Can anybody give an incite on insulted concrete forms for foundation building?
Discussion Forum
Discussion Forum
Up Next
Video Shorts
Featured Story
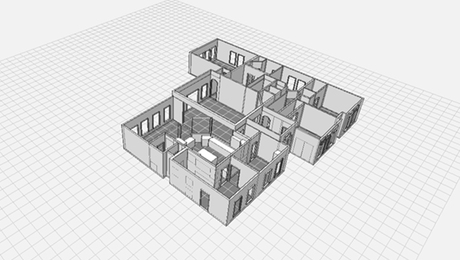
Hover's smartphone app offers an easier way to get precise 3D scans.
Highlights
"I have learned so much thanks to the searchable articles on the FHB website. I can confidently say that I expect to be a life-long subscriber." - M.K.
Fine Homebuilding Magazine
- Home Group
- Antique Trader
- Arts & Crafts Homes
- Bank Note Reporter
- Cabin Life
- Cuisine at Home
- Fine Gardening
- Fine Woodworking
- Green Building Advisor
- Garden Gate
- Horticulture
- Keep Craft Alive
- Log Home Living
- Military Trader/Vehicles
- Numismatic News
- Numismaster
- Old Cars Weekly
- Old House Journal
- Period Homes
- Popular Woodworking
- Script
- ShopNotes
- Sports Collectors Digest
- Threads
- Timber Home Living
- Traditional Building
- Woodsmith
- World Coin News
- Writer's Digest
Replies
I remember an article three years ago in FHB that covered it in great detail. http://www.taunton.com/store/pages/fh_toc_128.asp That'll be your best bet. The author name doesn't ring any bells, but there was likely a good editor that cleaned it up enough to make it readable.
(Tis a joke, the author is the current exec editor and sometime moderator of this forum.)
Hey -- I resemble that remark!
Most of what I wrote in that article still holds true. The one thing I'd do differently is use borate-treated ICFs. I think Reward makes them.
Andy Engel, The Former Accidental Moderator
There are also several threads here if the search feature is working.
Excellence is its own reward!
http://www.taunton.com/finehomebuilding/pages/h00031.asp
If you want I'll be glad to give you my experiance with them.. (very positive)
I will be glad to get any info from your experience with icf's.
If you want I'll be glad to give you my experiance with them.. (very positive)
Please do.
SamT
It was a breeze to use them.. I started out putting them down the evening I got them and by dark had three rows in place. I used a battery powered sawzall to cut them to fit where the corners wound up odd. I'd put them down and then spray the foam that glues everything together.. Take the time to make sure they are fully in place, if you don't by the time you get to the top row things will be pretty far off (more later)
After putting down three rows I wasn't at all tired (this was the first construction work I did so I wasn't in any kind of shape) bending the rebar was the hardest part and later when I got a bending tool it became a lot easier.. That weekend I traveled to Wisc. New car and the seats just didn't fit. 16 of steady driving hours and when I came back my back was terrible.. So bad that I wound up spending a month in bed under severe medication. My sister in law stopped by and hearing about my back problems offered to put the forms in place for me. (no she'd never done anything like that but it sounded easy and fun for her so she went ahead and put in place 4 more rows carefully spraying them in place..
leaving just two rows.
except she was rather careless.. she hadn't made certain the forms were fully in place. 1/4 inch here, a half there, and over there it missed almost completely. I was able to save it by some carefull cuts with the sawzall and refoaming.. I carefully braced the corners as instructions (they lend you a video)
Come the day of the pour I worried that the forms might not hold up with the refoaming and extra cuts so I had a couple of buddies standing around in the event of disastor..
Hour later the pump truck was cleaning out and I was writting a check for the concrete.. I learned later that I should have had a self leveling additive added and I wouldn't have needed to vibrate the forms etc.
All in all it was a great and easy job that I took a lot of pride in.. the hardest part of the whole job was holding onto the hose with the concrete. I didn't realize how heavy it was and had my buddies spell me every ten minutes or so..
