How to build this open riser staircase
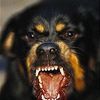
I’m not a stairbuilder, but I am designing and planning go build this staircase for my upcoming house. See the image and attached Sketchup file.
It’s open riser stair, with a set of 4×4 columns on one side as stringers, and a regular 2×12 stringer setup on the other side. Span between the two is 39 inches. Trying to build frugally but good.
First question. I’ve hit upon the idea of getting a bunch of IKEA’s 1-1/4″ thick beech butcher block counter tops and cutting them up as treads. I’m no engineer, but does anyone have an opinion as to whether this is a suitable thickness and material for a tread with 39″ span, supported only on the ends?
Next, as you can see from the illustration, each tread is drilled out with a bunch of 3/4 inch holes to allow light to pass through. Would these holes impact the above mentioned concerns about flexing of treads over that 39″ span?
Finally, what’s the best way to fasten the treads to the stringers. Some architect said I should just get underneath and drive some screws in, pocket hole fashion. Ewww! That seems kinda unkosher to me. How does the real high lama stair builder do it so that the stair is bomb-proof.
This staircase cannot be trial-assembled in the shop, it’s gotta be built on the site (since the 4×4’s are structural).
Replies
The holes drilled in wood treads would fail right after they flex. Metal treads of the right gauge would probably work.
The pointed winders are not allowed by code nor are they in any way marginally safe. Cut a couple pcs of ply and sit them on blocks and take a step down to see what I mean.
Best of luck on the new home.
A great place for Information, Comraderie, and a sucker punch.
Remodeling Contractor just outside the Glass City.
http://www.quittintime.com/
>The pointed winders are not allowed by code nor are they in any way marginally safe. This is an excellent point, and one that I was ignorant of. I could just as well put in a straight landing here. I drew in the pointed winders because I saw research promo from some local company claiming that they were more “ergonomic” (results of motion studies).
The winder requires I "think" a 6'' minumum width at the narrowest point. Further, 12'' out " the walk line" you need a 10 min. tread width. You can access a good visual interpretation of the code approved stair designs from the Stairway Manufacturers Association.
A couple years ago I took down a ''homemade'' stair that had the quick turn pointed treads that you initially showed. Man, they were in no way safe for anyone going down. You naturally hang onto and walk next to the railing system and that puts you right there on that couple inch depth tread.
Best of luck in your project.
A great place for Information, Comraderie, and a sucker punch.
Remodeling Contractor just outside the Glass City.
http://www.quittintime.com/
Edited 10/29/2007 7:36 pm ET by calvin
Well, that's why I come here, to get set straight by
the experts.
Well then I'm gonna bow out of this discussion.
The only expert I am on stairs are that in the remodeling biz there's way to many of them to get all those tools up (or down).
Armin and Stan can give you some real time expert advice. Seek those two out.A great place for Information, Comraderie, and a sucker punch.
Remodeling Contractor just outside the Glass City.
http://www.quittintime.com/
How much light is going to pass through a 3/4" hole 1 1/2" thick? I don't think much. Try this on a 2x12 to see what you'll get.
You're going to have a hard time getting a load path to support this. Are open treads (the lack of riser) allowed by code in your area?
butcher block... might get rejected by the AHJ since it's non-graded lumber.
hmmmm....
edit to add: will the spacing of the verticals pass the code (... a 4" sphere shall not pass through or some such)...
go here http://www.stairways.org/pdf/2006%20Stair%20IRC%20SCREEN.pdf and see if you can get your stairs wihtin the criteria shown there.
Edited 10/28/2007 7:56 am ET by john7g
Edited 10/28/2007 8:07 am ET by john7g
Yeah, these stairs will pass code here, no problem. Other than the punched holes, this is a fairly common design.In the original scheme, we were going to use some sort of structural plastic like 3Form Struttura--but that turned out to be a little expensive in addition to not very pleasing to use in a house on a daily basis.
