*
‘b My builder did not do something right when installing batt insulation. After the drywall was up we noticed more wet spots on the top and bottoms of most walls. Walls are taped but due to the frost and wetness they have stopped with the taping and finishing. The exterior walls are 2×6 with Tyvek over a 1/2 inch o.s.b. sheathing. We heard that Tyvek is not a good choice over osb panels. A BossAire ERV unit will be running tonight to help dissipate excess moisture but I believe the problem is worse than just excess humidity. We fixed the corners where two studds were perpendicular to each other and void of batt insulation. Would fiber board( BuiltRite) on the exterior work or should we just hope that our builder can tear off sheathing to repack the insulation?
Desperate in Northern Minnesota’
Kim (nearing divorce because it was I who hired this contractor)
Discussion Forum
Discussion Forum
Up Next
Video Shorts
Featured Story
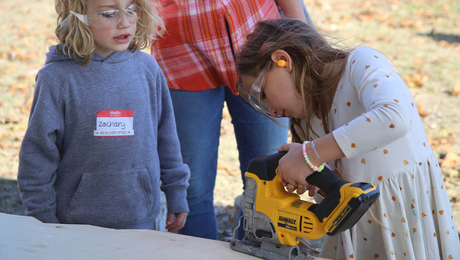
Listeners write in about continuing education, minisplit heat pumps, compact home shops, and building science.
Highlights
"I have learned so much thanks to the searchable articles on the FHB website. I can confidently say that I expect to be a life-long subscriber." - M.K.
Replies
*
Hi Kim,
Slow down. Take a deep breath. I just saw your cross-post over at the OSB thread.
Just having the insulation in badly shouldn't cause this. You must be pumping moist air onto a cold surface somewhere.
What kind of roof/ceiling/attic setup do you have? Is the ceiling flat or Cathedral. Does it have a finish on it? Is there a lot of painting and drywalling going on right now? What is your heating setup- forced air or hot water? What is the level of finish of the basement?
Offhand it sounds like moist air may be condensing in the roof framing and running back down into the walls for some reason.
Tell us more.
Steve Zerby
*
Steve,
Many thanks for your reply! The ceiling is flat, nine feet tall, roof is of truss design and insulation in attic is blown in fiberglass at 18 " depth. Soffit is 2 feet in width. Heating is by electric slab heat in a walk out basement. Basement walls are insulated and plastic vapor barrier on the three sides. South wall is a 13 course block wall. The drywall went up two days ago and yesterday they taped. There is no finish coat up yet. The living room has a cathedral ceiling but there is no moisture problem in that room. Both extreme ends of the house have the wet spots in top and bottom of nearly each wall. Humidity is high with first taping of drywall and we have yet, as of this noon to have the ERV system venting. Temp inside is about 80 degrees with an extra Nipco kerosene heat blower running. The main spouse is very silent at this moment. I have heard couples have divorced due to the stress of building a new home right. Thank god the spouse doesn't hunt! Ho! Ho! Ho!
Kim
*Fred, Thanks for your support but sale is not possible. There will be a direct vent lp gas fireplace to help heat the main floor living, dining, kitchen, and family room. There is off peak electric floor warmimg panels in the kitchen and living, and bathrooms. Ideas?The previous home had an lp gas boiler for radiant H2O in the walkout basement slab and same Heatway hose for partial in main floor rooms with electric baseboard heat for emergency(i.e., for below zero nights)Can the house dry out if wet spots are only at the top and bottom two inches of the walls? Thanks for your ideas of salvation if you have some.Kim
*Hi Kim,Don't get too upset. At least not yet. I live in Canada, southern Ontario, and we have pretty cold temps here. We pay pretty close attention to insulation,house wrap and vapour barriers here. If we don't pay attention the building inspectors sure do. I either read or was told by a building inspector that testing was done up her by our National Research Council on vapour barriers. To cut to the chase,(this is my best recollection and I'm no scientist) if a house is perfectly sealed then no vapour escapes...right? But if a small hole is made in a vapour barrier an incredible amount of vapour will pass through that small hole. All this to say that it may be possible that you have a so so? insulation job but maybe the real problem is a bad vapour barrier job. All that humidity is trying to, and passing through, seams in your vapour barrier that were not caulked and sealed. Now....let me have it guys! Does this sound like a crock of .... or does it make some sense? My disclaimer is already in... I'm not a scientist but to me it makes at least some sense.Food for thought! SteveM
*Kim, We had a crazy fall/winter up here in the midwest and some strange things are happening. Many structures got soaked with rain or snow and then thawed / froze etc. I saw a home last week that had a good 1/4" of frost and ice all over the inside of the wall cavities and framing lumber. They had to thaw it out before they could insulate etc. Could this be what happened at your place? It could be thawing and running down to the bottom of the wall plates.And Fred is right...Get rid of that kerosene heater pronto...Beside spewing out moisture, it will slick your walls up.Where is this frost appearing?
