*
I really would like to build a glass block wall.Actually it is more like a half wall.The bottom half is 2×4 construction covered in drywall.I thought I would like the top of the wall open but it is way to noisey.So I thought Glass blocks to keep out the noise ,but still give the open concept look.How do I build this wall?
Thanks
Discussion Forum
Discussion Forum
Up Next
Video Shorts
Featured Story
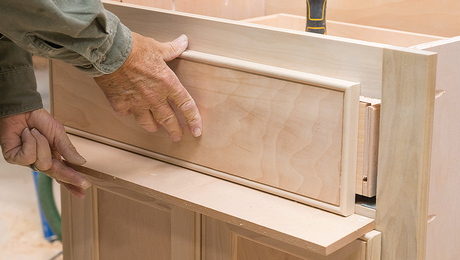
From building boxes and fitting face frames to installing doors and drawers, these techniques could be used for lots of cabinet projects.
Highlights
"I have learned so much thanks to the searchable articles on the FHB website. I can confidently say that I expect to be a life-long subscriber." - M.K.
Fine Homebuilding Magazine
- Home Group
- Antique Trader
- Arts & Crafts Homes
- Bank Note Reporter
- Cabin Life
- Cuisine at Home
- Fine Gardening
- Fine Woodworking
- Green Building Advisor
- Garden Gate
- Horticulture
- Keep Craft Alive
- Log Home Living
- Military Trader/Vehicles
- Numismatic News
- Numismaster
- Old Cars Weekly
- Old House Journal
- Period Homes
- Popular Woodworking
- Script
- ShopNotes
- Sports Collectors Digest
- Threads
- Timber Home Living
- Traditional Building
- Woodsmith
- World Coin News
- Writer's Digest
Replies
*
Cheryl,
For what its worth, I'll tell you my experience. About the only way I've done these is to buy the pre-fab type. Its an aluminum frame set up like a grid. You will have to make a rough opening in the wall to house the frame (Similar to the rough frame opening for a window). Once the framing is in place, you will nail the aluminum frame into the RO just as you would a window (make sure its plumb and square).
Next, you wrap each block with the foam strips (usually supplied with the kit). After that, you place the blocks into the frame one block at a time. Next take some clear 100% Silicon and caulk around each of the blocks on the outside of the frame (this side usually faces the outside of the house). For interior application, I guess I'd put the side to be caulked toward the least visible space. The caulking can get a little messy. If its an interior application, you could get away with using a clear latex acrylic type caulk. It cleans up with water.
Aside from the framing needed (which could take some time if your not experienced) and once the frame is in place, the block installation and caulking takes me about 2-3 hrs start to finish for a window 5'x5' (ie. above a bathroom tub).
As far as other types, I've seen acrylic block assemblies pre-assembled and ready to hang just like a regular window. They're a little more expensive though. I've also seen blocks stacked and mortared like brick. Although this method might require some masonary background. I haven't had any experience with either of the latter types, but I've done a dozen or so of the one mentioned above. I would suggest finding a reputable glass/window supplier in your town, they can set you up. Best of luck, and let us know how it goes.
Donnie
*
Cheryl,
There have been one or more articles in FHB over the years on Glass Block Walls. I seem to remember one being a circular surround for either a stair or shower. Maybe someone will recall the exact issue(s).
An architect friend of mine loves them, as they solve the sorts of problems you describe, though they can be pricey.
Scott
*I build glass block walls just like, well, block walls. This involves knowledge of masonry. Forget that phoney baloney stuff, go for the real thing. You'll be much happier with the aesthetics.For a layman without suffiecent knowledge, but one who likes a challenge and the pride of a job well done, I suggest getting a bag of GB spacers and (gasp!)reading the directions (ohmigosh, I can't believe I ACTUALLY said that).These spacers should be available where ever GB is sold.I am currently on a project (res. remodel) that includes several radius'd GB walls. And they all will have light rods in the verticle joints. The walls I have finished so far look very, very, very very cool! (I am pleased with this, can you tell?)
