How long should it take to frame a house? For example it takes our best crew of four 3 weeks to build a 3,000 Sq Ft two story house and it took another crew of 6, 6 weeks to build the same house. Needless to say the the foreman of the 6 man crew got fired. was this to harsh
Discussion Forum
Discussion Forum
Up Next
Video Shorts
Featured Story
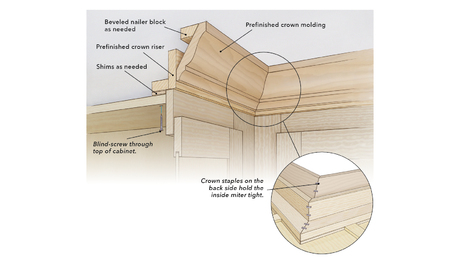
Use these assembly techniques when installing crown risers and molding to minimize visible gaps and nail holes.
Highlights
"I have learned so much thanks to the searchable articles on the FHB website. I can confidently say that I expect to be a life-long subscriber." - M.K.
Fine Homebuilding Magazine
- Home Group
- Antique Trader
- Arts & Crafts Homes
- Bank Note Reporter
- Cabin Life
- Cuisine at Home
- Fine Gardening
- Fine Woodworking
- Green Building Advisor
- Garden Gate
- Horticulture
- Keep Craft Alive
- Log Home Living
- Military Trader/Vehicles
- Numismatic News
- Numismaster
- Old Cars Weekly
- Old House Journal
- Period Homes
- Popular Woodworking
- Script
- ShopNotes
- Sports Collectors Digest
- Threads
- Timber Home Living
- Traditional Building
- Woodsmith
- World Coin News
- Writer's Digest
Replies
You're kidding, right?
Whoever is in charge (is it you?) should have been able to see the wreck that was happening on the large-crew site, after just a few days of work.
To have waited until the end for redress, and to spend three times as much on labor, is ridiculous.
Who dealt this mess?
Seems like a lot of possible variables here for a simple answer. Were the carps on both crews equally experienced? Were the 6 guys a bunch of kids with a grumpy lead carp? 1 Larry Haun = 5 common guys. Maybe the crew of three cut a few corners. Seems easy to blame the super from a distance, and of course he/she is ultimately responsible and it probably could have been caught early on, but something obviously doesn't add up.
Gene,
I tend to agree with you. A crew of 6 on that type project suggests a lot of un/simi skilled people standing around waiting for someone to tell them what to do. Maybe 4-6 people on big lift days but 3-4 otherwise.
My best crews were 5 on big lift days; 1 lead, 2 highly skilled, 1 good nail driver & 1 trainee. Then only 3 for close in.
I don't see how anyone can supervise large crews of mostly nail drivers and keep the labor cost under control, especially on custom plan projects.
Jim
I'm tempted to say that you're both too slow but, without seeing the prints, that's not fair. Got prints? Photos?
Where was this kind of job when I was subbing framing?
Your first crew probably made good time on that house. Depends on the complexity, of course, but it's in the right ball park.
Now this six man crew..... did this foreman get all the 'left overs' from the first crew? Could you have built that house much faster with the talent he was given to work with? It takes more than just a good cook to make a nice meal. He's gotta have some decent groceries to start with.
And was this his first house for you? It can take awhile to get some chemistry with a crew. That's why I try to not rock the boat unless it's absolutely necessary. My crew and I are always a bit out of rhythm for a job or two when I make changes to the crew... and I'm the foreman. So throwing a foreman in with a crew of six he's never worked with before can take some adjustment time. How much time is acceptable is debatable and probably has too many variables to figure out over the internet.
I think you've hit the nail on the head (haha) as far as chemistry goes. The framing outfit I learned from had 3 or 4 man crews, everybody knew thier job, not a lot of talking, steady pace, 2200-2400', 8-10 days. (platform frame, conventional lumber, hand-cut roof, roof only, no windows, no backframing.) Since then, I have taken on projects myself, but have never been able to match that production simply because I didn't have "real framers" working with me. Most carpenters think they can frame, but nothing matches a real crew that knows how to work together.
I no longer blame myself.
What's a telehandler?
Like a Lull or Skytrack Mike.
View Image
View Image
hh, thank you. Did you enjoy JLC?
Were the sites comparable? Did the slower crew have to spend more time than usual humping lumber? Large, deep overdigs that limited access to the decks?
Granted, 4 men/3 weeks vs. 6 men/6 weeks is a big discrepancy, something had to be different.
Its been 25 years since i worked on a framing crew, We did colonials, bilevels.splitlevels, I think 4 to 7 men, 7 days, frame sheet hang extdoors windows, drops for the kitchen,But the same houses but no nail guns. No trusses but no 9foot walls either, All roofs common rafters. I thought we did very good but i dont know how i would do with all these cut up houses nowadays.
ebuilder,
I'm glad you bring this up.. I watch contractors fairly closely to determine who gets a loan and who doesn,'t.. It's not just credit worthiness that gets them the loan, I've made loans to some pretty marginal characters, guys with credit scores in the 500's and even lower.
IF I get there at 7 am and the crews are busy and working efficently that scores a great deal with me.. Conversely If see one or two guys working while the rest of the crew takes time to BS, smoke, or grabasz that guys credit score better be well over 700.