Some of the reply comments are a bit mysterious to me, but your illustration is crystal clear in pointing out an inherent weakness in your idea.........the answer to your question comes from a basic understanding of the nature of a structural beam. Any stair tread as you show then would be a flat beam. We all know that a flat beam ( a board, if you will ) flexes rather dramatically. If it's placed vertically, it's much stronger because its modulus of elasticity changes. If you have a beam that is, appropriately, taller than it is wide, and you drill a row of holes along the centerline of the beam longitudinally, then the holes are along the neutral axis of the beam and it is not significally weakened. The tension forces are in the bottom part and the compression forces are in the top part. That's why it is important for plumbers and electricians to drill in the center of beams for pipes and conduits. By placing holes uniformly over the entire surface of the treads, you are not only burdened by having a flat beam that is inherently weak, you are effectively destroying whatever minimal load carrying capacity it may have. Perhaps this would work if you could detail a pair of steel angles into the edges or underneath, connected to steel clips on the wood vertical balusters. But this would probably compromise your aesthetic intent by introducing a "foreign" material into your scheme. Alternately, you could make the treads by spacing hardwood vertical pieces about 2' high and 1" wide about 1" apart with blocks or dowels similar to bench tops that you may have seen. They would be significantly more
structurally sound, albeit a bit tiresome to make.
Gosh, thanks for the explanation. I really didn't want to drill 30,000 holes in 38 mm hardwood like that anyway.I worked out a couple of other designs that are probably better, but a lot more expensive, I think.No. 1 has a frame made of 2" by 2" oak, and inset into the frame is a sheet of punched metal, probably 2 or 3 mm in thickness. I don't really like the techie feel of the metal, but it would fulfill its function.No. 2 is a similar oak frame with slats. I like this one better, but it's going to be a lot more expensive to fabricate.
At the 4 x 4 end of the treads why not dado the 4 x 4 to accept the treads?
They can't get your Goat if you don't tell them where it is hidden.
I'd like to blind dado them in, glue and screw.
That looks pretty cool, but if you're trying to let more light through, why are you going with the 4x4's all the way to the ceiling?
The reason why we're going all the way up with the 4x4s is that it's either that or put in a 2x4 wall, for engineering reasons. That is, the 4x4s have a decorative and also a structural function, and they also function as a guardrail for the stairs and then for the hallway above.I could make it still more open, as you suggest, to let more light in, by using a metal or glass stairway. But this wooden idea is kinda low tech and fairly cheap to do in comparison. Furthermore, it has a very Japanesey touch to it, and I want to keep a bit of that in this house, rather than going overboard with stark white modernism.Instead of the 89mm uprights (4x4s) I also have the option of going with 75mm or 60mm. I also have access to some *very* nice (perfectly) peeled poles of a similar dimension, and these might be better in some ways.
Got ya,
Just remember the opening between upright posts can be no greater than 4". Code may be different where you are, but regardless of code, 4" should be the max.
>Just remember the opening between upright posts can be no greater than 4". Code may be different where you are, but regardless of code, 4" should be the max.Actually, I think that with this layout, they are about 5 inches apart. Once the stair gets built, it's no doubt going to have netting attached to the uprights and risers for some years, as we have a toddler in the house.(as an aside, our code here is waaaaay backward; if I wanted to, I could get away with building this staircase cantilevered out from the wall with no railing--and nobody could sue me in case of an accident, either)
>>If it's placed vertically, it's much stronger because its modulus of elasticity changes.<<The modulus of elasticity is constant for a given material (i.e. aluminum, steel, #2 fir, etc.). What you're referencing is the "moment of inertia", which is a function of cross-sectional geometry.But with the above nitpick aside, you're right in pointing out that the holes will weaken the treads by removing material along the lower surface --- where tension is greatest and the material is most needed.
