How to Install Sheet Vinyl Flooring?
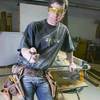
It has been a long time since I installed a sheet vinyl floor and I am looking for a refresher class.
I am going to give my bathroom a facelift (new toilet, floor, and paint) because I can not afford to take it totally out of commission until I set up a shower somewhere else in the house (basement, most likely).
Two boys have already grown up in this house (built 1957) and a third (my son) is doing so right now. Let’s say the boys’ ‘aim’ was less than optimal over the years. I plan to remove the toilet and crumbling tile floor, remove the underlayment, replace with fresh, clean underlaymenrt and then use a sheet vinyl remnant as a temporary floor until we can really dig in and re-do the whole bathroom.
Peel and stick vinyl tile would be quick and easy, but there’s a seam every foot, and I would like to avoid seams.
There is currently 1/2-in.plywood underlayment and 1/4 in. tile. I plan to replace with 3/4 in. underlayment before the vinyl.
Some questions:
What is the best underlayment? Is Advanteck OK, or is all OSB unacceptable?
Should I use more than one layer, so that if we decide on a tile floor when the actual renovation happens, I can remove the top layer of underlayment?
Any tips or comments on floor patchinh compound?
Any tips on cutting the sheet to get a tight fit along the tub? (two of the walls have hydronic baseboard heat, so the edges will tuck underneath, but the tub line will be visible.
Gluing strategy –just lay down the floor, fold back one half and glue iy down, then repeat on the other half?
Thanks in advance,
Dan
Replies
Dan
I would work the subfloor/underlay ht. to give you the proper level for your tile later. Remove what is necessary to provide a decent subfloor, add 1/4" vinyl underlay and lay down the sheetgoods. Remove both sheetgoods and underlay to get you ready for cementbd or whatever and ceramic.
Make a paper template of your finished floor, place that over the sheetgoods and cut to the pattern.
Check on your vinyl, much of it is perimeter glued only now. Glue along the tub and then add a beautiful caulk bead at that joint.
Nope, advantech or regular osb is not a proper surface.
I use Dependable brand seam patch. Do the seams (some say the staples also (( but only the cheapest vinyl will telegraph narrow crown staples)) ) real nice, lightly sand them smooth (a sanding block is fine).
As usual, doesn't hurt to get the manufacturers specs and install instructions just in case. Oh yeah, read them also.
Yeah, I second the paper template approach. A couple of us did a bathroom in a tornado-damaged home some years back, had only a vague idea what we were doing, but used the paper template and it turned out great. (This was an especially difficult situation because the piece of vinyl was irregularly shaped and about 1/4" short in both directions.)
We bought up the entire stock of brown wrapping paper in the small town to make the template. Just did the template around the edges (open in the center), taped together well so it held its shape.
The reason for folding back and doing half, then the other half only becomes obvious when you do it. But it works real well too.
Thanks.
For the sake of others who may stumble on this looking for information,
Why is advantech or osb unsuitable?
Is a caulk bead really the best way to finish that joint along the tub?
Is there any reason that I can't use felt paper for the template?
Have you caught on that I am trying to make a wikiarticle that we can publish in the blogs or magazine?
Thanks again,
Dan
Why is advantech or osb unsuitable?
Because the vinyl supplier says so in it's suitable underlay info.
Is a caulk bead really the best way to finish that joint along the tub?
Well, what do you have to offer that's better? I think running the vinyl just under the lip of the tub would be better, but you can't do that in just a flooring change. You do want to seal the joint-that is important. A pc of wood isn't good, it's need caulk behind, paint wouldn't hold up if constantly dripped on. Plastic? sure, but you still need that bead to seal the vinyl from water intrusion.
Is there any reason that I can't use felt paper for the template?
None that I can think of besides trying to see a line and maybe some tar residue getting all over your new vinyl which could be cleaned off with mineral spirits, but why? Further, taping pcs together would be an exercise in futility. Use rosin or protecto paper. Further, you only need a nice scribe at the tub, right? The wall perimeters cuts will be covered and don't need to be tight. Hold your paper's edge short of the wall less than the width of your straighedge (that you surely have). Fit the paper to the tub good and tape the rest down to hold it in place. Now, take your straightedge and use it to register all the walls, door opening, jogs etc. Slide it to the wall, draw a line on the paper. Do this all around-you've now scribed your perimeter. Lay the paper on the vinyl and have at it. Final triimming can be done with a sharp knife around casing's you didn't undercut etc.
I didn't catch on.
Might want to ask for advice on seaming-in case someone buys a pc of vinyl that's too small to do one pc and their too cheap to buy something bigger to make it easier, or they screwed up the first pc because our directions were lacking.............
Edit: What the heck are those dots on the left-outside the message border line? that went away when I edited........Odd, the message compose box looks different than the printed message.
