119994.1 | |
Home (built in 94) is in Texas and attics tend to get a bit warm 6 months out of the year. 2 HVAC units for 3300sf home are in attic, along with 2-40 gal water heaters (yup, I said the same thing, WH in the attic?), Anyway, HVAC could be near replacement stage, now 15 years old. Need your “expert” opinions – If you were to replace HVAC units, prior to new installation, would you . . . build an insulated cavity in attic for the HVAC to help new not work so hard to cool home? Other ideas to increase energy efficiency? Thanks for your opinion |
Discussion Forum
Discussion Forum
Up Next
Video Shorts
Featured Story
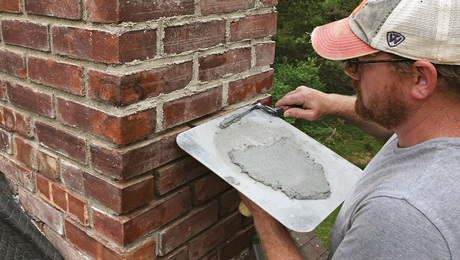
Old masonry may look tough, but the wrong mortar can destroy it—here's how to choose the right mix for lasting repairs.
Highlights
"I have learned so much thanks to the searchable articles on the FHB website. I can confidently say that I expect to be a life-long subscriber." - M.K.
Fine Homebuilding Magazine
- Home Group
- Antique Trader
- Arts & Crafts Homes
- Bank Note Reporter
- Cabin Life
- Cuisine at Home
- Fine Gardening
- Fine Woodworking
- Green Building Advisor
- Garden Gate
- Horticulture
- Keep Craft Alive
- Log Home Living
- Military Trader/Vehicles
- Numismatic News
- Numismaster
- Old Cars Weekly
- Old House Journal
- Period Homes
- Popular Woodworking
- Script
- ShopNotes
- Sports Collectors Digest
- Threads
- Timber Home Living
- Traditional Building
- Woodsmith
- World Coin News
- Writer's Digest
Replies
Where in Texas will matter. Lattitude and Altitude matter, Uvalde and Seguin are not too far apart but have singificantly different weather. Wichita Falls needs a very different answer than Waco which is different from Waller, too.
In much of eastern and central Texas, your best bet is to insulate the roof deck and the attic threeby. Just running the a/c units in a conditioned space is not really enough--you still have al lthe ductwork in that 130-140º attic. That R-6 wrap on the ductwork not very much at all versus that sort of delta-T (and that presumes the ductwork is sealed up tight in the first place, which is not terribly common).
From equinox to equinox roofs are getting 12 hours of solar gain on the entire surface, which then counducts through the deck and into the rafters. The rafters are tied into the framing, and you wind up pouring heat into all that mass.
Venting the atiic, whihc is often offered as an answer is a bit like leaving your car windows cracked open a inch or so. Which will make a difference in either your car or your house--about 4 to 5º in either case. Allowing high-temperature, high-RH air into an attic does not suggest cooling in any realistic sense. Stand under a carport or polebarn with 100% ventilation to see how that works.
So, your house, that we are trying to condition to about 78º, say; sits under a space filled with 125º air (that's 47ºdeltaT); sigificantly different than the walls, which might have 96º ambient, only 18ºdeltaT.
Best answer is to insulate under the shingles and over the roof deck--keep the heat out of the framing as much as possible. That can be complicated with some of the "modern builder's style" houses out there with 10/12 and 12/12 roofs--35-45 squares of roof over 3k sf houses is a lot of material to install. In retrofit, that leaves insulating under the deck, which has it's own set of problems. In your case there is the additional problem of combustion air for the WH (will guess that they are gas).
Now, there is yet another benefit of moving the insulation plane to the roof, you get your attic back as a storage area. You can put deck up with plywood or diagonal skip flooring without needing to rig some way to "fly" over 15-24" of insulation. This can make the Design Committee very happy. Not haing forgotten tea candles melt over the xmas decorations in the attic will also make her happy, too.
Share some more details with us, we can narrow down your options.
As of 1300 cdt, KCLL reports 84º HI of 88º with 59%RH at 69ºDP; I'm seeing 82º at 38%RH in the house; with 7 hours of near-continuous sunshine, attic is reading a nice mild 118º @ 48% RH.