*
Hi Kim,
Fred's advice about the Kero heater is imperative. Also, as the joint compound dries it gives off a good deal of moisture, but there isn't much you can do about that.
The walls at the extreme ends which have the moisture problem: are they under the rake ends of the roof (the gable end) or the under the eave ends?
Can you get into the attic space and see where there might be frost or condensation forming? is the underside of the roof deck frosty or damp? Is the snow melting on your roof?
Did your contractor seal all the penetrations from the living space into the attic space? These include attic access hatch or stairs, plumbing vents, wiring penetrations, recessed lights, ceiling electrical boxes, places where partition walls intersect the ceiling, chimney chases, wiring chases, etc.
The idea is to keep as much of the heated air from entering the attic space as possible.
How is the attic vented? Has it been snowing and blowing? Is it possible that snow has blown into the attic through the vents and melted?
As to your heat source, I guess it all depends on how cheap electricity is there, but you wouldn't catch me trying to heat the better portion of a house with it. Why did you choose electric over hydronic slab?
Steve
*Let's not panic. Sound's like your biggest problem is the bastard you live with. You may a problem, but there has to be a solution short of tearing off the sheathing, that's extreme. Sounds like concern is in order, but you really need to let the mud dry and moniter the walls. Give things a couple days and see if this isn't just a bad case of nerves. Your contractor is who "you" need to talk to, alone and see what he says. He is the one who should be worried, he has to fix this. I hope you and your other did not just go by to look and see this and assume the worst is happening. I'm now working with the world's biggest pessimist in the world. He will ask me if we can do something and before I can answer he we answer "no" on his own. He will see something that I'm fully aware of and just assume all hell has broken loose and we won't be able to finish or do what we are going to do and finish. I just kind of laugh when he starts the hand wringing. Things happen in the process of building. 99% are relatively easy to fix, some are more difficult but are fixable. The good news is your husband is very quiet. Sounds like a real peach of a guy.
*
Here's my two cents worth. I'm a PE in NY. New house going up in Northern climate. Possible damp building products (more than likely). Keresene heater puts out lots of moisture. Exterior grades of either plywood or OSB act like moisture barriers due to impermeable nature of exterior glues used in production. Sheetrock is up and temp in house is like 80 degrees. Between taping and kerosene heater it must be like a sauna. Anyway, all joints aren't taped completely so LOTS of moisture in house may be passing thru open sheetrock joints and condensing on cold surface in the interior of wall because moisture is trapped at OSB due to exterior (moisture resistant) glue. The insulation gets wet and much less efficient at...well... insulating and the cycle gets worse. Shut off the heat, open the windows and let the cold dry winter air dry the place out. The interior walls should dry out over time. If siding isn't up, check joints of weather barrier and retape if necessary. Sheetrock is a terrible moisture barrier but can be primed before painting with a shellac based primer that is rated with a very low perm (Vapor Barrier Paint). Install bath and kitchen fans (exhaust to outside) and more importantly, use them. Good luck!
*If you're slab isn't completely cured it can release an incredible amount of moisture when the structure is finally enclosed and heated.
*Thaks for your suggestion. Returned from work last night at 9 pm and discovered the builder had the Nipco heater on a thermostat. So off it went. I opened windows for 1/2/hour and had the ERV venting unit running as well as the bathroom exhaust fan on high. The temp inside was 86. This morning, house temp was at 62 and much of the prior wet spots, each about a three by two inch area, were nearly gone! We will have the main floor heated by this afternoon with a 27,000 btu direct vent wall fireplace LP gas fueled. The basement has had at least a few months to cure but I suppose it will still put out some moisture. My question now would be, should we remove the Tyvek? The north side of the house is not sided, Vinyl unfortunately, so no insulation value there. I'm betting a fiber board sheathing would have been a better choice with 1/2 inch ext.plywood for corners? How long can we expect the drywall to dry sufficiently to allow final finish and vapor retardant paint? Should we install unfaced batts on top of the blown in fiberglass insulation in the attic or maybe just add another few inches of it to the exsisting 18 inches? Our exterior temps shopuld rise to the low 30's this Friday through Tuesday.Thank you again for your expertise.
