*
Anyone have any experience with hydraulic elevator installations? Specifically, I have been told that the contractor will fill the shaft with sand after the piston is installed to keep it from shifting.
Discussion Forum
Discussion Forum
Up Next
Video Shorts
Featured Story
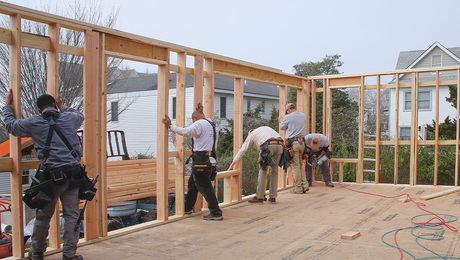
A rear addition provides a small-scale example of how to frame efficiently.
Featured Video
Builder’s Advocate: An Interview With ViewrailRelated Stories
Highlights
"I have learned so much thanks to the searchable articles on the FHB website. I can confidently say that I expect to be a life-long subscriber." - M.K.
Fine Homebuilding Magazine
- Home Group
- Antique Trader
- Arts & Crafts Homes
- Bank Note Reporter
- Cabin Life
- Cuisine at Home
- Fine Gardening
- Fine Woodworking
- Green Building Advisor
- Garden Gate
- Horticulture
- Keep Craft Alive
- Log Home Living
- Military Trader/Vehicles
- Numismatic News
- Numismaster
- Old Cars Weekly
- Old House Journal
- Period Homes
- Popular Woodworking
- Script
- ShopNotes
- Sports Collectors Digest
- Threads
- Timber Home Living
- Traditional Building
- Woodsmith
- World Coin News
- Writer's Digest
Replies
*
We pour concrete around the top of the casing as part of the elevator pit base.
Gabe
*b WBA At Your ServiceDitto Gabe. I can't imagine why you would want such a porous base. We are in the process of doing one now and the specs call for concrete with a sump pit formed into the floor.
*Ok, I wasn't clear. When the elevator is installed, there is a shaft drilled for the piston. The shaft is about 20" dia and the piston is about 8". A concrete slab is poured around the top of the hole to support the piston assembly and seal off the hole. The elevator installer puts in the piston and plumbs it damn near perfect, cause if it's off by a degree, the runout at the top of a 40' piston is excessive. Anyway, I have been told that it is normal practice to carefully fill the void between the piston and the walls of the shaft with sand to help keep the pistion plumb.Tim - how many floors will your elevator serve? What brand is it? I assume the GC drills the shaft - who installs the piston? I have been told that in south Florida Otis has the GC install the piston, but I don't believe it. Why would Otis not do such a critical step themselves
*I've got Otis installing 3 piston elevators in one of our buildings and we drilled the holes but they installed the pistons etc.Other than the fact all elevator companies live in a dream world that doesn't include schedules and being team players, they eventually get the job done. The bottom line is that they (Otis) is responsible or should be for the piston's installation and plumbness. It's their elevator and build under their licence.Gabe
*Gabe, I can't get into a lot of details now (probably the important ones) because we're getting our corporate attorney involved in the dispute and I don't want to take a chance on leaking somehting that might turn out to be a deal killer. It's a story that I look forward to telling in a few weeks. But tell me what th specs say concerning sand filling the shaft after the piston is in place. One of the elevator mechanics I was talking with, and I have to be real careful here because I don't want to get him in trouble, said that they normally put sand in the bottom 3-4 feet of the shaft, but sometimes the GC and/or architect gets hard nosed and makes them do it by the book and fill the entire shaft.
*Ed, I will do two things for you, first I will review all the specs on the elevator and then I will call the Otis foreman into my office tomorrow morning and report back to you on my findings asap.Gabe
*b WBA At Your ServiceEd, Ours is only servicing a 2 story building that has a very shallow piston. It is not an Otis, but at this point, I'm not sure who is doing the job since we just started the project 2 weeks ago.
*Okay here's the update.In our case the hole was drilled into rock, top to bottom. An outer protective casing was then lowered into the hole and because it already had a snug fit did not require any sand to secure it in any way shape or form.The piston assembly goes into this protective casing and is not secured anywhere other than at the top where we pour the concrete pad around the assembly.In the Otis general instructions and in most specs. sand is used to stablelize the outer casing, never the piston assembly which is free to align with the car during construction.Don't know what else I can tell you at this point but any direct questions you may have I can put to Otis here and it won't go any further.Gabe
*I would be deeply indebted to you for a copy of the Otis general instructions, especially if Otis' name is on the paper. Can you fax it? 210-283-6567. Thx.
