. It just makes my hinky to trust the structural integrity of a house to a glue joint between foam and OSB. I'm open arguments though.
Andy Engel, The Former Accidental Moderator
Hey, I was talking sales. Who said anything about trust? :-)>Kevin Halliburton
"I believe that architecture is a pragmatic art. To become art it must be built on a foundation of necessity." - I.M. Pei -
Ok Andy, since this thread seems wrought with challenges to concede I'll add one of my own. The structural integrity of UL certified panels is pretty well documented but I won't hassle you about the OSB version any more if you will concede that these guys haven't left much to criticize:
http://www.thermasteelpanels.com/index_i.htm
You get your structural double steel studs at 12" on center, with no thermal bridge, and a solid foam core serving as insulation and VB. Could you live with that?Kevin Halliburton
"I believe that architecture is a pragmatic art. To become art it must be built on a foundation of necessity." - I.M. Pei -
Yes. And I like panelized construction, or at least the theory.Andy Engel, The Former Accidental Moderator
"I like panelized construction, or at least the theory."
A man after my own heart..................(-:Wear short sleeves. Support your right to bare arms
Can't give you that one.............
It has to be on the most constant/stable side...........yes.
Which for 99% of the time would be the inside layer.
The side that has the most fluctuation must be the side to breath.
Gabe
Hmm, let me think about that. It has to be away from the side that has the greatest drying potential, but whether that's always the most stable side I don't know. I can imagine situations where the most stable side is always the wettest, but they'd be extreme and probably not found in most houses.Andy Engel, The Former Accidental Moderator
Take your time, a good meal has to be savoured and that takes time.
Gabe
:)
Okay Andy, time's up............
What do you think?
Gabe
To keep moisture out of framing assemblies, the VB has to be on the side with the greatest vapor drive over the course of a year. Moisture moves from wet to dry and from warm to cold, so in your climate, I'd generally argue that the VB should be inside. And yes, that's the most stable environment. In Florida however, I'd argue that any VB has to be on the outside of an air-conditioned building, which is the less stable environment. So I don't think that proper VB placement has much to do with environmental stability. It has a lot to do with the location of the greatest annual source of driven moisture, and conversely, with the location of the area of greatest drying capacity.Andy Engel, The Former Accidental Moderator
Andy,
Why is there a fear to have the framing assembly exposed to wet dry cycling?
If the inside of any home, regardless of climate, is the one element we strive to control it has to be that the inside temperature and humidity level would be a constant.
In any situation, from the living quarters outward, by sealing first and then insulating we can effectively minimize the amount of mass/volume/area that will require heating, dehumidifying, cooling or humidification thereby reducing the energy to do so.
Another inherit danger in installing the vb on the outside would be the likelyhood of inadvertantly installing one on the inside as well. If we accept the fact that most paints will act as a vb over drywall as will the other products previously named then we would have created an incubator inside certain wall conditions. In hot humid climates this would greatly accelerate fungus, mold and mildew.
Most modern day construction practices allow the outside layer of a house to breath. So any moisture that would enter, would have equal ability to leave harmlessly.
Gabe
I absolutely agree that framing assemblies need to be built in such a way that affords the opportunity for drying. I don't think we have any real disagreement re northern assemblies. It is the humid south that's hard to do right. Here's my concern: In the summer, the moisture drive from outside to inside (in the south) is tremendous. Assuming that the AC is running, and that there is no effective outer VB, the inside wall assembly will likely be cool enough to become a condensing surface, and so you've got a wall full of liquid water. If there's a VB there, no drying potential exists. If there's no VB, moisture can pass through the drywall and into the house where the AC can remove it. Sure, this doesn't work if you've got a paint or wallpaper VB, but what's the alternative? In my mind, it's cut and dry in the deep south. The problem areas are in the middle, where you've got both extreme winter and summer conditions. Andy Engel, The Former Accidental Moderator
We seem to be stuck on the south issue and I think that you have to join me outside the box for a little bit.
The vb issue regarding southern installation is rooted in tradition more than fact.
Let's step away from residential for a little bit and look at commercial construction.
Envelope integrity is dependant on understanding the 3 requirements for water infiltration into a building.
First you have to have water, whether in the form of rain or vapor.
Next you have to have a means of entry, a hole.
And last you have to have a force or pressure differential.
If you eliminate any one of the three, you eliminate the problem of water infiltration.
Plug the holes or pressurize the building would seem easy enough.
May sound simple but thousands of failed buildings testify differently.
Rain screens were considered to be the answer until we considered water in the form of vapor.
It was easy to build a shield around a building and prevent the rain from infiltrating the envelope. But what about the moist air condensating inside the wall cavity?
The easiest solution, build a shield away from the VB that seals the envelope and let any condensation drain freely to the ground.
Now back to the residential.
Let's look at a wall assembly. From the inside you have drywall, studs bridging to the outside, cavity filled with some form of FG or Celulose, sheathing, a VB and some form of exterior cladding, (brick, vinyl, wood, strucco,whatever).
In a perfect world or laboratory, moisture would be stopped dead at the exterior VB.
In the real world, moisture will infiltrate into the wall cavity. Will the wall assembly have the same amount of moisture top to bottom or will most of the moisture gravitate to the lower area?
Which is easier?
Let the moisture gravitate to the bottom and drain away from the wall assembly(in other words, let it breath to the outside) or try to suck the moisture through painted drywall into the room for the AC to dry?
It is impossible for a regular AC to dry the inside of any exterior wall cavities in any home that is lived in.
Therefore................It is much easier in a moist hot southern climate to maintain a healthy environment inside a typical home if the VB is closer to the inside face of the wall cavity.
Gabe
A short blurb on Isycene at Building Green:
http://www.buildinggreen.com/products/icynene.cfm
Speaking of green, I'm still rooting for the soy foam to prove itself worthy in the competition: http://www.soyfoam.com/
I'm currently using a non-toxic soy-based mastic stripper in my basement.
That little bean can do wonders. ;o)
Yeah, I saw the Soy Foam Insulation web site. I will definitely check that out when I get ready to insulate my cabin next year. The only thing that gives me little pause is the phrase "inhibits mold"... "Inhibits" as in slows down a little or a lot? I do like the part where they say 30% to 50% less cost passed on to the customer...
The simple answer? SIPs with great care to seal the joints. Now there's a holy grail.
"My confusion with VBs is in climates like MN, where the warm/humid side of the house switches with the seasons."
If you read some of the books from Buildingscience.com they discuss this. And you can see their recomendations by looking at the Buildings That Work section for the details in different cliamtes.
One of the things that they look at is the relative amount of water in the two cases. I don't know what the realitive vapor pressures or, but you might have 2 months of 20 degress difference in cooling and 6 months of 40 degress difference in heating.
And this is the reason that, except for the very coldest climates they don't recommend an impervious barrier like poly.
"Bathrooms should have a unit large enough that with a 1" undercut space under the bathroom door, there should be enough exhaust power to pull a sheet of toilet paper under the door."
In the houses I build I always leave less space under the bathroom doors than the other rooms so that the replacement air for the exhaust fan comes from the heating vent, usually located in the kick of the vanity cabinet, which has tempered, fresh air from the HRV, rather than stale air from the rest of the house.
On another note, does anyone else here use ADA, airtight drywall approach rather than poly, which i find a real pain in the backside to install? Since I was certified in ADA installation about 8 years ago, I haven't used poly vapor barrier and don't miss it one bit either, I might add :)
In the houses I build I always leave less space under the bathroom doors than the other rooms so that the replacement air for the exhaust fan comes from the heating vent, usually located in the kick of the vanity cabinet, which has tempered, fresh air from the HRV, rather than stale air from the rest of the house.
That would be a very dumb installation.
On another note, does anyone else here use ADA, airtight drywall approach rather than poly, which i find a real pain in the backside to install? Since I was certified in ADA installation about 8 years ago, I haven't used poly vapor barrier and don't miss it one bit either, I might add :)
That would be another very dumb installation method. You must be from British Columbia. The land of the biggest building envelope failure in Canadian history.
Gabe
From your comment, I can see you are very ignorant, and have provided no backing for your comments. If you have an understanding of the ada system and if it is done correctly then there is absolutely no problem with it. I am currently living in my own home which is built with this method, it is VERY efficient and the air is always fresh, cooking smells never linger around and i have a super tight air/vapor barrier, even have had my house tested with a fan door I've built many houses using this method for years now and they are some of the nicest, most airtight, upscale houses in our area. Unlike you, I actually have backing for my comments and statements. I have never had a "building envelope failure" and if you're talking about the leaky condo situation in the lower mainland of British Columbia, that has nothing to do with Airtight drywall but rather with poor stucco and flashing work. Are you always this rude to others on the forum?