I used reward forms but now I think I'd use AFM's forms since they are less expensive and more flexable regarding how they fit together and work (not nearly so critical)
cost wise it was less than a third of the lowest bid I'd recieved and the majority of bids were several thousand higher then the lowest guy! I like the ease which I can attach stuff (like sheet rock) to the walls. and while I was sckeptical at first, so I tried to pull out the screws and couldn't do it! the sheet rock was attached at least as well as typical stick built house.
The only thing I did wrong was get careless about the spacing.. (they have the attachment spot a fixed distance in each bloack so you can just measure and hit the right spot.. I'd cut up a bunch of forms and cheapskate that I am was determined to use every bit of each form.. If I'd matched the lines up I might have used another form but it would have been much easier to hit the spot for drywall screws..
Frenchy,
Thanks.
When I am able to go back to work, I am thinking of starting a foundation and basement business, 'cuz I feel that here in no-license Mo., it will give HO-GC's the best chance of getting a good structure and save them the most money by not having to tweak framing and sheathing to fit.
You would not believe some of the square/plumb problems from hacks around here.
I definately want to add ICFs and R/H to my repetoire.
Thanks for tip on self leveling admix, but I think I will still vibrate as I pour. (Belt and suspenders, don't ya' know.)
Now all I gotta' do is get the money to visit some manufacturers and attend their training and get certified.
SamT
I thought so too untill I saw it work on a retaining wall. It was absolutely amazing. Jammed into the the form was electrical rebar and drain pipe.. some places I didn't see how anything but water could flow, and that's exacatly what it flowed like. I had it chuted right out of the truck and on a 100 foot wall it flowed down hill just exactly like water I watched it slide around and over everything leaving absolutely no possiblity of air pockets.. the cement truck never moved. all 28 yards of concrete was pumped into one spot and it steadily flowed over everything! Kinda like watching a city flood! the high end was about 4 feet above the low end and it flowed so amazing I was awstruck! I had guys standing around with the vibrator and shovels to move the cement and no one ever lifted a finger.. It's like it sensed where it should go and it went there.. 4000 psi mixture that normally is pretty stiff and it flowed like water.. I know it wasn't watered down because when the driver first started to chute it it came out the way concrete usually does. When I compalined he checked the ticket and sure enough he needed to add a gallon of it to the 14 yards he was carring.. dumped it in and ran the mixer at high speed for about three minutes and out it came.. Magic!
Super plastisizer is what he added as add mix. Good stuff.
Sam, check out Integra and GreenBlock. Both products can be vibrated. Some products do not want you to use a vibrator. Also check on the largest lift you can make. Most mfg. recommend no more than a 4' lift at one time. Greenblock allows an 8' to 9' lift. Saves time and money.
I agree with you about some of the hacks that do foundations. I just did a layout for a local builder because his foundation man screwed the pooch on his last two houses. The guy does decent form work and manages to get the walls plumb, but doesn't have a clue about layout. Now if he can just set his footing forms and the walls to my pins, the framer won't have to get creative to square up the house.
Dave
Dave, thanks.
I went to the IntegraSpec site and saved the URL, then to the GreenBlock site and it is a flash site. I am on dialup and don't wait for flash.
Maybe I'll find an affiliate site later.
Anyway, thanks again.
SamT
bump, just for the fun of it.
Excellence is its own reward!
Price wise, how much do you think a 2200 sq ft basement will cost in concrete and icf forms. Oh, and what does AFM stand for and do they have a website?
It all depends..
I did it myself so I saved the labor it would have cost me. In general they were talking about $11,000 to do what I did and it cost me about $3500 adding everything in..
Your numbers might be similar
I don't know of a website, but then a lot of companies don't have web sites yet..
When you say including everything, do you mean both the concrete and the forms? How many forms and how much concrete did you use. If thats the case then $3500 is pretty inexpensive compared to $11,000, especially here in New Jersey. My husband is very good with his hands. I think he can do it considering all the little jobs he has done in the past.
I could look it all up but first I'd have to sort thru that pile of recepts on my desk.. That's several days work in and of itself..
But yeh, I think it was everything.. about 2500 for the forms and renting braces, scaffold etc.. about a thousand for the cement
You should know that the work is the tip of the iceberg..