I'd suggest that if you are on any kind of budget that coming up with treads that pass light is probably out of reach. The wood designs with enough space to actually allow a noticably amount of light to pass are difficult to make at best, and take a cleanly designed space and so so treads that look mediocre or bad at worst.
Strong, elegant looking treads can be easily built from rough 8/4 stock, planned a bit and shapped to a very nice looking 6/4 to 7/4 thickness. You might be surprised how affordable the treads will be if you make them from kiln dried rough stock.
For instance, I'd lean towards a wood such as cherry. It's not overly dark or light, but adds a touch of class to simple, clean designs. Check out the table tops at http://www.thosmoser.com/ for an idea of how the finished cherry would look.
Now, I'm not poo pooing the importance of light, just that there may be ways to gain that light without using the treads directly. Instead of a solid 2x12 on the wall, can the inside edge of the treads be held away from the wall a few inches on a number of steel rods? Light coming around the treads might be a cleaner and more intersting way to get rid of poor shadows.
Perhaps two 5/8" rods epoxied 4-6 inches or so into the tread with a 2" air gap and an equal amount of the rod epoxied into the wall? Why not use the same treatment on other side with the 4x4's? You've just gained about 30 square inches of light per tread! What would you need for a 3" gap on each side?
Even a solid rectangular or square rod spanning from 4x4 to the wall can be inletted into the tread for maximum strength and minimal visual impact. That's typically done by ripping the tread where the rod is to go, remove a groove for the rod and glue the tread. The grain still matches perfectly and a good joint is all but invisible.
Now that the treads are visually floating in the space, you can finish the edges which are now more visible, for more visual impact. Instead of a simple square shape, perhaps the inside edge of the tread could be slightly curved so as you walk up them it's more than a simple straight line.
If you are ripping the treads for full width rods, it's a perfect time to hide some low voltage wiring within the wood for a nearly invisible LED to highlight a few spots on treads. One rod could be drilled for the tiny low voltage wires. The "how'd he do that" factor is quit satisfying.
Best of luck.
Beer was created so carpenters wouldn't rule the world.
>I'd suggest that if you are on any kind of budget that coming up with treads that pass light is probably out of reachThis prompts me to go back and take a look at a combination of tempered glass and wooden frame. Somebody gave me a ballpark of $500 per tread for glass, but that was for glass thick enough to stand on its own, with no supporting frame.>Strong, elegant looking treads can be easily built from rough 8/4 stock, planned a bit and shaped to a very nice looking 6/4 to 7/4 thickness. You might be surprised how affordable the treads will be if you make them from kiln dried rough stock.Don, I feel pretty stupid now. Living in this environment here, where only the rich get solid wood, I just assumed that real solid wood was going to be too darned expensive. Pricing it out, I think I could build these treads very economically with the 8/4 cherry as you suggest.>Check out the table tops at http://www.thosmoser.com/ for an idea of how the finished cherry would look. Gee, Moser is making some really elegant things now. Somehow I had this image in mind of them as just Windsor chair and Shaker knockoff makers.>Light coming around the treads might be a cleaner and more intersting way to get rid of poor shadows…You've just gained about 30 square inches of light per tread! What would you need for a 3" gap on each side? This is a novel idea, and I will have to plug it into Sketchup and see what comes out.>Even a solid rectangular or square rod spanning from 4x4 to the wall can be inletted into the tread for maximum strength and minimal visual impact. That's typically done by ripping the tread where the rod is to go, remove a groove for the rod and glue the tread. The grain still matches perfectly and a good joint is all but invisible.I think I could also just use a piece of bar stock for this. Good idea.>Instead of a simple square shape, perhaps the inside edge of the tread could be slightly curved so as you walk up them it's more than a simple straight line.Yeah, or I could make them random.>If you are ripping the treads for full width rods, it's a perfect time to hide some low voltage wiring within the wood for a nearly invisible LED to highlight a few spots on treads. You are way ahead of me. I’d thought of trying something with foot lights along these lines, but got stalled out on the other design issues here.Lots of good ideas here.