Edit: I can see by reading the rest of this thread that you really are ignorant, because half of your posts actually support the ADA method, you speak of maintaining a vapor barrier on the inside of the home, and you also state that things like vinyl wall paper, kitchen and bathroom paint and ceramic tile all create effective vapor barriers, but through your stupidity and lack of knowledge you've failed to recognize this is a crude but similar approach to the system I and many other builders have successful used for years now. I hope for the customers of Ontario's sake that you are not a contractor.
Edited 10/11/2003 12:04:29 PM ET by SledBC
Are you always this rude to others on the forum?
No.
Only to arrogant people who butt in with useless information based on half baked theories. Certified in ADA my butt.
I have never had a "building envelope failure"
I don't think that you're qualified to identify one even if it bit you in the butt. There's more to a healthy house than the airtight issue. Drywall is organic and as such will promote mold and mildew. No use protecting the interior face of drywall if moisture attacks everything behind it and rots the gypsum.
and if you're talking about the leaky condo situation in the lower mainland of British Columbia, that has nothing to do with Airtight drywall but rather with poor stucco and flashing work.
Wrong again. It failed because of a combination of corrupt and incompetent building officials, poor code interpretations, inferior building products and applications as well as poor contractors. In handing down their final report on the failure, blame couldn't be assigned to any specific thing or group because the investigators found all were to blame.
I suggest you keep your mouth shut and your eyes open as this discussion between the devil's advocate and my main man at Taunton and you might actually learn something as this thread evolves.
Gabe
BTW you could probably fit all the the houses you have actually built into one of my projects and still have enough room to play 9 holes of golf.
"Drywall is organic and as such will promote mold and mildew. No use protecting the interior face of drywall if moisture attacks everything behind it and rots the gypsum."
This is the most idiotic thing you've said so far. According to this statement of yours, my system is far superior to yours, since my vapor barrier is INSIDE the drywall effectively protecting the gypsum, whereas yours is outside, leaving the drywall exposed to the humid air inside the envelope of the house. Or are you saying that you're getting moisture in your walls from the outside that can't rot the gypsum because its protected from behind with poly? I don't know what kind of places you're building but I'm glad you're not my contractor. I'd prefer to have a complete air/vapor barrier such as in the buildings I've constructed, to prevent humid air escaping into the wall cavity from the living area of the house. I don't understand where this moisture you're speaking of is going to get into my wall cavity. Why don't you enlighten us as to the problem with this system of building rather than just saying it's "dumb". If you can't back up your statements, do us all a favor and go back to 3rd grade.
I am not wrong on the leaky condo situation, I agree yes that it was due to poor (mostly foreign) contractors and the building officials were overwhelmed, but either way, it has nothing to do with the ADA system, which is completely effective and a superior way to constructing an air barrier to stapling some plastic over your wall studs that you cannot inspect after the drywallers hack it up and then cover it up. When stucco is put on in one really thick coat rather than 3, and flashings arent installed correctly causing water damage, rot, and concrete decks start falling off the side of apartment buildings, that has NOTHING to do with poor air barrier installation. Half of your statements are completely irrelevant and have absolutely nothing to back them up.
On another note, i don't give a rats #### how big a building you've built, square footage means nothing its quality of construction that matters. It's a hell of a lot easier to construct a 5000 sq foot barn with no penetrations to the air/vapor barrier, than it is some of the houses we've been building lately. There's a new walmart being built here as we speak, you should give them a call, maybe they need someone like you to tell them what to do, or maybe you can sell them some REALLY big sheets of poly.
Edited 10/11/2003 1:39:07 PM ET by SledBC
My my my, what a temper you have there. Chill out, there's no shame in being dumb, I'm sure you don't stand out amongst your friends.
This is the most idiotic thing you've said so far. Hang in there......I've said some far more idiotic things than that.
According to this statement of yours, my system is far superior to yours(is that what makes my statement idiotic), since my vapor barrier is INSIDE the drywall effectively protecting the gypsum, whereas yours is outside, leaving the drywall exposed to the humid air inside the envelope of the house. How did you get it inside the drywall? Did you peel back the paper and shrink wrap the gypsum? Did you consider the moisture from outside the envelope or doesn't that count?
Or are you saying that you're getting moisture in your walls from the outside that can't rot the gypsum because its protected from behind with poly? No... haven't said that and haven't indicated yet that I'm even referring to poly.
I don't know what kind of places you're building but I'm glad you're not my contractor. Not to worry.
I'd prefer to have a complete air/vapor barrier such as in the buildings I've constructed, to prevent humid air escaping into the wall cavity from the living area of the house. What humid air are you referring to? You already said your houses have a complete HRV system and all that stale moist air from your bathroom showers is sucked out into the wild blue yonder. I assume the same is true of the stale moist air from the kitchen and laundry rooms as well.
I don't understand where this moisture you're speaking of is going to get into my wall cavity. From the outside Einstein.
Why don't you enlighten us as to the problem with this system of building rather than just saying it's "dumb". If you can't back up your statements, do us all a favor and go back to 3rd grade. Is the 3rd grade where you quit learning and you consider it the pinacle of your education.
I am not wrong on the leaky condo situation, time for a flip flop I agree yes that it was due to poor (mostly foreign) contractors and the building officials were overwhelmed, but either way, it has nothing to do with the ADA system, I was just comparing the BC Deconstruction methods to the rest of Canada which is completely effective and a superior way to constructing an air barrier to stapling some plastic over your wall studs that you cannot inspect after the drywallers hack it up and then cover it up. I think he's going back to discussing the BC lawsuit again When stucco is put on in one really thick coat rather than 3, and flashings arent installed correctly causing water damage, rot, and concrete decks start falling off the side of apartment buildings, that has NOTHING EVERYTHING to do with poor air barrier installation. Half of your statements are completely irrelevant and have absolutely nothing to back them up. 38 YEARS IN THE INDUSTRY
On another note, i don't give a rats #### how big a building you've built, square footage means nothing its quality of construction that matters. You're right.It's a hell of a lot easier to construct a 5000 sq foot barn with no penetrations to the air/vapor barrier, than it is some of the houses we've been building lately. You're wrong. There's a new walmart being built here as we speak, you should give them a call, maybe they need someone like you to tell them what to do, or maybe you can sell them some REALLY big sheets of poly. I've never done a Walmart but I've shopped in several, will that earn me a BC contractor's licence?
Never done a little 5000 sq. foot barn either but might be fun for a weekend.
Said it before, you would be well advised to shut up and listen instead.
You have no clue where this discussion is going yet. Andy and I are only playing off one another so far and I will not tip my hand to you, regardless of the dumb comments you make.
Adios DF
Gabe
Wow, I cannot believe how many times you can contradict yourself within your own posts. No sense arguing with you since you obviously think you're king cheeze or whatever around here, but something tells me you have little respect from the others here, though that is just my first impression.
38 years in the industry hey? That explains a lot....you know the expression, old dog, new tricks...I'm not asking you to tip your hand, in fact I never wanted to get in an argument with you to begin with but you like to attempt to demean others, unfortunately making yourself look the fool. If you cant admit that there are other construction methods that are equal if not superior to what you learned 38 years ago, maybe you should consider retirement. You say "im right...im wrong...." yet all you have to back it up is the fact you're old....good sell there gramps.
since my vapor barrier is INSIDE the drywall effectively protecting the gypsum, whereas yours is outside, leaving the drywall exposed to the humid air inside the envelope of the house. How did you get it inside the drywall? Did you peel back the paper and shrink wrap the gypsum? Did you consider the moisture from outside the envelope or doesn't that count?
Pardon me, i should have said "Inside the building envelope, or on the interior face of the drywall".
I don't understand where this moisture you're speaking of is going to get into my wall cavity. From the outside Einstein.