You need to pour a floor and windows and doors etc.. plan all of the details in advance . I missed one electrical line and had to rent a big hammer drill with a 3 foot bit to get thru the foundation.. cost me an extra $45 dollars
think it thu, electrical, heat? plumbing etc..
It's not about being good with your hands.. (I'm average at best) but rather the ability to think the project thru and account for everything.. Maybe that's where you come in . Are you good with details? can you make a list of every system in a basement and then figure out how to accomidate it? If you can't figure out how it's done can you do the reaserch? Library is part of the solution but the best way is to go to where they are doing it and take notes of what goes on. spend a day or two watching then go home and go over your list.. Questions? come on line, there's a great bunch of guys here (and a few real nice ladies )
Frenchy,
The info I am getting from this forum is really an eye opener. I am going to be an owner builder. I think I can build my house just from consultations from you knowldgeable gentlemen/ladies. I am good with details and research. Oh that's how I came across this forum. I would appreciate info on the plumbing, heat and electrical. I will be doing a finished 9' basement. I am positive I will be using icf's. Locating a good and cheap form will be my next task. Recommendations will be highly appreciated.
Be very carefull with the word cheap..
There is cheap enough and too cheap. the differance is the too cheap will not do what you want it to do while the cheap enough will just barely do it..
With ICF's, failure is a real disaster.. you'll have quickly drying cement (maybe tons of it) and no way to get it where it should be and a terrible expense to chip it out remove the mess and start all over again.
Now it depends on your ability to deal with risk..
If you are a real gambler then go for the cheapest.. Just remember you are betting about ten thousand on it..
Cost of the wasted forms, cost of the cement, cost of busting up the concrete and cost of removing it, plus another set of forms and more cement..
Maybe ten grand won't cover it..
Now I can't honestly talk about anything other than the forms I've used (reward) and the forms I've seen used (AFM) a while back (several years ago Hometime did a segment on the forms on a house built on Lake Minnetonka
I'm considering going the ICF route too. I'm a homeowner considering an 8' deep basement for an addition to an existing house. I've got a pretty decent base of skills in carpentry, electrical, plumbing etc., but my concrete skills are basically non-existent at this point. I obviously have a lot of work to do to get up to speed!
The addition will go along the entire long wall of the existing house. The old house has only a ~6'6" basement ceiling height, whereas I want an 8' basement in the new place. The place is founded on good, stiff clay till and the ~70 yr old cast concrete wall and brick veneer above are good and straight (no settling)- but since I'm going lower than the existing footing, my options still seem to be either a bench which will eat up at least 18" of the addition's 12' width in the basement, or underpinning the entire wall. I've got a structural engineer friend of mine involved, so there'd be no problem getting the necessary underpinning details to do the job right- but there's so much manual labour involved in digging out under the existing footing and it has to be done in so many stages that it's got to be unbelievably expensive to get a sub to do it. Worse still, as a HO with no pull with the subs, I have nightmares about being stranded by the concrete guy while he does higher priority jobs for builders who have a better likelihood of giving him future business (the construction and renovation market around here is still pretty hot and no sign of slowing down any time soon!). So I'm tempted to get an excavation contractor in to dig the hole and then do the rest of the concrete work myself. Of course I'd be getting it inspected and having my engineer friend look the work over in progress too, regardless whether it was a sub or myself doing the work.
The ICF guys must have footing forms too, right? Not for the underpinning, but for the remaining 3 walls of the addition basement. Since I'll be using hydronic heating in the slab, I'd like the sides of the footing to be insulated. I presume you have to cast the footings and let them cure before you pour the wall, but you could start installing the ICFs over the footings the day after (since it'll take time to do that job correctly). Is that right?
I'm pretty confident I can do a good job of putting the ICFs in place for the walls. The wall pour would be nerve-wracking, but I wouldn't cheap out on materials (if I supply the labour, I figure I can afford to spend money on good forms and the recommended concrete additives).