The best crew I ever saw was a father and two sons who could build a two story 2400 sq.ft. house in 4 days and have it pass inspection without note the morning of the 5th. Buy that evening the house was roofed with shingles and windows and doors were on.. People could often move in during the middle of the 3rd week.
They didn't work hard but steady and they knew exactly where to put everything. (they only built 4 plans and evn though measuring tapes stayed mostly in their pocket and levels were untouched the houses were plum level and tru and passed framing inspection without note by the morning of the 5th day.. They started at 7 am and finished exactly at six.
In the 5 years since I watched him and his sons, they went from some down and out without even a permenant residence and a credit score right at the bottom to having 7 figure bank account and each owning their own home free and clear..
The best crew I ever saw was a father and two sons who could build a two story 2400 sq.ft. house in 4 days and have it pass inspection without note the morning of the 5th
They'll inspect the framing before the HVAC, plumbing, and electrical is roughed in? And further, you can't even start plumbing and electrical rough ins until the house is weather tight..... roofing installed, house wrap installed, windows/doors installed. At least that's how it is in MA anyway.
People could often move in during the middle of the 3rd week.
2400 sqft.....2 1/2 weeks.... frame to finish? That was the norm? Sorry Frenchy... I'm having a tough time buying that.View Image
dieselpig,
differant locations differant rules.. Framing inspection seperate from all other inspections here in Most of Minnesota. we get (depending on location) footing inspection, foundation inspection, framing inspection, wiring inspection (state NOT local), plumbing inspection (local not state) , HVAC inspection, insulation inspection, etc..
plumbers/HVAC who hack up framing members beyond code are required to repair their own errors or get the framer back in on their nickle.
dieselpig,
More typical would be about two to three weeks to frame 2400 sq.ft. Most framing crews aren't very efficent, lots of looking at plans, scratching heads, chaulk lines laid out, tape measure, level work, wood not stacked properly in the first place, not efficent use of telehandler, wood being double or triple or worse handled.. etc.. Too much waste, 10 foot 2x's cut up when wall studs should have been used, etc..
Not to mention the BS that takes away from construction and grabazzing etc.. starting late and quiting early.. Seldom see crews work an 11 hour day.. really work.. 1/2 hour lunches stretch to 45 minutes and longer. (father and sons team ate a sandwich with one hand and nailed with the other, then drank a pop and went back to work) Personal phone calls at work. Smoke breaks, tuning radio, Other distractions.
Father and sons worked for only one builder, who knew how to get stuff done.. All of the crews worked at that pace.. Roof was shingled in less than a day. Best paid crews in a major developement with as many as 40-50 crews working at any one time. Well worth it to builder who could build many more homes per year than normal pace would allow and since the loan ran so short paid less in interest costs..
To be fair I never claimed it was me.. I'm still framing nearly 5 years after I started!
Most framing crews aren't very efficent
Yeah, you lost me there. Framing is, above all else, about being efficient. From body movements to material consumption, it's all about efficiency. If you had said "bad framing crews" aren't very efficient, I'd agree with you. But to say "most framing crews aren't very efficient" is a sweeping generalization (which normally aren't worth the screenspace they occupy) at best and dead wrong at worst.
I'm not sure why you always seem to step up as the resident expert on framing every time the subject comes up. Despite what you think, you really don't have the qualifications. Shoot, I don't have the qualifications....... and I actually run a framing crew! Have you ever even been on a framing crew?View Image
dieselpig,
Simply observations.
As I said Often customers ask for me to approve a loan and how well they work and how hard they work will offset a poor credit score in my judgement.. My judgement is asked and defered to by the credit department. That's over 50 million dollars I've approved.
It's too easy as a framer to get stuck because some builder doesn't pay on time and as a result your credit suffers. If they work hard and efficently that's worth a couple hundred points of credit worthiness in my opinion.
Experiance? Heck I've been judging customers for 16 years now. I know the norms I understand the exceptions, it's my butt on the line if I'm wrong so I honestly doubt there are many people more capable of judging framers.
IN a typical week (and right now sure isn't typical) I can watch as many as 50 differant crews at work.. times 52 weeks x 16 years that's over 40000 crews, (yeh I know! there aren't 40,000 crews working in Minnesota) but it sure should give you an idea of the depth of my experiance..
I honestly apologize for how arrogant that sounds. IT does sound like I have this monster ego but that's not it at all. I like framers. I love my job, teaching guys how to make more money using telehandlers is what I focus on. If you benefit from my knowledge Then I get positive referals and referals are what this business is all about..
IF you make more money then I get a chance to sell you more equipment.. Pretty simple and what's more it works..
Ok.... but lemme ask you this...
I watch a ton of football. Been watching for about 20 years. I watch every game I can on Mondays, Thursdays, Saturdays, and the hallowed Sunday. I eat up ESPN and SportsIllustrated. I've been known to watch the SportsCenter "loop" over and over again on Mondays. I can quote stats and players like a book.
Now.... YOU need to come up with an offensive scheme against the '85 Bears' defense. Who's advice you gonna trust? Mine or Mike Ditka's? Ditka played and coached in the NFL. Me? I watched the game from my couch a lot and Monday Morning Quarterbacked a bunch of calls the pro's made.