So you're saying that you build leaky walls? If moisture in the wall cavity would rot the drywall, wouldnt you think it would damage the wood framing as well? Or wouldnt the drywall on my ceiling have begun sagging over the last 5 years of humid weather that we get where I live? Being right on the coast where it rains half the year and snows the other half, there would be no greater test to prove me wrong than my very own house. In fact right now I'm looking down the ceiling in my living area which is 53' long and it looks perfectly flat and the drywall is in perfectly good shape, yet there is nothing protecting it from the air in my well ventilated attic other than approx 11" (R40) of cellulose insulation, and my vapor barrier is on the Interior face of the board, so it seems to be working fine in practice. Im venturing to guess you're just calling me dumb with absolutely no understanding of how the system actually works.
I'd prefer to have a complete air/vapor barrier such as in the buildings I've constructed, to prevent humid air escaping into the wall cavity from the living area of the house. What humid air are you referring to? You already said your houses have a complete HRV system and all that stale moist air from your bathroom showers is sucked out into the wild blue yonder. I assume the same is true of the stale moist air from the kitchen and laundry rooms as well.
Wow, you actually understood something, now I wonder what your argument is, are you saying there is no need for an air/vapor barrier at all?
I would much rather have a civilized conversation where possibly we both could learn something from each other than continue this retarded arguing that you started. Rather than attempt to demean me once again with your useless comments, why don't you start by pointing out why you think this system of air/vapor barrier does not work?
Edited 10/11/2003 5:20:30 PM ET by SledBC
Gabe/Sled:
In between your chest-thumpings, I'm picking up some interesting points from both of you.
I think the argument between you two is confined to where to put the VB on the sheetrock...interior surface or exterior, correct?
I then have to ask, if paint/wallpaper is a VB then wouldn't most houses, by default, not need any other VB in the wall cavity?
"I then have to ask, if paint/wallpaper is a VB then wouldn't most houses, by default, not need any other VB in the wall cavity? "
Darrel, the difference is in the system of installation. With the ADA system there is a network of gaskets and caulking, eg, bottom wall plates are caulked/gasketed to the floor system, then a 1/4"x1/2" closed cell foam gasket is placed along the bottom plate and partition studs as well as the partition wall top plates where they meet an atic, the drywall is then screwed through the gasket, 8" on centre to provide an airtight seal, also special sealed and gasketed electrical boxes are used and the drywall is fastened there as well. A low perm primer (or 2 coats of oil paint) is then used to provide the vapor barrier rather than using a sheet of polyethlene.
If you know much about about air/vapor barriers you'll know that air leakage creates far more problems than vapor diffusion does, and this is where the ADA system is far superior to a sheet of polyethlene, if installed correctly, you can always visually see a hole, or imperfection in your air barrier, whereas, you could install poly perfectly the first time then it gets cut during wall board insulation and buried, now you have a hole you could never find. Its really nothing new, just a new approach to air/vapor barriers, in fact you probably have done or seen something similar, eg. a living area over a garage where the plywood subfloor acts as the air/vapor barrier, although plywood at a first glance doesnt look like a vapor barrier, you can't blow through it, so it will stop humid air from passing through :)
I hope that helps explain it a bit better to you :)
Edited 10/11/2003 6:04:14 PM ET by SledBC
Darrel,
That thought process has hatched the theory that if you install the drywall and seal the bottom, edges and super seal the electrical and plumbing outlets to the supreme then you would have an effective VB as long as you used a paint that would seal as well as decorate the walls.
They were always quick to point out the flaw in any poly installation being the multitudes of perforations due to the drywall screws etc. but failed to recognize the role that the poly played in the total assembly of the wall sandwich.
The problem with most high efficiency homes that are super sealed and depend on some form of heat recovery ventilation is that at first you do have a healthy environment for the occupants BUT because the same may not be true for the building itself, in time you have problems that start to surface long after the warrantee periods have expired.
The challenge is not to make a super sealed house but to create healthy construction practices. Any fool can seal a house but few really take the time to think out what actually occurs in a house during the changing seasons, freeze thaw cycles, wet dry periods or even the sometimes drastic temperature changes, never mind lifestyle considerations.
Our houses, given present construction costs, should live as long as the mortgage in a as new condition without having to worry about it falling down around you.
I believe in the basic premise that you don't screw with mother nature. What can get wet should have the ability to dry equally as well.
Gabe
I'll attempt this response in as much a non-argumentative way as possible :)
....failed to recognize the role that the poly played in the total assembly of the wall sandwich.
The poly served the purpose of the air/vapor barrier, we've just moved that 1/2" inward and made it actually air tight, instead of full of holes that you cannot see, which was and still is a very valid point. The poly served no other purpose than the above. It is possible to create a good air barrier using polyethlene, its just far more difficult than using a sheet good such as drywall or plywood. We still use poly in certain areas where it is more effective, such as behind tub enclosures or behind stair stringers against exterior walls.
Our houses, given present construction costs, should live as long as the mortgage in a as new condition without having to worry about it falling down around you.
As will anything we build. In fact houses that were built with absolutely no air/vapor barrier what so ever have stood for many decades with no problems. In renovation work, i've changed dozens of sheets of plywood on the exterior of houses with poor air/vapor barrier and little or no air exchange inside the home. Rotten areas behind every outlet and along the bottom wall plates are very common in the humid area I live that has more freeze-thaw cycles per year than most anywhere. We decided years ago to move to a superior system where we have more control over the quality of the homes we build for our customers.
I believe in the basic premise that you don't screw with mother nature. What can get wet should have the ability to dry equally as well.
I still don't quite understand what you are referring to and how this relates to the differences in our building practices, would you care to explain? If you're referring to the wall cavity, then that would be why the wall cavity needs to be ventilated to the exterior of the building, this is usually accomplished by spacing the sheathing, or we drill holes above the soffit line and under window plates to ensure that any moisture remaining within the wall cavity, or that which escapes through a hole in the air/vapor barrier has a place to escape. If this is the case, i definitely agree with you.
Edited 10/11/2003 8:16:01 PM ET by SledBC
Because my fine feathered friend, I have no interest in discussing anything with you. I don't know who you are and I have on reason to care at this point in time.
You were the fool who first challenged me with your drivel and I replied in kind, now let's leave it at that.
Adios,
Gabe
Let's refresh...
Myself: In the houses I build I always leave less space under the bathroom doors than the other rooms so that the replacement air for the exhaust fan comes from the heating vent, usually located in the kick of the vanity cabinet, which has tempered, fresh air from the HRV, rather than stale air from the rest of the house.
Gabe: That would be a very dumb installation.
Myself: On another note, does anyone else here use ADA, airtight drywall approach rather than poly, which i find a real pain in the backside to install? Since I was certified in ADA installation about 8 years ago, I haven't used poly vapor barrier and don't miss it one bit either, I might add :)
Gabe: That would be another very dumb installation method. You must be from British Columbia. The land of the biggest building envelope failure in Canadian history.
Did I challenge you? No, but rather it appears that you were the one that started this BS. If you feel threatened, that is none of my concern, I was simply discussing this, as it is a public forum and you chose to make a scene. I hope the rest of the forum users are not as ignorant, and are more friendly and open minded than yourself. If you're too afraid to have an intelligent discussion i feel sorry for you, and whish it could have been otherwise.
Have a nice day.
If I may interject ssomething here -
I know that Gabe is strongly opinionated and quite blunt.
I also know that he always has a reason for saying what he says.
Therefore, if he were to tell me that something I practice and proposae is dumb, my first responce would be to ask why amd reason theories out. Maybe I would become more educated and maybe i would agree to disagree after the discussion was over with.
Your choice was to rekindle the flame by telling him he is ignorant in the next post.
Things went downhill from there, entertaining and enlightening the rest of us.
compare this to a young fisherman standing in the same stream as an old-timer. The youngster says, "I always add a live worm to to this triple fitzle red feathered fly" The old guy says, "That's dumb"
From that point, the novice has the choice o asking why live bait and flies should not, in the oldsters opinion, be mixed and maybe learn from a lifetime of lore - or of telling the old fart that he is ignorant because this worm does occasionally land a trout. The old fart isn't going to share knowledge with someone who's mind is already closed..
Excellence is its own reward!
Piffin, I am always as willing to learn from experience, most of my knowledge was learned from others as well as learning the hard way over the years through practical experience. I don't know Gabe from the rest of you except he has the gall to say the way I do things is "dumb" and backed it up with nothing. He contradicts himself within his own statements and truly acts in an ignorant, uneducated manner.