With hydronic heating, there's a fair bit of work to do before pouring the floor slab- yet another reason for me to consider doing it myself. My biggest fear about the job, actually, is pouring the floor slab. I'd be tempted to do all the prep work and get a concrete sub in to do that job, so I get a floor slab with a decent finish.
What do you builders who have taken on the foundation work do about pouring the slabs? Do you just pick up the skills to do that job correctly, or do you get a sub in to do it?
Don't for gods sake! dig that manually! My back aches just thinking of it! rent a mini excavator! It will be money well spent. Spend an hour or so practicing with it before you go near your foundation. Try to get one with a zero tailswing. John Deere, Hitachi, Takahuchi, and Kumastso all have zero tail swing
you will have to pump the concrete. don't dream of chuting it. add a bunch of leveler to make your life easier.
'taint hard to float a reasonbly flat floor. I did mine, couple of tricks, go watch someone put one in (it will be the best afternoon you've spent, trust me) and make certain that you've got some extra help.. if things go well they just stand around and lean on shovels , if things go wrong it's buttholes and elbows..
Thanks for your concern and your suggestion, Frenchy!
The idea was to dig the foundation hole for the whole addition leaving a 45 degree slope adjacent to the footing of the existing building, but ending up at full depth everywhere else. The plan was to then muck out 3' under the footing 9' from the corners and every 9' between (by pick and shovel), dumping the soil into the middle of the hole. Hard work in clay till, that's for sure- but I don't trust myself to dig under the existing footing with automatic equipment- and the local Italian guys who do the concrete work would definitely do it by hand too.
The next step would be to form and pour the 3' long x ~20" wide x ~ 24" high underpinning piers up to ~ 1-2" below the underside of the old footings, then filling the gap with low-shrinkage grout and allowing the whole works to cure. Then repeat the process, then repeat the process again until you end up with the wall completely underpinned. Then bring the excavation contractor back for a day to muck out the spoils into a roll-off box, then do the prep for the footings and slab for the addition.
Back-breaking work digging by hand in clay till for sure. The stuff has an angle of repose of 90 degrees, but I wouldn't feel safe making the slope against the footing steeper than 45 degrees (that's the max slope my engineer friend would recommend too).
To avoid doing it by hand, I'd imagine you'd need the mini-excavator in the hole- and that would entail a big ramp or a crane, wouldn't it?
>I am going to be an owner builder. I think I can build my house just from consultations from you knowldgeable gentlemen/ladies.
That's pretty scary. Could you build it without the consultations from here? If not, then it's a pretty big gamble. Perhaps you were just being facetious.
Anyone concerned that the complexity of working properly with ICF's is being underestimated? Between leveling, securing, avoiding voids, avoiding blowouts, etc, it seems like it benefits from a fair amount of skill.
Anyone concerned that the complexity of working properly with ICF's is being underestimated? Between leveling, securing, avoiding voids, avoiding blowouts, etc, it seems like it benefits from a fair amount of skill.
I looked into the ICF program when it first was offered here several yrs ago. Rejected it primarily for insulative reasons, that we've discussed, and wall thinness. But I do recommend it to owner/builders who want to do their own forming, especially solo. Classes are offered but I thought the video I viewed adequate. From my recommendations, there have been several owner/builder trouble-free foundations, usually with the pour supervised by the sales rep. The AAB system school passed out a notebook at the end with enough pre-engineering such that the cost of the class was easily justified by that alone.
The horror stories I've heard were always from GC's who thought they knew so much they didn't have to pay attention to the instructions. Usually a problem with insufficient bracing. And minimal wood laying around, causing a frantic scavenger hunt through all nearby construction sites.
Voids usually happen due to lack of vibration. Reason enough for me to avoid the program. One professional pour I saw had concrete dropping 22'. Couldn't believe it! You can see daylight through several of the voids. The others, not visible, apparently didn't go all the way through the wall. Nobody has any idea just where or how large, but with adequate rebar it structurally probably doesn't matter. Just so long as it's not my house. PAHS Designer/Builder- Bury it!
>Nobody has any idea just where or how large, but with adequate rebar it structurally probably doesn't matter.