*
Hi Kim,
I wouldn't loose too much sleep over the exterior sheathing.
As to the Tyvek, it should be fine under vinyl. You must have some kind of water-resistant weather barrier under the vinyl, as it is not a very weatherproof siding. Wind-driven rain gets through it pretty easily. The Tyvek has to be installed properly though; lapped so water always drains, and taped at the seams, and overlapping drip caps rather than running behind them.
There have been reported problems with Tyvek in contact with unprimed cedar siding, as the tannins in the wood break down the water repellent nature of the tyvek somehow. I've not heard of such problems with OSB and Tyvek.
There has been a fair amount of talk that Tyvek is a waste of money and unproven performer and that roofer's felt (tar paper) is as good or better solution. I can't say if that's so or not.
I'm hoping all factions will weigh in here on the merits of the loose-blown FG in the attic. I'm not going to be the one to open that can of worms. Then there's always the vent situation to consider ;-)
Yours,
Steve Zerby
*
Hi Kim
Thanks for the most undeserved compliments, my wife is still groaning. . . loudly. I was already following this thread from the begining and thought that you were getting some excellent advice especially from Steve and M.Duval.You asked specifically about adding blown in Cells(?) to the stud bays to help with the poor installation job, and I would like to defer to Fred L. on that one because he's been known to do that sort of work. Barring that why not consider sheathing the entire exterior with one of the high R value Rigid Foam Insulating Boards, (extruded styrofoam R5/", Thermax polyisocyanurate R7.2/", Glasclad compressed f/g with one Tyvek type facer R4.5/") They're designed for this application, and can be edge sealed, strapped over etc. You then realize the added bonus of adding a thermal break to the structure so the actual 'system R value' is better than the accumulated R values, although with your suspect f/g batt installation you won't realize the maximum value.
I'm glad to read some of your moisture stain problems are dissipating, as mentioned by the others they could come from a myriad of problems, most of them bad.
A couple of details that could be clarified; current information on this board says that a special Vapour Retardent Paint is NOT necessary. . . a couple of coats with ordinary latex will do (the research supporting this was quoted on this board by Gene Leger,I think). You probably don't have OSB (Oriented Strand Board) on your exterior, just ordinary Aspenite/Flakeboard or what ever you Americans call that stuff. OSB is used where shear strength is necessary and in Trussjoists and the like. You're far better off with out any exterior fibreboard sheathing, it's only recognizable attribute is it's price. If your Tyvek was installed as Steve outlines, and is still in good shape you might as well leave it on (says he resignedly) unless you're going to add some RFIB's otherwise, 15# building felt remains my product of choice (we call it Tarpaper). I have an extremly low opinion of both Houswrap and Vinyl but as Fred wrote recently they're perfect together, they'll each last about 20 years. And finally I would suggest that if you're going to go to the trouble of blowing in more attic insul, why not give cellulose a try, the attic appears to be its ultimate application. I seem to recall reading not long ago that blown in F/G chunks have less R value/" than batt F/g, but if, after wards, you hear loud noises coming from the attic, you'll know it's the two materials dukeing it out, sorta like Fred & Bill & me.
Good Luck (with your old man too)
Patrick.
*Hi Patrick, You might not find this note stuck way down on the bottom of this other topic....but if you do I'd be interested in hearing more about how you sheath the outside of your homes. I used to build a lot of homes in a manner similar to what I think you do.Am I right in that you use plywood on the corners and sheath with foil faced foam insulating board? Do you then just tape the joints and leave it or do you then cover the whole structure with some kind of water shedding material? What types of siding do you usually install over this type of sheathing? Hope to hear from you.....
*
Patrick,
I like your suggestion about the rigid foam. I know it's pretty common practice, but has there been any informed debate about whether putting such a non-permeable product on the outside of house can cause problems by trapping moisture behind it?