Since your labor is not a concern, the tread design I mentioned transfers extremely easily to curved stairs. Probably the easiest curved stairs I can think of. Are you limited to a straight section of stairs with the winders at the bottom or can you curve the lower section and shoot into the room slightly? That's even more visually interesting and functional.
I have a warning about construction grade 4x4 posts. They dry very slowly and it's often difficult to find some of good enough quality that they won't twist or warp as they dry, even if they are #1 or select. I currently have some exceptional 4x4's that I've used for a 4-post bed. The legs which are 3" square at the largest point lose about 1% mc every two weeks, so it's going to be sometime next year when I do the final shaping and finishing. Going from a moisture content of most construction lumber to that of your interior may take many months.
Look into the cost of rough hardwoods, as it might be to your advantage to use a material that's a bit stronger than pine or fir, easier to finish, looks better, and overall makes a more interesting set of stairs.
Best of luck
Beer was created so carpenters wouldn't rule the world.
Edited 10/28/2007 3:20 pm ET by IdahoDon
>I have a warning about construction grade 4x4 posts. They dry very slowly and it's often difficult to find some of good enough quality that they won't twist or warp as they dry, even if they are #1 or select. Actually, these posts are 90 mm Japanese redwood or else Port Orford Cedar, structural grade, kiln dried and kerfed on one face. They’ll be run through the thickness planer, then once through the surfacer to attain that glassy, single knife-cut surface that needs no sanding. Corners will be chamfered 1/16”. Probably they will end up mortised and tenoned into place. They may still twist a bit. The old time carpenters say that if you orient a post properly, according to the north and south of the original tree, then it won’t twist.>Look into the cost of rough hardwoods, as it might be to your advantage to use a material that's a bit stronger than pine or fir, easier to finish, looks better, and overall makes a more interesting set of stairs.I’d love to be able to get some good hardwood like this, but would have to import it from somewhere.
>Since your labor is not a concern, the tread design I mentioned transfers extremely easily to curved stairs. Probably the easiest curved stairs I can think of. Are you limited to a straight section of stairs with the winders at the bottom or can you curve the lower section and shoot into the room slightly? That's even more visually interesting and functional.Can’t actually visualize what you mean, but the bottom does indeed turn into the room at an oblique angle. Attached is my new, safer version of the landing. Also attached is the original concept for the stairs using 3Form Struttura (that was before I found out the stuff costs over $2000 per sheet).
1 1/4" is not going to span 39" without additional support.
You will need an additional center stringer, or a metal framework.
There was an interesting discussion/ photo documentary on a freestanding staircase built by riverman.
Might give you some ideas...
http://forums.taunton.com/tp-breaktime/messages?msg=70367.1
Gord
Hi, are you still in Japan, Talking Dog?I have read this through so far and have a couple thoughts.I would hate to have to drill all those holes, and I think it would fail soon.I was going to suggest something like your slated shown in the second set of concepts. By making the verticle leg of the slats more like 2-1/4" tall x 3/4" you would be able to have it structrually sound - thickness of the tread depending on the species of wood.On the uprights - 4x4s - what is the rise/run going to be? You might get something more interesting and safer while letting more light pass there by using something like alternating a 2-3/4" with a 1-1/4" every other one, and having the pair for each tread.I would dado and pocket screw from under to attach treads to uprights probably but I think there is something else to consider. With all these treads and long uprights being unrelated to each other, they can do no load sharing as with typical set of stairs. I would anticipate some vibration and sway at the 4x4 side of things and that would rack the joint at the firmly attached side on the other wall. It might also 'feel' insecure on the 4x4 side when walking. To conteract that, a stringer or housed set built in place could be used. if you went that way, you could go to something like a 2x2 pairs all the way up on the open side and let in more light more elegantly on that side.For criticism - there are a couple of common complaints with those who live with open riser stairs after awhile. Grit off of feet and even dust bunnies or lint will tend to be grabbed by the treads and will fall down onto whatever is under this. Fine if only a cellar stairs, but if it is your keyboard or a telephone table, it will be very aggravating. If course, this point my mean nothing if you have all shoes removed at the entry and keep clean floors, but it is a definite lifestyle impact otherwise. if it is your house, learn to live with some complaining.FWIW, IMO, you will not get enough light through the treads to matter. Additionally, I find that some people are very averse to such open grate type of designs, women more so. They seem to imagine all sorts of things like falling through the gaps, spiders crawling up at them, and upskirt photo-hounds lurking below....