*Ed, Otis has a General Contractors Instruction Book that it gives to contractors around here after they have been awarded the contract as a check list of items that they require to do their work.However, as you can appreciate, as GCs, we ensure that all the responsibility for their work including warrantees belongs to Otis and they have to follow our schedule or they are held in default. So the Instruction Book gets filed 86.I will pick up the copy at work tomorrow, along with the specs sheet and fax you the relevant sections tomorrow nite.Gabe
*Ed, Email me a mailing address and I will send you a photocopy of the book. It has a lot of pictures that will not fax well.Also had a long discussion with Otis onsite today and found out why they don't put sand anymore. If you were to put sand between the casing/hole and the pvc piston casing and there was a failure 20 or 30 years down the road, you would not be able to pull the assembly out to replace it because the sand would fall in and fill the bottom making installation of a new assembly impossible.Gabe
*>If you were to put sand between the casing/hole and the pvc piston casing and there was a failure 20 or 30 years down the road, you would not be able to pull the assembly out to replace it because the sand would fall in and fill the bottom making installation of a new assembly impossible. Maybe they could get something like a shop vac on steroids and get the sand out?-- J.S.
*Gabe & xJohn - you're both pretty much on target. The situation is that we're doing a replacement of our cylinder, and the sand in the hole is the item of discussion. Our cylinder is about 34 ft long (tall?) by about 8" dia. The shaft was about 20" dia x 32 ft (there was a gap between the top of the shaft and the top of the cylinder) and the entire space was filled with sand. The elevator mechanics had a hell of a time pulling the old cylinder. They used a 50t jack and some chain falls, and the best they could do was lift it about 3-4 inches at a time (actually, it was up 6-7, fall back 3-4 because of suction). Once they got it about 3 ft up, it broke loose and came out easily. There are two proposed methods of removing the sand: one is with a drill rig running on the elevator rails, the other is with a truck mounted vacuum. One source for the vac is Super Products in Wisconsin. I think they call it a Super Sucker. Didn't I see a picture on the back of FHB (or was it JLC) about a guy in Colorado (?) that uses one of these trucks to suck groundhogs out of holes for relocation? Anyway, pending resolution with the elevator contractor, that's about all I can divulge now. More to follow.
*Ed --Yet another reason to be glad we're not groundhogs.... ;-)All this grief leads to another question: Why a hydraulic elevator in the first place? Trying to think of pros and cons vs. overhead traction, the only reason I can think of for hydraulic is that you don't have to build a little room on the roof for the machinery.-- J.S.
*The building (and elevator) were built in 1968 and since all that's bad is the cylinder, it was supposed to be an easy upgarade. Trying to find space for a machine room above the elevator shaft would be difficult.
*Ed, Would running a garden hose into the sand help reduce the suction? Liquifaction of sand should allow removal of cylinder.
*The cylinder is already out, it's the sand that we're working on now.
*b WBA At Your ServiceWe use our local duct cleaning specialist for jobs like this. One hundred feet of six inch suction hose connected to a vacuum that is driven off of a PTO on a 460 ci Ford engine can suck any size particle you desire. Right into his truck or into a dumpster we provide.
*Ed, Check with your local gas utility company for a vac. truck. They use them to suck out stop boxes and regulator vaults.If the cylinder casing failed, I would not suggest sucking directly into the tank of a vac. truck. They don't want to clean thier tanks of your leaked hydraulic fluid. A better way is to fit 55 gal. open head drums with an in and out port for the vacumn hoses. As you suck through the drum it fills with the hazardouse waste products and sand. When the drum is full, move the lid to the next drum and start agian. The vactruck tank stays clean and the contaminated sand is already drumed and ready for disposal.All of that is assuming you can get a truck in close proximatey to the pit. If not they may have smaller trailer mounted models that you can get into the area . Barring that, get a really huge sucker and lots of hose.We have recased three hydraulic elevator shafts in the past six years, and used this technique successfully on each one. After installing the new casings the elevator contrator had to pump some type of mud mixture in around them. Our elevators serve four floors and all the work was done in the lowest level elevator lobby durring off business hours. Able Elevator was our contractor and they had all the eguipment and knowledge to do the job in about a week for each shaft.Good luck, Dave
*Dave, I think you and I are on the same page, but you're a faster reader. We're only to the point of removing the cylinder. What brand elevators did you have? Why did you recase them? Could you do that without removing the cylinder & piston? What was the purpose of the mud, and was thaty a requirement of the elevator manufacturer? Sorry for all the questions, but I'm trying to see how similar our jobs are, and how yopu handled yours.