Thank you for your expertise. Home is in Dallas.
Part of the attic "upgrade" is removing/replacing the 2 40 gallon gas WH (also 15 years old and dont use 2nd WH) for 1-50 gal. gas WH.
I originally planned to have the HVAC contractor re-seal all flex ducts at junctions/outlets and have also considered spray foam on exposed flex ducts.
Please provide more details for "moving the insulation plane to the roof". Are you referring to re-roofing/redecking with foil-faced osb sheathing or re-roofing and adding attic foil stapled on roof deck prior to felt?
Read thishttp://www.buildingscience.com/documents/reports/rr-0111-placement-of-ducts-and-hvac-systems-in-conditioned-space-an-overview/view?topic=/resources/technical_resources
Are you referring to re-roofing/redecking with foil-faced osb sheathing or re-roofing and adding attic foil stapled on roof deck prior to felt?
Generally, yes; specifically, no. Foil-faced does not do that for you under three plies of shingles, and at least one layer of roofing felt.
The foil-faced osb only works on the exposed portions between the framing, and then only when clean (and in relatively still air, too). Where it is in contact with the framing, the conductive gain is far greater than the "loss" the low-emissivity foil nets you.
No, from a good, bare, roof deck, you can go up with 2-3" of rigid foam, then roof over that. The desired finish roof will drive the details for the roof install, whether it is wood or asphalt shingles or metal roofing or some other.
"UP" works as there's a lot of room to work, you have generally good access to flashings nad the like, and can reset them neatly. Downside is having a new, thicker, roof edge to detail, which can take finesse to handle. Other downside is with steep roof pitches (over 9/12)--it's a lot of squares of material to install on a very steep slope.
"Under" is where you move the insulation off of the pourous ceiling,and to the underside of the roof. Framing and deck are still heated by insolation, but, you are "defending" against that heat at the sourse, slowing it down on contact, as it were.
In retrofit, that's a number of methods. Rigid foam in panels between the framing; scrim cloth over the framing with dense-pack cellulose behind that; foam sprayed directly to the deck and framing. The first two benefit from being finished with 1" of foam sheets cross-wise over the framing. Now, some jurisdictions will then want a fire-resitant finish over the foam sheets. A spray foam contractor can apply a fire-resistant over coat in the same trip into the attic, which can be faster.
"Under" works best where the roof is simple. Downside is that all the areas narrow down to nothing. Also, everything has to come in through whatever attic access there is (which can be bad in trusses; worse in the multi-plane, goes-every-which-way, stick-built roofs common now a days. Also, every roof penetration is an excitement. The labor hours are lowest using spray foam, but that is also the highest material cost. Winds up being a stack of compromises, as does much in life.
Ok, Dallas County is '88 UBC; City of Dallas is '06 IRC (and also the Dallas Existing Building Code). Looks like you'd be required to have some material that confers FSI<25 & SDR < 50.
Otherwise you are looking at reinvent's excellent buildingScience reference for some sort of Raised plenum to site your AHU. And that will then have some complexities in Dallas for needed service access. Also, the ductwork really needs to also "live" in conditioned space, too.Occupational hazard of my occupation not being around (sorry Bubba)
Suggest you go to and check "general discussion section" for other comments on your subject.
Do you have a closet you are willing to lose? That is an option for the air handler. Otherwise I would build a conditioned dog house in the attic.
All flex would be minimum R8... I know R10 is available.
All inner flex connections would be sealed with mastic to their respective metal collars. Collars would be sealed to the ductwork. If necessary, collars would be sealed one day and flex connected after mastic has dried.
Air filters would have gasketed doors.
Furnace cabinet doors (at least the return blower section) would be gasketed and sealed as much as possible.
Ductwork and fittings would be installed to Manual D specs. All joints would be sealed... especially the return side.
A load calculation would be done.
A California Energy Commission (CEC) research project (PIER) researched the benefits of enclosing mechanical into the thermal envelope. The results were favorable (of course). Downside is the effort it takes to do that ... particularly in existing construction. Enclose it ... make equipment more accessible to promote bettter maintenance.
You should be able to look it up ... or just do it ...