I have nothing against ICF, but this hits on my hesitations. You just don't know when there's a problem. And if half the structure can be a void without compromise, then it means the building is over-engineered. I see that with thin-shells. They're probably twice the rebar and concrete as is really, really needed, but they're engineered with extra safety factors be/c the engineer doesn't know how much of the bar will really, really be encased in the shotcrete. At least there are ways of telling, though. With permanent forms on all sides, you're pretty much not gonna know unless you x-ray it.
CH,
You can feel voids in ICF walls. With concrete behind, the walls are hard and solid. With no concrete behind, the foam feels soft and has some give to it. It sounds different, too. Even the amount of noise you make running your hand over the wall is enough to detect a void. Then you can decide whether you're going to do anything about it.
We pour with a slump of about 6" with fly ash added to the mix. It will fill dam near any cavity that water will. The spots that are likely to cause trouble you recognize when you're assembling the form. They are the places where a lot of steel ends up blocking access such as in lintels and, often, near corners. Then, you just be more careful with the pour there. It's easy to see where the concrete is going in ICF forms and easy to see where it hangs up. And it's easy to fix just by rodding it or by external vibration - hammering on a piece of scrap. And after the first one or two you don't let the pace of the job be driven by the machinery. There's no need to rush a pour.
I plan to start an ICF house for myself in the spring.
Ron
Thanks for the info Ron. I imagine different ICF's would have a different feel. Rasta might be harder to tell than some other than some other.
Thanks for the explanation.
I know nothing about Rasta or any of the post and beam systems. I have only ever worked with open forms such as Blue Maxx (Arxx), Lite Form, Integra Spec.
Ron
You'll need to calculate the square footage of wall area, not the SF of the house or basement. Each form system covers a different square footage per block, and the manufacturers can tell you how much concrete you'll need per block.
I'm in NJ as well, so if you need any help figuring this out let me know.
Bob
mendemoi:
there's a decent article (with pictures) in the July '03 Journal of Light Construction (JLC) on ICF's. The contractor interviewed gave a "blow-by-blow" account of his first experience using ICF's. He used American Polysteel's forms because they provided the most useful information. I've since contacted them and received a free video on CD regarding the product and installing it. I'm with habitat for humanity and searching for a faster way of getting an insulated foundation for a crawl space house. Some of the pointers mention by frenchy were covered, but I really like his mention of the "additive" they cement supplier used.
rookie
p.s. in another discussion, there was mention of magazines which people prefer, and I have found that the JCL seems to address my interest the best. I have no concetion with either Polysteel or JCL.
Mendemoi,
We recently started doing our own foundations, with ICF's. Good subs here are hard to find. So far I love them. We've used the Wisconsin Thermal-Form system. It's a verticle form, with metal ladders inside. Poured a 10' tall basement, with lots of corners. Turned out exactly on dimension, and the worst corner was 1/16" out of square. Today, I'm finishing forming on a new shop here, for myself. Using Nudura forms to make 5' frost walls. They are a great horizontal block. They don't require any glueing, since they have interlocking tabs on the webs. Got about 5 hours into forming this by myself, and it's about an 1100 sf building. The Nudura's are a little cheaper. Whatever form you choose, make sure you have a knowledgeable local rep. Good level footings are the key to making these go together easy. Good luck!
Brudoggie
BRUDOGGIE,
Any other information on the the TF System? I'm looking into that exact system for a house going up in spring. How much do their forms cost? Ease of use? Stability during the poor? Bracing required? I've seen their manual on their website and it looks like a pretty good system.
Where are you located? House is going up in the Fox Valley, WI.
Nathan
Canoe,
I like the TF system. As said, we just poured a 10' high 10" thick basement. I was a bit concerned with the height, so we added another wailer( horizontal brace) about half way up. We did this both inside and out, in addition to the recomended knee high brace. We also run a wailer at the top, to attach the turnbuckles to. Extra bracing than they require, but cheap insurance. Also, helps to keep things accurate. If this is a DIY project, your supplier should come out and show you a few things. The installation manual is quite thorough, so I'd read it, cover to cover. Cost wise, I pay about $3.00 per square foot of wall surface, for the 10" core ,for the forms. Seems a bit high, but I only have one supplier available. That is why I decided to try the Nudara system. A little competition never hurt anybody. I really like the fact that you can vibrate the pour in the TF system. Not all block manufacturers recomend that. Says something about the structural integrity of the forms, to me.