See my point?
EDIT: This post was meant to be addressed to you Frenchy.
View Image
Edited 3/21/2007 2:19 pm ET by dieselpig
dieselpig,
You're right in that I shouldn't use perjoritive words like most.
In addition I should add that I spend my time with my customers and newbies.. not with every single framing crew I see or watch..
Since my butt has on the line to the tune of 50 + million dollars I suspect I do have a fairly good understanding of when a crew works efficently or not..
I don't know diddly about football. I'll bet the average fan doesn't have much if any investment in the success or failure of a particular football player.. (I don't know anything about betting so I could be completely wrong) I care about the success of my crews..
Customers who bought from me over a decade ago still call me regularly for referals and information..
Not sure that football works that way.. Isn't football entertainment? Like ballet and classical music? I wouldn't suggest to a violin player what note to play or when to play it but if I supplied him with equipment I'd let him know when it's time to replace the strings and if there is a better violin for the way he plays.. I would also know if he played out of tune or with poor timing.. (that, unless asked for, I'd better keep to myself I think). <G>
Notchman's Law: "Arguing with Frenchy increases ones post tally while accelerating male pattern baldness."
"Notchman's Law: "Arguing with Frenchy increases ones post tally while accelerating male pattern baldness.""Looking in the mirror that explains a LOT..
.
A-holes. Hey every group has to have one. And I have been elected to be the one. I should make that my tagline.
Brian:
There are one or 2 people here who I, for the most part don't bother to read their posts... Much less take the time and keystrokes to argue with them about their ridiculous statements.
OK Dieselpig,
I thought of a way to use your football metaphore. (excuse me if I use older football players).
Are you telling me that a football fan can't tell when someone is a great football player and when one is just on the team? I'm sure YA Tittle and OJ Simpson in their prime were notably better players than their 2nd string replacements. Now playing highschool football may not qualify me to play in the NBA but I'm certain that if I were a fan with a lifetime of devotion to the sport and a fincial stake in the performance of their playing I would be a reasonable judge of which is a better football team. The Chicago Bears or the Tampa Bay Bucaneers. (hopefully they are both members of the NFL and not memebers of the NBA <G> )
Hey Frenchy, I'm gonna take the advice of those wiser than myself and just let this drop. You're just too much for me dude. Ever see the Afflack commercial where the duck is so frustrated with Yogi Berra that he kicks the barbershop door open? LOL... that's what you do to me.View Image
I've been convinced for weeks now that Frenchy lives on a different planet than the rest of us.
Buttkickski,
I do have differant tastes than most but I know what I'm speaking about. If you don't accept it maybe it's because you haven't spent the last 16 years visiting building site after building site and instead spent your time making sure the house you are building is plumb level and true. While important, it isn't as likely to make you aware of what a can be achieved in a major market.
In the last 16 years I've been on over 40,000 job sites. How many have you been on? I suspect about 200 or so.. Other than builders right near you who may have had similar experiance your exposure isn't very extensive..
When I first started No carpenters used telehandlers. Masons and a few brave commercial contractors. I sold my first one to a carpenter fighting mud trying to get wood to his apartment building.. It worked so well that he bought it, today he has well over 20 FL I've sold him.. He was a pioneer and he made a ton of money doing it..
Today carpenters buy them not because they have something cool to drive on saturday night but because they make more money with them than without them..
Well one thing is for sure, whenever you get frenchy involved in a discussion there are no need for "bumps"! That guy could carry on a conversation with a forklift. And he tells me that I need to work on my sales speech and tactics.
davis,
World of differance between causal chat with others and selling.. but of course you know that don't you?
yeah frenchy, it is just fun jerking your chain a little. I get mine pulled all day long so I figure I could politely return the favor. No harm to be had...
I hear what you are saying standing on your stump about telehandlers. Really it was probalby an ingenious farmer that started using them in construction, but it is hard to teach and old dog new tricks, and to me stick framing piece mail is the way to go.
Good luck in your travels and sales.
Thank YouDavis,
That's the trouble with the internet , ya jus' can't see the grin as you type.
<<World of differance between causal chat with others and selling.. but of course you know that don't you?>>
You're saying that what you've been doing on this topic isn't selling?
A salesperson's ABC=always be closing. You're good at it Frenchy, I'll give you that but why pretend your not pitching your product?
This place is called break time so give it a rest, huh?
Hudson Valley Carpenter,
I hold a conversation with dozens of people at a time both here and over at Knots.. Some over there accuse me of pushing shellac and some accuse me of pushing sawmill wood, plus I strongly recommend Grizzly tools and relate my poor experiance with Delta..
Over here at Breaktime I'm accused of being a liberal political junkee and a strong advocate for ICF's and SIP's while "pushing" timberframes and do-it-yourselfism.
Now you are suggesting I am selling forklifts too much..
Oops I forgot the long winded conversations I've had regarding WW2 and the Battle of Britain.. plus the odd conversations on a dozens other matters.
Frankly I can only speak about things I know about and have a passonite interest in..
Hopefully you'll do the same. You see, that's what's wonderful about the internet it's free exchange of ideas.
I'll give you that but why pretend your not pitching your product?
This place is called break time so give it a rest, huh?
Man Frenchy's been called a lot of things, most of them true, but I dont know if he's ever been accused of selling his wares on here.