*Jim, the casing on all three of our elevators were old metal sleaves, that had been coated on the outside with a wrap like you use to see on underground gas lines. We are near the Ohio river and have both a high water table and sandy soil. The elevators were installed about 18 years ago with the above coating and a sacrificial anode on the casings. Electrolic reactions did them in. We recased with reinforced fiberglass and only the next ten years will tell how good they hold up.The pistons were not removed from the cars. The cars were run to the top floor an then winched up another 6 to 8 feet on the original installation rails. This was all done with an A frame mounted on the roof above the removed ventialtion hoods (full size). Everything was secured and checked several times and then the pressure was bled off the systems. Since the casing were junk at this point, they were cut into managable lenghts as they were pulled out of the holes. A caution here is to pull the timer on you fire/smoke detection system, and get some really big exhaust fans to draw the fumes and smoke out of the shaft.As I mentioned we have some very sandy soil and as the casings were pulled it had a tendency to cave-in the hole. Not a total collasp, but enough to need to be sucked out. There may have been sand around the bottom of each casing, but with our soil it was hard to tell were one stopped and the other started. Water was also a problem, so the first hour of each night was spent pumping and disposing of what bled into the hole durring business hours.The recasing went fairly smoothly considering the amount of space there was to work in. The piston had only cleared the shaft about three feet so it was always in the way, even though it was pinned in the back corner of the pit.I believe the mud or what ever the slurry was that they pumped in around the casing after it was in, was to fill the voids created by the small cave-ins, and secure the bottom of the casing. I don't know how much was pumped in as I was off shift on that night.All three elevators are Murphy's.I hope this helps a little. My job was as an observer and expediter. I work as a facility maintenance man and am thus responsible for lock out/tag out procedures and safety when a project like this unfolds. We spit the weeks work between six men working double shifts with the graveyard shift going on to his day work and a day work shift rolling on into the second shift. It is kind of hard to fit all the pieces of an operation like this together when all I got was my piece of the pie. Our maitenance supervisor could help you more, but he is retired and turned into a bass tourniment fisherman.I'll ask one of our former elevator repairmen any specific question you may have. He also just retired, but like to talk, a lot.Dave
*Ed, kinda late to be asking, but hows come the guys doing this job don't know how to do it and have the equipment needed? Don't you get a bad feeling when the person hired has to ask you how to do what you hired him to do? Joe H
*Ok, here's the whole story. We have an Otis hydraulic elevator that was installed in 1968, serves 4 floors, about 34 ft. Back then the cylinders were 'single bottom' which means that it was basically a steel tube welded shut on the end. Otis discovered that there was a problem with the end rusting off, with a resulting fall of the elevator. Hydraulic elevators don't have brakes. Riders would probably not get killed, but it would sure mess up your knees, ankles, etc, and the publicity was bad.So Otis decided that all single bottom cylinders had to be removed by 12/31/01 or else they would no longer service them. The new style has a second plate welded about 6" above the bottom, and they are typically encased in a closed-end pvc pipe that is slightly pressurized to keep ground water out. Otis now requires a log to be kept by the servicing mechanic as to any oil that is put in the cylinder for topping off. Seems that at some of the elevators that failed, (not ours) the mechanic was adding several gallons every few months. That should have alerted someone that there was a leak, but, oh well.Anyway, we signed a contract for about $25k to have the cylinder replaced. Once the mechanics got it out, and that's a tough job, the salesman announced that they had found the shaft full of sand and debris, and it would cost an additional $8k to have it vacuumed out, or 2-3 times that to drill it out if the vacuum didn't work. They pulled off the job and waited for our approval of the extra expense. The mechanics that were doing the retrofit were nice guys, and we had several convwersations during the removal. Actually, they came from the construction side of the company. They said that the sand had probably been placed there when the elevator was originally installed, and that they almost always encountered it. That's when I started this discussion, trying to see if any of you had similar experiences.Oops. Wife is calling on somehting hot. I'll finish this later. Sorry.