I know that the way we do things is prefectly acceptable, in fact superior to the standard methods in many ways. I never implied that the way gabe does things is unacceptable, in fact I stated that both ways can be done properly, its a matter of installation and quality of construction. I also made a point of stating the things with which I agree with him. And if you look back at my initial post, then Gabe's reply, its clear who is the ignorant one. I could care less how long he's been in the trade, if he doesn't have an open mind to new construction techniques, his experience is comprable to driving a 30 year old car, because "they just don't build things like they used to"....and I think we all know people who are that way. Either way, I know my trade, when the local medical clinic was built, they hired me to explain the Airtight Drywall Approach to 5 engineers since the architect specced the system for the building....I'm not a dummy. I'm always willing to learn from others but not if they are closed minded like Gabe. I'm sorry If you all respect him since he is a regular, but with me, respect must be earned, not demanded. I appreciate your comments and apologize if it appears that I created some sort of commotion here though that was definitely not my intention. I would much rather maintain a calm discussion of construction techniques and the advantages of each....that was after all my initial intention with posting :)
Nice to meet you all.
Nice to meet you too. I've learned a little from your side of this arguement.
But you are kind of wound up about it. Like a nun who thinks somebody violated her Mother Superior by lifting the skirts on her mother's posterior exposing to world view a rumpus inferior.
'course maybe I'd be wound up if it were me instead of thee
but itsnot.
Excellence is its own reward!
I don't appreciate being called dumb. Maybe my simple mind can't comprehend such things im not sure :D
Either way, its beautiful out here today, sunny, and fresh snow on the mountains, i still have some cap flashings to bend up to finish up the built in gutters on my house, so i'm going out to do that and put another coat of sealer on my stamped concrete sidewalks before the snow hits....then I'll be back in to argue a bit more :)
I see you're not done with your insults about me.
What made your statement dumb was that it was dumb. You may not be dumb but what you preached is dumb.
Typical of someone running with a concept, has no real understanding of what the big picture is and then gets insulted when he's not greeted with awe and defensive and whinny when challenged.
DF
Gabe
Challenged? Usually when you challenge someone you have something to back it up, not just saying "that's dumb".
I'm not running with a concept, I do whatever works best for each individual situation, I explained the reason I do things a certain way, you failed to do the same, in effect aren't you then the one blindly running with a concept? From my POV it's you without the real concept of the big picture Gabe.Either way I hope one day we can have a civilized discussion, you could start by answering my question in my previous post to youif you'd like, if not, no big deal.
OK, now....things to do :) Back in a couple hours :D
Hi SPHAUGH
I agree with your skepticism. I moved from the climate in Montreal to the wet coast in Vancouver and on the way passed through the praries in Winterpeg on the way. Each climate needs ventilation at different rates and humidity values during each season. We have had tremendous damage here due to moisture intrusion and rot with many design and technical goofs for water intrusion. Everyone is blaming someone else. Wood has to dry or be kept from getting wet! It is very simple.
Cheers
Mac
I think that I'd wait about ten years before jumping on that bandwagon. By then, the company will be bankrupt, the lawyers will be rich er and the increased mold claims on insurance will be the talk of the town
Excellence is its own reward!
Will it support/prevent mold growth? Can I spray stucco over it in North Carolina? Does it react with aluminimum window fins?
Fantastic, send me 50,000 sq-ft of it.
Will it support mold growth? No
Can you spray stucco over it in North Carolina? Well, sure, you could spray stucco over it anywhere for that m,atter, but you'd be spraying stucco on you inside wall.
Does it react with Aluminum window fins? If it's inside it can't. But I'm not sure I understand the question...Dan MorrisonOne happy assistant editor
Yes I have heard about the stuff...
An "energy guru" whom I recently had a conversation with mentioned it. He believes it is a great vapor barrier! He proceeded to 'plain the positives it has vs other barriers. He should know..
As for the price..he said it is abit "spendy" in comparison to other barriers, BUT..if you have cash and you're in an area that requires it, he said it's worth it.
Ahh, now I clearly see it was a misunderstanding on your part, re-read what I posted more carefuly.
In the houses I build I always leave less space under the bathroom doors than the other rooms so that the replacement air for the exhaust fan comes from the heating vent, usually located in the kick of the vanity cabinet, which has tempered, fresh air from the HRV, rather than stale air from the rest of the house.
A few points to clear things up Gabe, 1) I never said what I did was "better" or necessarily better in your situation. What I did say was that this is the way we do things as another option. 2) I never once stated that we installed a dedicated HRV supply duct in the bathroom, that WOULD be dumb since the HRV is not 100% efficient and the air would be mighty cool (especially if you were skrawny like me getting out of a warm shower, I do live in the north after all :) What I did say, was that the replacement air came rather than from under the door, through the heating system, which has tempered fresh air from the HRV (supplied through the heating system, usually dumped into the return air duct so that it can be equally distributed through the entire house. The furnace fan is running 24/7 on low speed when the furnace is not on for heating purposes). Exhaust air is taken through the HRV system in a dedicated manner as you previously stated, from kitchens, bathrooms as well as the laundry area (and any walk in closets for stale air to be exhausted) and supplied through the existing heating system to each individual room. 3)I never stated that there was an exhaust fan, but in most houses we install a large enough HRV that it can sufficiently exhaust the stale, humid air from the bathrooms. There is a 15 minute electronic timer installed on the wall in the bathroom that when triggered turns the HRV to high speed to exhaust a greater amount of stale air for that period of time, Getting rid of the bathroom fan and using the HRV in this manner makes it easier to provide a balanced system rather than possibly creating a negative pressure in the house by exhausting more air than you are replacing.
Now, rather than it being what I did that was "dumb" was it not what you misunderstood that was "dumb"? and in that case I do agree with you :) I would much rather have these types of discussions than the "youre dumb" type arguments which are completely pointless, wouldn't you? :)
Not having the bottom of the door gapped in a bathroom is still inefficient and therefore dumb.
As a matter of fact, you should have a grill installed in the door to ensure enough flow takes place.
Given that you claim to use the drywall as a vb adds to the need for flow.
Now about the other dumb idea.
The backside of standard drywall is celulose and mold feeds off a combination of celulose and moisture.
The most important line of defence from moisture is directly behind the drywall. You bring the drywall into the living controlled space where you can heat it, cool it AND DRY IT at will.
Leave the backside exposed to moisture and you have mold.
Spending money on a heat recovery ventilation system and not having a PROPERLY sealed home is money down the drain.
You have a very unhealthy home for your family.
Now you know "why" your plan is dumb.
Gabe
Here's a cool site from Minn. that you all may want to look at.
It's a real time temp. monitoring of a test house with a high efficiency Heat Recovery Ventilation system installed.
http://216.171.138.250/site/hrvlive.html
Gabe
just looked at the link. says it's pulling in 35 degree outside air, yet the outdoor temp is 15 degrees. how's that possible?
Because it's being filtered through a solar pre-heater before entering the house.
Gabe
Not having the bottom of the door gapped in a bathroom is still inefficient and therefore dumb.As a matter of fact, you should have a grill installed in the door to ensure enough flow takes place.
How is it inefficient if you're providing fresh air as well as exhaust to the bathroom? I would venture to say that is a far more efficient system than installing an exhaust fan and installing a short door. I know I would love to have a grille in my bathroom door so everyone in the vicinity can count the turds hit the toilet water, not only that but a grille in a door is a commercial style installation and not very architecturally pleasing IMO, and would never fly with my customers, or myself.
Given that you claim to use the drywall as a vb adds to the need for flow.
Once again your lack of knowledge in this particular installation is hindering your ability to comprehend. The paint becomes the vapor barrier, the drywall is simply an air barrier...hence the name air/vapor barrier :) Although the paint is also an air barrier, there are still small areas where the paint is not continuous and in these areas the sheet characteristics of the drywall will maintain a continuous air barrier.
The most important line of defence from moisture is directly behind the drywall. You bring the drywall into the living controlled space where you can heat it, cool it AND DRY IT at will. Leave the backside exposed to moisture and you have mold.
So are you saying your wall leaks? 95% of the water damage and mildew problems i've seen in wall cavities were a result of an incomplete air/vapor barrier, Using this system we have taken care of these problems, the rest is taken care of by correctly finishing the exterior of the wall/roof.
Spending money on a heat recovery ventilation system and not having a PROPERLY sealed home is money down the drain.
I agree 100% and that is exactly my point.
The backside of standard drywall is celulose and mold feeds off a combination of celulose and moisture.
Cel´lu`lose` n. (Chem.) The substance which constitutes the essential part of the solid framework of plants, of ordinary wood, cotton, linen, paper, etc.