Ignorantly,
Steve
*Pat - Two things.I was told by the manufacturer that Glasclad was no longer available. I called immediately after seeing it in the article in FHB.Polyisocyanurate would not be a good choice on the outside of the wall because the foil facing makes a great vapor barrier - stopping moisture just after the sheathing - rotting the walls.-Rob
*The slab heat may be drying the moisture out of th floor extra fast. Ventalation and another heat source ( not unvented kero or propane!!!!) durring construction should help untill things stabilize. Also make sure that you have soff. and ridge vents. Make sure that the inside of the walls are much tighter than the sheathing side.
*Kim after reading thur this I wonder if your house got soaked before your contractor got it weather in. I had a problem like yours a few years ago and the framing got VERY WET and then froze. After installing sheet rock and heat to the inside we found wet spots on the bottom of drywall. After removing a few pieces we found that as the studs thawed out they dripped water to the bottom plate and it was carried out by the drywall. after removing a few pieces we installed some dehumidifiers and some heat the problem cleared up. We removed some more drywall to check the fiberglass and found everthing ok.Let us know how this turns out
*
Hi Steve
I thought you were right up on all the arcane discussions on this board. . . LOL. One of the newest 'concepts' is to provide an impermeable 'Air Barrier' on the outside, which then effectively stops any possible convection through the wall, thereby eliminating possible condensation due to convection, thereby making a 'vapor barrier' redundant, and allowing for the somewhat easier to achieve "Air Vapour Retarder' that painted d/wall becomes. RFIB is ideal for an Air Barrier if it is carefully installed and taped/caulked at all seams. My choice would be XPS for both $$ and impermeabilty when the shiplap style is used and caulked at all seams with acoustical sealant.It lends itself to virtually any exterior tratment.
Rob,
I sorry to hear about Glasclad although I'm quite sure it's still avaiable to me in Ontario, my supplier still lists it in the price quote I get each month, although I haven't bought any in about 6 months. I've only used it once for it's intended purpose as an exterior insulating board, usually ripping it up to create insulated vent shutes in cathedral ceilings, a practice that new information from this board on so called 'hot roofs', and an agreeable change in our Provincial Building Code, has caused me to re-think. If you read the first part of this post you'll see why Thermax would make an 'ideal' exterior insulater. A special metal tape is available to seal all butt edges; the combo. of these two products gets a bit pricy though, compared to XPS and if the info. that I've read on this board about it degrading over time from R7.2 to R5.5 is accurate it may not be worth it by comparison.Although the foil facers remain an attractive detail for me.
The entire approach of incorporating an exterior RFIB has many things going for it: the aforementioned Air Barrier, thermal break for the framing structure, and removes the need to frame exterior walls with 2x6's which 'new information' from Gene Leger among others suggests is a supreme waste of wood.
Regards
Patrick
*KimFurther to the above, I found the source for the info. about R values. I suggest all interested party's look up FHb #100, March '96, and a well written overview of 'then current' insulation materials written by Alex Wilson, then editor & publisher of 'Environmental Building News' in Brattleboro, Vermont (800-257-7300). I haven't had the opportunity to check out whether a web site is now available. . .maybe one of you webizens could go surfing and report back? FWIW, I checked out the two following issues and there were no critical letters printed about his article.His chart lists f/g batts at R3.2/", blown in f/g chunks at R2.2/", and BIBS ( Blown Fibre with Binder) at R3.5/" (in an open attic config).Blown cellulose (loose) at R3.2/" and wet spray cell.(dense pack?) at R3.5/". "Contractor-applied" Polyurethane (Gene L's fave.) is R6.2/". No mention of Icynene (spelling?). Needless to say, none of these R values takes into account quality of installation or other "system factors" that always play a part in real wall performance. . . but as a "general reference" the are useful.RegardsPatrick
*AddendaOnce again this #@*#@#@ fancy software Sean bought is screwing me around, whenever I try to edit what I've already posted it wants me to sign in over, and over and bloody over, and won't accept it when I do. Maybe it's tryin to tell me something Anyway. . . the proper term is Vapour Diffusion Retarder (VDR) not air vapour retarder that I wrote above.Aint technology wunnerful. . . blaaaahhhh!!!!