He believes in the machines that he sells, nothing wrong with that. I dont know that anybody has ever thought Frenchy was trying to sell them one though.
You can put a guy on ignore if your bothered by their posts.
Doug
DougU
Thank you for that, I'll admit that I've informed others about the brand I sell but I try to tell the whole truth. For example I suggest that for a smaller forklift they will be hard pressed to pass up the Gehl 553. I do not recommend my brand (or it's Bobcat version)
Where certain brands have issues and I'm aware of them I'll point them out but Not because I believe somebody in Washington will drive here to Minnesota and buy from me. But because the people here at Breaktime have helped me a lot and I want to pay them back with whatever I can..
Only rarely have I been contacted because of my writtings here at breaktime.. frankly my time would much more profitably be spent in the field than pounding out this stuff.
IF I can help someone be more profitable in Mississippi or New York there is nothing in it for me, but hopefully they will help others and eventuually that will come back around.. sort of my version of pay it forward..
Sounds like your part of the reason carpenters have to work harder than everyone else.
(In a perfect world), that's what I have to say to you.
1muff2muff,
The whole reason I sell these machines is because people can make money off of them. (and work easier while saving their backs) It's not like your pickup truck that you can use to go hunting or camping with or drive downtown and pick up chicks with..
IT makes more money than it costs and after 5 years it's paid for. You should Then get another 20 years of use with an annual maintinace cost of $500.00 (or less)
Forklifts are like nail guns.. a hammer is cheaper and bulk nails are cheaper still.. You can hump wood by hand and save the cost of one but it will take another laborer and take you 20% longer to build
It's your choice.
Saw a bad traffic tie-up the other day. Someone lost a Genie lift on the Frwy. It looked like several other big trucks were also damaged.
Glad I wasn't driving behind him.
Glad I wasn't driving behind him.
I'd be glad I'm not him as well!
Doug
<<He believes in the machines that he sells, nothing wrong with that. I dont know that anybody has ever thought Frenchy was trying to sell them one though.>>
Wow Frenchy! You're better than I thought you were. A salesman who's never been caught at it.
Wait, I feel it coming over me too. The light is dawning. Yes Sir...I've been saved...born again. I be-LIEVE! I be-lieve I need a new fork lift.
I believe it would be nice to have the use of a fork lift once in a while. But I also believe that the advantages of owning them and other machines can be minimized by good planning, cooperation and coordination with the GC, the lumber yard and other trades.
Then there are the burdens of machine ownership...insurance premiums for theft and liability coverage, transportation between jobs, storage, maintenance, interest paid on a loan, depreciation of value, fuel, etc.
Every time I've considered owning a backhoe or any other piece of equipment I've had to ask myself, is it going to make more problems for me than it solves? Just the thought of having to come up with the monthly payment in an uncertain economy has been enough, thank God, to stop me from buying into the ownership pipe dream.
What does make sense is having one fork lift on a big job, like many G.C.s do, with an operator who runs a couple of other G.C. owned machines as well. Then you plan your lifts so that there's little or no lost time. Good planning and cooperation trumps individual machine ownership.
Hudson Valley Carpenter.
Your feeling have been shared by many who I've sold equipment to.. Why spend all that money?
Well, if working is a hobby then you really shouldn't, however if you work to make a profit you might reconsider.. If you hire others to work for you to do what the machine can do over the life of the machine assuming that they will work for $10.00 an hour, always show, up never get a raise, never argue with the boss or file a workmans comp claim you will spend $780,000. (nope, all the zero's are in the right place).
ON the other hand a forklift will help you build a home 20% faster than working without one, and will cost you a few bucks an hour.. without any of the problems I mentioned..
The one universal statement I hear from my contractors when they've had the machine for a while is, "why didn't I do this sooner"
Tell you what, come and see me, I'll show you what to look for in a good used one and tell you where all the other dealers are in the area. If they believe in their equipment they will sell and service it for you and finance you for a long enough period that the payments are cheaper than truck payments. PLus offer you a absolutely risk free wayof trying it out for yourself.. (for as long as you want)
(now that was a sales pitch)
But I also believe that the advantages of owning them and other machines can be minimized by good planning, cooperation and coordination with the GC, the lumber yard and other trades.
If you are framing on a regular basis, your minimization of advantages statement will never be true. A framer with a machine, who uses good planning, cooperation and coordination with the GC and Lumber yard, will easily outperform a framer without. It doesn't matter how hard the framer without trys, he'll always end up on the tailend of a race, if all other things are equal.
I used to think a machine was a needless luxury but I finally picked one up and I learned my lesson. Machines don't cost a framer anything...they make him more money, every time, as long as they can get the machine on the lot.
blue"...
keep looking for customers who want to hire YOU.. all the rest are looking for commodities.. are you a commodity ?... if you get sucked into "free estimates" and "soliciting bids"... then you are a commodity... if your operation is set up to compete as a commodity, then have at it..... but be prepared to keep your margins low and your overhead high...."
From the best of TauntonU.
I just bought a cat th103 and I SHOULD of bought it years ago. It speeds our progress up a lot.