The wood framing in your walls is also cellulose, where do you think the paper backing comes from? In effect your system has the identical problems to mine according to your theory, as mold/mildew can grow on wood framing just as it can in paper. Do you also disapprove of the use of cellulose insulation in walls and attics outside of the building envelope?It's no different than having the paper on the drywall outside the envelope as well is it? There would be far more surface area for unhealthy mildew to grow on in the cellulose insulation that on the backside of drywall and that has never been a problem in a well ventilated attic that I've seen. But if it was, either way its outside the building envelope so I wouldnt imagine it would provide a large health hazard to the occupants.
You have a very unhealthy home for your family.
You are wrong, my home is very healthy as are all the ones I've built. Once again you speak of something which you do not know. I live in a very humid area of the country, if anyone has seen moisture problems, mildew and water damage, I have. I've spent much time dealing with these things, repairing, installing ventilation systems in existing homes, etc, so its not like i'm just quoting you from a textbook with no backing.
Either way Gabe, I appreciate you actually attempting at backing your comments rather than just throwing "you're dumb" at me :)
Edited 10/12/2003 6:15:11 PM ET by SledBC
Edited 10/12/2003 6:21:05 PM ET by SledBC
You're still dumb and there ain't much I can do about it.
Too bad you're pawning your ideology off on your clients.
This folks is what is called a little knowledge being a dangerous thing.
Adios DF
Gabe
You're still dumb and there ain't much I can do about it.
LOL, I know you are but what am I.....:)
It's too bad you are so closed minded Gabe, if you can give an actual reason why the way I am doing things is wrong then i could respect that, the fact is, you can't, so name calling really won't get you anywhere. I am in fact not a dummy, and not an ideologist, oh well....my initial comment in regards to your ignorance has proven itself throughout this thread, I think i've answered you in a well explained manner with logical reasoning, and if you can't accept that there's nothing I can do, but I think you could learn something from this system of construction as it has many advantages.
I have one question for you though, how do you deal with living areas over unheated spaces, such as bedrooms over a garage? Where do you locate your vapor barrier? Do you install a sheet of poly first before you sheet the subfloor? I think you might realize that your construction methods really aren't that different from mine after all.
As Leghorn would say "your ears are flapping boy but you ain't listnening".
So why would I want to waste anymore time?
DF
Gabe
I hate when people can't admit theyre wrong, you still haven't made one valid point, you're right this is not worth wasting time over, especially for you, since answering my question is likely to prove me correct. Stubborn old goat you are.
You remind me of my father years ago....we were building 4 eight unit condos and he was doing the layout with batter boards and string lines, It took till the final foundation to convince him him to let us lay one out with the transit and scrap the darned batter boards, he admitted my way was superior, and we've done it that way ever since. Now I have an electronic theodolite that we use, its now even easier. Im guessing youre the batter board and string line type of guy....there's nothing wrong with that.
You've single handedly managed to ruin a discussion that was going to be as enlightning as entertaining.
Congratulations DF.
Gabe
You figgure? Read my first post, then your reply. It was you who ruined it. No matter, whats done is done.
For the record (and name calling aside) I found the debate educational.
Thanks, guys.
You're welcome :)
Yea, me to- I've got plenty to learn and appreciate the banter about different methods of construction. I didn't find it all that informative or entertaining until the methods were actually discussed a little though. Frankly, "That's dumb" was not very enlightening.
I appreciate Andy, Gabe and Sled all three for the genuinely useful information they posted. Now for the arduous task of personal research to see if I can figure out who's actually right. :-)>
Oh yea, welcome aboard SledBC. Been to the Tavern yet? You're gonna fit right in around here. In the interest of weighing the validity of your arguments, are you a "Liberal," "Conservative" or "other?" :-)>
(Don't answer that question - seriously) Kevin Halliburton
"I believe that architecture is a pragmatic art. To become art it must be built on a foundation of necessity." - I.M. Pei -
Trust me there's nothing to be had from the discussion so far.
All it did was confuse what Andy and I were debating and I sincerely hope that Andy comes back to finish.
ADA or Airtight Drywall Approach has been flaunted around here for 10 years and it's considered the lazy man's way of sealing a production house. The original concept that by only doing the sealing at the finish state of construction it would be faster and cheaper to do.
Which is fine for the builder developer but the maintenance is a pain to the home owner. Any cracks, shifts or even nail pops comprimise the integrity of the vb to a greater level than it would with conventional plastic vb.
In independent testing on partition walls and bathrooms in particular, it was found that the ADA scored lower than poly.
Even after 10 years of promotion, only a tiny fraction of new homes in Canada use this approach.
Another method which may be new to you is EASE Exterior Air System Element.
This uses a vapour-pervious spunbonded polyolefin paper between layers of pervious sheathing as an exterior air barrier.
Now that's a mouth full.
It's actually the most effective air barrier on the market todate. Least number of penetrations to seal and easiest to install effectively.
But it also does a wonderful job of trapping moisture and promoting mold.
My point is..................Sealing a house is not rocket science but understanding the long term effects is. It takes about 1 hours worth of instruction to use the ADA method or the EASE system but it takes lifetime of study to understand what happens inside an exterior wall of a common house.
A square ft. of drywall can have 300 million spores or more munching away happily. Health Canada is concerned about the long term effects of this hidden hazzard and is presently conduction surveys on new homes.
PH's like Sledbc can afford to give poor advice, they don't put their name or reputation on the line. If they screw up, they simply start again under another name. The dumb part was not undercutting the bathroom door to allow ease of air flow and this is also crucial with an HRV system as well. You never feed the areas that produce the contaminates, you exhaust them as quickly as possible. Trying to keep a bathroom snug only makes the total system ineffective. You have one air pressure flow with the door open and a different one with the door closed. Makes balancing a waste of time.
Gabe
it takes lifetime of study to understand what happens inside an exterior wall of a common house.
I hear you there. A thousand variables per square inch can change the equation on every job too. Insults aside, this thread has gone a long way toward helping me think more like a vapor droplet looking for the weak link in all the barrier methods.
EASE and ADA are both new ones on me, as SIPs were a couple of years ago. In the interest of contributing what brain matter I have to the public forum, I intruded on your discussion with SIP's much like SledBC did with ADA. Andy was gracious enough to give a little useful feedback and the primary reason he isn't comfortable with SIPs yet. Who knows - it might have been the first time someone on this public forum heard about SIPs too.
Those of us challenged with knowing what the heck we are talking about when the specs and drawings go out the door can benefit immensely from discussions and debates between those of you with long term building experience.
That last post at least had some real meat mixed in with the insults. Beat the heck out of "that's dumb." Thanks...Kevin Halliburton
"I believe that architecture is a pragmatic art. To become art it must be built on a foundation of necessity." - I.M. Pei -
As I stated in the beginning, I'm taking the role of a Devil's Advocate in this thread and as you know, the role involves making others learn by thinking instead of simply pointing out answers.
Gabe
Sigh Gabe...haha...
ADA or Airtight Drywall Approach has been flaunted around here for 10 years and it's considered the lazy man's way of sealing a production house. The original concept that by only doing the sealing at the finish state of construction it would be faster and cheaper to do. Which is fine for the builder developer but the maintenance is a pain to the home owner. Any cracks, shifts or even nail pops comprimise the integrity of the vb to a greater level than it would with conventional plastic vb.
I'm going to disagree with you once again here, the amount of work involved in properly sealing an ADA house is no more or less than doing one with poly. A lot of the problem areas are still dealt with in the same manner as with poly, but its a lot easier to know when it's done correctly with ADA. It has nothing to do with faster/cheaper, by the time i buy and install gaskets, electrical boxes, and the correct primer, the actual costs are quite similar if not greater than poly.
As far as maintenance goes, you could have 50 nail pops in an ADA house and that wouldn't even come close to adding up the air loss from one vertical corner in your poly being sliced by the drywallers, or a couple incorrectlly sealed up electrical outlets, the difference is the homeowner will actually do something about the nail pops.It takes about 1 hours worth of instruction to use the ADA method
HAHA now that's a laugh. Although it is definitely not rocket surgery, I took a 40 hr course that covered ADA as well as a few other things.
PH's like Sledbc can afford to give poor advice, they don't put their name or reputation on the line. If they screw up, they simply start again under another name. The dumb part was not undercutting the bathroom door to allow ease of air flow and this is also crucial with an HRV system as well. You never feed the areas that produce the contaminates, you exhaust them as quickly as possible. Trying to keep a bathroom snug only makes the total system ineffective.