*Hi G.Even though my Provincial Building Code abandoned the requirement for corner bracing in exterior walls some years ago, I've never felt comfortable with what I perceive to be inadequate racking strength, so I've continued to sheath all exterior walls with 1/2" plywood, applied horizontally, botttom to top. Because ply is strongest when applied horizontally I've never seen the value in applying it vertically at the corners only, and infilling with RFIB, as you suggest. I routinely sheath completely with ply and if an exterior RFIB is to be installed it goes over the ply. Now that I have embraced the concept of a tight Air Barrier on the exterior I will pay even more attention to 'sealing' the joints in the RFIB either with caulk or tape depending on the RFIB product used. Previously I would apply a layer of 15# felt/tarpaper somewhere in the sandwich, and strap the RFIB for application of any type of vertical or horizontal siding, or brick veneer (no strapping req'd) My personal Favourite being Board & Batten rough sawn Western Red Cedar.Getting awful tired of shoveling snow, and its only just beginning. . .Patrick
*AddendaThe chart referred to above does include Icynene under the heading "open-cell polyurethane" and gives it an R 3.6/" in open cavities & R4/" for closed cavity (stud bays).Patrick
*
Kim,
Did you get lucky and lose the a--hole and keep the contractor? Please realize that as one of my suppliers said in paraphrasing a rude slogan/bumper sticker: "Construction Happens".Worry more about paint colors in various rooms.
And that is not a sexist remark, I mostly mean for you think about more interesting things. Once the drywall is up it really goes into a place that can be home. Enjoy this, you are not worried about the 70's color scheme the other owners found terrific.
*
Bill,
Yes! The subfloor had an inch of snow on it(shoveled off) before the walls were framed. Earlier we had rain for a few days and the builder had not covered the subfloor with a tarp. Area between the rim joist and first tji joist, about 10 inch wide, I discovered had wet fg batt. I removed all batts in the floor joist end bays and it dryed out in a day. Still some moisture in north and west floor corners where I had not spray foamed between the subfloor and sole plate. The builder will do this today I hope . If not then I will do all floor to sole plate seams myself tomorrow. Seems like I should not have to do this "patch up work" when I have paid for the builder to do it right..but experience shows had I filled these seams in October instead of assuming the builder would do it,..well you know the rest of the story! Also, on his behalf I must say he discovered how the crew had installed the blue foam soffit attic vent chutes too far inward allowing an uninsulated top plate.
Thank you for your knowledge.
Kim
*J.D.The contractor is still there. He has one remaining payment of about 10,000 dollars to keep him "concerned". Do you think most builders routinely lay a sill sealer foam strip between the sole plate and subfloor? Kim
*Dear Patrick,Thank you for your advice. You just saved me alot of $$ by canceling the vapor retardant sprayed primer and going with two coats of good latex. If I understood you correctly, this is good? Brektime has been my saving grace. Wish I would have researched theses things more closely by reading Fine Home Building sooner. I just got the subscription a few months ago , a few months too late. The Magazine can post my notes as a strong attribute to their fine publication!Kim, alive and warm in Northern Minnesota.
*
Hi Kim,
A lot of builders won't "routinely" do anything extra unless you press them, and they still may not do it unless you watch them especially if it can be hidden with drywall. I use a foam strip or butyl caulk between the sole plate and subfloor myself. I dont believe in poor construction as a way of getting ventalation. I don't think that 2 coats of latex is a good vapour barrier, I use latex in the bilge of wooden boats because it breathes. Icynene and possably cellulose are the only insulations that I would use without a vapour barrier. I keep humidity at 50% even in the winter and use a taped or caulked poly vapour barrier with cellulose ins. or Icynene without a VB or SIPS for all my construction.
P.S. I know what your weather is like, my father was born in Mtn.Lake MN and I havent built a wall with less than R30 in over 20 years.
*Hi Kim,I have had good luck with Icynene. They have two versions, a fast set (5 seconds) with an r3.6 and a slow set (about a minute) with r4.0.
*
'b My builder did not do something right when installing batt insulation. After the drywall was up we noticed more wet spots on the top and bottoms of most walls. Walls are taped but due to the frost and wetness they have stopped with the taping and finishing. The exterior walls are 2x6 with Tyvek over a 1/2 inch o.s.b. sheathing. We heard that Tyvek is not a good choice over osb panels. A BossAire ERV unit will be running tonight to help dissipate excess moisture but I believe the problem is worse than just excess humidity. We fixed the corners where two studds were perpendicular to each other and void of batt insulation. Would fiber board( BuiltRite) on the exterior work or should we just hope that our builder can tear off sheathing to repack the insulation?
Desperate in Northern Minnesota'
Kim (nearing divorce because it was I who hired this contractor)