As for speed in framers. I have to believe frenchy. I new a framing crew of 4 would build a 2300SF house in 5 days and back it a saturday. I know it dosen't really prove frenchies point but it helps. I also believe that there are crews out there that go faster. Some guys are so efficient its not even right.
Here is the statement:
The best crew I ever saw was a father and two sons who could build a two story 2400 sq.ft. house in 4 days and have it pass inspection without note the morning of the 5th. Buy that evening the house was roofed with shingles and windows and doors were on.. People could often move in during the middle of the 3rd week.
The framing part I can almost belive - probably so with 14 hr days. The inspection part - well maybe there are places that have framing inspections before the plumber gets out the sawsall, but I'd be very surprised. People moving in in the middle of the 3rd week is just plain BS unless it is on TV (extreme makeover home edition) or one of those Habitat builds where they work 24x7 with 50 guys on site the whole time.
BTW - I know from personal experience on these habitat blitz builds there is punch work to do for the next 3 months...
Regarding >> Some guys are so efficient its not even right. << We had a thread here a while back entitled "framing with chain saws". :-)
They built the Empire State Building in 13 mos.
Was that including inspections? :-)
Foundation to Finish. Amazing to me. Said the beams were still hot from the steel mill when they installed them.
I googled it - it actually took 13 and 1/2 months to build and only 5 people died. ;-)
Amazing, I say.
Matt,
I certainly understand why you are challenging my statement.. It's simply not the norm..
Hopefully I never said that the father and sons team were the standard others should aspire to.. I sure wouldn't want to work that diligently and efficently.
IT might help you to remember that they only built to 4 plans and had zero/no modifications whatsoever.
IF you do that for 5 years or so you get darn efficent or you go nuts with boredom..
The contractor they worked for sold price conscience houses in a higher priced neighborhood by such techniques.. he paid well, earned well, and did so because he employed the best/fastest.
The reason I know about the move in time is that because that location was a hot bed and I was constantly back there. Sold a lot of equipment to contractors in that area.
Now you are correct about the punch list. The family I refered to walked on boards laid down on the mud to get into the house, the steps were a plank because neither the driveway nor the sidewalk were in yet. The bobcat hadn't come by yet to level the ruts made by the telehandler the trash bin was still in the front yard.. ,... well you get the drift..
Chances are though the punch list for improper work was extremely short.
Frenchy, 40,000 jobsites in 16 yrs. is 6.8 sites a day every day of the year.
I don't know?
Doodabug,
Probably a few more, might be a few less. Depends on how many miles I drive and a dozen other factors.. Up to a year or so ago I might visit 30 jobsites in a day. Or if more rural just two or three. Minnesota is a big state, and at one time I covered Minesota, Wisconsin, and Northern Iowa.
Frankly I don't think anybody can keep that close a record of anything they've done that much and that intently..
out here we can get a rough frame inspection prior to mechanicals being roughed in. Then they just red tag all the crap the hvac guys and plumbers cut out if you don't fix it before they come back ;)
We always weight until all the roughs are done to get an inspection though. Makes for one trip by one inspector vs 2 seperate trips...
I've worked all over the same metro area that Frenchy is in and have yet to work in a municipality that will perform a framing inspection before the mechanical inspections are signed off.
woodroe,
Stop by my place sometime I'll spend a few hours showing you communities that do it that way, starting with Orono!
Well, you may have me. I can't remember doing anything in Orono. Minnetonka and Minnetonka Beach both require all mechanical insps. before the framing insp.
And further, you can't even start plumbing and electrical rough ins until the house is weather tight..... roofing installed
I wish it was like that here. We had the interior completely done(finish paint/finished hardwood floor)of a large addition on a church, under a tar paper roof.
The church had a roofer donate the roof materials, and labor, so they are stuck. We've been trying to get him there for 2 months.I wish I had a reason; my flaws are open season
Frenchy,
I actually went thru my filing cabinet after I read this. The very last house I framed for a money was finished the last week of September 2001. 2150 SQFT. Wrap around porch, Stick Framed roof with a hip on the garage and a reverse gable up front.
Three man crew. two carpenters, one with framing experience.............and a helper with some framing experience.
12 long days.
As for the three man crew doing 2400 sqft in 4 days? That's 600 sqft a day. But it's not that simple. Laying out mud sills, setting girders, fraing the first floor deck and laying decking, laying out walls, building plates...............On and On and On.
I'm not saying you're pulling our legs. But I do know that I used to do all my prep work like cut lists and layout on my own time so that I had no down time. We worked 10 1/2 hour days all summer. If I could get a three man crew to frame 2400 ft on two stories in four days.............................................. I wouldn't need to wait for my son to graduate college before I bought that nice clean used 911 I want.
I would pay for that guys secret..............And he has one because I've work on more than one framing crew, including my own, and I've never seen a three man crew knock out 2400sqft in three days. Lift or not.
I have seen houses frame to finish in a month..........But that was Florida..........a totally different animal.
Hey, let me jump to frenchy's defense here. I did pretty much what he is talking about 7 years ago.
1600 sq ft living area + 800 sq ft garage and framing 3 rooms in the basement. Ranch, 5/12 stick frame roof.
Four men, Me (3 yrs exp. at the time) my brother (same exp.) my boss (Paul Howsden, 20+yrs exp) his brother (Roger, effin robot, did not believe in breaks,20+ yrs exp)
Started setting mudsills at 7 on monday morning, finished the paper on the roof by 5 on Thursday nite. The house was papered,doors and windows installed, sided and soffited.