Give me a break, we've been building top quality homes here since 1970 under the SAME name and are not planning on changing anything anytime soon. Your bathroom argument is retarded, if fresh air is supplied to replace the exhaust air it makes no difference whether it is through a supply duct or an unsightly gap under the door. The fact that you would criticize that is quite lame IMO. You talk about a balanced system then say that you should be able to suck a sheet of paper under the bathroom door, doesn't sound too balanced to me.
In independent testing on partition walls and bathrooms in particular, it was found that the ADA scored lower than poly.
OK that is a meaningless statement if you don't explain what the test was regarding, airtightness? I'm quite interested in reading this study, do you have a link?
I think it's quite obvious Gabe that you have made your mind up in advance and it's your way or the highway. Is there a reason you keep dodging my questions to you? I'd really like to know what the difference is between my method and yours that makes my method so "dumb" and unhealthy.
1) "How do you deal with living areas over unheated spaces, such as bedrooms over a garage? Where do you locate your vapor barrier? Do you install a sheet of poly first before you sheet the subfloor? "
2)"What's the difference between me having the paper backing of my drywall outside of the VB while you have wood framing and/or cellulose insulation outside of yours? All 3 can promote the growth of mildew if not ventilated properly. Is there a problem with having cellulose insulation in your attic, outside the building envelope?
Edited 10/13/2003 11:50:26 PM ET by SledBC
By Golly, are you two still gnawing on each other's tails?
I was impressed with the way Wrecked angle did what he always does - elevated the tone of the discussion - but this is starting to make me dizzy to watch you go round and round.
it is a fun thread though
As you were.
Excellence is its own reward!
Hey piffin not trying to go circles....i seriously would like to know what this guy is thinking here, thats all....I don't appreciate the personal attacks but rather than get all pissy back at him, Im just trying to have a civilized discussion. It seems rather difficult with this guy though, I love how he dodges questions that he knows the answer to, stubborn old bastard.
If I'm wrong, I have no problem admitting it, but to have someone imply that I do crappy work and basically rip of my customers is uncool.
First of all, I'm sorry about not seeing where SIPs were mentioned previous to my piping up.
Second, it's great to see builders who are so thoughtful and smart about these hard to understand subjects.
BUT... ADA was never meant to be a vapor barrier. Only an infiltration barrier. It accidentally becomes a vb if a good semigloss paint is used. Water vapor can easily cruise through drywall and flat paint. Poly sheet in theory could be a vb, but in practice it's not very good at stopping vapor or infiltration. So for the same reasons, this new high tech stuff is nearly worthless too. Tyvek, being on the outside, is an OK infiltration barrier, but to stop the vapor, you must do something else in addition to the Tyvek. Therefore, Tyvek is useful only as a moisture barrier. Tarpaper does the same thing much cheaper.
And the whole climate thing..... even if there were a "best practice" for the different climate types, it's too hard to figure out which region you're actually in! There's cold weather in parts of Florida, and muggy weather in Arizona, hot weather in Minnesota. Compromise isn't acceptable when it comes to water inside the walls.
So again, forget the whole argument and use Icynene or SIPs. With these, you at least have a chance of stopping the migration and condensation of water vapor.
Since I skimmed over all the mudslinging, I hope I haven't restated the obvious again.
Tarpaper does the same thing much cheaper.
Except for your some of your comments about foam, most of what you said wasn't all that accurate.
I highlighted your comment about tarpaper or felt paper or construction paper because in independent testing on wall assemblies, those with paper on the outside scored much higher than any other regarding water/vapor infiltration.
The conclusion was that the perm rate of any material making up a wall assembly had to be considered in judging the effectiveness ot the assembly as a whole.
Gabe
Oh heck. I was hoping I could just end the discussion and everyone could go back to work and their families. Totally unrealistic.
I highlighted your comment about tarpaper or felt paper or construction paper because in independent testing on wall assemblies, those with paper on the outside scored much higher than any other regarding water/vapor infiltration.
The conclusion was that the perm rate of any material making up a wall assembly had to be considered in judging the effectiveness ot the assembly as a whole.
Gabe,
I couldn't agree more with your last comment. If you have a link, or can point me to a reference where I can take a look at the particular studies you are referring to, I would sure appreciate it.
I would go so far as to say that lab tests are great - they help determine a lot of things - but, IMHO they rarely reflect the "true" performance of any given material in actual use. While it's a pretty unrealistic way to test products going to market, the only way to truly test exactly how anything will perform in a "whole assembly" is to install them in a complete structure, that is being used on a daily basis, and track their performance over a period of years.
Of course, every product has to have a "first time it's ever been done" point but it's sure a lot easier to trust the ones that have worked for a long time without fail. The flip side of that is that if you only do what you've always done then you'll only get what you've always got and, for a lot of reasons, "what we've always got" is no longer adequate for the long term survival of our planet.
That is especially true as far as energy wasted through leaky construction goes. Of course, if we "fix" the wasted energy problem with throw away buildings, we really haven't accomplished much. For all our advancements we sure don't seem to be "making them like we used to." Moldy houses is just one example where the cure has ultimately proven far worse than the ailment we were trying to address.
FYI for All:
Here is a link to a well known independent lab for anyone interested in how the tests to achieve AAMA, ASTM, UL and other certifications in various categories are conducted http://www.archtest.com/pages/pertes.aspKevin Halliburton
"I believe that architecture is a pragmatic art. To become art it must be built on a foundation of necessity." - I.M. Pei -
Wrecked, I think you have a pretty balanced view of this topic. I agree with you 100%, a lot of problems stem from individual products being developed which have no problems on their own, but stack a few of them together and you could easily create a problem.
As far as vapor barriers are concerned, I don't think it matters at all which system you use, if you don't consider the building as a unit and deal with the problems sealing a house up will create, you are taking a step backwards rather than forwards.
At the time of testing the focus was on a report regarding various residential sidings as a rain screen and in testing a dozen wall types in a wind tunnel, some of the walls had felt paper and tested much better than those with other wraps.
They were more interested with the gap or compartments between some siding products and the actual wall framing. So the felt paper effect on the final numbers was more of a side note than anything else.
WH did the testing for the National Research Council.
I tend to agree on the real world testing of products as opposed to lab testing but it does bring up interesting aspects to wall construction.
I'll try to dig up the report and link it later.
Gabe
Haven't found the right report yet but here's one that you can read and take from it what you will.
http://www.cmhc-schl.gc.ca/publications/en/rh-pr/tech/96214.htm
The final closing paragraphs make an observation about felt paper. In all the walls tested in this report, all had construction paper. The other, larger study had a mix and I will endeavor to find it.
Gabe
ADA was never meant to be a vapor barrier. Only an infiltration barrier. It accidentally becomes a vb if a good semigloss paint is used.
The low perm latex primer we use is an amazing vapor barrier, this was how the system was designed, it is no accident that it is an effective vb. In fact I once primed a garage ceiling with it, then later had a flashing leak on the roof. The paint on the ceiling where the water leaked in formed an 8" round baloon of paint, not a drop of water leaked in until i poked it with a nail :) Now if that's not an effective vapor barrier i dont know what is.
What primer are you using exactly?Kevin Halliburton
"I believe that architecture is a pragmatic art. To become art it must be built on a foundation of necessity." - I.M. Pei -
I'll slip out of my advocate's robe for a minute and share a little information with my brothers.
You've all heard or done the standard poly test on a concrete slab to detect moisture.
That's where you take a 12 in. by 12 in. piece of poly and duct tape it to the floor and you wait 24 hours to see if droplets form on the underside of the poly.
Now I want you to picture doing the same thing with a piece of drywall.
If moisture wicks up from the concrete and beads on the underside of the drywall, how long before you start seeing moisture stains and eventually find mold on the drywall?
That's what would be happening "behind" the sealer on drywall if you don't have some form of vapour protection and it's only a matter of time before it starts to affect the occupants of a home.
I never took a 40 hour course to learn how to paste a gasket on a stud but I do know my craft and I have seen 40 years of products and ideas. Some work and some don't. This one is dumb.
Gabe
You make a valid point Gabe but since the VB will always be the point of condensation, what keeps the vapor from inside the home from condensing and being trapped between the VB and the back side of the drywall in the same way? (Just thought I would give you a path back to your original point of debate with Andy - which side of the wall produces the condensation in various seasons and climates) I can see some benefit in taking pains to seal both sides of the drywall on an interior side VB at this point.