*Ed, if I understand the story, the price quoted was misleading because there is or was a reasonable expectation that the shaft would be filled or partially filled with sand? Now the price is going to go up 30% to 100% if a drill rig is required? If the guys doing the job say it's almost always there it sure sounds like the salesman lowballed the job. One of your earlier posts mentions the GC getting hardnosed and going by the book, filling the shaft entirely with sand. That makes it sound like it would be a certainty that there was going to be some sand in there, and only a question of how much.Did you get any other bids? Any of them mention the possibility of this occuring? Joe H
*Now in the event of a bottom cylinder head failure, wouldn't the sand help to slow the fall of the elevator and protect the passengers somewhat? I'm sure it would help if the casing were full to the top.-- J.S.
*xJohn - I think the sand is placed to help keep the cylinder plumb. I don't think it would have much effect on escaping oil. I'm not sure you realize where the sand is. It is in the drilled shaft below ground, filling the space between the hydraulic cylinder and the earth. No moving part of the elevator touches the sand. After a number of years, I think the sand would compact somewhat, so there wouldn't be much cushion to it. Joe - you're exactly right, or at least that's my position too.Ok, here's the rest of the rest of the story. Sorry about the interruption.The salesman, who I can't stand, told me when they discovered the sand that it would cost us extra to remove it from the hole. I countered that sand is common in hydraulic elevators, and they should have anticipated it. He and the branch manager disagreed and we were at a standstill. After several letters and phone calls back and forth, I finally got hold of the regional manager in Dallas and explained the situation to him. I found him to be very professional. He listened to my side, and said he would be in town the next day to talk with his staff. He and the branch manager came to my office and we talked for an hour. My position was based on two points: 1- the sand was at one time very common, and they should have anticipated it being there. Surely this is not the first time they have encountered it. 2- they should have included the expected cost in their original proposal, either as part of the lump sum, or as an optional line item. Chances are that we would have agreed to pay for it at that time, or at least we would have known that there could be anadditional cost. He agreed on both points. Their position was based on a clause in the contract, and I quote: "Drilling work is not included in this proposal. If any obstruction, hinderance, ground water, or cave-in in encountered below the ground..." I argued that no drilling was required, and that the sand was not the result of a cave-in. We went back and forth a couple of times, politely, and finally he agreed to bear the cost of sucking out the sand with the understanding that if they encounter water or if the shaft collapses, then the cost is mine.Part of what bothered me was the attitude of the salesman. he has only been with them for two monts, and most recently he worked for a credit reporting agency. I can overlook his lack of experince with elevators, but not his style, and I explained that to his boss. He won't look me in the eye when he's talking, and he tries to be buddy-buddy and uses a lot of cliches and tries to deflect responsibility. Un-f**ing-professional. He was not involved in the original proposal, but the branch manager was. However, she has only been here about 5 months, having transferred in from the south Florida office. If I were going to meet a client for the first time, I would put my best foot forward. Hope I'm not being too picky, but I didn't feel comfortable with what she was wearing. Her skirt was a little short, and her blouse was way too tight. During the hour long meeting, she must have tugged at the blouse 10-12 times to try to keep the front from gapping open. At least she kept her mouth shut and let the regional guy do all the talking.We have had a maintenance contract with Otis ever since the elevators were installed in 68, and we have been pleased with their service. So no, we didn't get any other bids for the repair work.Here are two pictures of the top of the shaft (hope this works). There is a concrete slab that the guy is standing on - it's about 36" below the finished floor level an it is what is normally called the elevator pit. There is a gap below that of about 24" because the building has a dirt floor sub-basement; you can see the old wood blocking when they shored for the slab pour. Then you can see the 20" dia shaft and the sand. The sand stops about 48" short of the top of the shaft. Theree is some debris in the shaft, but that is from breaking through the concrete slab.
*here's the other picture, a different angle and closer.
*
Anyone have any experience with hydraulic elevator installations? Specifically, I have been told that the contractor will fill the shaft with sand after the piston is installed to keep it from shifting.