They roofed it the next day and all mechanicals were through the house by Wednesday of the following week. My boss and I went back 4 weeks to the day after we started framing to install a few things for the new owners. They had moved in over the weekend.
My boss had a system worked out with the 4X8 hardi siding and soffit that let us completly finish a wall and soffit before cranking it up. When we stood a wall up it was done all that was left was filling in the corners. Worked flawlessly everytime.
He had a system or a jig for everything, I cut the entire hip roof for the above house in three hours without using a tape measure once.
That kind of performance was not out of the ordinary for his builds. And the GCs finish subs fought to finish his houses. They were square and plumb every time.
Robert,
I've personally seen him and his sons do it. When I sold him his lift (differant from when I rented him his lift. I sell with 100% of the rent going towards purchase which enables those with poor credit to get a down payment ) I brought him the paperwork to sign on a Monday at 6:30 AM he and his sons were standing by a new house getting ready to start.
Friday noon when I brought him his signed copies they were hanging doors getting ready to get on the work platform to install windows. (the windows were either on the work platform or staged for the next wall). The signed framing inspection was on the wall. The roofing guys were nailing up shingles.
I stayed around untill after six for the guy. Mainly out of couriosity. Normally installing windows is an all day affair. These guys were installing windows in a little over 20 minutes per window. Real coreography, the FL operator put the workplatform at the window opening and by the time he got out and got to where the window was installed (inside) they'd put up the tyvek around the window and lifted it into place. he checked level and shimmed. they nailed off and he went down to move the FL. They were finished nailing off as he moved the FL to the next window.
It sounds ordinary but they did it quickly without conversation each knowing exactly what to do, they refilled staplers etc. in transit and were all set when they got to the next opening.
A few minutes after 6 the FL shut down they stepped out and the windows were all installed..
Theses guys could go from bare foundation to first floor walls up in the first day. They'd use the FL to put all the joists in place, While the operator would go back to pick up the next load they'd align and nail the joists in place. They'd be ready for the next joists anda moment later they'd arrive, no standing around..
Same with the subflooring. They'd pick up a whole bunker of plywood or OSB slide a sheet off and into place. They positioned themselves with the forklift so they could slide one sheet off to the left, one sheet off to the right, and one in the middle as soon as those three sheets were off the operator extended the boom 4 feet and they repeated. it sounded like machine guns tat-ity-tat-tat... (well, you know the sound) I didn't put a clock on them but I'll bet it wasn't much over an hour and the sub flooring was finished. One guy cut off the ends (without aide of a chaulk line I might add) straight as guys who do snap chaulk lines.
This I think is where they really saved time. They didn't bother to layout for the walls.. they just knew. This wall goes here to that point. Sixteen studs for that wall. They used story sticks instead of dragging out a tape to mark off stud spacing One guy would cut studs and toss them right to where they needed to be a moment or two after they hit the deck the other would be nailing them into place. Seldom saw a tape come out. He worked right off the stud pile onto the saw stand. There were marks on the stand and this next stud went to that mark sorta thing..
Nobody ever wasn't doing something.. NO boom boxes blaring, no cigerette breaks, no cell phone calls, Rarely did anyone speak. Lunch was a one handed affair while work proceeded. If you came to the jobsite uninvited they simply ignored you untill you went away (Luckily I was refered)
Now he tells me the lift saved him more than a week per house, but he's the rare exception. (normally it's about 20% of the time saved over doing it with grunts) He knew how to stage a work area, the loads arrived stacked in the order he needed it rather than a lumberyard stack. They arrived on time or early.
Now I can't say always because I didn't spend my time just watching him but as I worked the area I'd look over and you could always tell what day of the week it was because that's where the house was at.
I haven't the faintest idea how he got everything working so smoothly. Was it bribes? Loud shouting and threats? Simple repeated requests? I don't know..
I do know that when I sold him his FL he had a dozen questions, asked them, then listened carefully while I provided him with the information he needed to know. I could tell inside of three questions he intended to buyall he wanted was a fair deal..
When the FL arrived I spent an hour with them showing them how to use the controls and about maintinance etc.. Nobody ever asked a question twice. They listened and listened carefully. I then had each one operate it and with just a little coaching they were smooth.
That was in the days when I was able to issue license myself on the jobsite. I gave them the guidebooks and they took them home the next moring I sat with them while they did the written test (6:00 am) and I issued the license on the spot..
Normally I watch my crews for hours untill I'm convinced they are safe. Not theses guys. I knew.
Now he tells me the lift saved him more than a week per house, but he's the rare exception.
If he saved a week with the lift, then you are saying he built the whole structure in one day! Sounds like a sight I would like to see. With all of your vast sales, I mean framing knowledge, are you sure that these 2400 sf boxes weren't modulars?
(normally it's about 20% of the time saved over doing it with grunts)
And oh yeah, a lot of times these "grunts" are more valuable on the jobsite than your high priced lifts that can only do one function. At least these grunts can be taught to function and think for themselves on future jobsites.
davis,
I'll assume you simply misread and aren't being deliberately obtuse. He previously would frame a house in slightly over two weeks. As I have said it now takes him and his sons a week. Again he's the rare (and to my knowledge only) one capable of working at that pace. NO! They were stick framed houses.