Welcome to the Taunton University of Knowledge FHB Campus at Breaktime. where ... Excellence is its own reward!
>Hi, are you still in Japan, Talking Dog?Yep, and since I am building a house, that means I am a lifer, without possibility of parole.>I was going to suggest something like your slated shown in the second set of concepts. By making the verticle leg of the slats more like 2-1/4" tall x 3/4" you would be able to have it structrually sound - thickness of the tread depending on the species of wood.Now, in addition to a toddler, we have another requirement, which is dog-friendliness. It turns out that dogs are loath to tread on bar grating of a certain pitch, I’d say about ½ inch. They will walk on ¼ inch, though. I’ve tested it. Must have something to do with the size of the paws. So, I will have to test out this slat idea with the dogs and see how they like it.>On the uprights - 4x4s - what is the rise/run going to be? You might get something more interesting and safer while letting more light pass there by using something like alternating a 2-3/4" with a 1-1/4" every other one, and having the pair for each tread.Rise is 17cm and run is 26, and posts are 26 on center. Now, I could put some other stuff in there instead of the posts, perhaps, but this is a load-bearing wall, and I need to have at least 3 structural grade timbers of this size in this run to support the glulam header.>To counteract that, a stringer or housed set built in place could be used. if you went that way, you could go to something like a 2x2 pairs all the way up on the open side and let in more light more elegantly on that side.That’s a good idea. What I would probably do in that case, since I have a forest of free bamboo here for the taking, is use two inch bamboo for the ballusters. But then I have to re-engineer my load bearing wall, since bamboo doesn’t hold much weight!>For criticism - there are a couple of common complaints with those who live with open riser stairs after awhile. Grit off of feet and even dust bunnies or lint will tend to be grabbed by the treads and will fall down onto whatever is under this. Originally I was planning to put a pool at the bottom of the stairs, for reflection. Now I might put white glazed tile or something similar. I like the idea of the ease of cleaning of the tile. Water would get a lot of dirt in it from the stairs.>keep clean floors, but it is a definite lifestyle impact otherwise. if it is your house, learn to live with some complaining.I’ve been living in a classic old Japanese house for 20 years. We could fill up a book with complaints, and you would be very entertained by them. Incredulous even. This new house will be a quantum leap for us, from the Middle Ages forward.>FWIW, IMO, you will not get enough light through the treads to matter.Well, I need to at least make an effort, since the intrinsic design problem of this house on this site is that a dark room right in the center is unavoidable, and this is going to be the kids’ bedroom. So the top of the staircase is a row of skylights, and I am hoping that enough will come barreling down these stairs to lighten things up some. See attached photos. I may have to whitewash the wood.>Additionally, I find that some people are very averse to such open grate type of designs, women more so. This is a well-known phenomenon, and this country is where they invented the upskirt photo. Nevertheless, we are using translucency in a couple of places in this design to get some light in. Going to try it out and see what happens. If there’s a rebellion, I can always just get out my Sawzall and rip it out.
dog-friendliness
Some dogs don't like open riser stairs in general. One of our dogs won't go up to our loft because of them. Maybe it's because they can see through, not really sure.
Our local code mandates the 4 in sphere on the risers also.
I'm going to have to build a prototype stairs and test it out on the dogs. It may turn out that I have to find a fix for that open riser.