ICF Foundations – Why not used more?
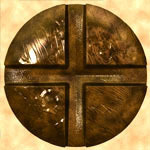
Maybe its because I live in a very rural Eastern Oregon, but why aren’t Insulated Concrete Forms used more in home construction, especially for foundations? It seems they are a time saver. Just wondering. Thanks!
Replies
Thank you for your question. The improper use of ICFs has been a pet peeve of mine for some time.
ICFs can be a time-saving method of construction and their insulating values are promoted at a bonus, but unfortunately the manufacturers fail to mention the disadvantages.
I speak from experience with a friend's raised ranch style vacation home, that was constructed with ICFs for the basement walls. The vacation home was built in Ontario, 2 hours north of Toronto (where commercial delivery trucks are driven on frozen lakes in the winter) . Being a raised ranch the basement was finished and because the ICF's were advertised with XX R value, no additional perimeter walls with insulation were installed.
When he'd arrive on Friday night in the depths of winter, it would take 24 hours before the basement was comfortable. Because one-half of the insulation was on the exterior of the concrete, one was actually slightly warming that massive concrete wall. Similarly when he'd leave on Sunday afternoon, that basement wall took 24 hours to cool down again.
When one understands this, several conclusions can be made.
1. The mass of the wall causes a delayed response to heating or cooling.
2. Heating the huge mass wastes energy. Construction of interior insulated walls is necessary for comfort and energy savings, which negates one of the advertised benefits.
3. R value, as a measure of energy efficiency, only applies to steady state energy transfer.--constant temp inside, constant temp outside. When the inside temperature is changing (night set-back thermostat, away at work set-back, etc), R value does not give a good indication of energy efficiency. The thermal mass that one is heating becomes an important factor.
Conclusion, ICFs are good where the temperature is moderate year round. Additionally, a climate where days are warm and nights chilly and thermal mass can provide energy savings is also ideal. Otherwise, be prepared to insulate just as one would a normal basement wall or a regular "stick-built" home.
It's really difficult to be certain how much insulation building materials are actually delivering. We only have information that manafacturers provide , and that can be hard to interpret. I always have had my doubts about ICF's because the walls are substantially concrete, which has an R-value of about 1 per inch. Sounds like your friend will have to do some retrofitting.
Thanks for the responses. I can see why that would be an issue. I guess what I'm really looking for is are ICF foundations, say for just a regular stem wall foundation, better than using traditional forms in terms of time and effort to get a foundation poured? It seems to me that the amount of time setting up forms vs. placing the foam block in place is a constraint, especially if doing more than one structure.
I think the short answer to your question is because right around the time you may have expected ICF's to become a more popular choice for foundations, the Superior Walls foundation system was gaining widespread acceptance among builders and now dominates as the alternative to poured concrete in many areas.
I'm not anti-ICF by any means but the question of what goes into the choice makes me think about some of the downsides/drawbacks to having an ICF foundation. First, in the "very heavy" termite risk areas (southeast and southern California), foam can't be on the exterior surface below grade or under slabs without an "approved method" of protecting the foam and structure from subterranean termites. "Approved methods" are not further developed in the code, so my guess here is this is a non-starter for most builders in these areas. So in other areas where burying the foam is permitted, the exterior below grade waterproofing is fairly straightforward as there are products designed for the EPS foam. Above grade you'd have to protect the soft foam with either mesh & stucco parging or maybe cement board and stone veneer. This step is not needed on poured or Superior Walls foundations, although I recognize it's frequently done for aesthetics. My point is, for many builders, it's a required extra step they'd like to avoid if they can.
On the interior, most ICF's I've seen still require a 15-min thermal barrier (ie 1/2" drywall). Though I imagine this is probably allowed to let slide by some building officials. Since you have to drywall it, you're probably going to need to run electrical, which means channeling-out the foam to run the wiring and place boxes. Again, required added steps that don't contribute any meaningful value over the alternatives. Poured concrete obviously can be left bare and Superior Walls uses a UL1715 fire test compliant foam and requires no additional thermal barrier so it can also be left unfinished. If you do want to finish the Superior Walls, there's preformed holes in the studs for wiring and steel stud faces so it finishes just like a wood-framed wall.