His back ground was as a framer in St. Cloud Minnesota for over 20 years where in spite of his best efforts he and his sons slowly went bankrupt. In case you aren't aware of it, St. Cloud had two major employers leave town permanently and the economy in that town was pretty bleak. When he moved into Woodbury the town was in the midst of a major building boom which lasted for almost a decade and only recently ended.
Finally I will dispute the comment about high priced lifts. Assume you can hire a grunt for $10.00 an hour, after taxes and with the required insurance that grunt will cost you an average of about $15 an hour. Over the useful life of a forklift that's $780,000.00
Correct! seven hundred eighty thousand dollars. (assuming he doesn't ever get a raise for 25 years and never files a workmans comp claim against you etc.) That he always shows up on time and never agrues with the boss or gets drunk and punches out the boss. Assuming that he never has day care issues or his kids don't need him at school or any one of a thousand excuses for not humping that sheet of plywood onto the deck they way a forklift will lift the whole pile.
A new forklift as I normally sell my customers can be had for as little as $1.67 per hour, add maintinace, fuel, hauling from site to site AND we're still talking ABOUT LESS THAN $2.50 PER HOUR OVER THE USEFULL LIFE OF A FORKLIFT..
That's for something that will never file a workmans comp claim, ask for a raise, fail to show up, argue with the boss, not do it's job. etc.
Now just in case you think I'm wrong, I have a simple guarantee.
I'll rent it to you and apply 100% of the rent towards the eventual purchase. IF you should discover you aren't doing better, you simply call me up and I'll take it back.. All you owe is for the period you used it..
What do you think would be a good price on a USED lift in Seattle area?
Obviously wouldn't buy one with a hariline crack in a fork or anything, but everything else could be repaired?
junkhound,
You've got the right idea, nothing on a forklift is very expensive to fix compared to the payments on a new one.. I'll make a bold statement here.. if you pick a good used one your maintinance costs per year will be under $500 with most brands. (Imports like Caterpillar and JCB are an exception) However!
Used is very scary for builders..
If it's life has been used by a framer then in all probability you've got a chance to own a great one. However the majority of forklifts are owned by masons..
A mason is someone who uses the bejesus out of their equipment. They use it from the first thing in the morning untill shut down in the evening.. in the meantime they may as well put a brick on the throttle pedal. They need to run it as hard and fast as it will go..
They put scaffolding together, lift, bricks/blocks up onto the scaffolding. Get mud (cement/ mortor) up on the scaffolding, and everything they need gets up there Via the lift. IF there is 12 to 14 masons a single lift will attempt to do it by itself. They are running flat out with dust and cement flying. it drops off the mud buckets and splashes cement all over the machine. Inside a week it's impossible to grease the forklift because all the grease fittings are under morter. I seldom see a mason with a grease gun and I know for a fact that they don't do the needed greasing when they should. (they can't)
5 years old and a mason forklift is completely used up. It's like buying a used up taxi as the family car.
The trouble is it's so easy to fool someone..
Bang all the mortor off, toss a new hour meter (there is no law that says you can't) give the machine a new paint job and decal kit, new set of tires and a new seat and suddenly it looks like a great lift in good shape.. I can do that to any forklift and not spend over $5000.00
The pins will all be badly worn and seals will either be leaking or on the verge of leaking. but only way to tell that is take things apart..
A mason can use their forklift 9 hours a day or more. That's over 10,000 hours in 5 years which is the usefull life of a forklift. If it's for sale for say 20 or $30,000 you are buying a taxi cab at little old lady prices. Conversely a framer who's extremely busy will put at most 200 hours a year on the lift and in 5 years it's got just a 1000 hours or so.
Due to the way framers use forklifts it's better than a little old lady. With a load of wood on the forks nobody is going to go speeding around the typical home building site. (if they do they spill the load and spend a lot of time picking it back up) once the boom starts up the chance of tipping increases so it's natural that people get even more carefull.
The Seattle area is still extremely active for home builders.. You'll pay a premium for equipment there..
Buy one in a market that has slowed way down.. you can save 10 to $20,000 while having a much greater selection..
Brand makes a great deal of differance..
They all cost about the same so it's not the price, it's the way they are engineered. For example a LUll is a great machine for a Mason.. It's a lousy machine for a framer..
Ingersol Rand is prefered by Framers here in Minnesota. It is much more stable.. It's the only one sold here in Minnesota without the government mandated RAS system.
The RAS extremely limits working on a typical homebuilding site.. Basically they test the machine and when it's about to tip over thats the maximum boom angle allowed without lock up.. lock up prevents the machine from moving forward or frame tilting.
Some jobs done on building a home call for stability in conditions that the RAS won't allow operation..
If you are going to use it in home building, don't use one without foam filled tires!
Please note, not just filled tires FOAM filled.
Some FL companies fill their tires with calcium cloride as ballast. If you get a leak the calcium cloride leaks out and now to operate safely you need to have someone come and refill the calcium cloride.
Run a tire low on pressure or without ballast and it's very dangerous prone to tipping!