Also, I'm about ready to shoot for dry-in and plan to wrap the outside of my SIP shell as a protective measure for the OSB. I will have a 2" air gap between the SIP and the masonry veneer on the first floor and fiber cement lapped on furring strips upstairs. I want to shed any infiltrating moisture in the air gaps to the weeps in the veneer without creating a nice mold culture environment between the wrap and the SIPs. I've got a stack of wrap samples and glorifying literature on my desk at the moment. Do you have a favorite one-way-breathable membrane or another suggestion for this application?
I'll appreciate weigh-ins from others on this as well.Kevin Halliburton
"I believe that architecture is a pragmatic art. To become art it must be built on a foundation of necessity." - I.M. Pei -
In spite of what some may think, I do believe in HRVs in homes but I would still use bathroom exhaust fans as well as kitchen exhaust fans.
With regards to house wrap..........Use felt paper instead of house wrap. It's the newest discovery of an old product that still out performs anything out there.
Behind masonry you want a space. Behind most other sidings you don't. Masonry has a perm rate of about 10 and that let's in a lot of moisture so you want space between it and your wall face. I'm a little naive about your cement board regarding it's perm rate so if it's high like other masonry products, you want space as well, so your furring is good. If the siding you use has a lower perm rate you can and should do without the furring.
Normally, creating compartments between your rain screen and your walls is not a good thing to plan for. Unfortunately the wind pressure inside the cavity will quickly match the outside and that will cause all kinds of possible problems.
Gabe
Well, I'm a felt fan myself. It's nice to finally hear someone not trying to talk me out of it. The primary reason for the furring behind the Fiber cement is to create a stronger attachment for the siding to the SIPs. Thanks for your feedback.Kevin Halliburton
"I believe that architecture is a pragmatic art. To become art it must be built on a foundation of necessity." - I.M. Pei -
If moisture wicks up from the concrete and beads on the underside of the drywall, how long before you start seeing moisture stains and eventually find mold on the drywall?
That's what would be happening "behind" the sealer on drywall if you don't have some form of vapour protection and it's only a matter of time before it starts to affect the occupants of a home.
Gabe, I understand your point of view to a certain extent, but once again, what is the difference between cellulose insulation, wood framing, and the backside of a sheet of dywall all being in the wall cavity outside the vb? If you actually do the quality job of installing your felt paper (which i also agree with you on, though most customers insist on housewrap since it has become a standard as of late) then you shouldn't have to worry about anything inside your wall cavity growing mildew. Also, your concrete/poly theory makes no sense, unless you are installing a vapor barrier on the outside of your wall cavity. Put that same sheet of poly down on concrete but instead of taping it to the floor, leave the edges free and ventilate the space, that would more closely exemplify an exterior wall, and no condensation would form on the underside of the poly.
I never took a 40 hour course to learn how to paste a gasket on a stud but I do know my craft and I have seen 40 years of products and ideas. Some work and some don't. This one is dumb.
You still haven't given one valid argument proving there is anything wrong with ADA what so ever, so saying it doesn't work when I know for a fact that it does is not an educated comment.
You have to first appreciate that I have little time for people who claim to be contractors selling another concept or half baked theory.
Remember this one point, houses were being built and built well for a long time before you were born. ADA is not proven by any stretch of imagination to be better or even equal to poly. It's just another sell.
It's up to you to prove your point. Show me the WH study or any JW reports on ADA supporting your claims and we'll go from there.
I will gladly spend all day helping someone who needs it but I've already wasted to much time on you.
I've got nose hairs to pluck.
Gabe
Gabe Martel,
Two points:
"If moisture wicks up from the concrete and beads on the underside of the drywall, how long before you start seeing moisture stains and eventually find mold on the drywall?" Depending on the amount of moisture in the concrete and the temperature of the drywall, condensation may not occur. For one thing, drywall is not a vapor barrier like poly; it is far more vapor permeable. If the drywall has been painted with an oil-based paint, or three or four coats of latex paint, it becomes less permeable, of course. But drywall with one or two coats of latex paint is permeable enough to allow it to dry to the interior in many circumstances.
Second point: "ADA is not proven by any stretch of imagination to be better or even equal to poly." ADA is a technique for creating an air barrier, not a vapor barrier. Most people who install poly are installing it as a vapor barrier, for good or ill. Poly as typically installed is not particularly good as an air barrier, although techniques exist to use poly as an air barrier. These techniques, however, involve mastics, glues, tapes, gaskets, and airtight electrical boxes, and guess what -- these techniques are very similar to the ADA techniques. No ADA proponent that I am aware of promotes ADA as a vapor barrier. Good air sealing techniques are important, but an air barrier can be installed at the sheathing, behind the dyrwall, or continuous with the drywall. But ADA is not trying to compete with poly.
Martin Holladay
I can't figure out the purpose of your post.
I don't know if you're agreeing with all that I've said, trying to set me straight on what I already know or just putting in your 2 cents worth.
But because your post was directed at me I'll simply say............okay fine.
Gabe
It's up to you to prove your point.
And I think I've accomplished that to a certain extent since you refuse to answer my questions which would prove me right. Every problem you've mentioned with ADA I've answered, or asked you how that differs from the poly system and you've refused to reply. Every argument you've put forth is a shot in the dark. Just because you're old doesn't mean you're right. You've made up your mind in advance that I'm wrong and there is no convincing you otherwise, that doesn't however mean that I'm not right.
Either way, Its a shame you don't have an open mind, or a valid argument. I'd much rather discuss this with you but since you've "wasted too much time" calling me dumb, i guess that's not going to happen.
I don't know your level of comprehension but this outa keep you busy eating crow.
http://www.morrisonhershfield.com/papers/MDLPoly.pdf
Always ready to hand over the salt.
Gabe
Good read, I don't think you have anything to gloat over, since if you look, they are comparing no vapor barrier to poly, or standard paint to poly. I'm going to see if I can find the perm ratings on the VB paint we have been using, but if my memory serves me correctly it was around 50, with poly being around 15 and raw drywall being around 3000. The advantages of being able to provide a much better A/VB with this system was enough for us to start using it.
I've seen horrible mildew on drywall where there was a hole in the poly behind it, usually in upper corners of ceilings like are showed in the pictures on that article. Often its also partially caused by poor insulating near the outer walls in the attic. I have never had this problem in one of our homes, whether using poly or ADA. I'll note that when we do ADA, we always apply the VB primer to points past the areas requiring the VB, to make sure we don't have those specific problems, eg. almost all the cutting in is done with the VB primer.
I'm going to print it out so I can read it more closely, while I do that, why don't you answer the questions I've been asking you all along that you seem to be dodging?
Hey guys check this out: http://www.proctorgroup.com/proctor.asp?op=products&top=14&left=71 & http://www.proctorgroup.com/proctor.asp?op=whatsnew&top=30&left=347
The same product is marketed here http://vmzinc-us.com/additional.htm as an alternative to Vycor, with the ability to be left exposed for 3 months. Anybody used this stuff? Anybody care to offer their thoughts? I'm sure you can't resist, Gabe!
I've been told that using Vycor on a roof with fiberglass insulation below is asking for trapped moisture troubles.. and this product's ability to breath supposedly eliminate that problem....
Onward!
Edited 10/16/2003 9:37:19 AM ET by SPHAUGH
Nothing to say. Just another product competing with tyvek and I still like felt better.
Unless you're planning on erecting a steel structure, I don't even know why you would consider this product.
Gabe
Hello all,
new to the site, presently renovating a 1928 schoolhouse outside Ottawa. Your thread has been intriguing and informative but I would like to pose a more specific question...how does one deal with sealing an old balloon-framed structure...brick veneer, tar paper, half-lap planking, 2x4 studwall, half-lap planking and plaster? I am looking to blow in cellulose from the attic, patch some of the plaster but in most places cover broken plaster and exposed lathe with drywall. "Vapour barrier" paint seems to be an attractive option...ceiling is to remain intact as it is 12' up and already has an inch of plaster and 3/4" T&G hanging off doubled 1x6 ceiling joists
What you're proposing is like putting a new bandaid over an older one. It doesn't get to do anything worthwhile.
There is only one way to renovate one of the old schoolhouses in our area. Strip the inside out completely.