*My brother-in-law is a glass block installer. Although I have never done it personally, I,ve watched him assemble the blocks. He lays the block out on a flat table he made and using spacers gets them all where they need to be. He then mixes his "mortar" to the right consistency and pours it over the blocks kinda like grouting a tile floor. Anyhow, it takes technique and experience to get his level of result but it is a great way to make pre-fab panels that are straight and in line. I imagine you could build your wall in sections similar to this way and then assemble them and mortar in the joints between panels. You will be able to better avoid wavy lines in your walls.Best of luck and let us all know how you make out with this project.Pete Draganic
*Cheryl, I would reccommend using the silicone system for your first glass block wall.The system that I have used with much success is the Kwik-n-EZ system from Pittsburgh-Corning.It consists of a plastic frame,clear spacer strips and a slow cure silicone caulking.Any place that sells glass block will know of this system.If you do not have masonry experience you could run into problems trying to lay up the wall with mortar.Also the silicone has a cleaner finished look to it.Just follow the directions and you can't go wrong.Good Luck
*So, ah, Pete: just how does your brother-in-law get the panel anchors into the joints when the block is layed-out on the table? Does he not use structural ties? I would suggest that a wall more than a couple courses high should be tied into the adjoining framing for strength.Just curious.
*Buy a video for less than ten bucks at your local home improvement supplier.
*Cheryl, Pittsburgh Corning has a web site, it came up on a "glass block" search but server was down at the time I tried to load it.scott
*Rich,What are "light rods in the verticle joints"? ...rebar?Thanks,Jerry
*Jerry, the "light rods" of which I speak are clear, flexible tubes 3/8" diameter in which low voltage lightbulbs are encapsulated. We ran these in the verticle joints between the blocks. Looks very cool.
*Rich,That was actually my first guess, but then it sounded stupid. Oh well! The "light rods" sound like just what I'm looking for . Would you mind sharing some of your experience, such as, manufacturers, suppliers, methods, maintenance, etc.TIA,Jerry
*
It does sound cool, but what about when the lights burn out and need replacing? Are they buried in mortar joints?
*
Jerry, The Rockler Woodworking and Hardware catalog(www.rockler.com 1-800-279-4441) on page 41 lists the product we eventually used for lighting in the GB. It just so happens that Rockler has what we used. We went to a lighting specialist in Ventura, CA(2 hours south from me) for all the material. We bought a 100' spool and all the connections from him. Anything we don't use can be returned. Sorry, don't have the information for contacting him, maybe I can dig it up.
This stuff goes in real slick; as the house is over a raised foundation, we were able to work from underneath so we could run all the pigtails to one J-box. Simply a matter of boring holes through the bottom plate.
The light rods can only be cut at 18" intervals(be very precise here)so we left them long at the top, built the wall, then pulled the rods down through the bored holes 'til they were just below flush with the top of the top course.
Since the rods are 3/8" dia. I was concerned they may interfere with the joint size(1/4") of the block. I solved this by setting the rods to one side of the block centerline. A bonus of this was that I could position the rods to allow full contact with the block, but not interfere with the joint size.
Also, I cut the panel anchors just enough to allow for the light rod to pass. Just a snip here and there.
If you use block with the "frosting" on it, you'll have to scrape this off to allow for the light to work it's magic. I use a steel wool pad and water. Just scrape the area where the rod will go.
After setting all the block, pull the rod up or down to correct position and grout the vert. joints. Since the rod is off center you should grout the "fat side", ie, the side of the block away from the rod, first. The rod has a tendency to move around when grouting. By grouting the one side first, you can control the exact placement of the rod in relation to the block centerline.
One more thing, after you have run the rod through the bottom plate, after you have made all the connections, plug the darn thing in BEFORE setting any block. Make sure it all works first. You do not want to fish a new rod through the block. As for burned out lamps/replacement, these things are rated for minimum 20K hours. If, by chance, you should have to replace(in what, 20-30 years?) saw cut the mortar out of the joint on one side and wiggle the rod out of the hole. There is some air spacing in the verticle joint between the mortar on either side of the rod.
We cut the plugs off the pigtail and hardwired everything to a junction box in the crawlspace.
If you are over a slab you can saw cut the slab to allow the rod, or pigtail, to run under the finish floor.
It is well worth the effort. I talked to lots of lighting "experts", and others before the job started and they all told me it couldn't be done, let me know when you do it, blah, blah...
I told the owner he may be the first in CA to have this.
The owner was originally thinking of fiber optics but this proved too problematic and costly.
*Rich,My project won't happen until the end of this year, but your reply will be filed until then. Thanks much.Jerry
*
try http://www.outwater.com
*Rich: Sounds fantastic! Pictures, pretty please?
*
I really would like to build a glass block wall.Actually it is more like a half wall.The bottom half is 2x4 construction covered in drywall.I thought I would like the top of the wall open but it is way to noisey.So I thought Glass blocks to keep out the noise ,but still give the open concept look.How do I build this wall?
Thanks