Can anyone out there provide guidance on insulating a cantileaver on a raised bungalow, as the floors over the cantileaver are very cold in the winter. The basement is heated and the joist cavities are currently filled with fiberglass insulation. I have access to the joist cavities from the inside.
Discussion Forum
Discussion Forum
Up Next
Video Shorts
Featured Story
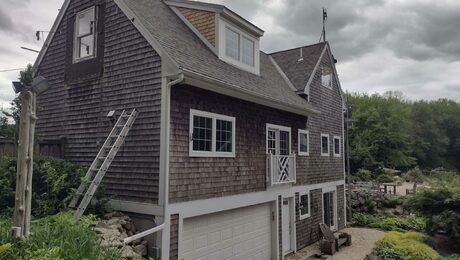
Listeners write in about ventilation and radon control and ask questions about tightening basement garages, ventilation solutions, and safer paint stripper.
Highlights
"I have learned so much thanks to the searchable articles on the FHB website. I can confidently say that I expect to be a life-long subscriber." - M.K.
Fine Homebuilding Magazine
- Home Group
- Antique Trader
- Arts & Crafts Homes
- Bank Note Reporter
- Cabin Life
- Cuisine at Home
- Fine Gardening
- Fine Woodworking
- Green Building Advisor
- Garden Gate
- Horticulture
- Keep Craft Alive
- Log Home Living
- Military Trader/Vehicles
- Numismatic News
- Numismaster
- Old Cars Weekly
- Old House Journal
- Period Homes
- Popular Woodworking
- Script
- ShopNotes
- Sports Collectors Digest
- Threads
- Timber Home Living
- Traditional Building
- Woodsmith
- World Coin News
- Writer's Digest
Replies
If I’m understanding your structure properly, my advice would include the installation of a vapor barrier immediately under the flooring of that entire cantilever. Without it, moisture will migrate and accumulate in the FG insulation, rendering it virtually useless and the floor cold as a result. I’ve seen these situations without the vapor barrier that accumulated so much moisture under the floor during the winter that the weight of the resulting ice caused the soffit material to sag severely. Many gallons of water thawed from these areas in the spring. If removing the existing flooring and/or sub-flooring is not an option, then you might consider applying several coats of oil-based poly or better yet, several coats of shellac, to the flooring or sub-floor, as this will serve as a second-best vapor barrier.
Goldhiller,
If you have seen saturated fiberglass batts in cantilevered joist bays, the source of the moisture is almost certainly not diffusion from the interior. The typical subfloor (OSB or plywood) is a perfectly adequate vapor barrier. Far more important than worrying about vapor diffusion is ensuring that there is an adequate air barrier. In the case of the joists described, the most important air sealing detail is at the blocking between the joists at the point where the cantilever begins. The blocking can consist of 2-by lumber or rigid foam, but must be installed with caulk or expanding foam around the perimeter of each piece of blocking. If this step is neglected, warm moist interior air may enter the joist bays, where cool surfaces permit condensation, leading to the saturated batts you describe.
you could pull the useless fiberglass out , put in solid blocking and blow the cavity with Dens-pak cellulose.. and forget about the vapor barrier....
or not..
....but hey......
Mike Smith Rhode Island : Design / Build / Repair / Restore
Yes, I failed to mention the necessity of blocking in the joist bays. It's one of those things that is so 2nd nature to me to install in these situations that I neglected to mention it. Definitely, an oversight on my part.
However, I am absolutely convinced that the water that accumulated in the FG of those joist bays came from the absence of the vapor barrier because it has never occurred again since we installed one. This was the one and only change made to the construction of the room. The joist bays were blocked from the git-go and the subfloor was 3/4" OSB before and after. This was in a 2nd story bedroom, not in a kitchen or bathroom where one might expect high humidity levels and so took us all by surprise when it occurred the first time and we were summoned to assess the situation and offer resolutions. The installation of the vapor barrier under the floor was the only thing that could potentially be the cause and so we put it in. We were all pleased with the initial results the following winter and monitored the situation for four years running. No more problems.
About a year after this initial incident, we were called into another situation with the same result, but this time the homeowner wasn’t willingly to bear the expense of tearing up the subfloor, so we coated the floor with three coats of shellac as it offers the best resistance to water vapor of any commonly available wood finish. Then the carpet was reinstalled. Apparently, it worked also because the problem has not reoccurred.
Needless to say, we include vapor barriers in the floors of all cantilevered situations now as I learned two things from these experiences…….1- Although I’d never seen it before, it can happen and… 2 - plastic is cheaper than repairs.
Thank you for the great advice, it has been difficult to get around here. I have 5 written sources(each one on energy conservation) and all 5 give different methods to deal with the problem. One local insulation expert suggested spraying urethane foam on the box joist and the bottom of the joist cavity, leaving an airspace for warm air to circulate. the second expert suggests using styrofoam SM in layers on the bottom of the joist cavity and on the box joist, and then seal with caulking. They both stressed air cirulation will help keep the floor warmer and condesation to an absolute minimum. Both methods also provide an air barrier.
Any thoughts?
No, I guess I don't. I'm not familiar enough with these approaches and consequently wouldn't want to advise you one way or the other. While I've had some experience with the use and characteristics of urethane foam, I certainly don't qualify as an expert on the subject. These two methods may very well perform equally. Whatever method you may choose just make sure that you've eliminated any sources for moist air to migrate into the area and provided adequate insulation to control heat/AC losses. If you do this, everything should work out fine.
Edited 9/6/2002 12:19:57 AM ET by GOLDHILLER
Take another look at Mike's post. Short and sweet. And effective...both thermally and cost-wise. But hey...whadda he no?
Also, you need to ventilate the underside of the insulated space. Even with a vapour barrier, there will still be moisture in the insulation space. Failure to ventilate will lead to rot in the framing.
Fur down the joists with 3/4 inch strips and use strip ventilation.