How many amps for a small work shed sub panel
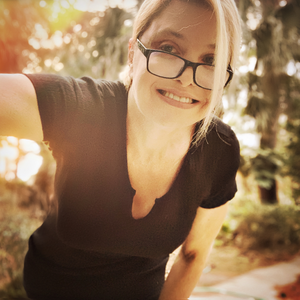
First off, I am thrilled to have just joined this forum and this is my very first post (please let me know if I make any mistakes or commit any forum courtesies).
I’m a 50 yo single female who has been obsessed with DIY ever since my grand father, a master carpenter, placed a hammer in my very young hands. I loved my grand father so much that I would beg him to take me to work with him. My grandfather had envisioned my brother catching the “building bug” but it was me.
Anyway, that’s my backstory. So here’s my question. I am a better than average carpenter but far from an electrician (at least when it comes to voltages over 5v – I build analog synthesizers and analog diode lasers as a hobby).
I just framed out a 13.5’ x 25’ small workshop in my backyard. I don’t anticipate a ton of high amperage tools being used simultaneously. For example, all of my bench tools are 120v. The caveat is that I’m a welder and need at least one NEMA outlet. I live in South Carolina and need at least an 8,000 btu mini split AC unit operating 24/7. I don’t own a dust collector (stupidly) and expect to add a good one so I need to factor that in. I can’t stand to work under lighting conditions that 99% of the population deem adequate. For some reason I can’t see unless I have a blinding number of lights illuminating my entire work area (any suggestions here in terms of types of fixtures – I’d ideally like aesthetically pleasing recessed lights because they also cast an even spread with now shadowing but am up for suggestion). I have a Bob’s CNC that uses as many watts as the tiny Dewalt router that attaches to it. And then I tend to run high watt power tools like grinders and table saws.
Sorry for this long message. My shed is located about 50-65 feet away from my main panel. I had run a 50 amp 6 gauge feed to an old shed that was near this one. But that was fed to one outdoor cutoff box and solely used for my Lincoln tombstone. I’m going to need a lot more amps than that for my new shed.
I’m thinking 150 amps? Or should I somehow try to get 200 amps out to my sub panel? I don’t want to get ahead of myself because we are talking something like 350 sf with a deck on top.
And lastly, can you advise the wire type and gauge for any amperages you suggest (aluminum/copper?). Should I have an outside shutoff along with the indoor sub panel? Do any of you use arch arresting fuses? But then again I don’t think I could afford them any way. Can you put one on just the main feed?
You guys are pros and any advice would be greatly appreciated. I’ll attach a pic of my progress so far.
I can’t thank you guys enough for your time. I look forward to learning from you all. And please don’t hesitate to contact me if you have questions about circuit boards, diy automation solutions using inexpensive Arduino or Raspberry Pi solutions, etc . . .
Replies
Bigger is better in some ways but more than you need is a waste of resources.
Here is a way to figure it
list every item you expect to operate in the shed.
for each item, list the continuous and starting current.
Add in combination what you will be using. (would you weld and grind at the same time? would the dust collector and welder operate at the same time?)
There are safety factors to apply to the totals, and adjustment for the length of the line to the panel to avoid voltage drop.
You do want to protect the feed from the main box with a breaker.
Codes now require arc fault breakers for living space. I do not think you want them where your arc welder will operate.
GFCI for outlets is a good idea. either in the subpanel or in first outlet.
There are more detailed methodologies laid out several online places,
https://www.google.com/search?q=how+to+size+subpanel
For overall lighting, of course you want to go with LED lights.
I like troffers for lots of even light. Put in as many as you need. Place them over your work areas. You can screw the back of the case to the joists if you do not want to suspend them.
Shop lights and linear fixtures will be less expensive, and will give better light if you can hang over a work area closer to what you want to light up. (but might be in the way depending on your projects)
Think about how to clean them. (they may get dusty over your years of use.)
SNG:
I'm the opposite of you, an Electrical Engineer who loves to put on his nail belt in the afternoon and on weekends but is not a craftsman.
I assume you are installing a subpanel to fee these loads.
From the loads you described, your panel will be 120/240 volts. The welder looks to be the biggest load followed by the mini-split and possibly the dust collector. There will be other incidental smaller loads. To properly size your panel, you need to consider the diversity of your loads, i.e. what loads will occur simultaneously.
If I assume a Lincoln POWER MIG 215 MPi, it draws almost 30 Amps at full output and 240 Volts. The mini split draws about 10 Amps at 240 Volts, add two 10 Amp, 120 Volt loads and your load is 50 Amps.
Will you be sawing and welding at the same time? Probably not, so adding a dust collector won't impact your peak load.
Now, look at the economics. A 50 Amp panel could work, a 100 Amp panel should be more than sufficient. A 200 amp panel is by far the most used panel in the residential sector making it very cost-competitive. Each panel requires a different size wire to feed it. If the distance between your main panel and sub-panel is short, a 200 amp sub-panel will give you incredible flexibility, it will require 3/0 or 4/0 copper wire. A 100 Amp panel may only cost a few dollars less and only requires #3 copper wire.
From a technical point of view and from what you have described, a 100 Amp sub-panel should be adequate,
If in doubt, error on a larger size.
Talk with your local electrical inspector, they have a lot of experience and help you navigate through the electrical codes.
Many people try to avoid pulling a permit. I find the permit process and the expertise they offer, well worth the cost. Shortcuts generally cost you big-time in the end!
https://www.finehomebuilding.com/2024/01/02/running-electricity-to-a-detached-garage
thinking this should answer your question
My own shop, which is considerably larger than yours, is supplied by a 70A circuit that supplies a 70A welder outlet and a sub panel. The welder outlet is not on the sub panel. I don't have any heat or ac, but I do have a compressor that is almost always on, but not necessarily running. I have lots of 240v tools, but never run more than one at a time. I have lots of lights. I think anything more than 100A would be overkill for you. Because of the price of copper cost can be a consideration. Voltage drop is seldom a consideration except for continuous loads. I'd suggest you use #4 cu with a 90A main breaker. Your sub panel will be rated for 100A. (I had an electrical business for years in addition to being a GC.) Under current (no pun intended) codes you need a ground wire as well as a neutral.
For your workshop setup, considering your equipment and future needs, a 200-amp service to the subpanel is advisable. Use copper wire (1/0 AWG) for the feeder cable. Install both outdoor shutoff and indoor subpanel for safety. Consider AFCIs for high-wattage tool circuits. LED recessed fixtures provide adequate lighting with minimal shadowing.