I'm in NE, Wi. up near the UP of Mi. Your location should provide you with a few contractors, or suppliers to choose from. Check them out. If you are hiring this out, get a recomendation from the factory in Sturgeon Bay, if possible.
If you let me know a few more details about your plan, I may have some tricks to help make the job easier. Let me know. Good luck!
Brudoggie
Brudoggie,
Thanks for the information. I have contacted the factory and got a couple of names from them. Hope to meet with one of them pretty soon.
My main objective is to be able to get the ICF basement for the cost of a poured one. Obviously, less would be nice too. So I would like to do some of the work setting up the forms and stuff, but have someone with experience to check them out once they are setup and be the lead for the pour.
The main basement will have 9 foot walls, but one wall will probably be at least 12 feet (x 39 feet). Also, I will have spancrete for the garage so I need a four inch shelf for that. A couple other things about the plan is the angled garage relative to the house, not a 45 degree. Not the best for ICF's but definitely do able. Any recommendations there?
Ever do the walls of a house as well as the foundation? I've been considering it, but I'm not convinced on the ability to install trim, run wiring, etc.
I also talked with a friend of a friend who used the TF system and did it himself, so I've gotten some information from him as well.
The one thing I haven't looked into yet is the turnbuckles for bracing the form. Can those be rented? By looking at it I'm guessing it is a lot easier to use turnbuckles, than just nailing diagonal bracing that you can't adjust.
Thanks for the advice so far. Any interest in looking at a house in Wrightstown, 15 minutes sout of Green Bay?
Nathan
Canoe,
Angled garage to house is no problem with the TF's. They make a stock 45 degree corner, and will custom any other angle, I believe. Bracing requirements may be a bit more extreme, with the angles, depending on the wall lengths. The ledge is possible, there are a couple different examples in the installation manual.
Never done the whole house. Only 2 have been done up here, as far as I know. Not sure what system one used, but the other used the Nudura, I mentioned. I just came in from pouring 140 lf of 5' by 8" frost walls, for my new shop. First try with the Nudura's. I'd check them out, if available down there. They are faster, and slightly cheaper. Nice system. I think we're finished with the TF's, after the one we've got to pour, next week. Nothing against the TF's, but time is money! One of my concrete supplier's is the owner of the Nudura, poured home. They even did the gables, and were talking truck drivers here, not experienced foundation men.
Turnbuckles may be available for rent, in your area. TF is trying to get some of their installer-suppliers, to set up a trailer with the needed gear, to rent out to DIY customers. Ask around. If not you could buy some and resell when done. Ambrosious concrete in DePere sells them. Expect to pay about $13 each. Heck, I might even take some of them off your hands.
As far as coming down to work. I appreciate the offer, but I don't think you want to wait until '05. Besides, you want to do it cheaper than a hard form job right? We're anything but cheap :) It would cost you a fortune, just in beer!!! For after work of course!
Check references, check out work in progress, ask lots of questions, shop local!! That will get you your best value. Keep in touch. I get down there about every 2 or 3 months. Might be able to do a drive by pre-pour inspection for you. Advise is free, and worth exactly what you pay for it !!:)
Brudoggie
Say have you looked at another product other then spancrete. There are a few different products, Like Polysteel's PanelDeck or Light deck. I have used them a few times on a few different projects and they worked well. Around the same cost of spancrete but you gain the insulation on the bottom of the form and the steel tabs to fasten your sheet rock to also.
I am in Denmark WI. I deal with the Polysteel System and if you would like some info I can send you out some.
Sincerly Brian
Polysteel Bayland Inc.
We use ARXX and NuDura forms if you want a 10' high basement walls we are cheaper than just concrete. figure $8.00/sf that is material and labor this includes water proofing not damp proofing.
tim kiser