As messy as it sounds, get rid of that old horse hair plaster on the walls AND ceiling before a chunk falls on someone and hurts them. Not one wall at a time, the whole thing at the same time. Back up a dumpster from one of the local suppliers and fill the puppy up. One weekend and it's done.
Now you have a dry roof over your head and you can do the renovations as money and time allow.
This will allow you to check out the electrical wiring to make sure that it's safe and you can update any that is not.
This will allow you to check the "real" condition of your new home's framing and you can repair or replace any wood that is not sound.
This will allow you to properly seal around doors and windows.
This will allow you to "choose" from a variety of insulation options. Foam would be my first choice. Give Quicksilver a call for a quote. Foam will seal and insulate in one application.
With your house warm and cosy this winter, you can install drywall at your leizure and finish the trim as conditions dictate.
Good luck
Gabe
OK, I'm convinced. Now, what do you do at the electrical outlets?
Now, what do you do at the electrical outlets?
We use a sealed electrical box with a 1/2" gasketed flange on it, the wires penetrate a neoprene seal then are caolked afterwards. The box is airtight and 2 screws are put in the drywall to sandwich it to the box.
About the primer, Wrecked Angle, I've used 2 kinds, glidden used to make one called insul-aid, then we started speial ordering the same thing from benjamin moore....i forget the actual name but the tag read "vapor barrier paint" and then a #, I would have to go look at a pail to tell you exactly.
Edited 10/14/2003 9:26:08 PM ET by SledBC
Let me welcome you, too, Sled. You've certainly earned your red wings.
In any debate, the first person to resort to an ad hominem attack is the loser, IMO. And when participants continue in attack mode like we've just witnessed it just results in a great number of people tuning out and going away, never to return.
...it is definitely not rocket surgery...
rocket surgery - LOL! I love it! Got a new smart-alec comment out of this discussion too. Lord knows you can never have too many of those.
Mind if I swipe that one for my repertoire Sled?Kevin Halliburton
"I believe that architecture is a pragmatic art. To become art it must be built on a foundation of necessity." - I.M. Pei -
...it is definitely not rocket surgery...
rocket surgery - LOL! I love it! Got a new smart-alec comment out of this discussion too. Lord knows you can never have too many of those.
Mind if I swipe that one for my repertoire Sled?
Feel free, I think I stole it somewhere myself years ago :)
Wow, I step away for vacation & seem to have missed a sheet-storm over here.
To all: I'm still interested in Certainteed's MemBrain & this new discovery: http://pactiv.com/green-guard/ A "draining" exterior sheet product. hmmmm
Also roofshield from proctorgroup of Scotland looks quite interesting - a roofing subcontractor is recommending that we use it on my golf house project. http://www.proctorgroup.com/proctor.asp?op=products&top=1&left=32
Seeking comments on any/all.
I'm still curious about everyone's opinion on my project with 12" light gage stud roof with 10.5" batts/1.5" air space (ventilated soffit & ridge) with poly VB @ bottom flange. Can't afford Icynene on this one.
Lastly: Gabe, please tell me your recommendation for a typical exterior wall - kinda like Joe L has done at http://www.housesthatwork.com Assume: stud wall framing, not SIP. Qualify any way you like.
Thanks,
Scott
Aw the ultimate cold climate house. That elusive dream.
First..........any siding you want, even vinyl.
Next.......a good quality felt paper (because of it's perm rating), overlapped horizontally bottom to top, don't bother to wrap at the windows/doors. Terminate nice and neat. Use window and door jambs that have an exterior brick molding and tape the exterior tight.(foam in the window and door jambs later) Double overlapped at the corners.
Double 2x4 stud walls. One directly on the foundation wall (fully insulated with whatever you want, no breaks or interuptions) and the second up on the deck (also insulated) with a 1 inch gap. Exterior wall with conventional framing, double top plate and full structural. Interior wall with single plate, 24" spacing, window and door opennings framed like standard interior headers. (2x4 only)
Window and door opennings boxed with 5/8 PT plywood to RO dimensions.
Use poly vb with full acoustical caulking and all penetrations sealed to R2000 specifications.
Drywall.
Of course if it were mine.............
Use PUR foam, forget the second wall, frame with 2x6 and forget the vb.
Gabe
What is your opinion of Icynene? Does it eliminate the need for vapor and air infiltration barriers? How does its cost compare with conventional wall insulation?
Thanks,
vlperk
Most foam installations still require a layer of paint in order to achive a level 1 vb rating but I have trouble with this one. I think that 3 inches of PUR or Icynene would be a sufficient air and vapour barrier on it's own.
Beats the crap out of most other insulation.
Most of my projects include PUR foam insulation somewhere.
Gabe
hey all,
now that my interest is certainly piqued, can any of you recommend any books or websites that explain some of this stuff in more detail? i would certainly like to look into this more.
thanks up front,
brad
Hey, why would you go anywhere else for answers? You may learn more but you'll never have as much fun. :-)>
Seriously, there are a couple or three very sharp cookies in this thread. I'd be interested in knowing some of the resources, in addition to your vast experience, that you fellers have used in reaching your respective conclusions too.Kevin Halliburton
"I believe that architecture is a pragmatic art. To become art it must be built on a foundation of necessity." - I.M. Pei -
this is considered the best source http://www.housesthatwork.com/
And if Joe L has any mistakes, the guys on this thread are quite experienced.
Oh yea, welcome aboard SledBC.
Thanks, It's nice to know someone welcomes me :) Actually piffin did as well. Either way hello to all of you too.
Oh, BTW, you can check me off under "other" ;)
I agree with Wrecked Angle too, this conversation has caused me to refresh myself on the reasons we use ADA and how the building envelope works. I also am not overly familiar with EASE system and wouldn't comment on it either way until I was better informed. If it really is just a 1 hour course though as Gabe said, sign me up, sounds interesting :)
Edited 10/14/2003 12:00:04 AM ET by SledBC
Your vapor barrier is rated at 15, mine is rated at 50-60, an unprotected wall is rated at 3000, anything under 100 is considered an effective VB for all intents and purposes. Yours probably has some holes at key locations, though you can't be sure, mine doesn't. If you're worried about the back of the gypsum being exposed to the wall cavity, what about the cellulose insulation or the wood framing?
I understand the concerns over mildew forming on unprotected gypsum, but you must agree that this mildew is caused either by improperly installed vapor barrier on the inside, or improperly installed flashing/siding/housewrap/felt-paper, or simply a poor exterior finish.
Your article is referring to systems with leaky or NO VB whatsoever from what I can see in the quick read I've had so far. I will have another read over it.
One thing i have learned here is that 1) you are too scared to answer simple questions that you know will upset your theories, and 2) you are very rude.
I think the conclusions of the article are very much in favor of using poly behind drywall regardless of other construction details. However, this study is mostly based on computer modeling, so you need to buy into their computer model and the parameters they have selected for the three cases. Vancouver, BC, is a Mediterranean climate, which means generally warm dry summers and cool wet winters, and their chosen parameters tend to reflect this type of climate.
My reading of the article is that they say that most of the moisture that creates problems in their model is forced in through the siding and the insulation and condenses on the back of the drywall. I didn't see that they said there had to be poor construction practices for this to occur. They seem to indicate that the paper on drywall is particularly conducive to mold growth.
My impression from their studies is that under the conditions they have set, that using more moisture resistant interior paint would simply trap more moisure on the backside of the drywall rather than letting more of it penetrate through to the interior.
Edited 10/15/2003 10:12:06 PM ET by CaseyR
Alot of those pictures had poly in the wall construction, and the steel and wood framing was horribly water damaged. There is no way that is normal, proper construction. Our summers are similar to vancouvers, but our winters are colder and wetter, and the only walls I've seen like that are either from a horribly leaky vapor barrier, or leaky siding/window flashing etc.... or those 40 year old houses with a window in the bathtub....;)
My point is, if you put poly in your wall is it all of a sudden acceptable to have rotten framing like in those pictures? Or what about cellulose insulation? it has far more surface area than the back of a sheet of drywall and is made of the identical material. Having poly or not is irrelevant...having a proper vapor and air barrier is, no matter what it is made of or what side of the drywall it is on. And its a heck of a lot easier to create an effective air AND vapor barrier with the ADA system than it is with poly.How do you deal with a floor or overhang over unheated area such as living area over a garage? Do you install poly before you sheet your subfloor? My guess is that alot of your construction techniques are identical to the ADA system, but with absolutely no vapor barrier.