Yeah, I can't see that felt would work very well -- too stiff, too fragile, too hard to tape together. Plain housewrap would probably work, but remember that you only need the paper around the edge -- no need to cover the center. (And it's probably better to not cover the center, so you can stand in the middle without standing on the template.)
Seams
Each manufacturer seems to have thier own seam kit now days. Armstrong, Manington, and Congolium are each a little different in the method they use to seal a vinyl seam.
Basic pattern matching and overlay cutting are covered in the installers guide from each mfg, Mannington use to have a neat little patern match mark on each edge of the roll and enough of a clear margin area to give you a nice overlapp for the cut. Don't know about todays products. I let my certifcations lasp many years ago for both Mannington and Armstrong. Ya gotta have a good set of knees under you to do a lot of vinyl work. Mine aren't.
Don't think I ever used a template for any sheet good floor. Register marks for center lines and a chalk line for seam locations, then roll, cut and glue. A sharp razor knife and a couple of stiff blade narrow and wide putty knives along witha 6' steel straight edge and a 30 # roller. Some of the later products I installed were edge glue only and one I remember was no glue except at a seams or at a tub, shower or toilet. Shoe mold and staples were used a lot in the late eighties. I didn't care for them, but by then I was about done with vinyl floors.
GP use to make an excellent osb type underlayment. Most manfactures speced it for thier products, but I don't know what they call out now.
Dependable is a great product for cracks and seams. Use the liquid vinyl mix for the the best results. FloorStone is another good one, but harder to work with because of the faster set time and hardness after cure. (kinda like Durabond vs. Easysand setting compounds).
use felt paper for the template
When you make the first template, you often will not make an exact cut. You want to be able to tape an 'extension' piece of paper to the edge to make a better more exact cut.
For floor area as small as a bath, a few taped together flattened cardboard boxes are much better than paper, the stiffness avoids errors due to folds and crinkles.
One other hint, esp on larger jobs. The big box stores often short you by 2" if a novice does the cutting (cuts on the wrong side of the bar). I did my 24 yard kitchen and had measured exactly for pattern match, etc. and had to splice on 2" under a kickspace - HD did retroactively refund $100, but it was a pain. So, unroll and measure your sheet good before the very first cut, you may need to return it for the correct size piece. My roll was 30 ft. long, had made the first cut before doing the final unroll, my mistake there.
I'd posted the HD shorted length episode here a few years back, somebody not a regular (but a nose in the air 'pro') said you should always order an extra 18" - what a waste, person had 'added' that sheet flooring was not a DIY job. What a jerk. Think Paul told him 'you tried to pick on the wrong DIY' <G>.
OSB products can have loose fibers on top that will effect good adhesive bonding. They can be effected by moisture and swell, particularly on joints.
Caulk is the best way to seal edges but it will need renewal in time. Vinyl base can be used but isn't very attractive and it won't seal out water, unless you caulk it.
Felt paper is too fragile, easily tears and may transfer black marks to the flooring. If you have some Grace Triflex left over from a roofing job, it makes for a nice template material, otherwise, kraft or rosin paper can be used. I think there is a special paper that is available for templates that lays nice and flat. Typically, some holes are cut in the field of the template so a piece of tape can be placed over them to hold the template flat and correctly in place. They can also help to see line up with patterns in the flooring.
Most modern vinyls are perimeter glued only. Many experienced installers cut the vinyl in place like wallpaper, I wouldn't try it. Don't pull up old vinyl and try to use that for a new template, it often shrinks as much as 1/2" when taken up. Don't use cheap or small shank screws on the underlayment, heads can break off and then transfer through the flooring. Cleanliness is paramount. The smallest piece of debris will eventually show, another issue with OSB since tiny splinters often come loose.
One point regarding the template: You need a space somewhere else, at least a couple of feet larger in all directions than the room where the vinyl goes, where you can lay out the vinyl with the template on top. Often, of course, this space is a finished area, so you need a piece of plywood or some such to put below the section you're cutting as you cut the vinyl. And beware that the back and cut edge of the vinyl is often fairly abrasive, so don't let it rub against finished surfaces.
(And be sure to mark "TOP" on the template in several spots!)
Template
I'm a pretty advanced diy. The last time I did sheet vinyl, I used the scraps from the masonite beadboard I had just installed in the pantry. They worked better than anything else I have seen used.
They are about an 1/8th of an inch thick. The stuff I had was white, so scribe marks stood out really well. I scribed it, cut to just outside the scribe mark with a jig saw, and then free handed to the scribe on my big router table, (the big router table is a 3-0 X 6-8 solid core door with a hole in 3-ft from the end fitted to the router plate, and a piece of 8-ft long 3X3 aluminum angle as a fence), using a 1/4 inch carbide up cut bit.
Trimmed it to the scribe line, and then checked it against the tub.
The resulting template is hard enough to guide the blade against.
Anytime I go to HomeDesperate I check the cull pile for offcuts of the masonite bead board, and the 1/4-inch vinyl faced mdf they sell for cabinet backs. Both make great templates.