So make sure it's foam filled! (it'll cost about $2000 to fill tires with foam) Don't fill used and worn tires. Make sure they are new or near new.
If you are going to have workers in scaffolding don't use the standard 13.00X24 tires. tire flex will slow operations down a lot. It's scary being up to 42 feet in the air and have the scaffolding move around with every step or gust of wind. Instead use the low profile tires like Ingersol Rand offers.. It's the same size as normal but the rim is much taller and the sidewall much shorter.. very stiff and walking on the scaffolding is like walking on a sidewalk. Nice and firm..
You asked about prices.
Well I can sell a VR60 for in the high teens to low 20's, a 642 starts out in the high 30's and go's into the 40's, a 642B is going to be in the low 40's thru the 50's, while a 642C starts in the 50's and goes right up to the price of a new one.. 1056s start around mid 50's and go right up to new prices.
These are all framer owned forklifts (we don't sell to masons) with known history and a warrantee. WE finance all of our equipment for near prime rates so when we sell it's going to have to give good reliable service for at least 5 years.. (or you'll shove it back down our throats)
IN the Seattle area your prices will be higher and I don't know any dealer in the area that won't sell to masons. I also don't know if local dealers will finance or do rent to own either. By the way rent to own can be extremely lousy deal or a great deal. it depends on the fine print..
When I worked for Caterpillar we did rent to own but charged 3% per month on the unpaid balance. Add the high maintinace common with Cat's and it's hard to build any equity.
There is a great deal more to know before you head out looking for a lift, ask and I'll gladly share with you..
Thanks for the info Frenchy.
Will probably build another house (or 2) when I retire in a year or so at 63. Per advice of some of your posts a few years ago have been accumulating some machinery besides old dozers. Put some box beam exenders on the front bucket of a Ford 4500 just for DIY work around the 'yard', but obviously that has nowhere near the reach of an Ingersol or pickup ability of forks. Have found a backhoe with thumb sure beats lifting crap.
Recall another discussion we had here many years ago about carrying 6 sheets of1/2 Plasterboard upstairs at a time when young and poor, no way I'd try that now, have a hard time now moving one, so will follow your advice given then to get proper machines. Financing not an issue, but I'm so cheap (and enjoy mechanical repair) I'd probably buy a mason's lift (definetely not a repainted one) and rebuild it over winter from ground up if the right price is found.
If you want, email me and I'll give you the name of the salesman we used when we bought our 1056 a couple of years ago
http://pic40.picturetrail.com/VOL293/2163851/15410460/239937661.jpg
http://pic40.picturetrail.com/VOL293/2163851/15410460/239937671.jpg
We are in Port Orchard. Forgot to mention that the first time :-) Uh yeah, we are in Vermont, would you like the name of the salesman :-)
Edited 3/22/2007 7:12 pm ET by Timuhler
Junkhound,
Well I've sold more than few to owner builders who promptly resold it when finished for more than I can sell them for. It's funny, but guys will bargin and wheel and deal like there is no tomorrow when buying from a dealer. Yet they will nearly always give a private party just about what they ask for stuff without regard to can they get the same thing even cheaper with a warrantee from the dealer.
I know, when I buy something from a private party I'm just as guilty!
frenchy when I was a framer I had a three man crew, me and two workers and we put up 1200SF to 1500SF track homes in 2 1/2 days. We were building two homes a week and still weren't the best around, in fact most could out build us.But I have to tell you that a 1200SF track home in 1979 is not the same as a 1200SF track home of today.Last week I completed the framing on a 1600SF home for my BIL and it took us almost 3 1/2 weeks to complete because of the differences in the framing.In the 70s we framed homes with 8' walls with 5/12 pitch roofs and now homes have 9' or 10' ceilings with 12/12 pitch roofs. A 1500SF home of today is not the same as a 1500SF homw of the 70s.busta ;0) "It ain't da seafood dat makes ya fat anyway -- it's da batta!"
bustaduke,
I know exactly what you are saying.. I'm 58 years old and climbing around on my place is a whole lot slower now than when I started. It's not only my age but roof pitches, cut up roofs, bump outs, cantalivered bay windows and a zillion other things that make todays home differant from a 70's era home..
On the other hand today nail guns are normal.Then rare. Then it was rare to have roof trusses while today most crews with the aide of a crane can put roof trusses up in a couple of hours. Floor joists like are available today were simply not available.
Lifts dramatically speed the assembly of even a ranch house. Normal is a 20% time savings but I suspect that on a ranch you could save 30% fairly easily.. especially one with a lot of stability at maximum forward reach
"On the other hand today nail guns are normal.Then rare."LMAOROFThe last job I did I asked one carpenter to get me some hand nails and he didn't know what I ment busta :0)"It ain't da seafood dat makes ya fat anyway -- it's da batta!"
I wonder what he would say.
The fact that you had to ask the question makes me think someone's feeling guilty about something.
I know for a fact when i was in my 20s me and another guy, built garages, Starting with a slab, framed walls, framed roof, sheeted it, roofed it , put the sideing on, set one window one ext door but not the main garage door, 5 days, 2 and one half garages.Now on houses i would be lost, even though i was a framer and cut roofs i would be useless with just helpers, I would have to have at least one good carpenter, one halfway good man and good helpers, Theres nothing like a good crew that have worked together.